Практическая вибродиагностика
Предисловие
В последние годы в отечественной и зарубежной литературе появилось множество публикаций по проблемам распознавания технического состояния машин и механизмов. Опубликованы фундаментальные труды по теории диагностики, методическим вопросам и принципам построения диагностических и измерительных систем. Опубликованы также многочисленные исследования по диагностированию зарождающихся и развитых дефектов зубчатых зацеплений, подшипников, электрических дефектов и др. Однако, комплексное взаимоувязанное изложение теоретических вопросов, практических исследований, описание выпускаемых промышленностью измерительных систем и опыта внедрения виброакустического неразрушающего контроля на предприятии — явление достаточно редкое.
Целью настоящей книги является комплексное краткое изложение информации, необходимой для внедрения технологии периодического вибромониторинга основного и вспомогательного оборудования на промышленном предприятии, требуемой для повышения квалификации специалистов.
Книга основана на многолетнем опыте практических работ по выявлению и устранению дефектов механического оборудования авторов и их коллег на предприятиях транспорта нефти и газа, химической и нефтеперерабатывающей промышленности, электроэнергетики, металлургии и целлюлозно — бумажной промышленности России. Книга включает описание: методологии вибродиагностирования зарождающихся и развитых дефектов и сведения о вибрации и надежности работы оборудования; современных методик вибромониторинга технического состояния оборудования; средств сбора, обработки и анализа данных; принципов определения норм вибрации и оценки технического состояния оборудования и практическое руководство по выявлению дефектов оборудования на основе частотного анализа колебаний. Прочитав ее, начинающий специалист и менеджер получат полное четкое представление о совокупности методов и средств вибродиагностики, приоритетах в постановке целей, инструментах и механизмах осуществления вибромониторинга. Для опытного специалиста огромный интерес представят приведенные диагностические признаки и параметры дефектов, иллюстрированные более чем 60 реальными примерами различных выявленных и подтвержденных на практике дефектов оборудования на основе анализа спектров, форм, орбит, огибающих и кепстров сигналов вибрации и др.
Авторы выражают глубокую благодарность И.С.Минасяну,
Г.С.Донгарову, Е.Ю.Сементовской, И.Э.Власову, А.Л.Колпакову,
И.З.Нигаметзянову, Б.В.Сливко, А.С.Гольдину, Г.В.Зусману, С.В.Пермякову,
без помощи и участия которых книга бы не была написана. Особую
благодарность авторы выражают Р.В.Васильевой за редактирование
настоящей книги.
При подготовке материалов 1-й главы использовались книги: "Виброакустическая диагностика зарождающихся дефектов", Балицкий Ф.Я., Иванова М.А., Соколова А.Г., Хомяков Е.И. М.: Наука, 1984, 129 с., Карасев В.А., Ройтман А.Б. "Доводка эксплуатируемых машин. Вибродиагностические методы." М.: Машиностроение, 1986, 192 с. При подготовке материалов 5— й и 7 —й главы использовалась книга: Гольдин А.С., "Устранение вибрации турбоагрегатов на тепловых электростанциях", М.:Энергия, 1980, 96 с.
Отзывы и пожелания просим направлять по адресу фирмы, с помощью которой книга была приобретена.
• Методология диагностирования зарождающихся и развитых дефектов • 1 - 1 •
Методология вибродиагностирования зарождающихся и
развитых дефектов[1]
Отечественный и зарубежный опыт показывает, что внедрение средств диагностирования является одним из важнейших факторов повышения экономической эффективности использования оборудования в промышленности. Назначение диагностики — выявление и предупреждение отказов и неисправностей, поддержание эксплуатационных показателей в установленных пределах, прогнозирование состояния в целях полного использования доремонтного и межремонтного ресурса.
Практически мгновенная реакция вибросигнала на изменение состояния оборудования является незаменимым качеством в аварийных ситуациях, когда определяющим фактором является скорость постановки диагноза и принятия решения.
Вибродиагностика и мониторинг состояния механического оборудования позволяют:
• уточнить причины дефекта и условия его возникновения и развития, оценить влияющие факторы;
• вовремя устранить дефект или увеличить среднюю наработку парка на проявление дефекта (отказа);
• снизить интенсивность проявления дефекта (отказа) при наиболее ответственных режимах работы и эксплуатации машины;
• улучшить организацию работ по разработке и внедрению мероприятий, направленных на устранение дефекта;
• оценить эффективность мероприятий, направленных на устранение дефекта, и выбрать для внедрения наиболее эффективные;
• получить чисто экономический эффект благодаря снижению затрат на внедрение мероприятий, предотвращающих дефект или устраняющих неисправность, и затрат производства на изготовление деталей;
• оценить возможный эффект от разработанных и внедренных мероприятий на ранней стадии, что очень важно, так как полное проявление действия этих мероприятий зависит от наработки изделия после их внедрения
• Методология диагностирования зарождающихся и развитых дефектов • 1—3 •
Назначение виброакустической диагностики.
Вибродиагностика, являясь разделом технической диагностики, есть отрасль знаний, включающая в себя теорию и методы организации процессов распознавания технических состояний машин и механизмов по исходной информации, содержащейся в виброакустическом сигнале.
Основным физическим носителем информации о состоянии элементов работающего оборудования в вибродиагностике является виброакустический сигнал — собирательное понятие, включающее информацию о колебательных процессах (вибрационных, гидро — или газодинамических и пр.) и акустическом шуме механизма в окружающей среде. Следовательно вибродиагностированию может подвергаться любое оборудование, функционирование которого сопровождается возбуждением колебательных процессов. В данной книге рассматриваются в основном проблемы диагностирования дефектов узлов роторных машин и механизмов (в дальнейшем агрегатов). Всякое отклонение параметров функционирования оборудования от нормы приводит к изменению характера взаимодействия его элементов и к изменению сопровождающих взаимодействия виброакустических процессов.
Возможные состояния оборудования.
Различают следующие состояния оборудования:
• исправности - состояния, при котором исследуемый агрегат соответствует всем требованиям, установленным нормативно — технической документацией;
• работоспособности — состояния, при котором исследуемый агрегат способен выполнять заданные функции в пределах, установленных нормативно -технической документацией; проверку работоспособности исследуемого агрегата осуществляют при выводе из монтажа или ремонта и на стадии эксплуатации, она может быть менее полной, чем проверка исправности, т. е. может оставлять необнаруженные неисправности, не препятствующие применению его по назначению;
• правильности функционирования — состояния исследуемого агрегата, при котором он выполняет в текущий момент времени предписанные ему алгоритмы функционирования; проверка правильности менее полна, чем проверка работоспособности, так как она позволяет убедиться лишь в том, что исследуемый агрегат правильно функционирует в данном режиме работы в данный момент времени;
• предельного (аварийного) — состояния исследуемого агрегата (отказа), при котором его дальнейшая эксплуатация невозможна вследствие ухода его параметров за недопустимые пределы.
Совокупность технических параметров оборудования, характеризующих возможное отклонение функционирования оборудования от нормального, определяет состояние оборудования в текущий момент времени (диагноз). Поиск неисправностей — одна из важнейших задач диагностики состояния оборудования.
Множество возможных состояний оборудования вследствие непрерывности их изменения во времени бесконечно. Их можно разделить по крайней мере на два подмножества:
• работоспособные состояния, позволяющие оборудованию выполнять возложенные на него функции;
• состояния, соответствующие возникновению в оборудовании неисправностей, приводящих к потере им работоспособности, или предельные аварийные состояния (отказ оборудования).
• Методология диагностирования зарождающихся и развитых дефектов • 1—5 •
для каждого класса технических состояний и разработку правил принятия решений о принадлежности к тому или иному классу состояний.
Если к дефекту агрегата отнесена его выходящая за допустимые пределы виброактивность, то необходимым этапом диагностического исследования является локализация источников повышенного уровня колебательной энергии. При этом различаются два возможных варианта: либо источники вибрации независимы, либо статистически связаны. Необходимость разделения влияния коррелированных источников намного усложняет процедуру диагностирования.
Эффективность процессов постановки диагноза определяется не только качеством алгоритма диагностирования, но и, в неменьшей мере, средств диагностирования. Эффективная организация системы сбора и обработки информации, увеличивающая достоверность диагностирования, уменьшающая влияние субъективных факторов, затраты времени, труда и средств, должна определяться Регламентом предприятия.
Существуют два вида систем диагностирования: тестовая функциональная. Тестовое диагностирование заключается в подаче на механизм специально организуемых тестовых воздействий. Функциональное диагностирование в качестве входных воздействий использует рабочие воздействия, предусмотренные алгоритмом функционирования механизма. Настоящая книга затрагивает второй подход, поскольку специфика эксплуатации оборудования, с одной стороны, и взаимодействия деталей и узлов механизмов, с другой, не всегда позволяют заменить естественные воздействия искусственно сформированными.
Особенность методов диагностирования дефектов, особенно на ранней стадии развития, заключается в использовании разнообразных приемов повышения чувствительности компонентов вибросигнала к изменению технического состояния механизма, поскольку на стадии зарождения дефектов во многих случаях помеха значительно превышает уровень полезного сигнала, содержащего информацию об изменении технического состояния.
Задачи вибродиагностики.
Итак, вибродиагностическими методами решаются две основные задачи диагностики эксплуатируемых агрегатов: распознавание состояния эксплуатируемого агрегата и выявление причин и условий, вызывающих неисправности, которые следует устранить.
В теоретическом плане задача вибродиагностики при мониторинге парка агрегатов и выявлений изделий с потенциально ненадежными деталями может рассматриваться применительно к эксплуатации сложных систем по фактическому техническому состоянию как часть задачи управления случайным процессом повреждаемости на основе косвенной информации о процессе. При этом управление процессом или наблюдение за ним во многих случаях начинается не с начала эксплуатации агрегата, а по событию — проявлению неисправности, и проводится зачастую в условиях неполноты и неопределенности информации.
Косвенность информации заключается в том, что для определения состояния деталей используют вибрационные сигналы, прошедшие через динамическую систему и преображенные ею. Неполнота информации обусловлена технической невозможностью получить все необходимые сведения, неопределенность — неточностями постановки задачи и описания диагностируемых состояний, влиянием помех.
Как говорилось ранее, роль диагностики в управлении процессом заключается в установлении границ и условий, в которых допускается или происходит протекание процесса, обнаружении и прогнозе выхода параметров процесса за установленные границы. При этом существенно то, что к функции
• Методология диагностирования зарождающихся и развитых дефектов • 1 — 7 •
Разнообразие дефектов, обнаруживаемых методами вибрационной диагностики, и сложность сигналов, порождаемых неисправностями и колебаниями деталей агрегатов, заставляет при выявлении и измерении диагностических параметров проводить разнообразную обработку сигналов:
• разделение вибрационного сигнала в частотно — фазовой и временной областях на "элементарные" сигналы, т. е. на компоненты, обусловленные различными факторами, каждый из которых является самостоятельным источником, вызывающим колебания;
• пространственное разделение вибрационных сигналов;
• восстановление форм выделенных "элементарных" сигналов;
• линейные и нелинейные преобразования сигналов (фильтрацию, нормализацию, интегрирование, дифференцирование и т.
д.);
• измерение отдельных параметров и статистических характеристик сигналов;
• измерение характеристик взаимосвязи сигналов.
Выбор способа обработки сигнала и соответствующей структурной схемы измерительного канала определяется постановкой диагностической задачи, особенностями исследуемого и выделяемого сигналов, особенностями конструкции обследуемого оборудования и прочими факторами.
Успех решения задач вибродиагностики при эксплуатации парка оборудования во многом зависит от контролепригодности конкретных агрегатов.
Разбиение агрегата, как объекта диагностирования, на элементарные блоки.
Любой сложный агрегат состоит из ряда деталей (элементов, узлов), соединенных между собой, поэтому отказ любого из элементов может вызвать нарушение работоспособности всего агрегата. Сложные функциональные зависимости при взаимодействии элементов агрегата и большое число структурных параметров затрудняют описание его поведения. Методы и приемы, облегчающие процесс диагностирования сложных систем, сводятся к следующим операциям: агрегат разбивается на подсистемы, которые в свою очередь разбиваются на узлы, связанные между собой иерархической структурой. Разбиение агрегата на узлы способствует упрощению процедуры поиска возможных неисправностей, приводящих к отказу. Во многих случаях, если пренебречь некоторыми связями, диагностирование узлов возможно независимо друг от друга. Для получения достоверной информации о состоянии оборудования используются различные виды диагностических обследований, например общее по основным параметрам работоспособности объекта и поэлементное, сопровождающееся последовательным распознаванием неисправностей механизма.
Состояние элементов выявляется некоторой последовательностью проверок (измерений) называемых работами по исследованию вибрации. Совокупность проверок, достаточную для определения состояния агрегата вплоть до выявления характера неисправностей, называют диагностическим тестом. Такая проверка может быть поэлементной, когда проверяется исправность каждого элемента (узла) в отдельности; по модулям, когда производятся измерения в отдельных блоках, состоящих из ряда элементов, и по группам элементов, составляющим функциональное звено системы — отдельный механизм агрегата.
Первоочередными объектами диагностирования являются те элементы и сопряжения (узлы), отказ которых наиболее вероятен. Такие узлы называют критическими.
Критичность узлов оценивают коэффициентом повторяемости неисправностей, их средней частотой, процентным отношением числа появлений неисправностей данного элемента, а также стоимостными и трудовыми затратами на устранение пропущенных отказов и проведение диагностирования.
• Методология диагностирования зарождающихся и развитых дефектов • 1-9 •
• по последствиям (отказ, устраняемый при эксплуатации; отказ, ведущий к досрочному выводу оборудования из эксплуатации; отказ, ведущий к происшествию; отказ, ведущий к аварии);
• по способам устранения (заменой детали, регулировкой, мелким ремонтом, заменой узлов в эксплуатации, доработкой в заводских условиях и т.д.);
• по связи дефектов и отказов между собой (независимые и зависимые). Рассмотрим основные факторы и процессы, вызывающие прочностные отказы
и дефекты оборудования, их связь с вибрационными процессами.
Нагруженность деталей оборудования.
Нагрузки бывают нескольких видов: статические, динамические (переменные и ударные), циклические.
Статические нагрузки могут оказывать влияние на вибрации в оборудовании, главным образом в тех случаях, когда они вызывают изменение геометрической формы деталей, например кинематических пар. Кроме того, под действием статических нагрузок могут изменяться частоты собственных колебаний деталей, вследствие увеличения жесткости, например, под действием центробежных сил на диски и лопатки турбомашин. При действии достаточно высоких статических нагрузок в течение длительного времени явления ползучести материала могут привести к изменению геометрической формы деталей и появлению трещин.
Циклические нагрузки не вызывают вибраций оборудования, но приводят к явлениям усталости металла, что в свою очередь может оказать влияние на вибрацию.
Динамические нагрузки — основная причина колебания деталей агрегатов и их динамической напряженности, приводящей к усталостным поломкам.
Усталость.
Существуют несколько видов усталостных разрушений деталей: типичная усталость по действием переменных напряжений происходит из-за развития трещины, распространяющейся в материале по экспоненциальному закону; контактно-усталостные разрушения (питтинг, шелушение, усталостное выкрашивание контактных пар), начинающиеся с зарождения язвины или отдельного очага усталостного разрушения и, затем, с увеличением числа язвин относительно быстрого разрушения; коррозионно-усталостные разрушения деталей начинаются с очага коррозии (например, подверженных воздействиям агрессивных газов), служащего началом трещин, после заполнения которых продуктами коррозии происходит коррозионное растрескивание и разрушение деталей; термическая усталость на начальной стадии сопровождается слабым изменением геометрической формы тела вследствие образования сетки мелких трещин, затем магистральных трещин, приводящих к разрушению под действием динамических напряжений.
Под действием переменной нагрузки усталостная долговечность имеет обратно-степенную зависимость от ее значения с показателем степени порядка восьми и более в зависимости от материала.
Связь усталости и вибрации.
Вибрация вызывает усталостные разрушения деталей, действуя как переменная нагрузка. При появлении усталостных трещин изменяются собственные частоты колебаний деталей вследствие изменения их жесткости и могут изменяться демпфирование и характер колебаний (например, начинают проявляться эффекты нелинейности), что может вызвать изменение характера вибрации данной детали.
• Методология диагностирования зарождающихся и развитых дефектов • 1 - 11 •
Коррозионный износ. Возникает вследствие взаимодействия деталей агрегата с агрессивной средой.
Кавитационная эрозия. Возникает вследствие локальных гидравлических ударов жидкости в зоне кавитации.
В процессе износа выделяют три стадии:
• приработка, когда изменяется микро- и макроструктура поверхностей и имеет место уменьшение скорости износа;
• нормальный износ, когда можно принять линейную связь между значением износа и временем;
• прогрессивный износ, когда имеет место возрастание скорости износа.
Основными факторами, влияющими на значение нормального износа, являются удельное давление и относительная скорость движения трущихся деталей.
Износ деталей кинематических пар приводит к увеличению зазоров в парах, что усиливает проявление динамических сил взаимодействия деталей, приобретающего в некоторых случаях ударный характер, и обогащение вибросигнала шумовыми и импульсными составляющими. Износ может также изменить жесткостные характеристики системы, что влияет на частоты и формы колебаний.
Отказы из-за несовершенства изготовления и сборки оборудования.
Причинами отказов могут быть как эксплуатационные факторы, так и несовершенство изготовления и сборки оборудования. Эти причины весьма многообразны.
Причины отказов, закладываемые при проектировании машины, могут быть следующими: неудачный выбор формы деталей, например, с концентраторами напряжений и резким изменением сечений; неудачный выбор материалов и их сочетаний; недооценка нагрузок и действующих сил; неучет их возможных изменений в процессе эксплуатации машины и т. д.
Причинами отказов, закладываемыми при изготовлении машины, могут быть, например, неудачные допуски, использование бракованных деталей и материалов, нарушения технологии изготовления, неполнота контроля.
Нарушение технологии в процессе сборки — частая причина отказов, например, из-за неправильно установленных зазоров, пятна контакта, нарушения посадок, ослабления затяжки и др.
Другая частая причина — изменения конструкции или технологии, влияние которых на надежность машины трудно определяется при разработке и внедрении и проявляется в ходе эксплуатации машины.
В машинах протекают различные, связанные с их функционированием, динамические процессы, происходящие в различных средах: газовых, жидкостных, воздушных и т. д. Большинство этих процессов оказывают динамическое воздействие на элементы конструкции и вызывают их колебания. Некоторые динамические процессы (вибрационное горение, кавитация и др.) вызывают разрушение деталей машин.
В диагностическом плане динамические процессы могут быть связаны с колебаниями элементов конструкции и как возбуждающие вибрацию, и как изменяющие ее.
Итак, в процессе эксплуатации структурные параметры оборудования изменяются, упорядоченность системы в целом и ее функциональные качества ухудшаются, деградируют. Для того чтобы измерить степень этой деградации в данный момент и прогнозировать ее на ближайшее время, необходимо знать закономерность изменений структурных параметров под воздействием типичных эксплуатационных факторов. Такими изменениями структурных параметров механизмов являются изменения, приводящие к постепенному или внезапному отказу механизма.
• Методология диагностирования зарождающихся и развитых дефектов • 1 - 13 •

Рис. 1—02. График изменения уровня вибрации с наработкой при локальном износе контактирующих поверхностей.
Как правило, эти закономерности не совпадают с изображенными на рис. 1 — 01, например, локальный износ контактирующих поверхностей вызывает сначала падение уровня вибрации (этап приработки), затем этот уровень практически остается неизменным на достаточно большом интервале времени (нормальная работа), и только на третьем этапе (интенсивный износ) наработки уровень начинает расти по экспоненте до момента отказа (рис. 1 — 02).
Требования к диагностическим признакам.
Вибродиагностика оборудования есть не что иное, как распознавание классов технических состояний агрегата по совокупности его вибрационных характеристик. Эта проблема может быть решена как методами статистической теории распознавания при наличии большого объема информации, так и детерминистскими методами, более кратко описывающими наиболее существенные стороны явления.
Распознавание состояний оборудования — это отнесение предъявленного к опознанию виброакустического образа к одному из возможных классов (диагнозов) с помощью специально построенного решающего правила. Для успешного решения этой задачи должна быть набрана статистика соответствия диагностических признаков классам технических состояний.
Исходя из изложенного выше, задачу диагностирования можно рассматривать как двойственную задачу: с одной стороны, задачу построения характеристики класса состояний, которому принадлежит совокупный виброакустический образ, и, с другой стороны, задачу принятия решения о принадлежности к одному из классов состояний испытуемого виброакустического образа. Решение такой задачи обеспечивается правильным выбором ряда структурных параметров (диагностических признаков), в частности параметров вибрации.
Рациональный выбор диагностических признаков, т. е. соответствующим образом представленных характеристик колебательных процессов, чувствительных к изменению технического состояния машин и механизмов, в значительной мере определяет успех диагностирования. Казалось бы, чем больше число признаков, тем полнее они характеризуют объект диагностирования и тем надежнее распознавание. Но это справедливо лишь в том случае, когда признаки независимы. Очевидно, что наиболее полезными признаками являются те, которые инвариантны (нечувствительны) к изменению внутри класса и резко меняются при переходе от одного класса к другому. Каждый из признаков, характеризующих состояние механизма, при измерении может получать случайные значения как в результате погрешностей измерения, так и в результате разброса параметров состояний, принадлежащих одному классу. Наиболее информативными являются
• Методология диагностирования зарождающихся и развитых дефектов • 1 — 15 •
Свойства вибросигнала роторных агрегатов.
Представление вибросигнала полигармонической и квазиполигармонической моделями.
В оборудовании, рассматриваемом в настоящей книге, характер взаимодействия элементов подчинен периодическому закону, связанному с вращательным движением. К такого рода агрегатам относятся роторные, где периодическое возбуждение в наиболее простом виде проявляется как сумма гармонических составляющих, кратных основной частоте возмущения, т.е. в виде полигармонической вибрации
x(t)=? ak cos(kwr t + jk )
В роторных агрегатах одной из основных частот возбуждения вибрации является оборотная (роторная) частота, называемая в дальнейшем частотой вращения ротора:
fr = wr / 2p ,
где wr - угловая частота вращения ротора.
На установившихся режимах спектр колебаний — дискретный со спектральными составляющими на частоте вращения ротора и ее гармониках (kfr).
Таким образом, информативными параметрами в такой модели колебаний являются значения амплитуд дискретных составляющих спектра на частоте вращения ротора и ее гармониках и скорость их изменения при увеличении наработки механизма. Амплитуды колебаний на роторных частотах определяются чаще всего величиной дисбаланса, несоосностью валов, кинематическими погрешностями и отношением критической частоты вращения ротора к рабочей.
Помимо упомянутой выше вибрации, кратной частоте вращения ротора, в спектре вибросигнала роторного агрегата могут присутствовать такие характерные частотные составляющие, как
fz = k (fr z) , k = 1, 2, 3, ..., n,
где z — число элементов взаимодействия на окружности ротора. Для зубчатого зацепления z равно числу зубьев шестерни; для турбины, насоса и вентилятора — числу лопаток рабочего колеса и т. п.
Модель полигармонического возбуждения колебаний в роторных агрегатах является удобной формой представления спектра колебательного процесса, позволяющего сконцентрировать внимание лишь на определенных частотах kfB , кратных основной частоте возбуждения колебаний fB диагностируемого узла агрегата. Первичный процесс локализации источников повышенной виброактивности конструкции агрегата состоит как раз в выявлении потенциальных источников возбуждения, вызывающих колебания на данной частоте.
Практика вибродиагностики роторных агрегатов показала, что полигармоническая модель вибросигнала является лишь нулевым приближением в описании сложного колебательного процесса реального агрегата, хотя может с успехом использоваться в задачах локализации источников и в задачах диагностирования грубых дефектов типа разрушения лопаток турбины, деталей подшипников, поломки зубьев и т.
п., вызывающих существенное увеличение уровня колебаний на определенных частотах. В работе реального агрегата абсолютное повторение с течением времени условий взаимодействия его деталей между собой и с внешней средой практически невозможно.
• Методология диагностирования зарождающихся и развитых дефектов • 1 — 17 •
определенной формы. Такая модель достаточно универсальна, так как она позволяет математически описать процессы возбуждения колебаний как в роторных механизмах типа зубчатого зацепления, подшипников качения и скольжения, турбинах, вентиляторах, циркуляционных и центробежных насосах, так и в поршневых машинах с механизмами циклического ударного действия.
Обозначая функцию, определяющую отдельный импульс, через f(t), можно представить периодическую последовательность импульсов в виде
x (t) = S f(t - tk) [1.2]
где tk = kT + t0 , a k - целое число.
Функция x(t) может быть как детерминированной, так и случайной, отражающей случайность одиночного импульса, которая заключается в том, что его амплитуда, длительность и момент появления могут быть, вообще говоря, случайными величинами.
В ряде практических моделей вибросигнала функционирующих механизмов имеет место периодическая последовательность импульсов, модулированных по амплитуде, при неизменной форме, длительности и частоты следования импульсов. Такой вид модуляции, называемой амплитудно-импульсной модуляцией (АИМ), наиболее часто используется для математического представления акустического сигнала.
Если импульсы, сохраняя свою форму и величину, смещаются во времени на величину Dt , то имеет место временная импульсная модуляция (ВИМ). При этом различают фазово-импульсную модуляцию (ФИМ), когда импульсы имеют постоянную амплитуду и длительность, а меняется их положение на оси времени от периода к периоду, частотно-импульсную модуляцию (ЧИМ), когда импульсы сохраняют амплитуду и положение на оси времени, но меняется их длительность.
Все виды модуляции в той или иной мере применимы к задачам моделирования акустического сигнала.
В работающем агрегате в зависимости от характера физического процесса, протекающего в нем, возможны различные отклонения в последовательности импульсов, которые можно охарактеризовать модуляцией амплитуды, длительности или моментов появления имульсов, однако при функционировании оборудования с заданной функцией взаимодействия деталей, определяющейся кинематикой агрегата, наиболее часто встречается амплитудная модуляция, обусловленная разбросом величины силы взаимодействия его элементов в каких-то пределах (неоднородность структуры контактирующих поверхностей зубьев, приводящая к вариации пятна контакта колес зубчатого зацепления; неравномерность воздушного потока в зазоре, отклонение геометрических размеров лопаток турбины вследствие обгара, эрозии и др.). В то же время погрешность окружного шага или явление заедания в зубчатом зацеплении, изгибная деформация, приводящая к неравномерному размещению лопаток в диске или на рабочем колесе турбины, являются причиной возбуждения модулированных по фазе импульсных колебаний.
На рис. 1-04 приведен случай периодической последовательности импульсов, следующих с тактовым интервалом Т, равным, например, периоду пересопряжения зубьев в зубчатом зацеплении, модулированных по амплитуде квазидетерминированным процессом. Т0 - период низкочастотного процесса, например оборотов вала шестерни. В нижней части рисунка изображен спектр такого колебательного процесса. В окрестности основных частот 2p?/ Tz следования импульсов в спектре присутствуют комбинационные частоты, отстоящие от основных на q(2p/Т0), где q — целое число. Амплитуды комбинационных составляющих равны 2s2q/Т, где s2q— дисперсия компоненты с номером q,, s2 - суммарная дисперсия модулирующей функции.
• Методология диагностирования зарождающихся и развитых дефектов • 1 — 19 •
На рис. 1—05 приведен узкополосный случайный процесс (амплитудная модуляция), описываемый математическим выражением вида:
у(t) = А[1+mЕ(t)]соs(w0t + j0??);
где w0 — несущая частота, например, частота пересопряжения зубьев, А — амплитуда, m — глубина модуляции (меняется от 0 до 1). Е(t) — в общем виде сумма гармонических низкочастотных колебаний, кратных основной частоте возбуждения Wо, например, частоте вращения шестерни:
E(t) = SBk??соs(k W0t + jk?)
Выделение огибающей производится с помощью амплитудного детектора.
Методология диагностирования зарождающихся дефектов.
Дефекты контактирующих поверхностей и характер их проявления в виброакустическом сигнале.
Вибродиагностика базируется на анализе изменений свойств вибропроцессов, в предположении, что вибросигнал работающего агрегата содержит всю информацию о взаимодействии его деталей. Задача заключена в разработке алгоритмов извлечения из него информации о состоянии определенного узла и локализации возникающих неисправностей. Большой уровень помех и сравнительно малые изменения полезного сигнала определяют специфику поиска информативных диагностических признаков, чувствительных к развивающемуся дефекту и инвариантных к мешающим факторам. Лишь в исключительных случаях увеличение общего уровня вибросигнала свидетельствует о зарождении определенного дефекта. Как правило, существенное увеличение общего уровня вибрации или отдельных спектральных компонентов говорит лишь о грубых изменениях состояния диагностируемого агрегата, приводящих к потере его работоспособности. Локализация же развивающейся неисправности, еще не приведшей к развитому дефекту, определение степени развития зарождающегося дефекта и прогнозирование возможны лишь на основе исследований тонкой структуры виброакустического сигнала и связи его с кинематикой и динамикой агрегата.
Изучение свойств вибропроцессов роторных агрегатов показало, что при появлении неисправности меняется структура сигнала, т. е. меняется соотношение между его компонентами или появляются новые. Это подтверждается моделированием колебаний кинематических звеньев механизмов, представляемых в виде суперпозиции квазиполигармонических и шумовых процессов.
Периодическая последовательность импульсов, следующих с частотой пересопряжения зубьев в зубчатых передачах, модулированных по фазе и амплитуде низкочастотным полигармоническим процессом, на фоне шумовой составляющей имеют спектр мощности вида:
S(t) = Sak d ( f - k fr ) + Sam d ( f-m fz ) + SS akm d [ f- (m fz ± k fr)] + SN (f) , [1.2]
содержащий:
• спектр низкочастотного и среднечастотного процесса с частотами,
кратными оборотной частоте fr ;
• спектр высокочастотного процесса с частотами, кратными
зубцовой частоте fz ;
• спектр комбинационных частот m fz ± k fr ;
• спектр шумовой компоненты SN (f).
• Методология диагностирования зарождающихся и развитых дефектов • 1—21 •
развитии дефектов типа выкрашивания, появления трещин и задира не позволяют с достаточной достоверностью определить вид дефекта. Спектр мощности, являясь усредненной энергетической характеристикой сигнала, годен лишь для распознавания предаварийных ситуаций, находящихся на грани катастрофических изменений в механизме.
Для выявления дефектов на ранней стадии необходимо привлекать более информативные характеристики, такие, например, как число выбросов сигнала в единицу времени, превышающих некоторое пороговое значение, глубина амплитудной и фазовой модуляции, спектр огибающей, кепстр.
Большинство методов диагностирования зарождающихся дефектов механизмов имеет в своей основе одну и ту же отправную диагностическую модель: развитие дефекта вызывает рост амплитуд и числа кратковременных импульсов в вибросигнале. Задача состоит в применении оптимального способа обработки сигнала, который сводит к минимуму влияние помех и позволяет однозначно соотнести полученную характеристику сигнала с видом дефекта.
Способы выделения информативных компонентов.
Характер изменения структуры вибросигнала при выявлении неисправности определяет способ его обработки для выделения информативного компонента, характеризующего изменение технического состояния объекта диагностирования.
В зависимости от типа агрегата и вида возникшего в нем дефекта используются различные способы увеличения отношения сигнал/помеха.
Если физика воздействия неисправности на колебания механизма связана с появлением амплитудной или фазовой модуляции, то исследуются свойства огибающей вибросигнала.
Появление в сигнале или усиление периодического компонента заставляют искать эффективный способ выделения периодического сигнала на фоне помехи, например, метод синхронного накопления.
Появление или усиление полигармонических колебаний можно уловить с помощью кепстрального анализа, сжимающего информацию об изменениях в сигнале до обозримого количества гармоник, амплитуды которых легко оценить количественно.
Возникновение и развитие дефектов в механизмах приводят к появлению нелинейных эффектов, использование которых для формирования диагностических признаков позволяет получить более ценную диагностическую информацию, чем на основе рассмотрения линейных динамических моделей. Для этой цели используют величины амплитуд комбинационных частот, глубину амплитудной модуляции или частотной девиации.
Перечисленные выше методы анализа виброакустических процессов позволяют сформировать характерные диагностические признаки зарождающихся дефектов даже в тех случаях, когда спектр мощности сигнала практически не меняется. При наличии инвариантности диагностических признаков гарантируется достоверность диагностирования даже на ранней стадии развития дефекта.
• Методология проведения диагностических виброизмерений роторных агрегатов • 2 — 2 •
значительные усилия, производя оценку состояния всего парка оборудования предприятия с использованием детального спектрального, кепстрального виброанализа, анализа огибающих и др., оптимально разработать для каждой конкретной группы агрегатов и ситуации индивидуальный подход распознавания состояния с использованием минимума необходимой для этого информации, а затем подвергать более детальному виброанализу только ту часть оборудования, состояние которой изменяется достаточно быстро.
Для решения этой задачи необходимо оборудование разделить на категории в зависимости от потенциальной возможности и значимости внеплановых отказов, а также сложности обслуживания. Как правило, большая часть роторных агрегатов может быть отнесена к одной из следующих пяти категорий:
• 1-я категория — критические основные агрегаты большой единичной мощности, где внеплановый отказ или авария сопровождаются значительными потерями продукции, серьезными экологическими последствиями и др.; в эту категорию включают, как правило, непрерывно эксплуатируемые безрезервные турбоагрегаты, компрессора и насосы единичной мощностью свыше 1 МВт;
• 2-я категория — критические основные агрегаты средней единичной мощности, где внеплановый отказ или авария сопровождаются значительными потерями продукции, серьезными экологическими последствиями и др.; в эту категорию включают, как правило, непрерывно эксплуатируемые безрезервные турбоагрегаты, компрессора и насосы единичной мощностью 0,2...1 МВт;
• 3-я категория — критические или, возможно, склонные к внеплановым отказам и авариям основные агрегаты со сложным ТО, где внеплановый отказ или авария подвергнет опасности остановки, но не прервет основное производство; в эту категорию включают, как правило, резервированные турбоагрегаты, компрессора и насосы единичной мощностью свыше 200 кВт;
• 4—я категория — критическое вспомогательное оборудование, требующее необременительного обслуживания; в эту категорию включают, как правило, компрессора и насосы единичной мощностью менее 200 кВт;
• 5—я категория — некритическое вспомогательное оборудование, технологические обвязки (трубопроводы, аппараты, арматура).
Оборудование 1 категории и наиболее ответственные позиции оборудования 2 и 3 категорий целесообразно оснащать стационарной аппаратурой контроля рабочих параметров, т.е. применять непрерывный контроль, позволяющий быстро распознать состояние и продиагностировать агрегат. Поскольку этот способ является дорогостоящим, в промышленной практике существует ограниченный ряд агрегатов, где непрерывный контроль может-окупить вложенные средства.
К ним относятся:
• критические агрегаты и агрегаты определяющие качество продукции: например, если внеплановый отказ приведет к дорогостоящему ремонту или к значительному снижению выпуска продукции, или если в производственных процессах повышенная вибрация оборудования может ухудшить качество продукции, то для таких агрегатов непрерывный контроль позволит быстро предупредить об изменении контролируемого параметра (уровня вибрации и др.), т.е. изменении состояния, что обеспечит персоналу предприятия возможность предвидеть развитие проблемы и принять необходимые меры до того, как будет нанесен экономический ущерб;
• пожаро— и взрывоопасные производства, и агрегаты в которых могут скоротечно развиваться катастрофические поломки, разрушающие сам агрегат или соседнее оборудование;
• Методология проведения диагностических виброизмерений роторных агрегатов • 2 — 4 •
документации машины и Регламенте проведения виброизмерений предприятия. Кроме того, должны быть указаны способы крепления преобразователей, технология прокладки электропроводки от вибродатчика к средствам диагностики и возможности использования других сигналов, например, сигналов частоты вращения роторов.
В связи с тем, что техническое обслуживание эксплуатируемых агрегатов иногда проводится по "непредусмотренным" при проектировании агрегата отказам, требуется реализация принципа адаптирования контролепригодности к отказам, возникающим в ходе эксплуатации.
Контрольные точки измерений вибрации.
Поскольку реакции механических систем на возбуждение механическими колебаниями определяются сложными физическими процессами, то при измерении даже на одном элементе агрегата в близких друг к другу точках ввода может наблюдаться различный характер исследуемых колебаний. Вышесказанное особенно актуально для высокочастотной составляющей вибросигнала, что часто определяется различными типами распространения высокочастотных колебаний по поверхности.
Важно производить замеры вибрации в одних и тех же местах, называемых контрольными (штатными) точками измерения вибрации.
Обычно, измерения параметров вибрации в контрольных точках производятся на подшипниковых опорах агрегата, корпусе агрегата и на анкерных фундаментных болтах.
Абсолютную вибрацию (при диагностировании большинства механических дефектов) рекомендуется измерять в трех взаимно перпендикулярных направлениях: вертикальном, горизонтально — поперечном и осевом. Преобразователи для измерения горизонтально —поперечной составляющей вибрации крепят на уровне оси вала против середины длины опорного вкладыша. Осевую составляющую вибрации следует измерять в точке, максимально приближенной к оси вала на корпусе опоры подшипника вблизи горизонтального разъема между крышкой и корпусом. Вертикальную составляющую вибрации измеряют на верхней части крышки подшипника над серединой его вкладыша.

Рис. 2—01. Типичные контрольные точки измерений вибрации на корпусе подшипника.
• Методология проведения диагностических виброизмерений роторных агрегатов • 2 — 6 •

Рис. 2—03. Рекомендуемые места крепления датчика.
В большинстве случаев целью измерений вибрации является контроль условий работы вала и подшипника. Датчик следует устанавливать так, чтобы на его рабочую поверхность непосредственно действовали механические колебания подшипника. Датчик 3 воспринимает механические колебания подшипника при меньшем влиянии вибрации, возбуждаемой другими узлами и деталями агрегата, по сравнению с датчиком 4, который воспринимает преобразованные при прохождении через разъемное соединение колебания подшипника и механические колебания, генерируемые другими узлами агрегата. Аналогично, датчик 1 расположен более целесообразно с точки зрения распространения механических колебаний, чем датчик 2. Измерение вибрации на тонкостенных участках корпусов и крышек недопустимо.
Способы крепления датчика на поверхности.
Качественное и надежное крепление вибродатчика на поверхности исследуемого объекта является одним из самых важных условий достижения точных и надежных результатов при измерениях вибрации и распознавании состояния оборудования.
Ненадежное крепление датчика приводит к уменьшению области линейности амплитудной характеристики датчика, и, следовательно, значительному уменьшению диапазона измерений акселерометра.
При проведении измерений измерительный кабель не должен подвергаться интенсивным колебаниям и должен быть удален (по мере возможности) от источников сильных электромагнитных полей.
Наилучшим считается крепление датчика на гладкой плоской поверхности ввода прочной стальной шпилькой. На рабочую поверхность датчика рекомендуется наносить слой консистентной (силиконовой) смазки, что увеличивает общую жесткость механического соединения датчика и объекта измерений и создает хороший акустический контакт.
Глубина резьбового отверстия должна быть достаточной, чтобы шпилька не упиралась в дно отверстия в основании датчика. В соответствии с рекомендациями ISО 1101 — 1969 поверхность для крепления датчика должна удовлетворять следующим условиям :
• шероховатость поверхности — не более 1,6 мкм ;
• неперпендикулярность оси резьбового соединения к плоскости крепления преобразователя — не более 0,02 % ;
• Методология проведения диагностических виброизмерений роторных агрегатов • 2 — 8 •
для датчиков массой не более 20 г при виброускорениях с амплитудами (диапазон измерений) до 100 м/с2. При креплении пьезодатчика при помощи воска необходим определенный опыт, иначе этот метод крепления может оказаться ненадежным.
Широкое распространение в силу простоты и дешевизны нашло крепление датчиков на гладкой поверхности объекта с помощью постоянного магнита. При этом статическая сила сцепления магнита с измерительной поверхностью во многом влияет на диапазон измерений. Требования к обработке поверхности те же что и для шпилечного соединения.

Рис. 2—06. Амплитудно-частотная характеристика пьезодатчика при применении для крепления датчика постоянного магнита.
Резонансная частота в этом случае уменьшается примерно до 7... 15 кГц и зависит от типа магнита. То есть, этим методом можно пользоваться при измерении и анализе вибрации с верхним пределом частотного диапазона измерений 2...5 кГц.

Рис. 2—07. Амплитудно-частотная характеристика пьезодатчика при применении щупа.
Наиболее простым и быстрым является измерение вибрации с помощью щупа, соединенного с вибродатчиком. Однако, рабочий частотный диапазон при этом в большинстве случае составляет примерно 10...1000 Гц.
Угол между измерительной осью вибродатчика и направлением измерения на должен превышать 25 градусов. Следует также учитывать, что
• Методология проведения диагностических виброизмерений роторных агрегатов • 2 — 10 •
вращения ротора. Таким образом, ширина каждой частотной полосы автоматически регулируется во время сбора данных на основе фактической частоты вращения ротора агрегата.
При плановых остановах рекомендуется записывать частотные характеристики на выбеге и/или пуске агрегата. Текущие данные измерения вибрации необходимо сравнивать с записанными ранее. При сравнении однотипных данных, полученных в разное время, легко зафиксировать любое изменение резонансных частот и амплитуд, которое может указывать на происходящие изменения в системе ротор — опора — фундамент.
Весьма важным при приведении мониторинга состояния оборудования может оказаться периодический анализ изменений фазы вибрации на частоте вращения ротора. Фазовое окно должно быть установлено таким образом, чтобы учесть возможные изменения режима. Для установки пределов такого окна может потребоваться накопление статистических данных, т.е. проведение нескольких замеров вибрации.
Хотя анализ частотных и фазовых характеристик имеет важное значение, цена их сбора и анализа в качестве текущей задачи периодического вибромониторинга может оказаться недоступной в силу различных причин (экономические ограничения, отсутствие персонала, сложность измерений). Сбор этих характеристик, вероятно, будет экономически оправдан только для тех агрегатов, которые находятся в критическом состоянии и/или имеют хроническую историю отказов. Сбор и анализ таких данных при периодическом мониторинге для всего парка оборудования предприятия противоречит философии ОФС, заключающейся в анализе большой совокупности информации для выделения нескольких "возмутителей спокойствия", нужде ющихся в детальном анализе.
Проведение измерений.
Подготовка к проведению измерений.
При развертывании системы периодического мониторинга оборудования или включении дополнительного агрегата в число диагностируемых по параметрам вибрации необходимо оборудование точек измерения вибрации. Точки измерения обычно назначаются в соответствии с Регламентом предприятия. Требования к оборудованию точек измерений описано ранее.
Механики и/1ли операторы цехов (установок, станций) должны иметь карты регистрации уровней вибрации диагностируемого оборудования, содержащие нормируемые уровни вибрации и перечень регистрируемых сопровождающих технологических параметров. Карты регистрации уровней вибрации разрабатываются и распространяются службой Технической диагностики.
Проведение измерений.
Диагностические измерения и исследования вибрации оборудования можно условно разделить на следующие виды: контрольные измерения работающего агрегата, специальные диагностические измерения работающего агрегата, а также обследование остановленного агрегата.
Контрольные измерения предназначены для распознавания и прогнозирования технического состояния агрегата с учетом влияния на состояния технологических режимов эксплуатации оборудования. Контрольные измерения в свою очередь можно разделить на текущее контрольное измерение вибрации и полное контрольное измерение вибрации.
Специальные диагностические измерения и обследование остановленного агрегата предназначены для выявления дефектов и причин их возникновения, оценки и прогнозирования степени развития дефектов и разработки рекомендаций по их устранению.
• Методология проведения диагностических виброизмерений роторных агрегатов • 2 — 12 •
Полное контрольное измерение вибрации должно включать в себя опрос эксплуатационного персонала, при необходимости ознакомление с документацией на оборудование, осмотр агрегата, подготовку виброаппаратуры и проведение измерения вибрации, составление отчетной документации.
Опрос обслуживающего персонала необходим для прояснения следующих вопросов:
• если были, то когда и при каких обстоятельствах обнаружены признаки изменения состояния агрегата (в процессе эксплуатации, после проведения капитального или текущего ремонта);
• характер изменения параметров вибрации, температуры, условий эксплуатации и др. при этом;
• какие приняты меры по обеспечению безопасности агрегата: агрегат остановлен, оставлен в эксплуатации с ограничениями по нагрузке (производительности) и т.д.
Если изменению вибрации предшествовал ремонт агрегата, должны быть рассмотрены монтажные и ремонтные формуляры, отчетные документы и технические акты, имеющие отношение к вибрации. При необходимости рассматриваются также чертежи агрегата. При ознакомлении с документацией необходимо определить соответствие зазоров и натягов в подшипниках, а также параметров центровки рекомендуемым значениям, выяснить изменение амплитуд вибрации во времени и в зависимости от режима работы агрегата.
При осмотре агрегата обращают внимание:
• вызывает ли что —либо опасения (необычные шумы или звуки, вибрация трубопроводов, стола фундамента и др.);
• имеются ли разливы или потеки технических жидкостей (смазок, охлаждающих) вокруг агрегата или подшипников, замасливание фундамента;
• имеются ли нарушения или трещины конструкции;
• имеются ли утечки (продуктов);
• проверяют соответствие показаний термометров, манометров, вольт— и амперметров и других датчиков рекомендуемым нормам.
Полное контрольное измерение вибрации производятся без вмешательства в режим эксплуатации агрегата и, в основном, ограничивается измерением трех составляющих вибрации в контрольных измерительных точках (как правило на опорах). Иногда в контрольные измерительные точки включают точки основания (рамы, фундаментных болтов), статора и других частей агрегата, в которых вибрация измеряется только в случае достижения значением параметра вибрации какой —либо из контрольных точек установленного допустимого значения.
Если повышенная вибрация возникает при определенном режиме, то для периодического обследования выбираются два режима: с нормальной и повышенной вибрацией.
В тех случаях, когда вибрация локализуется на одном подшипнике или части фундамента, или консольной части ротора, необходимо произвести измерения в дополнительных точках (например, снятие контурной характеристики вибрации).
Полное контрольное измерение позволяет распознать состояние агрегата, выяснить наиболее вероятные причины вибрации и при необходимости построить последующие работы таким образом, чтобы выделить из группы вероятных действительную причину.
Специальные диагностические обследования.
Если по результатам полного контрольного измерения вибрации агрегата не удается однозначно установить причины повышенной вибрации, то
• Методология проведения диагностических виброизмерений роторных агрегатов • 2—14 •
Периодичность измерений вибрации.
В большинстве случаев период развития механических дефектов агрегата, прежде чем последний окажется в предельном состоянии, достаточен для их обнаружения средствами и методами периодического вибромониторинга. Период развития дефекта зависит от многих факторов (например, от вида износа) и может составлять от нескольких минут или часов (при заедании) до многих месяцев (при абразивном износе). Поэтому интервал периодических измерений вибрации обычно выбирают исходя из перечня контролируемых дефектов и режима эксплуатации оборудования. В большинстве случаев интервал, составляющий 7...30 дней, считается достаточными для своевременного распознавания изменения состояния при развитии большинства механических дефектов агрегатов. Однако, резкое изменение состояния агрегата иногда может произойти и значительно быстрее, чем за один месяц: это могут быть дни, минуты и даже секунды. Вероятность проведения виброизмерений именно в этот момент невелика, в силу чего для критичного оборудования устанавливают стационарные системы для постоянного вибромониторинга и/или значительно сокращают интервалы между сбором данных.
Только стационарная система контроля вибрации может с большой вероятностью исключить аварию. В то же время, при проведении стационарного контроля, данные, собранные с применением систем периодического мониторинга, например, в случае появления проблемы, могут помочь организовать правильную работу оборудования (или персонала) до момента останова агрегата. Такие решения принимаются от случая к случаю по соображениям безопасности и экономическим последствиям различных вероятных исходов.
Исходя из рекомендаций РДИ (см. сноску 1) и опыта авторов и группы их коллег по минимизации внеплановых отказов и проведения периодического мониторинга на предприятиях химпрома, энергетики и трубопроводного транспорта, можно дать несколько рекомендаций, которые в большинстве случаев позволяют своевременно обнаружить значительные изменения состояния агрегатов с вращающимся ротором.
Различают несколько этапов проведения виброизмерений: после ремонта и монтажа, после завершения процесса приработки, на начальном этапе эксплуатации, в процессе эксплуатации, после нарушений технологического режима, после изменения состояния агрегата и перед остановкой агрегата на ремонт.
Виброизмерения после ремонта и монтажа.
В процессе послеремонтных испытаний агрегата или сразу же после выхода агрегата на рабочий технологический режим проводят полные контрольные измерения с целью оценки качества проведения ремонта и распознавания состояния агрегата по параметрам вибрации. В этот период рекомендуется у оборудования 1 и 2 категорий регистрировать собственные частоты. В случае некачественно проведенного ремонта, при оценке состояния агрегата "требует принятия мер", агрегат следует остановить для проведения повторного ремонта. В базе данных ЭВМ необходимо описать проведенный ремонт.
Виброизмерения после завершения процесса приработки.
Полные контрольные измерения проводятся спустя 3...5 суток после выхода агрегата на технологический режим. Если текущие уровни вибрации в контрольных точках ниже уровней "нормального" состояния, то агрегат принимается в эксплуатацию.
В этот период оптимально минимизировать число точек для проведения текущих контрольных измерений. Уровни и спектры вибрации, зарегистрированные на этом этапе следует принимать в качестве опорных (эталонных). Если текущий уровень вибрации одной из точек выше
• Методология проведения диагностических виброизмерений роторных агрегатов • 2 — 16 •
Средства сбора и обработки данных.
Требуемый при проведении работ по периодическому вибромониторингу современный комплекс средств измерений и диагностики (измерительная система) состоит из следующих частей: аппаратные средства измерений (приборы для измерения и анализа вибрации), вспомогательные устройства и каналы связи, программное обеспечение для обработки измеренной информации и ЭВМ. В настоящем разделе текущей главы рассматриваются средства измерений вибрации и программное обеспечение ЭВМ.
Вибрация измеряется, контролируется и анализируется в большинстве случаев с применением двух типов аппаратуры: стационарной и переносной (мобильной). Применяемые передвижные вибролаборатории условно включены в мобильные средства.
Стационарная аппаратура.
Стационарная аппаратура контроля состояния оборудования применяется для непрерывного контроля параметров вибрации, температуры, давления, числа оборотов и др. Стационарная аппаратура делится на два основных класса: контрольно — сигнальная аппаратура (контроля текущего уровня параметра) и аппаратура для мониторинга (анализа тенденций изменения параметра). Первая служит для сигнализации или отключения агрегата при превышении контролируемым параметром (в т.ч. вибрацией) некоторых пороговых уровней (например, допустимых значений вибрации). Вторая позволяет анализировать тенденции и проводить диагностику, т.е. выявлять причины изменения состояния агрегата. Как правило, аппаратура непрерывного мониторинга в качестве основы содержит в своем составе контрольно — сигнальную аппаратуру.
Контрольно — сигнальная аппаратура включает следующие составные части: первичный вибропреобразователь (датчик), крепящийся на контролируемом объекте, предусилитель, соединительный кабель, вторичный блок контроля.
Вторичный блок может располагаться в непосредственной близости от агрегата (полевое исполнение) или выноситься в операторную (щитовое исполнение). Вторичный блок служит для индикации, сигнализации или отключения агрегата в случае достижения уровнем вибрации уровней аварийных уставок. Обычно аппаратура может:
• измерять СКЗ (амплитуду, размах) виброскорости (виброперемещения) полигармонической вибрации с непрерывной индикацией в аналоговой (цифровой) форме, как правило, на передней панели;
• индицировать значение контролируемого параметра, соответствующее предупредительному и аварийному уровням вибрации;
• индицировать состояние превышения предупредительного или аварийного уровней вибрации;
• управлять внешними устройствами при превышении предупредительного или аварийного уровня вибрации.
Аппаратура для мониторинга, кроме вышеупомянутых блоков, обычно включает компьютерный блок, содержащий программное обеспечение, позволяющие собирать, хранить, обрабатывать и отображать информацию по алгоритмам мониторинга.
Переносная аппаратура.
Переносная аппаратура применяется для периодического контроля и мониторинга уровней измеряемых параметров. Переносная аппаратура условно может быть разделена на два класса: аппаратура для измерения общего уровня вибрации (виброметры) и аппаратура для измерения, сбора и анализа вибрации (виброанализаторы и сборщики данных).
• Методология проведения диагностических виброизмерений роторных агрегатов • 2 — 18 •
Рассмотрим подробнее пьезодатчики. Пьезодатчик является универсальным вибродатчиком, в настоящее время применяемым почти во всех областях измерения и анализа вибрации в промышленности. Эксплуатационные параметры пьезодатчиков в общем случае лучше, чем у любого другого типа вибродатчиков. Пьезодатчики отличаются широким рабочим динамическим и частотным диапазонами измерений, прочной конструкцией, надежностью и высокой стабильностью параметров.
Так как пьезодатчики являются активными датчиками, генерирующими пропорциональный ускорению механических колебаний электрический сигнал, при их эксплуатации не требуется источник питания.
Отсутствие движущихся элементов конструкции исключает возможность износа и гарантирует исключительную долговечность пьезодатчиков. Отметим, что отдаваемый пьезодатчиком сигнал, пропорциональный ускорению, можно интегрировать с целью измерения и анализа виброскорости и виброперемещения механических колебаний.
Основной частью пьезодатчика является чувствительный элемент из пьезоэлектрического материала, в качестве которого используется искусственно поляризованная ферроэлектрическая керамика. Подвергаемый действию силы (при растяжении, сжатии или сдвиге) пьезоэлектрический материал генерирует на своих поверхностях, к которым прикреплены электроды, электрический заряд, пропорциональный воздействующей силе.
Конструкция датчика предусматривает наличие инерционной массы, воздействующей на пьезоэлемент с силой, пропорциональной ускорению механических колебаний в соответствии с законом Ньютона, согласно которому сила равна произведению массы и ускорения.

Рис. 2—08. Конструкция пьезодатчика.
На частотах, значительно меньших резонансной частоты общей системы масса — пружина (см. рис. 2 — 08 ) ускорение инерционной массы совпадает с ускорением его основания и, следовательно, отдаваемый пьезодатчиком электрический сигнал пропорционален ускорению воздействующих на него механических колебаний.
Представленный на рынке широкий ассортимент вибродатчиков способен удовлетворить различные запросы пользователя. При приобретении определенного типа датчика всегда приходится выбирать компромиссное решение с учетом стоимости, порога чувствительности и предела измерений акселерометра, частотного диапазона измерений и размеров, расположения
• Методология проведения диагностических виброизмерений роторных агрегатов • 2 — 20 •

Рис. 2—09. Коэффициент преобразования акселерометра и рабочий диапазон в зависимости от размеров пьезоэлемента при прочих равных условиях.
• широкий диапазон измерений, т.е. способность акселерометра работать в области как высоких, так и низких уровней вибрации; нижний предел диапазона измерений чаще определяется не характеристиками пьезоэлемента, а качеством соединительных кабелей и разъемов, усилительными каскадами и электрическим шумом (для работы в области особо низких частот применяются специальные сейсмодатчики); верхний предел диапазона измерений акселерометра определяется прочностью его конструкции и способами его крепежа;
• размеры и собственная масса (миниатюрность), т. е. возможность применения акселерометра для измерения вибрации труднодоступных мест и легких объектов; важно следовать правилу, что масса вибродатчика не должна превышать десятую часть динамической массы объекта, на котором он закреплен.
В области резонанса нарушается пропорциональность между выходным электросигналом пьезодатчика и ускорением механических колебаний исследуемого объекта. При измерении вибрации в широкой полосе частот попадание резонансной частоты акселерометра в анализируемую частотную полосу приводит к ошибочным результатам, особенно если измеряемый процесс содержит составляющие с частотами в области резонанса акселерометра. Решением этой проблемы является использование фильтров нижних частот, как правило устанавливаемых в предусилителях.
Предусилители.
Подключение нагрузки (даже с относительно большим импедансом) непосредственно к выходу пьезоэлектрического акселерометра может быть причиной значительного уменьшения его коэффициента преобразования и сужения его частотного диапазона измерений. Чтобы уменьшить до минимума это нежелательное влияние нагрузки, вместе с акселерометром используется
• Методология проведения диагностических виброизмерений роторных агрегатов • 2 — 22 •
неравномерность АЧХ измерительного тракта в полосе частот до 1000 Гц. Фильтр верхних частот имеет срез на частотах ниже 10 Гц. На выходе интегратора вырабатывается напряжение, пропорциональное виброскорости. Далее детектор СКЗ преобразует это напряжение в напряжение постоянного тока и затем постоянное напряжение, пропорциональное СКЗ виброскорости поступает на индикатор. Одновременно производится сравнение сигнала с аварийными уставками, в случае превышения которых срабатывает предупредительная или аварийная сигнализация.

Рис. 2—11. Структурная схема вторичного блока контроля вибрации.
Если вторичный блок контроля вибрации имеет интерфейс для соединения с ЭВМ, то появляется возможность компьютерного мониторинга состояния оборудования.
Ввиду разнообразия и сложности конструкций компьютерных блоков, мы не будем подробно останавливаться на их особенностях, выходящих за рамки идеи настоящей книги, и рекомендуем при выборе оборудования пользоваться услугами квалифицированных специалистов в области вибродиагностики и мониторинга. Компьютерный блок, управляемый программным обеспечением, позволяет собирать данные измерения вибрации от группы контрольных точек агрегата в синхронном или асинхронном режимах, хранить их с помощью дисковых накопителей в больших объемах, обрабатывать и отображать данные измерения вибрации во временной и частотной областях и наблюдать за изменением параметров вибрации по алгоритмам мониторинга. Основным отличием от контроля СКЗ виброскорости в этом случае будет способность наблюдать за изменениями отдельных спектральных составляющих с течением времени и создавать индивидуальные пределы тревожной сигнализации (уставки) для отдельных параметров вибросигнала. Более детально возможности программного обеспечения рассмотрены в соответствующем разделе.
Переносные виброметры.
Приведенная на рис. 2—12 структурная схема иллюстрирует конструкцию и принцип действия виброметра. Пьезодатчик соединяется с усилителем заряда (напряжения), образующим входной каскад измерительного средства, отличающийся высоким импедансом. В этом случае отпадает необходимость применения внешнего предусилителя. Если применяется усилитель заряда, то появляется возможность применения относительно длинного кабеля без заметной потери чувствительности.
• Методология проведения диагностических виброизмерений роторных агрегатов • 2 — 24 •
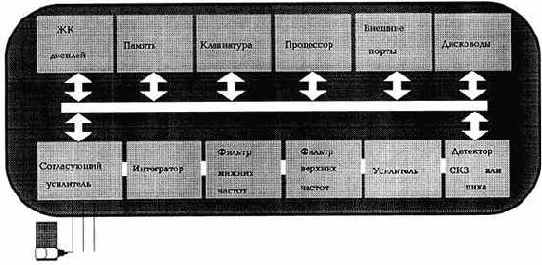
Рис.2—13. Структурная схема сборщика данных.
Приведенная на рис. 2—13 структурная схема иллюстрирует принцип действия сборщика данных. Пьезодатчик соединяется со входным согласующим усилителем заряда (напряжения) или может иметь собственный предусилитель, питание которого осуществляется от сборщика данных. Входной усилитель с переменным коэффициентом усиления должен обеспечивать подключение внешних источников сигналов не только со стандартными (контрольными) выходами.
В этом случае обеспечивается подключение сборщика данных к контрольно — сигнальной аппаратуре, термометрам, толщиномерам и др., и непосредственно к некоторым типам не вибрационных датчиков, например таким, как токовый пробник, микрофон, стробоскоп или штрих —сканер. Обычно сборщик данных автоматически сканирует входной сигнал и устанавливает пределы измерений для максимизации разрешающей способности динамического АЦП (12...14 бит, 72...80 дБ).
Сборщик данных обычно содержит включаемые по желанию оператора каскады аналоговых интеграторов и фильтров верхних и нижних частот, которые можно настраивать согласно требованиям к измерению. В то же время может обеспечиваться и цифровая фильтрация и интегрирование.
Современный сборщик данных может предоставить следующие возможности анализа: отображение в реальном времени и хранение формы сигнала, спектра, каскадного спектра, третьоктавного спектра (со взвешиванием или без), орбиты, диаграмм Боде, диаграммы Найквиста, кепстра, спектра огибающей и др.. Он должен осуществлять проведение синхронного накопления. Должна быть обеспечена возможность запуска от внешнего источника.
Важнейшей функцией сборщика данных является способность загрузки маршрутов обхода и уровней тревог (для оперативного распознавания состояния на месте измерения) из базы данных, хранящейся на ПЭВМ. При этом должна обеспечиваться возможность выбора маршрутов обхода, отдельных агрегатов и точек и т.д. После проведения измерений на месте должна обеспечиваться возможность оперативного просмотра данных о состоянии агрегатов и сигнализация о превышении текущим уровнем контролируемого параметра уровня той или иной тревоги, как в частотной полосе, так и по общему уровню. Некоторые модели сборщиков данных позволяют на месте оценивать состояние подшипников качения.
• Методология проведения диагностических виброизмерений роторных агрегатов • 2 — 26 •
База данных должна содержать несколько иерархически связанных уровней (для быстроты доступа) организации хранения данных.
Например, возможна трехуровневая организация (см. рис. 2—14):
• станция (производство, цех, установка): верхний уровень иерархии, состоящий из групп агрегатов, объединенных по физическому, функциональному, территориальному или другим признакам;
• агрегат: средний уровень иерархии, состоящий из привода и исполнительного механизма;
• точка: нижний уровень иерархии — контрольные точки на агрегате, где производятся измерения вибрации; все точки измерений одного агрегата группируются в составе соответствующего агрегата.
В базе данных должна также содержаться информация о параметрах анализа вибрации, уровнях тревог и частотах неисправностей.
Функция создания и управления маршрутами обхода оборудования при проведении измерений вибрации.
Эта функция позволяет создавать маршруты обходов агрегатов для проведения измерений вибрации. Агрегаты группируются в удобную для обхода схему. В дальнейшем маршрут измерения может загружаться в сборщик данных для проведения измерений. Программа должна позволять пользователю любые изменения (добавление, удаление, переупорядочение, и т.д.) для модифицирования соответствующих маршрутов.
Функция обмена данными между ЭВМ и сборщиком данных.
Эта функция осуществляет обмен данными между ЭВМ и сборщиком данных. Обычно сначала в сборщик данных с ЭВМ оператор загружает созданные в БД ЭВМ маршруты обхода измерительных точек и различной дополнительной и служебной информации. После проведения измерений собранная информация, хранимая в сборщике данных, разгружается в базу данных ЭВМ. Желательно, чтобы данная программа позволяла использовать МОДЕМ для передачи информации от удаленных объектов по телефонной линии.
Функция визуализации данных измерения вибрации.
Данная функция должна обеспечивать специалисту произвольный выбор данных, собранных и хранящихся в БД ЭВМ, и вывод этих данных в требуемом формате на дисплей или печать, а также обеспечивать диагностические функции, позволяющие распознавать вибросостояние агрегата.
Функция визуализации данных измерения вибрации используется, когда необходимо исследовать временные и частотные характеристики вибросигнала и тенденции их изменения. В частности должно обеспечиваться:
• отображение формы сигнала по одной или нескольким точкам измерений;
• отображение частотного спектра (по возможности и спектра огибающей) по одной или нескольким точкам измерений;
• отображение кепстра по одной или нескольким точкам измерений;
• по возможности отображение векторных диаграмм, орбит, частотных характеристик, каскадных спектров и др.;
• сравнение сигналов;
• отображение тенденций изменения (трендов) измеренных параметров;
• сигнализацию при превышении текущей вибрацией установленных уровней тревог.
• Методология проведения диагностических виброизмерений роторных агрегатов • 2 — 28 •
числом плоскостей коррекции и при различной частоте вращения ротора. При балансировке требуется измерение амплитуды и фазы вибрации.
Программа центровки агрегата позволяет вычислять требуемые смещения для правильной состыковки нескольких узлов агрегата одновременно. При этом обычно учитываются влияния температуры на линейные расширения опор.
Автоматизированная диагностика.
Такая функция обеспечивает сканирование собранных в базе данных, распознавание состояния оборудования, извлечение оборудования с признаками "тревожного" состояния, анализ и перечень предполагаемых развивающихся или развитых дефектов и соответствующих решающих правил. Другими словами, при работе такой программы сканируется файл с измерительной информацией, содержащий данные об агрегатах и вибрации, выбираются агрегаты с повышенной вибрацией, анализируется и диагностируется их состояние, предоставляет перечень вероятных дефектов. Обычно сканирование автоматизируется так, что диагностический отчет может генерироваться для выбранного агрегата, маршрута агрегатов, станции (установки) или всех агрегатов базы данных. Отчет может состоять из графиков, распечатки извлеченных особенностей, распечатки диагностических данных и т.д.
• Организация периодического мониторинга технического состояния оборудования • 3 — 2 •
спектра. Это позволяет пользователю анализировать текущие изменения общего уровня вибрации, формы сигналов, спектры, кепстры, вектора гармонической вибрации, частоты вращения ротора, давления, напряжения, тока и других параметров, а также их хранить. Типичный сборщик данных при весе 1...2,5 кг имеет запоминающее устройство, способное хранить данные, измеренные на сотнях измерительных точек. Кроме того, сборщики данных могут выполнять синхронное временное и другие виды усреднения сигнала, сбор данных с запуском от внешнего источника, сбор данных на выбеге и разгоне (диаграммы Боде, Найквиста и каскадные спектры).
Сборщики данных также используются для многоплоскостной многоскоростной балансировки при помощи загружаемых балансировочных программ, а иногда и для центровки.

Рис.3—01. Технические компоненты и шаги вибромониторинга.
Современные технологии мониторинга нацелены на совместное использование сборщика данных и анализирующей программы в базовом компьютере. Для передачи данных между сборщиком данных и базовым компьютером обычно используется стандартный канал связи, например, последовательный порт RS232. Информация, отображаемая на дисплее сборщика данных, также может быть распечатана на принтере с применением последовательного порта RS232. Связь между сборщиком данных и базовым компьютером осуществляется либо напрямую через указанный порт, либо с помощью МОДЕМа по телефонной линии. Например, при скорости передачи в 9600 Бод (пропускная способность обычной телефонной линии), спектр вибрации с 400 частотными составляющими может быть передан в базовый компьютер меньше, чем за одну секунду.
Основой компьютеризированного мониторинга является программное обеспечение, устанавливаемое на базовом компьютере.
Использование программного обеспечения предусматривает:
• создание и заполнение базы данных оборудования, содержащей информацию о каждом агрегате (его компонентах и точках измерения), подвергаемом периодическому мониторингу, служебную информацию, маршруты обхода оборудования и др.;
• определение параметров анализа данных для обеспечения гибкости выбора метода анализа, который будет использоваться на конкретных измерительных точках агрегата, а также определение предельно допустимых значений параметров анализа данных;
• обмен информацией между ЭВМ и сборщиком данных (загрузка маршрутов обхода оборудования и разгрузка собранных виброданных в базу);
• Организация периодического мониторинга технического состояния оборудования • 3 — 4 •
проведения всех запланированных измерений на маршруте, собранные в сборщике данные "разгружаются" в компьютер для анализа. Опыт показывает, что целесообразно построить работу на маршрутах таким образом, чтобы в течение рабочего дня техник мог охватить измерениями максимальное количество измерительных точек, число которых может составлять от 200 до 600 и более.
Специалист по диагностике, применяя программное обеспечение на компьютере и используя последовательности управляемых с помощью меню операций, производит анализ собранных данных с целью определения (распознавания) состояния обследованных агрегатов. В рамках вибромониторинга возможны два (применяемых в большинстве случаев совместно) метода, при помощи которых производится оценка состояния оборудования:
• анализирующее программное обеспечение под управлением специалиста, имеющее встроенные программируемые автоматические модули, в автоматизированном режиме сравнивает текущие уровни контролируемых параметров (вибрации, температуры и др.) с предельными, и, в случае достижения текущим уровнем контролируемого параметра предельного уровня, предупреждает о точках агрегата (агрегатов), параметры которых превышают нормы, принятые в промышленности, или рекомендуемые заводом — изготовителем оборудования, или установленные экспертом по вибродиагностике;
• анализирующее программное обеспечение строит тренды параметров и прогнозирует состояние агрегата, автоматически предупреждая о том, на каком оборудовании имеются тенденции к опасному постоянному возрастанию измеряемых параметров; параметры, используемые для оценки состояния оборудования, могут изменяться в соответствии с индивидуальными особенностями конкретного агрегата.
В случае, если требуется проведение виброанализа, инженер, имеющий квалификацию в области вибродиагностики, при помощи программного обеспечения производит анализ измеряемых параметров вибрации (форм сигналов, спектров и др.) оборудования и выдает заключение о возможности дальнейшей его эксплуатации и ТО (кроме того, имеются экспертные программные пакеты, т.н. искусственный интеллект в области вибрации, работающие в автоматизированном режиме и проводящие "черновой" предварительный анализ, что, с одной стороны, экономит время, а с другой — обеспечивает доступ к накопленным знаниям и опыту большинства авторитетных специалистов в виброанализе и позволяет пополнить собственные представления и опыт основами накопленного знания). По данным анализа планируются сроки проведения ТО. Программное обеспечение в автоматическом режиме может генерировать различные формы отчетной документации.
Особый интерес представляют архив и отчеты об истории проведения работ по ТО агрегатов, обнаруженным дефектам, затратам на ремонт и экономии средств. Именно они служат доказательством эффективности ОФС и позволяют расширять применение различных технологий мониторинга на предприятии.
Хотя даже первое измерение обычно позволяет провести оценку состояния агрегата, для построения трендов и прогнозирования изменений параметров вибрации требуется несколько замеров. По мере накопления данных уточняются предельные значения параметров вибрации и повышается вероятность достоверного прогнозирования изменений вибрации агрегата. Обычно первый замер показывает, что 10...40% оборудования нуждается в немедленном техобслуживании.
Пути реализации программы периодического вибромониторинга.
Путь первый — использование услуг сторонней сервисной организации, имеющей соответствующую лицензию и опыт, для проведения работ в области вибромониторинга.
• Организация периодического мониторинга технического состояния оборудования • 3 — 6 •
Стадия 4.
Добавление возможности анализа огибающих, каскадного анализа, по возможности, гребенчатой фильтрации, записи длительных временных сигналов и др.
Стадия 5.
Дооснащение различными дополнительными принадлежностями, такими, как различные (трехкомпонентные, высокочастотные, низкочастотные) вибродатчики, токовые клещи, дистанционные термометры, микрофонный комплект, преобразователи нагрузка — напряжение и др.
Стадия 6.
Полная система поверки (калибровки). Динамический вибростенд для калибровки в широком диапазоне частот.
Стадия 7. Добавление возможности многоканального анализа и многоканальной длительной записи вибросигналов с применением двух— или многоканального виброанализатора. Дополнительные предусилители и датчики, в случае надобности.
Первая стадия может быть вообще пропущена или несколько стадий могут быть выполнены одновременно, например, вторая, четвертая и пятая стадии. Однако, если проходятся все семь стадий, то, по мере прогресса в обучении и практике, формируется единый комплекс взаимодействующих инструментов и методов. Самая большая ошибка, которая может быть сделана, — это попытаться сделать слишком много и слишком быстро.
Капитальные затраты на организацию вибромониторинга.
Опыт показывает, что приемлемый уровень начальных капитальных вложений для типичного промышленного предприятия в средства измерений для периодического мониторинга должен составлять не более 1% стоимости оборудования, предназначаемого к мониторингу. В этом случае, как правило, отношение затраты/прибыль при хорошо организованном обслуживании по фактическому техническому состоянию достигает приблизительно 1:5, т.е. рентабельность составляет 500%. По данным Заепййс А11ап1:а и ежегодно публикуемым сведениям Министерства энергетики США, в электроэнергетике в целом при средних ежегодных удельных затратах на проведение планово — профилактического технического обслуживания механического оборудования 11 $/Вт, в случае внедрения ОФС происходило снижение этих затрат не менее, чем на 1 $/Вт, т.е. примерно на 10%; в нефтехимической промышленности, соответственно, затраты на ППР — 15 $/Вт, ОФС — 12 $/Вт, т.е. снижение на 25...30%. Наибольший эффект наблюдается на флоте, особенно военно-морском, где затраты снижаются на 35...40%.
Аналогичные результаты наблюдаются и в России.
Затраты при внедрении переносных средств измерений периодического мониторинга значительно варьируются в зависимости от выбранного пути. Единовременные затраты на программное обеспечение для реализации вибромониторинга на предприятии обычно составляют 5000...25000$, сборщик данных — 5000...12000$, ЭВМ и дополнительное оборудование — 25...50% стоимости сборщика данных. Кроме того, требуются затраты на содержание инженера и техника, помещение и расходные материалы. Приведенных выше затрат достаточно для первой попытки реализации разумного сочетания различных видов ТО, и не должно быть неожиданностью, если годовой экономический эффект от этого в 10 раз превысит стоимость оборудования для вибродиагностики.
• Организация периодического мониторинга технического состояния оборудования • 3 — 8 •
ряда его технических параметров, но и на основе анализа изменений измеренных параметров предсказывать необходимость и планировать сроки проведения ремонта, т.е. проводить ремонт только тех агрегатов, где он необходим. Такой вид обслуживания называется "предупредительным", или обслуживанием по фактическому техническому состоянию (в дальнейшем ОФС). Достоинством такого метода обслуживания является минимизация ремонтных работ (исключение ремонта бездефектных узлов) и увеличение на 25...40% межремонтного ресурса по сравнению с ППР. Серьезным недостатком такого вида обслуживания может быть ситуация, когда необходимость в проведении ремонтных работ на нескольких агрегатах одновременно превысит возможности ремонтной службы.
Проактивное техническое обслуживание (в дальнейшем ПАО) — подход, направленный на снижение общего объема требуемого технического обслуживания и максимизацию срока службы оборудования (т.е. в идеале — создание "вечного" агрегата, не требующего технического обслуживания) путем систематического устранения источников дефектов, приводящих к преждевременному выходу оборудования из строя. Другими словами, по результатам обобщения наиболее часто встречающихся дефектов, выявляемых в процессе работы оборудования, проводится анализ и определение причин их возникновения и влияния на межремонтный интервал, а затем принимаются меры по недопущению возникновения этих дефектов.
В частности, производится постоянный анализ работы ремонтного персонала и выявляются недостатки работы той или иной бригады, проявляющиеся на группе агрегатов (например, некачественная сборка, центровка или балансировка), анализ работы ремонтного производства с выявлением недостатков ремонтных технологий (например, технологии изготовления подшипников скольжения), анализ оснащенности (например, отсутствие оснастки по нагреву подшипников качения при монтаже), конструктивные изменения (например, применение износостойких материалов) и
др.
Характерные особенности влияния различных подходов к техническому обслуживанию на производственный процесс и межремонтные интервалы представлены в таблице 3 — 01.
Таблица 3-01.
Вид технического обслуживания |
Характерные особенности |
Реактивное (реагирующее) обслуживание |
Повышенная вероятность значительных внеплановых остановок оборудования и перебоев в работе |
Планово — профилактическое обслуживание |
Всеобъемлющее обслуживание оборудования для профилактики внеплановых остановов и сбоев в работе |
Обслуживание по фактическому техническому состоянию |
Обслуживание только дефектного оборудования в сочетании с профилактикой внеплановых остановов |
Проактивное обслуживание |
Продление межремонтного интервала и интервала между обследованиями |
• Организация периодического мониторинга технического состояния оборудования • 3 — 10 •
На рис. 3-05 приведены графики отражающие взаимосвязь различных видов износа и срока эксплуатации (межремонтного интервала) оборудования.

Рис.3—05. Схема характерных процессов изнашивания узлов механизма в зависимости от наработки. 1 — износ упругого сопряжения; 2 — износ жесткого сопряжения; 3 — классическая кривая Лоренца; 4 — усталостный или кавитационный износ; 5 — коррозионный износ.
Техническое и промышленное обеспечение ППР базируется на том, что имея статистические данные истории отказов оборудования и зная характеристики развития процессов изнашивания узлов механизма в зависимости от наработки, можно определить и установить такой срок эксплуатации оборудования (межремонтный интервал), при котором вероятность интенсивного износа и отказов мала. Ревизия и замена компонента оборудования по прошествии очередного фиксированного межремонтного интервала значительно уменьшает вероятность внезапного отказа.

Рис.3—06. Классическая схема, лежащая в основе планово—профилактического обслуживания.
Однако в реальных условиях не существует сильной (характерной для рис. 3 — 06) взаимосвязи между сроком эксплуатации и техническим состоянием агрегата, если не присутствуют эрозионные формы износа и разрушения деталей агрегата, которые тесно связаны со сроком службы. Техническое состояние агрегата, линейно связанное со сроком службы (или количеством переработанного продукта), наблюдается обычно в том случае, когда высокоактивные частицы продукта входят в контакт с деталями производственного оборудования и вызывают фрикционную механическую эрозию и износ, усталостный износ или химическую коррозию. В качестве примера можно привести механический износ перекачиваемым продуктом, например, воздухом, содержащим мелкие абразивные частицы (угольную пыль, песок, высушиваемый продукт), рабочих колес воздуходувки, связанный практически линейной зависимостью с количеством перекачанного воздуха.
Следовательно, если периодическое планово —
• Организация периодического мониторинга технического состояния оборудования • 3—12 •
Обслуживание по фактическому техническому состоянию имеет ряд преимуществ по сравнению с ППР:
- наличие постоянной информации о состоянии агрегатов, охваченных мониторингом (вибродиагностика позволяет определять "проблемное" и "нормальное" оборудование), позволяет планировать и выполнять техническое обслуживание и ремонт без остановки производства и практически исключить отказы (внеплановые остановы) оборудования;
• посредством внедрения ОФС можно добиться увеличения эффективности производства от 2 до 10%;
— прогнозирование и планирование объемов технического обслуживания и ремонта "проблемного" оборудования; снижение расходов по техническому обслуживанию за счет минимизации ненужного ремонта (увеличение межремонтного интервала) "нормального" оборудования;
• в результате проведения мониторинга технического состояния агрегатов и их обслуживания по фактическому состоянию внеплановый объем работ, вызванный чрезвычайными ситуациями, обычно составляет менее 5% от общего объема работ, а время простоя оборудования составляет не более 3% от времени, затраченного на техническое обслуживание; опыт показывает, что типичные расходы на ремонт при аварийных отказах оборудования в среднем в 10 раз превышают стоимость ремонта при вовремя обнаруженном дефекте;
— обеспечение эффективности ремонта за счет послеремонтного вибрационного обследования;
• опыт показывает, что примерно от 2 до 10% новых деталей имеют дефекты изготовления, которые могут привести к быстрому выходу замененной детали из строя и/или отказу оборудования, а также вызвать повреждение других нормально функционировавших деталей; дефектная деталь или нарушения технологии сборки в ряде случаев могут быть обнаружены в процессе проведения виброиспытаний после ремонта;
— эффективное планирование распределения обслуживающего персонала, запасных частей, инструмента и др.; возможность сокращения резервного оборудования;
— повышение качества продукции;
• качество продукции в некоторых случаях может подвергаться неблагоприятному воздействию со стороны оборудования, имеющего механические дефекты; поскольку качество продукции часто проверяется на заключительном этапе производственного процесса, до момента обнаружения проблемы может быть произведено большое количество низкокачественного продукта; мониторинг технического состояния и упреждающий ремонт позволяют не допускать изменения механического состояния оборудования до приводящего к браку, поскольку ремонт может быть произведен до того, как будет поставлено под угрозу качество продукта;
— улучшение охраны труда и устранение нарушений экологических требований;
• проведение ремонтных работ в чрезвычайной обстановке внезапного отказа и опасности внеплановой остановки производства приводит к повышению травматизма;
— экономия энергоресурсов;
• устранение источников повышенной вибрации или, например, недопущение фрикционного износа щелевых уплотнений может снизить удельные затраты энергии на 1..15%;
— эффективность переговоров с поставщиками оборудования относительно его гарантийного ремонта, восстановления, замены или изменения конструкции;
• поскольку записываемые параметры вибрации документально отображают техническое состояние агрегата в момент пуска, приработки и гарантийной эксплуатации, они являются доказательствами для арбитража;
Основой обслуживания по фактическому техническому состоянию является вибромониторинг оборудования. Наблюдение за развитием и применением средств измерений показывает, что предприятия (особенно крупные) начинают осуществлять программу ОФС именно с распознавания и определения состояния оборудования при помощи мониторинга вибрации и, получив экономический эффект, внедряют и другие технические новинки в этой области. Затраты на
• Организация периодического мониторинга технического состояния оборудования • 3—14 •
Обслуживание оборудования по фактическому техническому состоянию базируется на применении ряда методов технической диагностики и распознавания технических состояний, которые, в сочетании, позволяют определять большую часть различных дефектов, возникающих в технологическом оборудовании предприятия.
В таблице 3 — 02 представлен список наиболее распространенных методов технической диагностики и распознавания технических состояний оборудования, применяемых при ОФС.
Проактивное техническое обслуживание оборудования.
Идея проактивного технического обслуживания оборудования (в дальнейшем ПАО) заключается в обеспечении максимально возможного межремонтного срока эксплуатации оборудования за счет применения современных технологий обнаружения и подавления источников отказов.
Основой проактивного технического обслуживания являются:
• идентификация и устранение источников повторяющихся проблем, приводящих к сокращению межремонтного интервала оборудования;
• устранение или значительное снижение факторов, отрицательно влияющих на межремонтный интервал или срок эксплуатации оборудования;
• распознавание состояния нового и восстановленного оборудования с целью проверки отсутствия признаков дефектов, уменьшающих межремонтный интервал;
• увеличение межремонтного интервала и срока эксплуатации оборудования за счет проведения монтажных, наладочных и ремонтных работ в точном соответствии с техническими условиями и регламентом.
ПАО базируется на применении нескольких, приведенных ниже, компонентов, сочетание которых дает максимальный эффект.
Анализ причин внеплановых остановов, аварий, укороченных межремонтных интервалов, включающий выявление повторяющихся проблем, возникающих при эксплуатации оборудования.
Техническое обслуживание и ремонт обычно устремлены на устранение в основном очевидных дефектов оборудования. При этом нередко частые ремонты воспринимаются как вполне нормальное явление. Анализ коренных проблем отказов направляет передовые аналитические средства и инженерную логику на идентификацию и коррекцию скрытой основной проблемы. Принятие программы анализа коренных проблем отказов часто приносит предприятию значительную экономию.

Рис.3-09. Зависимость вероятности отказа от наработки в “детском возрасте агрегата”, связанная с конструкторскими, эксплуатационными и технологическими дефектами.
• Организация периодического мониторинга технического состояния оборудования • 3—16 •
балансировка ротора и центровка узлов оборудования. Дополнительные затраты времени и ресурсов для достижения при проведении этих операций самых жестких норм не намного больше, чем те, которые требуются для проведения этих операций со средним качеством, но достижение уровней жестких норм часто способно увеличить даже вдвое межремонтный интервал оборудования.
В качестве примера можно привести результаты внедрения лазерного оборудования для центровки, документированные на ряде нефтетранспортных и нефтехимических предприятий, где была реализована эта программа. Эффект от точной центровки был следующим: средний срок службы подшипников и муфт возрос (на некоторых предприятиях) в 3...8 раз, затраты на техническое обслуживание уменьшились в среднем на 5...7%, межремонтный интервал возрос в среднем на 10...12%, внеплановые остановы оборудования, возникшие в результате расцентровки, сократилось более, чем наполовину.
Анализ основных причин выхода подтттипников качения из строя показывает, что, по статистике, исправный подшипник выходит из строя примерно в 30% случаев из —за нарушения технологии монтажа. Таким образом, применяя недорогое специализированное оборудование для нагрева подшипников при монтаже, можно добиться снижения выхода из строя подшипников по этой причине почти на треть.
Оценка технического состояния агрегата после ремонта.
Важнейший этап проведения контроля состояния: вывод агрегата из монтажа или ремонта и проверка исправности (работоспособности) всего агрегата. По статистике 20% обслуживания такого типа производится с нарушением качества, приводя к сокращению межремонтного интервала оборудования.
В качестве примера можно привести следующий случай: в процессе перехода от ППР к ОФС, при анализе срока службы 16 насосных агрегатов на четырех установках нефтехимического предприятия было установлено, что уровень вибрации и межремонтный интервал (последний более чем в два раза) существенно зависят от того, какая из трех бригад, одинаково оснащенных, проводит ремонт.
Характерно, что администрация имела некоторую информацию об этом и до проведения анализа, показавшего, что одна из бригад допускала низкое качество сборки подшипниковых узлов, а другая — балансировки и центровки. Причина — низкая квалификация слесарей. Внедрение вибромониторинга явилось камешком, стронувшим лавину — перераспределив имеющийся ремонтный персонал между бригадами и проведя дополнительное обучение, администрация достигла значительного увеличения межремонтного интервала.
Наблюдения, проводимые на ряде предприятий, показывают, что завершающие операции, такие как крепеж (или проверка крепежа) узлов агрегата к фундаменту (иногда в ходе центровки) и соединение узлов агрегата между собой проводятся менее добросовестно, чем ранее следующие в процессе технического обслуживания технологические операции. Оценка технического состояния агрегата после ремонта и проведение статанализа не только выявляет неприлежных ремонтников, но и совершенствует мастерство добросовестных исполнителей.
Входной и выходной контроль.
В процессе испытаний при выводе оборудования из ремонта или монтажа, особенно силами сторонней подрядной организации, предприятие, обладающее средствами контроля качества работы оборудования, может влиять на исполнителя, даже если в условиях контракта не предусмотрены многие требования, например, к уровню вибрации, поскольку нормы вибрации определяются отраслевыми нормами, нормами завода — изготовиталя и стандартами России, обязательными к выполнению.
• Организация периодического мониторинга технического состояния оборудования • 3—18 •
Программа ОМНО при реализации должна обеспечить:
• исключение внеплановых остановок (внезапных отказов) оборудования при достижении максимально длительного полезного срока службы дорогостоящего оборудования;
• постоянное наличие (предоставление) информации о состоянии оборудования, позволяющее судить о состоянии общей производительности, а также прогнозирование и планирование потребности в обслуживании;
• обеспечение равномерной прогнозируемой и обоснованной загрузки ремонтного персонала, совместное планирование графиков и объемов обслуживания ремонтными и технологическими службами;
• снижение эксплуатационных затрат предприятия, увеличение прибыли, повышение безопасности труда, охраны окружающей среды, качества продукции и сокращение отходов.
Эффективное приложение практики ОНМО может значительно уменьшить вероятность внезапного отказа, особенно в начальный и заключительный период эксплуатации.
Как правило, в начале реализации программы мониторинга и ОФС внедряются в небольших объемах и нередко испытывают недостаток выделенных ресурсов. Однако, если появляются положительные результаты, они получают поддержку и возможности для расширения на все оборудование предприятия. Развитие программ на предприятиях можно условно разбить на три стадии: начальный период — внедрения (запуска), период проактивного расширения и период зрелой ОНМО —программы. Ниже дано краткое описание.
Начальный период.
Обычно, в течение первого года программа ОНМО рассматривается в качестве пробной концепции, и, как правило, она реализуется на предприятии, практикующем только планово — профилактическое техническое обслуживание, считающееся достаточным для удовлетворительной работы оборудования. Опыт ряда специализированных и эксплуатационных предприятий, занимающихся периодическим вибромониторингом, свидетельствует, что первым шагом в развертывании программы ОНМО на предприятии является создание двух основных структурных подразделений (расположены в верхней части структурной схемы, рис. 3—11), предназначенных для выполнения основополагающих функций: группа планирования ремонта (технического обслуживания) и группа обеспечения надежности (технической диагностики и мониторинга).
Группа планирования ремонта обычно уже существует на любом достаточно крупном предприятии в том или ином виде (с различными названиями), например, в виде группы профилактического обслуживания ОГМ предприятия, однако ее функции несколько расширяются от долгосрочного планирования (год и более) повседневной работы ремонтной службы к полномасштабному (краткосрочному и долгосрочному) планированию ТО.
Эта группа должна осуществлять следующие основные функции:
• координация повседневной планово — профилактической работы службы ремонта предприятия, необходимого планового периодического ТО с распознаванием состояния оборудования, сроков и обстоятельств проведения технического обслуживания с руководством производства (с учетом минимизации последствий остановки или снижения производительности производства);
• планирование объема работ по ТО, включая процедуры, инструмент, запасные части, трудозатраты, осмотры и обследования и т. д.;
• контроль за выполнением работ и отслеживание затрат, включаяфункционально — стоимостной анализ;
• Организация периодического мониторинга технического состояния оборудования • 3 — 20 •
ОНМО вообще и вибромониторинга в частности. Предпочтительно, чтобы один из руководителей службы ремонта предприятия, который в дальнейшем будет управлять этой структурой, также прошел начальный курс обучения. Это позволит, с одной стороны, избежать многочисленных ошибок при организации и постановке задач службы по обеспечению надежности, а с другой — правильно, без недооценки или переоценки, уяснить возможности вибродиагностики и вибромониторинга, а также грамотно и уверенно участвовать, при необходимости, в разборе причин отказов.
Группа обеспечения надежности должна осуществлять следующие основные функции:
• проведение мониторинга и виброобследований оборудования предприятия, управляемого регламентом предприятия и запросами группы планирования ремонта (ТО) и руководителя объекта;
• обеспечение своевременных сведений о состоянии оборудования для группы планирования ремонта (ТО), с целью планирования ремонта и исключения любых внеплановых остановов производства;
• ведение архива оборудования, в т. ч. сведений о простоях оборудования, состоянии оборудования, проведенном ремонте и его результатах, результатах функционально — стоимостного анализа и др.;
• внедрение технологий проактивного обслуживания и других технологий мониторинга.
Расширение обслуживания по фактическому техническому состоянию и введение проактивного обслуживания.
Для предприятий, практикующих сращение ППР и ОФС, типично в течение второго...четвертого года действия программы ОНМО (при условии, что позволяют финансовые возможности предприятия или, что хотя бы часть экономии от программы ОНМО идет на расширение самой программы), помимо вибромониторинга, добавление новых технологий распознавания состояния оборудования, таких, как АЭ —диагностика, термография, трибодиагностика и др. На этой стадии информация о состоянии оборудования уже вполне интегрирована с периодическим обслуживанием и проактивными технологиями, включая точную центровку с использованием лазеров, балансировку в собственных подшипниках, анализ коренных причин отказов и др. Для совершенствования обслуживания на большинстве предприятий штат группы обеспечения надежности увеличивают на несколько специалистов, проводящих завершающие технологические операции по обслуживанию оборудования — балансировку, центровку, иногда совместно с ремонтными бригадами предприятия, и виброобследование. Важно на этой стадии изменить отношение к техническому обслуживанию на предприятии: убедить администрацию поощрять персонал не за объем проведенных ремонтных работ, а его уменьшение для определенных групп оборудования, а рабочих — изменить негативное отношение к предсказанию и устранению источников проблем "белыми воротничками с чистыми руками" и поверить в возможность совместной работы — доказать, что служба диагностики не враг, а друг. Выполнение основной части измерений группой обеспечения надежности начинает сдвигаться от однособытийного обследования агрегата, намеченного к ремонту, к полномасштабному мониторингу всего парка оборудования предприятия.
Развитая ОНМО—программа.
Для передовых предприятий стадия развитой программы ОНМО примечательна двумя признаками: применением большинства существующих технологий ОФС и происходящим изменением отношения к ним. Передовые предприятия выгодно отличаются от рядовых с точки зрения акцента администрации и персонала на ОНМО: внимание полностью фокусируется на ликвидации (устранении) внеплановых остановок, теперь уже воспринимаемых как
• Организация периодического мониторинга технического состояния оборудования • 3 — 22 •
• средняя оценка состояния оборудования;
• процентное соотношение оборудования в исправном состоянии, состоянии, требующем принятия мер и предельном (аварийном) состоянии;
• удельные затраты энергоресурсов на единицу продукции;
• соотношение используемого и производимого пара;
• общее значение и потребление инвентарных запасных частей.
Если каждый отдельный показатель может быть неточен (или фальсифицирован) или отражать успехи других подразделений (мероприятий) по увеличению эффективности производства, то вместе взятые они однозначно толкуют успех или неудачу программы ОНМО.
В качестве примера можно привести практический опыт одного из химзаводов, полученный при эксплуатации технологической установки по производству стирального порошка. В процессе проведения эксперимента установили, что заработная плата каждого из рабочих стала зависима от показателя, называемого на предприятии "наработка на отказ" ("время наработки на отказ"). Этот показатель объединял три других существенных показателя эффективности производства: межремонтный интервал как функция общего времени использования (т. н. "полезность"), процент стоимости отходов или брака в себестоимости произведенной продукции (т. н. "качество") и процент времени использования оборудования по отношению к общему полезному времени (т. н. "использование"). Для измерения этих показателей работы оборудования на установке, в конце каждой смены операторы были обязаны предоставлять письменный отчет, объясняющий, почему их участок не обеспечил специфицированную выработку: причину и предполагаемого виновника. Все неисправности оборудования, вызывающие потери выработки, регистрировались с указанием конкретной локализации дефектов. Все оборудование установки и критические компоненты были занесены в компьютерный реестр, а компоненты с высокой степенью ненадежности исследовались для определения эффективных корректирующих мер, направленных на повышение их надежности.
Каждый рабочий установки знал, что каждый 1% увеличения периода "наработки на отказ" означает прибавку к его зарплате суммы, эквивалентной $20 (примерно 20% от полученного эффекта). Через год условия эксперимента изменили, поскольку на этой установке период "наработки на отказ" был увеличен на 40%, — снизили прибавку заработной платы до $5/1%. Тем не менее период "наработки на отказ" продолжал стабильно увеличиваться и превысил на 70% первоначальное значение (два года ранее). Результатом проведенных мероприятий стало сокращение объема ТО (бюджета службы ремонта) более чем на 15%, а численность ремонтного персонала — на 35% при существенном росте объема (стоимости) производимой продукции. Характерным стал сильнейший интерес рабочих, ремонтного персонала и ИТР к результатам вибромониторинга (как инструмента для распознавания технического состояния оборудования) и вибродиагностики, от которых во многом стало зависеть их благополучие. Однако главной причиной быстрого успеха было то, что их администрация была инициатором программы ОНМО и на всех ее стадиях оказывала серьезную поддержку ее организации.
• Методология нормирования вибрации и распознавания состояния оборудования • 4 — 2 •
В подтверждение вышесказанного в настоящей главе приведены выводы, сделанные авторами при анализе материалов исследований, охватывающих некоторые типы центробежных компрессорных и насосных агрегатов, вентиляторов, применяемых на предприятиях России. В частности, приводятся доводы в пользу того, что не существует также единственного набора критериев оценки технического состояния, подходящего не только для класса оборудования (например, для класса центробежных агрегатов: для центробежных компрессоров или для центробежных насосов, или центробежных вентиляторов со сходными мощностными характеристиками и сходной частотой вращения), но и даже для типа и типоразмера (например, для вентиляторов: воздуходувок одного типа или дымососов одного типа). Другими словами, из-за различий в конструкции, ТО и условиях эксплуатации каждый агрегат имеет свои собственные, несколько отличные от других, критерии и нормы оценки технического состояния.
Успех любой системы вибромониторинга в основном зависит от методов оценки состояния агрегата, т.е. способов определения допустимых значений (норм) вибрации и параметров анализа вибрации, интегрированных в анализирующее программное обеспечение пользователя. Главные алгоритмы оценки состояния оборудования продаваемого на рынке программного обеспечения обеспечивают распознавание состояния по общему уровню вибрации, по вибрации в сравнительно узкой полосе частот или по огибающей спектра.
Оценка состояния по общему уровню вибрации.
Разработанные международные (FDG 2056, ISО 2372, ISО 3945 и др.) и Российские стандарты и нормативно — методические рекомендации на предельные уровни вибрации основаны на допущении, что подобные по мощности, высоте оси вращения и частоте вращения ротора, способам установки, условиям монтажа и эксплуатации агрегаты имеют примерно одинаковые допустимые значения вибрации при достижении предельного состояния.
При оценке вибрации агрегатов с вращающимся ротором в качестве нормируемых параметров в большинстве случаев устанавливается один из следующих:
• среднеквадратическое значение виброскорости, Vе [мм/с];
• среднеквадратическое значение виброскорости в октавной полосе
частот, включающей в себя частоту вращения ротора, Vео [мм/с];
• среднеквадратическое значение виброскорости на элементах
крепления агрегата к фундаменту на месте установки, Vеф [мм/с];
• пиковое значение (размах) виброперемещения, S3 [мкм].
Так, например, в соответствии с одним из стандартов России оценка интенсивности вибрации при приеме — сдаточных, периодических, квалификационных, типовых и приемочных испытаниях машин электрических с частотой вращения ротора 3000 об/мин и массой ротора до 2000 кг должна соответствовать величинам, указанным в таблице 4-1.
Таблица 4—1.
Нормируемые параметры вибрации |
Срок эксплуатации не ограничен |
Ограниченный срок эксплуатации |
Эксплуатация недопустима |
СКЗ виброскорости Vе, мм/с |
до 4,5 |
4,5 7,1 |
свыше 7,1 |
СКЗ виброскорости Vео, мм/с |
до 3,3 |
3,3 5,2 |
свыше 5,2 |
СКЗ виброскорости Vеф, мм/с |
— |
— |
свыше 2,0 |
Другой стандарт на машины электрические вращающиеся с высотой оси вращения свыше 355 мм (методы измерения и допустимые значения) при приемо —
• Методология нормирования вибрации и распознавания состояния оборудования • 4 — 4 •
Оценку технического состояния электроприводов центробежных электроприводных нефтяных насосов по интенсивности абсолютной вибрации (Центробежные электроприводные нефтяные насосные агрегаты, эксплуатационные нормы вибрации) следует определять (те же РДИ) в соответствии с таблицей 4 — 4.
Таблица 4—4.
Интенсивность вибрации, СКЗ виброскорости (мм/с) |
Оценка технического состояния |
||
Высота оси вращения ЭД (мм) |
|||
от 80 до 132 вкл. |
св.132 до 225 вкл. |
св.225 до 400 вкл. |
|
до 1,8 |
Допустимо после ремонта |
Допустимо после ремонта |
Допустимо после ремонта |
св. 1,8 до 2,0 |
Допустимо |
||
св.2, 8 до 4,5 |
Еще допустимо |
Допустимо |
|
св.4,5 до 7.1 |
Требует принятия мер |
Еще допустимо |
Допустимо |
св.7,1 до 11,2 |
Недопустимо |
Требует принятия мер |
Еще допустимо |
свыше 11,8 до 18 |
Недопустимо |
Требует принятия мер |
|
свыше 18 |
Недопустимо |
Оценка технического состояния центробежных электроприводных нефтяных насосов по интенсивности абсолютной вибрации (Нормы вибрации адаптированные) следует определять (те же РДИ) в соответствии с таблицей 4 — 5.
Таблица 4—5.
Интенсивность вибрации, СКЗ виброскорости (мм/с) |
Оценка технического состояния |
||
Потребляемая мощность, кВт |
|||
до 50 |
свыше 50 до 200 |
свыше 200 |
|
до 1,2 |
Отлично |
Отлично |
|
св. 1,2 до 1,8 |
Хорошо (допустимо после ремонта) |
Отлично |
|
св. 1,8 до 2,8 |
Допустимо |
Хорошо (допустимо после ремонта) |
|
cв, 2, 8 до 4,6 |
Еще допустимо |
Допустимо |
Хорошо (допустимо после ремонта) |
св.4,6 до 6,3 |
Требует принятия мер |
Еще допустимо |
Допустимо |
св.6,3 до 8,2 |
Не допустимо |
Требует принятия мер |
Еще допустимо |
св.,8,2 до 10,5 |
Не допустимо |
Требует принятия мер |
|
свыше 10,5 |
Недопустимо |
"Отлично", "Хорошо" — оценка качества ремонта, допустимо при приемных испытаниях после ремонта; "Допустимо" — бездефектное эксплуатационное состояние; "Еще допустимо" — необходимость проведения мероприятий по обнаружению дефекта, усиление контроля; "Требует принятия мер" — планомерный вывод в ремонт; "Недопустимо" — эксплуатация на допускается.
• Методология нормирования вибрации и распознавания состояния оборудования • 4 — 6 •
центровки или дисбаланс, значительные изменения уровня вибрации на частотах с низкими уровнями будут недостаточны для "срабатывания тревоги" по общему уровню.
В качестве иллюстрации к вышеизложенному можно привести такой пример: на рис. 4 — 01 показан тренд вертикального компонента вибрации опоры ЭД в продолжение семи месяцев эксплуатации и нанесены допустимые значения в соответствии с одним из Государственных стандартов. При таком СКЗ виброкорости срок эксплуатации агрегата не ограничивается.

Рис. 4—02. Спектры виброскорости в вертикальном направлении подшипника ЭД в продолжение семи месяцев.
Однако, если рассмотреть динамику изменения спектров вибрации этой же опоры ЭД (см. рис. 4 — 02) с течением времени, то можно отметить, что несмотря на некоторое уменьшение уровня вибрации, на частотах 50 и 100 Гц, вероятно вызываемой расцентровкой узлов агрегата, произошло существенное увеличение виброскорости (примерно в 10 и более раз) на некоторых частотных составляющих в полосе частот 200...600 Гц в период с 16.01.94 по 1.03.94, -т.е. в продолжение всего 45 дней. Таким образом очевидно быстрое развитие дефекта подшипника качения, т.е. необходимо принимать меры по тщательному наблюдению за данным агрегатом и, возможно, планировать его вывод в ремонт.
На рис. 4 — 03 показано изменение общего уровня вибрации и вибрации в частотной полосе 6...10 fr в течение семи месяцев эксплуатации и нанесены допустимые значения вибрации в соответствии с общепринятыми стандартами.
Также нежелательно определение состояния агрегата только по уровню вибрации настроенному на "низкоуровневые" дефекты, такие, как ряд дефектов подшипников качения или дефектов зубчатых муфт, поскольку, например, неопасное (незначительное) увеличение дисбаланса может вызывать необоснованное "срабатывание тревоги".
По этим причинам, большинство
• Методология нормирования вибрации и распознавания состояния оборудования • 4 — 8 •
или принять в качестве эталона послеремонтный "хороший" спектр (или предыдущий текущему спектр).
Учет пожеланий специалиста в формировании эталонного спектра для конкретного случая в продаваемых на рынке готовых программных пакетах во многих случаях весьма ограничен. По этой причине при оценке состояния оборудования с применением анализа изменения огибающей спектра иногда появляются необоснованные "срабатывания" тревоги, преимущественно потому, что вибрация оборудования с вращающимся ротором обычно немного флуктуирует по частоте и амплитуде относительно определенной линии спектра с четкой границей.
Флуктуация по частоте: совершенно постоянная частота вращения ротора агрегата труднодостижима. Небольшие ее флуктуации, вызываемые изменением нагрузки, частоты сети и др. (2...8% fr у асинхронных и до 1% fr у синхронных электрических машин), часто приводят к ощутимому сдвигу первой и высших гармоник частоты вращения ротора в текущем спектре (частот спектральных линий) относительно эталонного. Например, при уменьшении частоты вращения ротора асинхронного электродвигателя (fr=2950 об/мин) насосного агрегата с 7 лопатками на рабочем колесе насоса на 0,5 Гц (примерно 1%) ведет к уменьшению лопаточной частоты на 3,5 Гц, а в зубчатой передаче с 47 зубьями на ведущем колесе — на 23,5 Гц. Это может привести превышению допустимых значений опорного спектра и ложному появлению сигнала об изменении состояния оборудования.
Флуктуация по амплитуде: это явление означает практически постоянное присутствие апериодических скачкообразных изменений амплитуд вибрации. Значения как общего уровня, так и отдельных частотных составляющих вибрации часто демонстрируют небольшую флуктуацию во времени вокруг некоторой величины, затем без явной причины происходит резкий переход к новым величинам с новыми флуктуациями. Эти изменения легко наблюдать при мониторинге вибрации в высокочастотной области спектра, особенно они характерны для "промежуточных" частот.
Хотя амплитудные флуктуации во многих случаях могут быть небольшие, их апериодический и "неслучайный" характер приводит к ложному "срабатыванию" тревоги.
К самым существенным недостаткам мониторинга по огибающей спектра вибрации можно также отнести отсутствие исходных данных на начальном этапе мониторинга при организации обследований новых и модифицированных агрегатов или при отклонении эксплуатационных режимов.
По этим причинам, оценка состояния по огибающим спектра считается, в лучшем случае, относительно надежным и достоверным методом анализа.
Оценка состояния по значениям параметра в частотных полосах.
Этот метод распознавания состояния оборудования является компромиссным между оценкой состояния оборудования по общему уровню вибрации и по огибающей спектра, а точнее частным случаем оценки состояния по огибающей спектра, поскольку дает возможность произвольно устанавливать положение, ширину частотной полосы и допустимое значение параметра (критерия) который сравнивается с текущим значениями и далее строить тренды параметра в этой полосе, давая возможность пользователю оценивать и прогнозировать состояние оборудования. Количество частотных полос обычно составляет 6... 18.
Ряд методов вибродиагностики основан на том, что определенные механические дефекты по мере развития генерируют вибрацию в определенных частотных полосах с определенным соотношением величин параметров. Например, рассматривая амплитуды определенных рахмоник кепстра, полученного в определенном частотном диапазоне спектра, можно легко установить глубину модуляции высокочастотной вибрации, которая определяется степенью износа ряда деталей и узлов агрегата. Другой пример — достаточно интенсивная вибрация
• Методология нормирования вибрации и распознавания состояния оборудования • 4—10 •
СSI, США) предполагает индивидуальный подход к каждому агрегату, паспортизацию его исходного или среднего работоспособного состояния и отслеживание изменений его состояния во времени на основе проведения периодических замеров технических параметров, что обеспечивает высокую чувствительность системы мониторинга к изменению состояния оборудования.
С другой стороны чувствительность системы мониторинга повышается за счет возможности расчета, отслеживания и прогнозирования трендов различных параметров: вибрации, динамического давления или температуры и пр.
Подобный подход предусматривает отказ от стандартных допустимых значений и возможность определения индивидуальных критериев состояния оборудования вплоть до каждой измерительной точки каждого агрегата.
При определении "нормального состояния" оборудования возможно использование двух методов:
• принятие в качестве критериев "нормального состояния" данных замеров контролируемых параметров на новом (только что смонтированном) оборудовании или после его капитального ремонта, в обоих случаях, разумеется, после обкатки и приработки (исходное состояние);
• определение в качестве критериев "нормального состояния" среднестатистических величин контролируемых параметров, полученных при обработке данных некоторого количества периодических измерений (для агрегатов, работающих в стационарном режиме количество необходимых измерений обычно шесть и более) при работе агрегата в заведомо работоспособном состоянии (средне—нормальное состояние).

Рис.4—05. Схема сбора данных для расчета средненормальнного уровня вибрации и допустимых значений вибрации различных состояний.
Большинство стандартов, регламентирующих допустимые значения вибрации, основаны на статистической обработке достаточно большого количества данных по самым разнообразным типам оборудования различными исследовательскими группами. При этом в них определена схожая градация по классам состояния на основе уровней в 4, 8, ... дБ (соответственно, примерно 1.6, 2.5, ... раза). Эти относительные величины и принято использовать в качестве разделительных границ для сигнализации по степеням вибросостояния оборудования (нормальное, допустимое, ограниченно - допустимое, предельное состояния).
• Методология нормирования вибрации и распознавания состояния оборудования • 4—12 •
Таблица 4-2.
Измерение |
Параметр |
||||||
СКЗ |
Пар.1 |
Пар. 2 |
Пар.З |
Пар. 4 |
Пар. 5 |
Пар. 6 |
|
НПС 1 |
|||||||
НА1 -V1 - 20.03.95 - 16:32 |
3.807 |
0.738 |
2.691 |
0.409 |
0.623 |
2.443 |
|
НА1 -V1 - 1 1.04.95 - 15:47 |
4.812 |
0.651 |
2.716 41 |
0.633 |
3.101 |
1.383 |
6.156 |
НА1- V1 -26.10.95 -10:26 |
6.263 |
0.129 |
4.837 |
1.315 |
3.77 |
0.085 |
7.375 |
НА4- V1 -20.03.95 -16:52 |
2.422 |
0.512 |
1.786 |
1.011 |
0.293 |
1.067 |
|
НА4-V1 -11.04.95-16:22 |
4.49 |
0.496 |
1.432 |
0.648 |
3.696 |
1.017 |
3.219 |
НА4 - V1 - 30.05.95 - 13:59 |
2.827 |
0.332 |
1.873 |
1.178 |
1.451 |
0.881 |
1.875 |
НА4 - V1 - 20.06.95 - 12:59 |
2.51 |
0.233 |
1.935 |
0.936 |
1.098 |
0.58 |
1.688 |
НА4- V1 -02.07.95 -12:48 |
4.525 |
0.409 |
1.935 |
0.98 |
3.721 |
0.924 |
3.266 |
НА4 - V1 - 24.07.95 - 14:33 |
2.923 |
0.194 |
1.997 |
1.774 |
0.874 |
0.682 |
2.078 |
НА4- V1 -20.10.95- 15:26 |
2.541 |
0.2 |
1.935 |
0.471 |
1.017 |
1.141 |
1.914 |
НА4-V1 -30.10.95- 14:20 |
2.348 |
0.15 |
1.898 |
0.484 |
0.961 |
0.85 |
1.688 |
НА4-V1- 13.11.95- 13:15 |
4.32 |
0.245 |
2.022 |
0.623 |
3.473 |
0.924 |
1.555 |
НА4- V1 -08.12.95-05:30 |
3.061 |
0.276 |
1.687 |
0.251 |
1.873 |
1.6 |
2.078 |
НПС 2 |
|||||||
НА4- V1 -20.03.95 -15:42 |
2.785 |
1.525 |
1.104 |
0.812 |
0.881 |
1.575 |
|
НА4- V1 -11.04.95-14:29 |
3.67 |
0.515 |
2.406 |
0.747 |
1.271 |
2.084 |
0.563 |
НА4- V1 -30.05.95 -14:08 |
4.56 |
0.419 |
3.001 |
0.305 |
0.626 |
3.299 |
1.242 |
НА4- V1 -02.06.95- 14:19 |
3.605 |
0.899 |
1.898 |
0.592 |
2.294 |
0.732 |
3.906 |
НА4- V1 -31. 10.95- 14:52 |
5.485 |
0.667 |
2.195 |
0.38 |
3.721 |
3.175 |
1.555 |
Среднее арифм. (хср) |
3.719 |
0.477 |
2.186 |
0.752 |
1.930 |
1.357 |
2.677 |
Дисперсия (s) |
1.112 |
0.331 |
0.779 |
0.381 |
1.252 |
0.851 |
1.812 |
Верхняя граница (хмакс) |
7.056 |
1.472 |
4.524 |
1.898 |
5.687 |
3.913 |
8.114 |
В таблице 4 — 2 вызывают сомнение в достоверности данные в помеченных серым цветом клетках, поскольку они превышают уровень среднего арифметического плюс утроенная дисперсия. После их удаления можно получить исходные данные, которые могут использоваться для дальнейшего статанализа или определения состояния агрегата.
Анализ улучшенных таким образом выборок показывает, что их совокупность достаточно хорошо подчиняется нормальному закону распределения. Проверка гипотезы осуществлялась с применением графического метода с помощью "вероятностной бумаги" и показала по всем компонентам колебаний одинаковых опор (штатных контрольных точек) однотипных агрегатов и во всех случаях удовлетворительные результаты.
Установление близости совокупности измеренной вибрации одинаковых опор однотипных агрегатов нормальному распределению существенно облегчило оценку полученных результатов. Известно, что при нормальном распределении среднеквадратическое отклонение а характеризует границу отклонения не менее 2/3 измеренных значений, а согласно теореме Чебышева при достаточно большом числе независимых опытов среднее арифметическое значение наблюдаемых случайных величин сходится по вероятности к ее математическому ожиданию. Поэтому в основу дальнейшего анализа было положено рассмотрение математических ожиданий значений параметров однокомпонентной вибрации одинаковых опор (штатных контрольных точек) однотипных агрегатов и их дисперсий.
• Методология нормирования вибрации и распознавания состояния оборудования • 4—14 •
Таким образом были использованы два способа определения допустимых значений вибраций в частотных полосах:
• превышение 85% —ной (требует принятия мер, "предупреждение")
и 95% —ной (предельное состояние, "опасность") границ совокупности данных;
• превышение среднего уровня вибрации на 4 и 8 дБ.
Оба способа направлены на то, чтобы выделить 5 и 15 % всей совокупности данных измерений вибрации, отражающих наивысшую вибрацию агрегатов, хотя необходимо понимать, что приблизительность критериев отбора в дальнейшем корректировалась в каждом отдельном случае в зависимости от конкретных нужд.
Все спектры, по одноименным измерительным точкам, отображались по 40 гармоникам частоты вращения ротора для определения зон наибольшей гармонической активности. Было подтверждено, что с увеличением номера гармоники амплитудная активность уменьшается, см. рис. 4 — 07.

Рис. 4—07. Наложенные друг на друга 189 спектров насосов 14—и однотипных ЦНА с подшипниками скольжения и частотой вращения ротора 50 Гц.
Вибрация анализировалась отдельно по каждому узлу различных типов агрегатов (ЭД, насос, мультипликатор, компрессор, насос, вентилятор) и направлению измерения (вертикальное, горизонтально — поперечное и горизонтально — осевое).
Поскольку с увеличением номера гармоники виброактивность уменьшается к 10 гармонике в среднем в 10 и более раз (по отношению к первой) и после 10—15 гармоники, в основном, остается неизменной (кроме случаев с дефектами в редукторах и подшипниках качения), именно этими частотными полосами и был ограничен анализ:
• СКЗ виброскорости в полосе частот 2 Гц ... 40 fr (индекс Vе);
• Методология нормирования вибрации и распознавания состояния оборудования • 4—16

Рис. 4—09. Пример гармонического состава вибраций группы центробежных вентиляторов одного типа.
На рис. 4 — 09 приведены границы распределения вибраций свыше 85% ("предупреждение") и 95% ("опасность") совокупности данных измеренных на 24 воздуходувках мощностью 120...250 кВт с подшипниками качения. Примечательно наличие виброактивности на 1...5 гармониках частоты вращения ротора и отсутствие сколько-нибудь заметной виброактивности на "лопаточных" частотах.

Рис. 4—10. Пример гармонического состава вибраций группы центробежных компрессоров одного типа.
На рис. 4—10 приведены границы распределения вибраций свыше 85% ("предупреждение") и 95% ("опасность") совокупности данных измеренных на 16 ЦБ компрессорах мощностью 2400...3500 кВт и частотой вращения ротора 150...190 Гц с подшипниками скольжения. Существенная виброактивность в
• Методология нормирования вибрации и распознавания состояния оборудования • 4—18 •

Рис. 4—12. Пример усредненного по направлениям гармонического состава вибраций группы центробежных компрессоров (I), асинхронных электродвигателей (2) центробежных насосов (3), воздушных вентиляторов(4).
У агрегатов с подшипниками качения виброактивность в области шестой и более высоких гармоник частоты вращения ротора несколько ниже, чем у агрегатов с подшипниками скольжения.
Некоторые выводы.
Статистический анализ показал, что не существует единственного набора критериев оценки состояния оборудования, подходящего не только для класса оборудования (например, одинакового для центробежных агрегатов: для компрессоров, насосов или вентиляторов со сходными мощностными характеристиками и частотой вращения ротора), но даже для типа (например, для различных типов вентиляторов: воздуходувок и дымососов; для различных типов насосов: многоступенчатые или одноступенчатые) и направления измерения вибрации (вертикальное, горизонтальное, осевое). Из —за различий в конструкции и эксплуатации каждый агрегат имеет свою собственную, несколько отличную от других, характеристику.
Предельные значения при распознавании состояния оборудования могут быть рассчитаны индивидуально для одноименных штатных измерительных точек агрегата, подшипниковых опор, общие по типу агрегата, по группам агрегатов (например, рассортированным по степени их вибронапряженности) или для всего обслуживаемого парка машин. Большая степень "индивидуализации" предельных значений увеличивает чувствительность системы мониторинга, но и лавинообразно увеличивает трудозатраты на их расчет и внесение изменений в базу данных.
Другими словами, применяя индивидуальный набор критериев и предельных значений для оценки состояния агрегата на каждой измерительной точке можно максимально повысить чувствительность системы мониторинга к изменению состояния оборудования, но при этом выполнять огромный объем работы по статобработке виброданных, дополнительным виброизмерениям, описанию и изменению в базе данных параметров анализа и уровней тревог, съедающий львиную долю рабочего времени.
В условиях производства этот путь в большинстве случаев нецелесообразен.
• Методология нормирования вибрации и распознавания состояния оборудования • 4 — 20 •
соответствующим либо 10 гармонике частоты вращения ротора, либо лопаточной частоте, в зависимости от того, какое из этих значений больше, либо требованиям РДИ.
Для мониторинга агрегатов с подшипниками качения верхний предел частотного диапазона измерений виброскорости рекомендуется выбирать приблизительно в пять раз больший, вычисленной частоты дефекта внутреннего кольца подшипника. В большинстве случаев он лежит ниже 50— й гармоники частоты вращения ротора и позволяет включать в анализируемую полосу различные гармоники всех частот дефектов подшипника, либо требованиям РДИ.
Внутри этих интервалов определяют различные частотные полосы, в зависимости от конструктивных особенностей агрегата.
Для всех без исключения агрегатов следует контролировать пиковое значение виброускорения в диапазоне 1000...10000 (по возможности 20000) Гц.
Количественные предельные значения интенсивности вибрации опор (подшипниковых щитов) роторных агрегатов.
С диагностической точки зрения очевидно, что оптимальным состоянием при эксплуатации агрегатов является отсутствие вибрации опор подшипников, точнее требование, чтобы их уровень был ниже порога чувствительности средств измерений. Однако, при установлении нормативных значений необходимо учитывать реальную возможность их выполнения и затраты, связанные с наладкой оборудования для достижения таких норм.
Установление близости совокупности измеренных вибраций нормальному распределению позволяет в качестве исходных значений при развертывании системы вибромониторинга рассмотреть математические ожидания, дисперсии и доверительные интервалы оценок.
При выборе предельных значений необходимо учитывать требования стандарта ИСО 2372 — обязательного использования шкалы нормо — чисел, составленной от среднего порога чувствительности человека к вибрациям с равным коэффициентом увеличения 1,6.
Такие выбираемые интервалы соответствуют ощутимым с точки зрения действия и субъективного восприятия изменениям параметра, а также обеспечивают отсутствие перекрытий в оценках вибрации при суммарной относительной погрешности измерения ±10%.
Согласно указанной шкале нормо —чисел предпочтительными для назначения нормативных значений являются следующие значения среднеквадратических виброскоростей ...0,45; 0,71; 1,12; 1,8; 2,8; 4,5; 7,1; 11,2; 18,0; 28,0; ... мм/с.
При сопоставлении данной шкалы рекомендуемых нормативных значений математическими ожиданиями среднеквадратических виброскоростей скоростей полученных авторами в результате приведенных выше исследований, естественно получилось совпадение с большинством из действующих стандартов России. Исходя из этого при развертывании программы мониторинга вибрации на предприятии или расширении ее на неохваченные обследованиями агрегаты, когда специалисту неизвестны особенности и характер вибросостояния каждого конкретного агрегата, можно рекомендовать следующие частотные полосы контроля параметров вибрации и коэффициенты и значения для определения допустимых значений в полосах:
• для агрегатов с опорными подшипниками скольжения см. данные, приведенные в таблице 4 — 5;
• Неуравновешенность ротора • 5— 1 •
Неуравновешенность ротора1
Неуравновешенностью ротора называют состояние ротора, которое во время вращения приводит к появлению центробежных сил и моментов, вызывающих переменные нагрузки на опоры ротора и его изгиб. Неуравновешенность ротора могут вызвать источники механического происхождения, рассматриваемые в этой главе, гидродинамического и др.Неуравновешенность ротора и дисбаланс механического происхождения.
Неуравновешенность ротора механического происхождения вызывается возникновением (в силу различных причин) отклонений рабочих геометрических размеров ротора от номинальных конструктивных, т.е. дисбаланса. При вращении такого ротора с некоторой угловой скоростью в каждом поперечном сечении, имеющем отклонение размеров от номинальных, возникает центробежная сила, вращающаяся вместе с ротором и вызывающая переменные нагрузки на опоры.
При этом для наблюдателя результирующая центробежная сила вращается, как и ее отдельные составляющие, но для ротора она неподвижна и является статической нагрузкой, которая может вызывать значительный изгиб.
Воздействие центробежных сил, или дисбаланса, на опоры в большой степени определяется динамическими свойствами ротора, т.е. его способностью к изменению формы при вращении. Большинство крупных агрегатов, например, турбоагрегатов, крупных электрических машин и др., имеют ротора с изменяемой при вращении формой оси, то есть т.н. гибкие ротора, однако, основная часть агрегатов средней и малой мощности имеют практически недеформируемые при вращении жесткие ротора.
Условно виды дисбаланса валопроводов можно разделить на две категории: механический, или "жесткий", дисбаланс и дисбаланс, связанный с прогибом ротора.
Механический, или "жесткий", дисбаланс — один из основных источников повышенной вибрации оборудования. Причины его возникновения можно разделить на две группы. Первая из них — это дефекты, связанные с нарушением технологии изготовления, сборки и балансировки ротора после сборки, с заменой или перестановкой деталей в процессе монтажа, характеризующиеся повышенной вибрацией непосредственно по завершении ремонта или монтажа оборудования. Другая группа — дефекты эксплуатации, такие как разрушение и "вылет" частей ротора (например, частей рабочего диска, лопаток и др.) в процессе работы, характеризующиеся внезапными однократными скачкообразными изменениями амплитуды и/или фазы вибрации, и различные виды износа поверхностей ротора (например, трущихся и рабочих — шеек вала, лопастей колес), отложения в процессе работы, уменьшение натяга (нарушение посадок) деталей вала, в большинстве случаев характеризующиеся сравнительно медленными (в течение часов, дней, месяцев и более) изменениями амплитуды и/или фазы вибрации.
• Неуравновешенность ротора • 5 — 3 •
многих случаях периодические или почти периодические, с периодом колебаний, соответствующим частоте вращения ротора (fr), и имеют форму, близкую к синусоидальной.
Амплитуда и фаза вибрации на частоте вращения ротора практически стабильны во времени. Кривая (форма сигнала) виброускорения часто имеет более "сложный" ("случайный") характер, особенно если ротор опирается на подшипники качения.

Рис. 5—02. Формы сигнала виброскорости и виброускорения измеренные на подшипниковом щите электродвигателя, имевшего неуравновешенность ротора.
На рис. 5 — 02 приведены формы сигнала виброскорости (нижний график) и виброускорения (верхний график) измеренные с интервалом в несколько секунд в одной и той же точке подшипникового щита электродвигателя, имевшего неуравновешенность ротора. На рисунке вертикальными пунктирными линиями помечен временной интервал, соответствующий одному обороту ротора. При этом кривая (форма сигнала) виброускорения имеет "сложную" форму за счет
• Неуравновешенность ротора • 5 — 5 •
ротора, а индексом fm вибросоставляющая, возбуждаемая подшипником качения, которую не следует принимать во внимание. Необходимо добавить, что виброактивность на высших гармониках частоты вращения ротора при дисбалансе во многом определяется нелинейностью, весьма индивидуальной для каждого подшипника, и уменьшается с ростом порядкового номера гармоники.
При механическом дисбалансе параметры вибрации зависят от частоты вращения ротора и практически не зависят от режима работы агрегата, внешних условий работы агрегата и температуры. Вибрация может проявляться как в поперечном, так и осевом направлениях, однако, в силу ее зависимости от жесткости подшипника, пространственно анизотропной, обычно горизонтально — поперечная вибрация преобладает над вертикальной. При этом чаще наблюдаются более интенсивные колебания опор ротора с дисбалансом, и влияние последнего на колебания опор сопряженных роторов агрегата, особенно в случае применения гибких муфт, обычно относительно невелико2.
В силу изложенного выше, большинство специалистов используют распределение вибрации на частоте вращения ротора как по различным опорам агрегата, так и по пространственным компонентам в качестве диагностических признаков неуравновешенности ротора, а количественные характеристики и особенности изменений амплитуды и фазы вибрации в качестве диагностических параметров.


Рис. 5—04. Схема контрольных точек и распределение вибрации по опорам насосного агрегата под влиянием, неуравовешенности ротора насоса. Индексы 1 и 2 — опоры ЭД, 3, 4 — насоса, V, Н, А — пространственные компоненты виброскорости.
• Неуравновешенность ротора • 5 — 7 •
направлении, и уровни вибрации опор по совпадающим направлениям измерений отличаются не более чем на 10...30%, т.е. вполне сопоставимы по величине.
На рис. 5 — 05 приведены спектры виброскорости передней и задней подшипниковых опор насоса. Вибрация преобладает на частоте вращения ротора (помечена индексом fr ), уровни вибрации высших гармоник частоты вращения ротора существенно ниже. Частотные составляющие спектра с максимальным уровнем вибрации (в горизонтально — поперечном направлении) помечены стрелками.
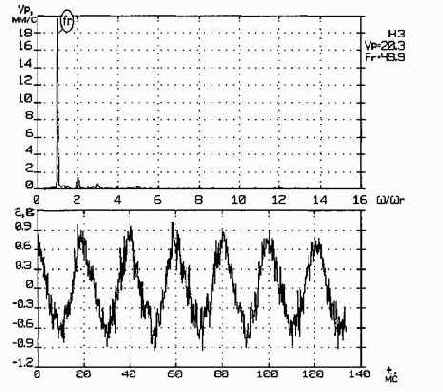
Рис. 5—06. Форма и спектр сигнала вибрации передней подшипниковой опоры насоса под влиянием неуравновешенности ротора.
На рис. 5 — 06 приведены форма виброускорения и спектр сигнала виброскорости передней подшипниковой опоры насоса в горизонтально — поперечом направлении. Уровень преобладающей на частоте вращения ротора виброскорости (помечена индексом fr ) превышает уровни виброскорости высших гармоник частоты вращения ротора более чем в 10 раз (20 дБ), а уровень шумов более чем на 40 дБ. Кривая виброускорения представляет собой суперпозицию колебаний в основном первой и значительно меньшей по амплитуде четырнадцатой гармоник частоты вращения ротора (14fr — удвоенная лопаточная частота), случайная вибрация сравнительно мала.
Признаки неуравновешенности ротора налицо. Насос был разобран и ротор поместили на балансировочный станок для проверки, в результате которой выявилось, что начальный дисбаланс многократно превышал допустимый дисбаланс по ТУ на данный тип роторов. После проведения балансировочного цикла, сборки агрегата и измерения вибрации при рабочей нагрузке уровень виброскорости не превышал 2 мм/с.
В дальнейшем так и не удалось установить какая из двух явилась причиной послеремонтной механической неуравновешенности ротора: высокий остаточный
• Неуравновешенность ротора • 5 —9 •

Рис. 5—07. Схема валопровода и размещения контрольных точек насосного агрегата а вибрации опор при различном расположении дисбаланса. V, Н, А — вертикальные, горизонтально-поперечные и осевые компоненты вибрации.
Нижний график был получен перед выводом в ремонт агрегата, требующего по межремонтному интервалу капитальный ремонт ротора насоса. В процессе частичной разборки насоса при осмотре ротора был обнаружен недопустимый износ рабочих колес, более сильный со стороны электродвигателя, а в некоторых местах кромки лопастей были разрушены.
При механическом дисбалансе осевая вибрация подшипников в силу различных причин может достигать значительных величин и преобладать над поперечной.
В качестве примера можно привести следующий. При обследовании магистрального насосного агрегата мощностью более 10 МВт была обнаружена вибрация подшипниковых опор, превышающая допустимые для эксплуатации значения. Синхронный электродвигатель агрегата имеет гибкий ротор с
• Неуравновешенность ротора • 5—11 •

Рис. 5—09. Форма и спектр сигнала вибрации задней подшипниковой опоры электродвигателя в осевом направлении.
Агрегат был остановлен и проведена балансировка под нагрузкой. Единственный корректировочный груз установили в плоскости коррекции в районе возбудителя, помеченной вертикальной стрелкой на рис. 5 — 08.

Рис. 5—10. Влияние корректирующей массы, установленной в районе возбудителя на вибрации опор магистрального насосного агрегата. Снизу вверх графики СКЗ виброскорости по подшипниковым опорам до (график 1) и после (график 2) установки корректирующего груза, V, И, А — вертикальные, горизонтально—поперечные и осевые компоненты вибрации.
Влияние установки корректировочного груза на изменение уровней вибрации опор магистрального насосного агрегата приведено на рис. 5—10. Вибрация снизилась по всем контрольным точкам на опорах агрегата, а в точках с максимальной вибрацией в несколько раз.
• Неуравновешенность ротора • 5—13 •
повышенная чувствительность к механическому и тепловому дисбалансу осевых компонентов вибрации опор.
Такие типы машин при проведении мониторинга и диагностики следует выделять особо, чтобы недопускать неверного диагноза, поскольку подобные симптомы характерны и для некоторых других дефектов, например, для расцентровки.
Тепловая неуравновешенность ротора.
Тепловой неуравновешенностью ротора будем называть состояние ротора, которое вследствие неравномерного нагрева ротора или изменения его температуры во время вращения приводит к появлению центробежных сил и моментов, вызывающих переменные нагрузки на опоры ротора и его изгиб.
Происхождение тепловой неуравновешенности ротора, и связанного с ней теплового дисбаланса ротора, в большинстве случаев вызывается одной из следующих причин:
• несимметрия тепловых полей ротора электрической машины вследствие витковых замыканий в обмотке ротора, обрывов и растрескивания стержней, при неравномерной толщине изоляции обмотки ротора, отсутствия тепловых зазоров между пазовыми клиньями и др.; при этом допускаемая тепловая несимметрия в большинстве случаев лежит в пределах 0,2...1 0C;
• неравномерное охлаждение ротора вследствие насадки рабочих колес, пром.вставок и других деталей с перекосом и недостаточными осевыми зазорами, нарушения равномерности теплообмена, отсутствие осевых зазоров между насадными деталями ротора;
• изменения остаточных напряжений от термомеханической обработки или многократных перегревов при нагреве ротора, вызывающие перераспределение масс относительно оси ротора; такой тепловой прогиб возможен и при совершенно равномерном прогреве, например, при разогреве ротора после пуска двигателя неуравновешенность ротора может меняться до достижения ротором стабильной температуры;
• разъединение (ослабление) посадки деталей (например железа или массивных дисков) ротора на валу при температурных расширениях;
• касания (задевания) статора ротором ( в т.ч. в лабиринтных уплотнениях) из —за недостаточных зазоров, эксцентриситета или повышенной вибрации.
При асимметрии температурного поля ротор прогибается в сторону большей температуры, что приводит к появлению теплового дисбаланса.
Для свободно опертого стального ротора при линейном распределении температур в радиальном направлении стрела теплового прогиба может быть определена по приближенной формуле:
у = 1,5х10-6 l2 Dt /d ;
где: l — длина ротора, Dt - разность температур между горячей и холодной образующими ротора, d — диаметр ротора.
Например, при длине ротора 8 метров и диаметре 1 метр на каждый градус разницы температур стрела прогиба составит 0,1 мм, что примерно в 20 раз превышает допуск на отклонение центров масс при балансировке на станке.
Характерные особенности тепловой неуравновешенности ротора.
Для тепловой неуравновешенности ротора свойственны диагностические признаки механической неуравновешенности ротора и характерно режимное изменение дисбалансов ротора, при этом каждому установившемуся тепловому режиму соответствует определенная вибрация.
• Неуравновешенность ротора • 5—15 •
критической частоте при выбеге нагретого ротора по отношению к разгону холодного ротора или выбегу неуспевшего прогреться ротора.
При обнаружении диагностических признаков теплового дисбаланса следует учитывать, что в некоторых ситуациях, например, при пуске холодного агрегата, аналогичными диагностическими признаками может сопровождаться изменение соосности роторов агрегата под действием меняющихся температурных полей при разогреве опор и фундамента.
Рис. 5—12 иллюстрирует случай изменения параметров вибрации во времени, имевший место на электрической машине (генераторе) при тепловой неуравовешенности. После пуска машины вибрация определялась вектором ао (вибрация на холостом ходу, верхняя диаграмма) и точками с индексом "0" графиков амплитуды и фазы (соответственно нижний и верхний графики, нижней диаграммы). После приложения 50% —ной нагрузки (на нижней диаграмме момент приложения 50% —ной нагрузки помечен левой вертикальной пунктирной линией) вибрация менялась в продолжение примерно 2,5 часа, причем вначале происходило некоторое снижение, а затем она несколько возросла и, наконец, стабилизировалась.
Моменту стабилизации вибрации соответствует вектор а1 и точки с индексом "1". Далее была приложена номинальная нагрузка (на нижней диаграмме момент приложения номинальной нагрузки помечен правой вертикальной пунктирной линией) после чего снова наблюдалось изменение (рост) вибрации в продолжение примерно 3 часов. Моменту практически полной стабилизации вибрации соответствуют вектор А2 и точки с индексом “2”.
Во многих случаях подобная картина изменения амплитуды вибрации наблюдается во время пуска холодного агрегата при расцентровке, однако в данном случае происходит синхронное изменение как амплитуды, так и фазы вибрации на частоте вращения ротора. Другим важным доводом, говорящим в пользу теплового дисбаланса было то, что после снятия нагрузки по мере охлаждения ротора происходил обратный процесс изменения параметров вибрации. Таким образом, по мере приложения нагрузки к начальному вектору вибрации механического дисбаланса ао добавляются тепловые вектора DА1 и DА2, вызываемые термической деформацией ротора, и общая вибрация является результатом сложения этих векторов.
При несимметрии тепловых полей ротора электрической машины, например, вследствие виткового замыкания в обмотке ротора, обрывов и растрескивания стержней ротора асинхронного электродвигателя, при неравномерной толщине изоляции обмотки ротора, появляется зависимость вибрации от тока ротора, т.е. от нагрузки. Для этой причины характерно режимное изменение дисбалансов ротора, в основном статических, после пуска до рабочего прогрева ротора, затем стабилизация при постоянной нагрузке и новое изменение дисбалансов ротора пропорционально изменению нагрузки до стабилизации новых температурных полей ротора.
Наиболее распространенной причиной теплового дисбаланса роторов турбин является отсутствие осевых зазоров между насадными деталями ротора — рабочими дисками, уплотнительными втулками. Из —за небольших отклонений торцов насадных деталей от перпендикулярности оси при их расширении вместе со значительными осевыми усилиями возникают изгибающие моменты, приводящие к тепловому прогибу ротора.
Известны случаи, когда эта причина исчезала после разгона ротора до скорости срабатывания автомата безопасности за счет ослабления посадочных натягов и перемещения насадных деталей в осевом направлении. Эта же причина теплового прогиба ротора может иметь место на роторах насосов, имеющих насадные диски и работающие на перекачке горячего продукта.
При неравномерном охлаждении ротора вследствие насадки рабочих колес, пром.вставок и других деталей с перекосом и недостаточными осевыми зазорами появляется моментная неуравновешенность ротора с противофазными векторами
• Неуравновешенность ротора • 5—17 •
В качестве примера можно привести встречающееся непрерывное перемещение пакета железа относительно вала электродвигателя. Ослабление посадки железа ротора под действием центробежных сил и теплового расширения пакета при его ориентации относительно вала приводит к тому, что вал изгибается в направлении смещения пакета. Такой изгиб обусловлен тем, что участок вала, контактирующий с пакетом имеет более высокую температуру, чем его противоположная сторона.

Рис. 5—13. Один цикл изменения амплитуды и фазы вибрации опоры электродвигателя на частоте вращения ротора под влиянием разъединения посадки и переориентации теплового прогиба ротора.
Нарастание прогиба сопровождается увеличением вибрации, пока центробежные силы не переориентируют его на полную величину зазора, образовавшегося в результате освобождения посадки. Затем происходит выравнивание и нарастание в противоположную сторону, т.е. временное уменьшение вибрации и последующее нарастание с периодичностью в несколько часов. При переориентировании прогиба ротора и смещении пакета в противоположном направлении фаза вибрации на частоте вращения ротора меняется соответственно на 180 градусов. Величины прогиба ротора и зазора могут быть сравнительно невелики, однако этого достаточно для возникновения значительной тепловой несимметрии ротора.
На рис. 5—13 приведены графики изменения во времени амплитуды и фазы вибрации опоры электродвигателя на частоте вращения ротора, иллюстрирующие полную переориентацию на 180° теплового прогиба ротора: точки 1 и 2 на кривой фазы, график с индексом j°, и соответствующие им максимумы амплитуды, точки 1 и 2 на кривой амплитуды, график А.
Отсутствию теплового прогиба соответствует точка 3 с локальным минимумом амплитуды и промежуточным значением фазы.
• Неуравновешенность ротора • 5—19 •

Рис. 5—15. Разогрев и два цикла изменения амплитуды и фазы вибрации газовой турбины на частоте вращения ротора под влиянием разъединения посадки диска и переориентации теплового дисбаланса ротора.
На рис. 5—15 приведена динамика изменения амплитуды и фазы вибрации газовой турбины на частоте вращения ротора, полученные в процессе испытаний агрегата.
В продолжение примерно 10...15 минут после пуска агрегата амплитуда и фаза вибрации практически не изменялись. Этому периоду соответствует отрезок АВ на графиках амплитуды и фазы вибрации.
Далее, по мере развития теплового дисбаланса и нарушения посадки диска, амплитуда вибрации значительно возрастает (отрезок ВС) примерно в продолжение 50...60 мин, фаза вибрации при этом изменяется в пределах 30°, что говорит о развитии изгиба ротора примерно в одном направлении.
В итоге амплитуда вибрации практически стабилизируется, что говорит о примерно постоянной величине дисбаланса ротора, однако начинается циклическое изменение фазы. Этому периоду соответствуют отрезки СD и DE на графиках амплитуды (А) и фазы (?°) длительностью примерно по 65...70 мин каждый.
Эти же данные, воспроизводящие полный цикл переориентации теплового дисбаланса ротора, представленные в полярной системе координат приведены на рис. 5— 16. Отрезок АВ сливается в точку. Далее вибрация возрастает за счет роста теплового дисбаланса (отрезок ВС). После того, как дисбаланс достигает максимального значения (посадка диска нарушена), он постепенно переориентируется против часовой стрелки относительно неподвижного поперечного сечения ротора. Таким образом тепловой вектор вращается против часовой стрелки относительно точки А, отстоящей относительно начала координат на 11...13 мкм, соответствующей механической неуравновешенности ротора.
• Неуравновешенность ротора • 5 — 21 •

Рис. 5—17. Траектория движения шейки вала в подшипнике скольжения при задеваниях.
При этом возникающие в момент задевания ударные импульсы во многих случаях достаточно хорошо заметны на временных реализациях вибросигнала. Наложенные на кривую вибрации, они следуют с временным интервалом, соответствующим одному обороту ротора.
На рис. 5—17 приведена траектория движения шейки вала в подшипнике скольжения при задеваниях вращающейся детали о неподвижный элемент статора. Появление на кривой движения ротора "пятен" и "всплесков" (один из таких элементов на графике помечен стрелкой) встречается весьма часто, хотя их вид в значительной мере зависит от характера задеваний.
На рис. 5—18 приведена схема валопровода насосного агрегата с асинхроным электродвигателем, на которой стрелкой помечена плоскость задеваний детали ротора о неподвижный элемент статора, и гармонический состав вибрации опор на частоте вращения ротора (график помечен индексом fr ), ее второй и третьей гармониках (2fr, 3fr) в полосе частот с граничными 4 и 12 гармониками (4— 12fr). Диагностические признаки неуравновешенности ротора налицо.
• Неуравновешенность ротора • 5 — 23 •
останова агрегата. Нередко последствием задеваний является остаточный прогиб ротора.

Рис. 5—19. Форма и спектр сигнала вибрации подшипниковой опоры электрической машины при задеваниях ротором статора.
Задевания не всегда приводят к интенсивному росту вибрации. Они также могут быть следствием, а не причиной вибрации. В большинстве случаев небольшие задевания, например, в радиальных уплотнениях, компенсируются местной фрикционной выработкой материала уплотнений. Подобный эффект также иногда наблюдается при задеваниях муфтой защитного кожуха. В крупных агрегатах, например магистральных насосах, выработка щелевых уплотнений может привести к падению КПД до 5 процентов относительно номинального значения, что выражается в виде существенных издержек на электроэнергию.
Устранение тепловой неуравновешенности ротора — прежде всего устранение причины, вызывающей тепловой прогиб, а если это затруднено, то тепловая балансировка, балансировка на рабочих режимах (что может привести к увеличению вибрации агрегата с холодным ротором).
Однако приведенные выше меры не всегда могут дать положительный результат, пример тому — термическая нестабильность дисбалансов ротора.
• Нарушения соосности валов (расцентровка) • 6 — 2 •
примеры некоторых видов траектории движения ротора в подшипнике скольжения при расцентровке, хотя на практике встречаются и более сложные кривые.

Рис. 6—01. Прамеры некоторых траекторий движения ротора в подшипнике скольжения при нарушениях соосности валов: "деформированный" эллипс, "бананообразная" и "восьмеркообразная".
В спектре вибрации практически всегда можно наблюдать преобладающие первую и/или вторую гармоники частоты вращения ротора. Иногда наблюдается сравнительно высокая виброактивность и на гармониках с более высокими номерами, обычно не превышающими 3...5. При нарушениях соосности валов в спектре обычно наблюдается сравнительно низкий уровень шумов, что обусловлено малым уровнем случайной вибрации в вибросигнале.
При значительных нарушениях соосности валов (и отсутствии других развитых дефектов) для формы сигнала виброускорения во многих случаях свойственны следующие особенности: почти периодическая, "нехаотическая"
• Нарушения соосности валов (расцентровка) • 6 — 4 •

Рис. 6—02. Формы и спектры сигналов виброускорения и виброскорости подшипниковой опоры ЭД насосного агрегата при расцентровке.
Некоторые источники (например, J.Mitchell, "An Introduktion to Machinery Analysis and Monitoring", 1981) сообщают, что, "... как правило, если отношение значений виброскорости второй и первой гармоник частоты вращения ротора составляет 0,3.. .0,75, то состояние оборудования не вызывает опасений и срок эксплуатации оборудования не ограничивают во времени. Если это отношение составляет 0, 75. ..1,5, вполне возможно наличие какого — либо повреждения муфты даже при допустимом уровне вибрации, и данная ситуация должна быть тщательно исследована и исправлена при первой же возможности. Когда значение вибрации на удвоенной частоте вращения ротора более чем в 1,5 раза превышает значение
• Нарушения соосности валов (расцентровка) • 6 — 6 •
причем вибрация на первой возросла более чем в 3,5 раза, на четвертой — в 1,4 раза.
Июнь (верхний график) — текущее значение вибрации в 1,9 раза превысило предельно допустимое. В спектре преобладает вибрация на частоте вращения ротора.
После останова агрегата была обнаружена практически только торцевая расцетровка со следующими значениями: осевой сдвиг по вертикали V = 0,07мм, по горизонтали Н = 0,04мм, излом осей по вертикали V= 1,22мм/100мм, по горизонтали V = 0,05мм/100мм. Эта расцентровка появилась в результате весенней подвижки грунта и свайного фундамента в районе заднего подшипника ЭД: опустилась задняя подшипниковая опора (и рама) ЭД. Вибрация на четвертой, восьмой и двенадцатой гармониках частоты вращения ротора (помечена наклонными стрелками) и заметный уровень шумов в спектре были связаны с развивающимися дефектами зубчатой муфты. После замены изношенной муфты и центровки агрегата вибрация опор не превышала 2,1 мм/с.

Рис. 6—04. Спектры вибрации задних подшипниковых опор ЭД и центробежного насоса в вертикальном, горизонтально—поперечном и осевом направлениях при изломе осей.
• Нарушения соосности валов (расцентровка) • 6 — 8 •

Рис. 6—05. Спектры вибрации передних подшипниковых опор ЭД и центробежного насоса в вертикальном, горизонтально—поперечном и осевом направлениях при осевом сдвиге.
На практике в чистом виде радиальная или торцевая расцентровка встречаются реже, чем их комбинация: т.е. анализируя пространственное распределение компонент вибрации и соотношения уровней вибрации на гармонических составляющих спектра достаточно сложно количественно предсказать величины сдвигов и изломов осей по вертикали и горизонтали (особенно при наличии других дефектов агрегата), но это в общем случае обычно не требуется.
Косвенно можно судить об этом с достаточно большой вероятностью имея данные о температуре и давлении масляной пленки вкладышей подшипников: при расцентровке давление и температура более низкого подшипника будет меньше по значению, чем у смежного с ним, но расположенного выше.
• Нарушения соосности валов (расцентровка) • 6 — 12 •
агрегата: осевой сдвиг составил по вертикали V = 0,01мм, по горизонтали Н = 0,02мм, излом осей по вертикали V = 0,01мм/100мм, по горизонтали V = 0,01мм/100мм.
В данном типе мультипликаторов главная ось быстроходного колеса обычно при работе под нагрузкой смещается в сторону от тихоходного и "зависает" в районе "10 часов", если смотреть со стороны переднего подшипника тихоходного вала.
Затем была произведена центровка агрегата с учетом изложенного выше и проведены повторные испытания.

Рис. 6—09. Спектры вибрации подшипниковых опор мультипликатора, и компрессора в осевом направлении до и после центровки с учетом влияющих факторов.
На рис. 6 — 07. приведены вектора вибрации ОА3 и ОВ3 на оборотной частоте ротора при работе под номинальной нагрузкой. Таким образом можно утверждать, что появление векторов вибрации А2A3 и В2В3 связано с тем, что при центровке не учитывались температурные расширения узлов агрегата и положение роторов в подшипниках при работе под нагрузкой.
• Нарушения соосности валов (расцентровка) • 6 — 14 •

Рис. 6—10. Спектры вибрации подшипниковых опор генератора (Т) и возбудителя (В) парового турбоагрегата.
• Нарушения соосности валов (расцентровка) • 6 — 16 •
Каких —либо нарушений жесткости опорной системы возбудителя обнаружить не удалось.
•Нарушения жесткости опорной системы • 7—2 •
односторонними нарушениями жесткости опоры, например с отрывом фундаментной плиты с одной стороны.
Нелинейная жесткость опор характеризуется нарушением пропорциональности между вынуждающей силой и деформациями. Вследствие нелинейности при воздействии гармонической силы возбуждения (вызываемой например, неуравновешенностью ротора) и гармонических (или близких к гармоническим) перемещениях вала опорная реакция может иметь сложный спектр, содержащий различные гармоники (субгармоники) оборотной частоты. Высшие гармонические составляющие опорных реакций возбуждают колебания с соответствующими частотами.
Анизотропность и нелинейность в общем случае не связаны с какими —либо дефектами, тем не менее их влияние на характер вибрации весьма велико. Существенную нелинейность и анизотропность имеет масляный слой: поперечная жесткость масляной пленки в несколько раз (по некоторым данным примерно в 10 раз) ниже, чем вертикальная. На нелинейных опорах могут наблюдаться субгармонические колебания, или субгармонический резонанс. Субгармонические колебания имеют частоту, в целое число раз меньшую частоты вращения, при этом преобладают колебания с половинной частотой. Анизотропность и, в меньшей мере, нелинейность могут возникать и в других элементах опоры при отсутствии в них каких —либо дефектов.
Величина и характер вибрации при ослаблениях жесткости зависит от степени развития дефекта (изменения жесткости системы), величины сил возбуждения (зависящих или независящих от технологических параметров) и свойств конкретного агрегата — анизатропности и нелинейности опорной системы (точно предсказать последние на практике сложно). Вибрационный сигнал обычно имеет сложный характер, в нем обычно присутствуют колебания в широком диапазоне частот: вибрация с частотой возбуждения, ее гармониками и возможно субгармониками, шумовой компонент и, иногда, другими частотными составляющими.
Промышленные агрегаты имеют большое количество соединений, ослабление жесткости которых может привести к повреждению или аварии. Ослабления жесткости можно условно разделить на два класса:
• ослабления жесткости структурных элементов (опорной системы): фундамента (трещины на фундаменте, контакт стола фундамента и перекрытия, осадка фундамента, отрыв фундаментной плиты от фундамента и др.), рамы, корпусных элементов (корпусные трещины), подшипниковых опор, неподвижных деталей подшипников, неподвижного направляющего аппарата и импеллеров;
• ослабления жесткости вращающихся элементов: деталей, крепящихся на роторе, ротора в подшипнике, в зубчатых муфтах, в редукторах.
Диагностические признаки нарушений жесткости.
При некоторых видах нарушений жесткости траектория движения ротора агрегата в подшипнике может сильно отличаться от эллиптической: ротор может совершать хаотическое движение в подшипнике. На рис. 7 — 01 приведена траектория движения центра ротора электродвигателя за один оборот при значительном износе вкладыша и ослаблении крепежа в подшипнике скольжения.
Во многих случаях характерным признаком ослаблений является зависимость уровня и характера вибрации от направления измерений. Этот эффект помечен горизонтальными стрелками: размах колебаний по вертикали составляет примерно 65 мкм, в то время как по горизонтали — менее 25 мкм.
Весьма характерна также высокая гармоническая активность. Вертикальными стрелками помечены семь минимумов кривой, свидетельствующих о нарушении жесткости именно в этом направлении, в то время как в горизонтальной плоскости их число значительно меньше.
• Нарушения жесткости опорной системы • 7—4 •

Рис. 7—02. Спектр вибрации подшипниковой опоры электродвигателя насосного агрегата в вертикальном направлении, имеющего дефект прокладки виброизолятора.
На рис.7 —03 приведена картина развития ослабления жесткости в течение десяти месяцев.
Январь — в спектре наблюдается две преобладающие спектральные составляющие: на частоте вращения ротора и ее третья гармоника (помечена наклонной стрелкой) и относительно высокий уровень шумов — 0.3 ... 0.4 мм/с.
Апрель — увеличивается гармоническая активность на частоте вращения ротора и ее гармониках (помечены наклонными стрелками).
Июнь — вибрация на гармониках частоты вращения ротора продолжает увеличиваться, появляется заметная вибрация на дробных гармониках частоты вращения ротора (помечены вертикальными стрелками), возрастает уровень шумов.
Ноябрь — резко возрос уровень вибрации на частоте вращения ротора.
После останова при ревизии обнаружено аварийное состояние подшипника.
Вибрация на высших гармониках частоты возбуждения бывает весьма велика и может даже быть сравнима с вибрацией на частоте возбуждения.
Обычно с увеличением номера гармоники частоты возбуждения (особенно в случае развитых дефектов и больших значений сил возбуждения) величина вибрации уменьшается. Но в процессе зарождения и развития дефекта, вибрация на одной или нескольких высших гармониках в продолжение ряда измерений могут превосходить вибрацию на частоте возбуждения.
Можно сказать, что чем ближе дефектное соединение (сочленение, место с нарушением жесткости) к ротору (в системе фундамент — рама — опора — подшипник —ротор), тем интенсивней проявляется нелинейность, т.е. интенсивней высшие гармоники частоты вращения ротора (или иной частоты возбуждения) по отношению к первой, в сигнале вибрации.
• Нарушения жесткости опорной системы • 7—6 •

Рис. 7—04. Три спектра измеренные с интервалом в 1 секунду при нарушении центровки и износе вкладышей подшипников воздуходувки с частотой вращения ротора 25 Гц.
Если наблюдать спектр сигнала на экране анализатора, особенно анализатора, работающего в реальном времени, то бывают хорошо заметны "флуктуации гармоник" — от кадра к кадру на экране анализатора на "картинках" спектра уровни вибрации на гармониках частоты возбуждения и уровень шумов (характерные для нарушений жесткости) значительно меняются. При этом усреднение спектров должно отсутствовать.
На рис. 7 — 04 приведены спектры вибрации иллюстрирующие этот эффект. Горизонтальными стрелками помечены флуктуирующая по величине вибрация на второй и третьей гармониках частоты вращения ротора, а вертикальными — меняющийся уровень шумов.
При ослаблениях жесткости (и отсутствии других дефектов)4 для формы сигнала виброускорения, в ряде случаев, свойственны следующие особенности:
• непериодический, хаотический характер кривой вибрации: нет повторяющейся "картинки" кривой вибрации от оборота к обороту ротора;
• нерегулярные интервалы между преобладающими пиками, количество и величина которых (в продолжение временного интервала, соответствующего нескольким оборотам ротора) могут значительно меняться; при этом пиковое значение может достигать 6д и более в случае развитых дефектов;
Однако этого может не наблюдаться (особенно при сильном развитии некоторых видов нарушений жесткости) при "удаленности" плоскости ослабления жесткости от ротора.
• Нарушения жесткости опорной системы • 7—8 •
Вертикальными стрелками помечены следующие с периодом, соответствующим одному обороту ротора три периодических максимума, величина которых в продолжение пяти оборотов значительно уменьшилась.

Рис. 7—06. Форма сигнала вибрации в вертикальном направлении подшипниковой опоры насоса при несимметричном отставании опоры от рамы насосного агрегата. Частота вращения ротора — 50 Гц (20мс/об).
При нарушениях жесткости кривая сигнала вибрации может быть сильно асимметрична, положительные и отрицательные значения амплитуд могут отличаться в 1,5 и более раз5.

Рис. 7—07. Форма сигнала осевой компоненты вибрации передней подшипниковой опоры насоса при отставании подшипниковой опоры насоса от рамы насосного агрегата. Частота вращения ротора насоса 50 Гц (20мс/об).
На рис. 7 — 07 приведен пример асимметричной формы кривой сигнала вибрации наблюдавшегося в осевом направлении измерений на передней подшипниковой опоре насоса при одностороннем отставании подшипниковой опоры насоса от рамы. Стрелками помечены максимум и минимум, абсолютные значения которых отличаются более, чем в два раза. Следует отметить почти периодический вид кривой сигнала вибрации (часто наблюдающийся при развитых нарушениях жесткости и достаточной "удаленности" дефектного соединения от
• Нарушения жесткости опорной системы • 7—10 •
V04, МВ1-МВ2--МВЗ-МВ4, МS1-МS2-МS3-МS4, РВ1-РВ2-РВЗ-РВ4 можно отметить, что вибрация в точках V01, VВЗ, MS3 и РВ4 (помечены на рис. 7 — 09 горизонтальными стрелками) выше, чем в других из соответствующих групп, что явно указывает на локализацию причины повышенной вибрации в области правой стойки фундамента в районе заднего подшипника ЭД.

Рис. 7—08. Схема расположения точек измерений питательного насосного агрегата.

Рис. 7—09. Распределение СКЗ виброскорости по точкам измерения вибрации на питательном насосном агрегате.
На рис. 7— 10 приведены спектры вибрации трех контрольных точек (V01, МВЗ, МS3) в области правой стойки фундамента в районе заднего подшипника ЭД и двух точек (НР8, НР9) непосредственно на стойке. Спектры вибрации этих точек имеют как общие черты, так и различия. На спектрах вибрации точек V01, МВЗ,
• Нарушения жесткости опорной системы • 7—12 •
показано изменение характера вибрации на фундаментной стойке в двух близлежащих точках: с расстоянием примерно 1 см между точками ввода (см рис. 7-08).
Приведенные на рис. 7—11 форма и спектр сигнала вибрации одной из точек фундаментной стойки не могут дать решающего перевеса в доводах в пользу нарушений жесткости. На осциллограмме однонаправленными стрелками помечены в какой —то мере свидетельствующие в пользу ослаблений жесткости некоторая небольшая несимметричность сигнала вибрации, флуктуации фазы гармонических составляющих и флуктуации амплитуды вибрации от оборота к обороту. Однако, эти признаки проявляются весьма слабо: например, аналогичными признаками могут обладать спектры и формы сигналов вибрации при расцентровке.

Рис. 7—11. Форма и спектр сигнала вибрации измеренные в точке НР8 правой стойки фундамента со стороны агрегата над трещиной.
Наглядно демонстрирует свои возможности метод локализации нарушений жесткости с помощью снятия контурной характеристики. На рис. 7—12 приведена снятая в горизонтально — поперечном направлении по 12 —и точкам вдоль задней подшипниковой опоры ЭД и правой фундаментной стойки контурная характеристика вибрации.
На графиках амплитуды и фазы вибрации на частоте вращения ротора между контрольными точками (точками ввода) НР8 и НР9, отделенными друг от друга сантиметрами, заметен скачек: фаза вибрации изменяется на 70 градусов, а амплитуда уменьшается более, чем в 4 раза.
• Нарушения жесткости опорной системы • 7—14 •
вибрации на насосе и допустимую вибрацию ЭД. Вибрация переднего подшипника насоса (контрольные точки на рис. 7—14 помечены горизонтальными стрелками) выше, чем заднего (контрольные точки на рис. 7—14 помечены вертикальными стрелками).
Кроме того можно отметить что на каждой из подшипниковых опор насоса горизонтально — поперечный компонент вибрации наибольший, а вертикальный наименьший.

Рис. 7—14. Распределение СКЗ виброскорости по точкам измерения вибрации на насосном агрегате.
На рис. 7—15 приведены спектры вибрации контрольных точек на крышках переднего и заднего подшипников насоса. Спектры вибрации почти всех точек имеют 4 преобладающих гармоники частоты вращения ротора (помечены наклоненными вниз стрелками). Уровни высших гармоник (5-й и выше) существенно (в 4...8 раз) меньше уровня первой.
В процессе проведения измерений вибрации в горизонтальном направлении были заметны флуктуации гармонических составляющих спектра: от кадра к кадру на экране анализатора на "картинках" спектра значения первых 4-х гармоник изменялись на 15...30 %.
Отношение значения вибрации в горизонтально — поперечном направлении к значению вибрации в вертикальном направлении на частоте вращения ротора на передней и задней подшипниковых опорах насоса (см. спектры точек VОЗ и НОЗ, а также спектры точек V04 и Н04 ) составляет соответственно 5,22 и 9,1, что говорит о чрезмерной гибкости опоры в горизонтальном направлении.
Возбуждение вибрации вызывается небольшой расцентровкой агрегата, что следует из анализа спектра АОЗ, вторая гармоника которого помечена наклоненной вверх стрелкой.
• Нарушения жесткости опорной системы • 7—16 •
виброданных ЭД и насоса показывает, что возбуждение вибрации вызвано нарушением центровки насоса и ЭД.

Рис. 7—16. Спектры вибрации передней подшипниковой опоры насоса насосного агрегата в горизонтально— поперечном и осевом направлениях.

Рис. 7—17. Контурная характеристика вибрации передней опоры насоса в горизонтально-поперечном направлении.
При снятии контурной характеристики вибрации передней опоры насоса рис. 7—17 обнаружен скачек фазы на 60 градусов и уменьшение вибрации в 4 раза
• Нарушения жесткости опорной системы • 7—18 •
В ряде случаев при ослаблениях жесткости наблюдается влияние крутящего момента на вибрацию агрегата.
Это происходит при зависимости сил возбуждения от крутящего момента, ослаблениях в подвижных муфтах (ослаблении посадки муфт, износе и разрушении рабочих поверхностей, нарушении контакта по зубьям, кулачкам, пружинам), отрыве опорной поверхности под действием реактивного момента статора и др.
Вибрация насосного агрегата с консольным расположением ротора насоса, перекачивающего углеводороды, с ЭД мощностью 30 кВт, подшипниками качения и трехкулачковой муфтой, соединяющей ЭД и насос, превышала норму. После проведения измерений агрегат был остановлен и выведен в ремонт. При ревизии было установлено разрушение резиновой прокладки трехкулачковой муфты.
Вибрация бала велика по всем опорам агрегата и существенно преобладала по вертикали. На рис. 7—18 приведены формы сигналов виброускорения и спектры сигналов виброскорости, измеренных на переднем подшипнике насоса в вертикальном направлении при ступенчатом разгружении агрегата от номинальной нагрузки до половины номинальной нагрузки, а затем до холостого хода. Примерно такой вид спектра был характерен и для ряда других контрольных точек.
На спектрах преобладают четыре гармоники "кулачковой" частоты, соответствующей утроенной частоте вращения ротора, помеченные горизонтальными стрелками.
Спектр и форма сигнала вибрации типичны для ослаблений жесткости: высокая гармоническая активность, высокий уровень шумового компонента, непериодичная форма кривой виброускорения.
По мере уменьшения крутящего момента вибрация, вызванная люфтом в муфте (помечена горизонтальными стрелками), снижалась, причем интенсивней при малых значениях крутящего момента. Характерно, что СКЗ и пиковое значение виброускорения по отношению к виброскорости при разгружении изменились значительно меньше (в пределах 20...30%), как и уровень шумов в спектре.
Интенсивная вибрация указывает на развитый дефект.
Приведенные ниже данные измерения вибрации наблюдались на компрессорном агрегате, сконструированном и смонтированном таким образом, что не допускались перемещения ЭД и мультипликатора друг относительно друга в поперечном и осевом направлении, т.е.
была ограничена возможность по центровке ЭД и мультипликатора агрегата.
Ремонтный персонал, при необходимости, имел возможность несколько уменьшить несоосность роторов ЭД и мультипликатора изменяя зазоры в подшипниках в пределах допусков на зазоры, проверяя качество центровки при работе агрегата после прогрева под нагрузкой, совмещая эту операцию с балансировкой на месте под нагрузкой. Обычно агрегат после ремонта имел допустимую несоосность, значения которой близки к границам допусков, и вибрацию несколько снижали балансировкой на месте при номинальной нагрузке.
На рис. 7—19 приведены вектора вибрации на оборотной частоте при балансировке ротора ЭД в собственных подшипниках на холостом ходу ОА01 , ОА11, ОА21, ОВо1, ОB11, ОВ21 и под нагрузкой Оаo, ОА1, ОА2, ОВ0, ОВ1, ОВ2, соответственно до установки корректирующих масс (индекс "О"), после установки корректирующей массы в плоскости коррекции в области задней опоры А (индекс "1") и после установки корректирующей массы в плоскости коррекции в области передней опоры В (индекс "2"). Нагрузочные вектора вибрации А01А0, А11А1, А21А2 — при всех пусках пропорциональны вибрации на холостом ходу и приводят к увеличению вибрации под нагрузкой, треугольники, полученные при соединении вершин векторов вибрации на XX и под нагрузкой подобны и лишь вращаются относительно начала координат (признак ослаблений жесткости).
• Нарушения жесткости опорной системы • 7—20 •

Рис. 7—20. Спектры вибрации до и после проведения балансировки на месте и ремонта подшипника.
• Нарушения жесткости опорной системы • 7—22 •
проскальзывании детали на валу и обуславливающих возникновение сложных сигналов вибрации.

Рис. 7—22. Формы и спектры сигналов вибрации передней подшипниковой опоры насоса в вертикальном и поперечно—осевом направлениях при нарушении посадки соединительной муфты.
Приведенные ниже данные измерения вибрации измерены на насосном агрегате, имевшем нарушение посадки насадного диска на вале на входе рабочего колеса центробежного насоса.
На рис. 7 — 23 приведены спектры вибрации заднего и переднего (индексы 1 и 2) подшипниковых щитов ЭД и передней и задней опор насоса (индексы 3 и 4) измеренные в вертикальном направлении. Вибрация
• Нарушения жесткости опорной системы • 7—24 •

Рис. 7—24. Спектры вибрации передней подшипниковой опоры насоса в вертикальном направлении до и после возникновения нарушения посадки насадного кольца на валу насоса.
Нарушение посадки кольца приводит к появлению в спектре малозаметной и труднообнаруживаемой составляющей на частоте 6,8 Гц (fm), вклад которой в общую величину вибрации крайне мал, в то время как угловые колебания ротора, возникающие из —за периодического изменения жесткости посадки кольца при проскальзывании, приводят к значительной угловой модуляции частоты вращения ротора. Следовательно, появляются весьма заметные боковые частотные составляющие kfr ± nfm вокруг составляющей на частоте вращения ротора и ее гармоник. В частности, две из них, возникшие вокруг составляющей на частоте вращения ротора (fr ), на рис. 7 — 24 помечены индексами fr + nfm и fr - nfm .
• Дефекты подшипников скольжения • 8 — 2 •
"Вихревая смазка" (Oil whirl).
Опыт эксплуатации агрегатов, имеющих гибкие ротора, показывает, что такое снижение устойчивости, а в отдельных случаях возникновение высокоинтенсивных автоколебаний на масляной пленке, более характерно для роторов с рабочей частотой вращения, превышающей первую критическую частоту вращения ротора, но меньше его удвоенной первой критической частоты вращения. В большинстве случаев "вихревая смазка" связана с существенной разгрузкой подшипника или поворотом вектора нагрузки на подшипнике против вращения вала (другие причины приведены ранее).

Рис. 8—01. Траектория движения шейки вала в подшипнике скольжения при "вихревой смазке".
"Вихревая смазка" может вызывать интенсивную вибрацию на частоте 0,42...0,48 fr и ее гармониках. Эта вибрация определяется прямой прецессией вала в подшипнике под действием смазки.
Влияние " вихревой смазки" на форму траектории движения шейки вала в подшипнике скольжения заключается в том, что она по сравнению, например, с формой траектории при дисбалансе значительно усложняется: если при дисбалансе обычно это эллипс, то при "вихревой смазке" внутри эллипса появляется петля, вращающаяся в направлении движения ротора. На рис. 8 — 01 приведена достаточно типичная траектория движения шейки вала в подшипнике скольжения при "вихревой смазке", хотя на практике встречаются и более сложные кривые. Цифрой 1 на кривой помечена точка, соответствующая началу одного из оборотов ротора, цифрой 3 — точка, соответствующая завершению этого оборота и началу следующего оборота ротора, цифрой 2 — точка, соответствующая завершению второго оборота ротора (а также цикла вращения состоящего из двух оборотов ротора). Таким образом за временной интервал, соответствующий одному обороту ротора можно увидеть примерно половину одного цикла вращения. Петля
• Нарушения соосности валов (расцентровка) • 6 — 10 •
муфта не может быть заклинена. Аналогично и для абсолютной вибрации подшипниковых опор — в случае расцентровки вибрации смежных опор в осевом направлении, измеренные с разных сторон муфты должны находиться в противофазе (при отсутствии вибрации, вызванной другими причинами).
В качестве иллюстрации вышеизложенного на рис. 6 — 06 приведены графики амплитудных спектров и взаимного фазового спектра вибрации в осевом направлении внутренних подшипниковых опор ЭД и насоса магистрального насосного агрегата при расцентровке со значениями: осевой сдвиг по вертикали V=0,06мм, по горизонтали Н = 0,10мм, излом осей по вертикали V = 0,35мм/100мм, по горизонтали V = 0,46мм/100мм. Также был обнаружен дефект муфты. Разность фаз вибраций подшипников на частоте вращения ротора составляет 190 градусов (см. точки, помеченные стрелками), т.е. вибрации практически антифазны. Для вибраций на второй и третьей гармониках частоты вращения ротора разность фаз составляет соответственно 5 и 7 градусов, т.е.
вибрации практически синфазны.
Часто, и достаточно обоснованно, администрация предприятий предоставляет возможность проводить специальные исследования вибрации специалистам по вибродиагностике на работающем оборудовании только в крайней нужде — когда многократные ремонты не приводят к снижению вибрации, или внеплановые остановы приносят ощутимый экономический ущерб. Но в момент вывода агрегата или технологической установки из ремонта, например, на нефтехимическом предприятии обычно раз в год, можно получить весьма ценную, хотя и не всеохватывающую, информацию о вибрации. Это касается влияния крутящего момента и теплового состояния агрегата на вибрацию, снятия частотной характеристики, а также получения каскадных спектров. Приведенный ниже пример иллюстрирует это.
В соответствии с рекомендациями завода изготовителя при выводе компрессорного агрегата из ремонта проводились испытания по следующей схеме: пуск агрегата на холостом ходу, выдержка в течение четырех часов, четырехступенчатое увеличение нагрузки до номинальной с выдержкой по часу между ступенями, одноступенчатое снятие нагрузки и останов агрегата с возможностью проведения осмотра и, при необходимости, ремонта перед пуском технологической установки.
Центровка компрессора и мультипликатора проводилась без учета тепловых расширений корпуса мультипликатора и опор компрессора после пуска агрегата, а также без учета толщины масляной пленки и типичного положения шеек валов в подшипниках при работе под нагрузкой.
На рис. 6 — 07 приведена картина поведения векторов вибрации на частоте вращения ротора (измеренных в осевом направлении на передней подшипниковой опоре компрессора, индекс А, и крышке заднего подшипника быстроходного вала мультипликатора, индекс В) в процессе нагружения агрегата. Вектора вибрации ОА0 и ОВ0 получены при измерении вибрации непосредственно после пуска агрегата, ОА1 и ОВ1 после четырехчасовой выдержки и достижения стабильного теплового режима, ОА2 и ОВ2 при номинальной нагрузке агрегата. Таким образом вектора А0А1 и В0В1 — вектора вибрации, возникшие от тепловых расширений мультипликатора и компрессора, а А1A2 и В1B2 — нагрузочные.
Можно считать, что эти вектора параллельны и разнонаправлены (для удобства восприятия на графике проведены две параллельные прямые).
Характер изменений параметров вибрации в этих и других контрольных точках агрегата при его разогреве и нагружении указывает на расцентровку компрессора и мультипликатора.
• Дефекты подшипников скольжения • 8 — 4 •
Гц (S0.41 ), частоту вращения ротора (S 1), ее вторую (S2 ) и третью (S3 ) гармоники, а также в полосу 152... 500 Гц (S4-10 ) приведен на рис. 8 — 02.
Причиной низкочастотной вибрации оказалось нарушение центровки роторов низкого давления и генератора (что очевидно, если проанализировать соотношение частотных составляющих вибрации), приведшее к разгрузке четвертой и шестой опор (индексы контрольных точек на рис. 8 — 02 — ТО и GI) более, чем на 50%. Разгрузка указанных опор сопровождалась и более низкими температурой подшипников 4 и 6 и давлением в масляном клине этих же подшипников. Был поставлен вопрос о возможности дальнейшей, пусть даже кратковременной, эксплуатации турбоагрегата.

Рис. 8—03. Спектры вибрации опоры №4 турбоагрегата К—200—130 в горизонтально-поперечном, направлении при различных режимах усреднения под влиянием, нарушения центровки и "вихревой смазки".
Известно, что низкочастотная вибрация может и не говорить о достижении агрегатом предельного состояния, если образующая ее составляющая (0,42...0,48kfr ) невелика и имеет малую флуктуацию по амплитуде. Необходимо постоянно сравнивать величину низкочастотной составляющей с величиной вибрации на частоте вращения ротора: опыт показывает, если низкочастотная вибрация значительно меньше вибрации на частоте вращения ротора, агрегат может успешно работать в течение достаточно длительного времени.
На рис. 8 — 03 приведены два спектра виброперемещения опоры №4 в горизонтально — поперечном направлении. Верхний спектр получен при обработке вибросигнала "среднеарифметическим спектральным усреднением" по восьми спектрам, т.е. каждая частотная составляющая итогового спектра является средней арифметической величиной из восьми составляющих той же частоты, полученных в процессе последовательного измерения и обработки восьми спектров.
Нижний спектр получен в режиме т. н. "максимального пика", т.е. каждая частотная составляющая итогового спектра выбирается максимальной из восьми
• Дефекты подшипников скольжения • 8 — 6 •
"Взбиваемая смазка"(Oil whrip).
В отличие от "вихревой смазки", возникновение таких автоколебаний на масляной пленке чаще встречается у роторов с рабочими частотами вращения, вдвое превышающими их первую критическую частоту, и требует подвода внешней энергии, подпитывающей вихрь, связанной, например, с воздействием вибрации или нагрузки. "Взбиваемая смазка" может вызывать интенсивную вибрацию подшипника скольжения на частотах, близких к первой критической частоте вращения ротора и ее гармониках.
Иллюстрацией может служить такой случай: во время пуска турбоагрегата К —300 —240 —ТВВ —320 —2 возникли низкочастотные колебания, наиболее интенсивные в районе шестого подшипника (генератора со стороны турбины), которые нарастали по мере увеличения нагрузки. Размах виброперемешения достиг 140 мкм при 100% нагрузке. Вертикальный компонент вибрации в 1,5...2 раза превышал горизонтальные. Вибрация других опор была существенно меньше. На рис. 8 — 05 приведен спектр вертикального компонента вибрации опоры №6.

Рис. 8—05. Спектр вертикального компонента вибрации опоры N6 турбоагрегата К—300—240—ТВВ—320—2 под влиянием "взбиваемой смазки .
Вертикальными стрелками помечена первая (15,54 Гц) и некоторые высшие (31,08; 46,62; ... Гц) гармоники низкочастотных колебаний. Горизонтальными стрелками помечены частота вращения ротора (50 Гц) и ее гармоники. Наклонными стрелками помечены суммарные и разностные частоты низкочастотной вибрации и первой (34,45 и 56,54 Гц), а также второй (84,46 и 116,54 Гц) гармоник частоты вращения ротора. Частота 15,54 Гц практически совпадает с первой критической частотой ротора генератора. Наличие "масляной вибрации" очевидно.
Далее произвели разгружение турбоагрегата — на рис. 8 — 06 приведен каскадный спектр вибрации при снижении нагрузки с 290 МВт до 200 МВт.
Каждый последующий график спектра записывался при снижении нагрузки
• Дефекты подшипников скольжения • 8 — 8 •
интенсивная низкочастотная вибрация. На Рис. 8 — 07 приведен спектр вибрации паровой турбины, возникающий при превышении пороговой нагрузки (80% от номинальной). Стрелками помечена собственная частота ротора турбины 26,29 Гц и ее некоторые гармоники. Примечательно, что частота вращения ротора меньше его удвоенной собственной частоты.

Рис. 8—07. Спектр вертикальной компоненты вибрации опоры паровой турбины компрессорного агрегата под влиянием "взбиваемой смазки".
В результате работ по снижению парового возбуждения, достигнутого перераспределением радиальных и осевых зазоров в проточной части турбины, низкочастотная вибрация была устранена.
"Сухой вихрь"(Dry whirl).
"Сухой вихрь" — низкочастотная вибрация, возникающая при разрыве масляной пленки и контакте (трении) между валом и подшипником, вызванном неравномерной или неправильной смазкой подшипника (нарушение подачи и качества масла). В этих условиях при контакте поверхности вала и подшипника появляется "скрип" и, в результате, скачкообразное движение вала, сопровождающееся обычно повышением температуры подшипника. При этом может возбуждаться вибрация на резонансных частотах подшипника, субгармониках частоты вращения ротора (например, 1/2 или 1/3 fr ), гармонических (kfr ) и "дробных" гармонических частотах (1,5, 2,5, 3,5 ... fr ) как в области средних, так и высоких частот.
Влияние "сухого вихря" на форму кривой траектории движения ротора в подшипнике заключается в том, что она по сравнению, например, с формой кривой при "вихревой смазке" имеет неподвижную петлю, появляющуюся при наблюдении двух и более последовательно выводимых на экран виброанализатора оборотов ротора. На рис. 8 — 08 приведен пример траектории вала в подшипнике скольжения при возникновении "сухого вихря", хотя на практике встречаются и более сложные кривые.
Горизонтальной стрелкой показано направление движения
• Дефекты подшипников скольжения • 8 — 10 •

Рис. 8—09. Спектр вибрации при перекосе оси вкладыша подшипника и оси вращения ротора (нарушение верхнего и боковых зазоров подшипника) и возникновении неравномерной смазки и разрывов масляной пленки.
Дефекты опорных подшипников.
Опорные подшипники воспринимают радиальные усилия на ротор и фиксируют его радиальное положение относительно корпуса. Основные причины выхода из строя опорных подшипников следующие: повышенное давление в радиальном направлении из —за нарушений технологических или расчетных режимов; нарушение подачи масла и качества масла; дефекты сборки и подгонки; эксплуатационный износ и загрязнение подшипников.
Повышенное давление в радиальном направлении из—за нарушений технологических или расчетных режимов, нарушения подачи и качества масла.
Повышенное давление и нарушение подачи и качества масла во многих случаях мало влияют на характер вибрации агрегатов, но в большинстве случаев приводят к повышению температуры и/или давления в клине наиболее нагруженных подшипников. Это явление обычно сопровождается ускоренным износом и/или повреждением баббитового слоя вкладыша подшипника, наволакиванием материала подшипника на шейку вала, и может приводить к внезапному скоротечному выходу подшипника из строя (см. "Заедание").
Неудовлетворительное состояние шеек, изготовления, подгонки и сборки подшипника. Приработка подшипника.
Нарушение подгонки и последующая приработка (и свойственные ей диагностические признаки) — явление временное, обычно возникающее при выводе агрегата из ремонта и пуске его в эксплуатацию. Маловероятно
• Дефекты подшипников скольжения • 8 — 12 •
Нарушения подгонки и сопровождающая их приработка могут приводить к последствиям, делающим невозможной дальнейшую эксплуатацию оборудования, например, таким, как изгиб и деформация (возможно остаточная) вала.
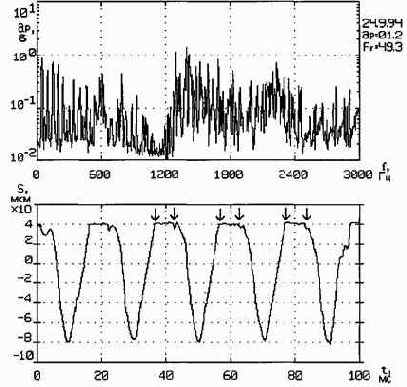
Рис. 8—11. Форма и спектр сигнала вибрации подшипниковой опоры, наблюдавшиеся при нарушении подгонки и приработке подшипника.
Повышенный зазор в подшипнике, неравномерные зазоры по радиальной плоскости (нарушение цилиндричности формы вкладыша), нарушение постоянства величины верхнего зазора и боковых зазоров вдоль оси.
Повышенный радиальный зазор и/или его неравномерность в подшипнике вследствие дефектов изготовления или эксплуатации приводят к сложной зависимости жесткости смазочного слоя от угла поворота, что практически всегда вызывает увеличение вибрации на частоте вращения ротора и особенно ее высших гармониках. Однако, определенная неравномерность зазора может повысить устойчивость вращения ротора в подшипнике, для чего, например, применяется эллиптическая расточка вкладыша подшипника.
Нарушение верхнего и боковых зазоров в подшипнике может также приводить к разрыву масляного клина и возникновению "сухого вихря", что сопровождается повышением температуры подшипника (см. выше по тексту).
• Дефекты подшипников скольжения • 8 — 14 •

Рис. 8—13. Форма и спектр сигнала вибрации подшипниковой опоры, наблюдавшиеся при пониженном зазоре и наклепе подшипника.
На рис. 8—13 приведены форма и спектр сигнала вибрации подшипниковой опоры ЭД насосного агрегата, наблюдавшиеся в процессе приработки при пониженном (относительно номинальной величины) зазоре и развивающемся наклепе подшипника. Диагностические признаки в этом случае практически совпадают с диагностическими признаками нарушений жесткости и приработки подшипника.
Нарушение состояния баббитового слоя во вкладыше подшипника может приводить к появлению импульсов (возрастанию случайной вибрации) на кривой вибросигнала в момент приближения траектории движения вала к локальным дефектам, иногда сопровождаемые повышением температуры подшипника. Жесткость масляной пленки в момент приближения вала к локальному дефекту, уменьшается, что происходит раз за оборот вала (fr), а также происходят флуктуации давления при упругогидродинамическом взаимодействии в этот момент.
Нарушения жесткости крепления.
Нарушения жесткости крепления подшипников связаны с нарушением плотности прилегания вкладышей (колодок, опорных подушек) к постели; нарушением плотности прилегания вкладышей друг к другу в разъеме (проверяется при капремонте, при перезаливке и замене вкладышей); нарушением натяга между крышкой подшипника и верхним вкладышем, и все эти дефекты имеют диагностические признаки нарушений жесткости, изложенные в соответствующей главе.
• Дефекты подшипников скольжения • 8—16 •
опорам компрессорного агрегата. Легко заметна преобладающая вибрация компрессора в осевом и горизонтально — поперечном направлениях.

Рис. 8—15. Спектры вибрации передней и задней подшипниковых опор компрессора под влиянием неудовлетворительной площади контакта и нарушения величины номинального осевого зазора в упорном подшипнике компрессора.
Осевую вибрацию опор компрессора могут вызывать различные причины: например, расцентровка, неуравновешенность ротора, дефекты упорного подшипника и др. Анализ спектров и распределение вибрации по опорам (преобладающая вибрация наблюдается на частоте вращения ротора компрессора fr2 (79,6 Гц) в осевом и чуть меньше в горизонтально — поперечном направлениях (рис. 8—15)) скорее говорит в пользу дефекта упорного подшипника, хотя на практике подобная картина встречается, как говорилось выше, и при других дефектах.
• Дефекты подшипников скольжения • 8 — 18 •

Рис. 8—17. Спектры пространственных компонент вибрации передней и задней подшипниковых опор ЭД под влиянием эксплуатационного износа и нарушения величины номинального осевого зазора в подшипнике.

Рис. 8—18. Спектр вибрации задней подшипниковой опоры ЭД в осевом направлении под влиянием эксплуатационного износа и нарушения величины номинального осевого зазора в подшипнике.
• Дефекты подшипников качения • 9 — 2 •
нарушения смазки, 30% — нарушения сборки и установки, 20% — неправильное применение, повышенная вибрация и др. и только 10% — естественный износ. Основные частоты составляющих вибрации при дефектах подшипников качения приведены в таблице 9 — 1.
Влияние нелинейной жесткости подшипников на вибрацию подшипников.
Выражается в появлении дополнительных гармонических составляющих вибрации из —за неодинаковой статической и динамической нагрузки на тела качения (непостоянства жесткости подшипника при вращении ротора) даже при отсутствии дефектов изготовления, сборки и при низкой остаточной неуравновешенности ротора.
Поскольку статическая нагрузка (в большинстве случаев — сила тяжести горизонтально расположенного ротора) воздействует одновременно на 2...4 тела качения и число этих тел изменяется во времени с частотой перекатывания по наружному кольцу, возникают параметрические колебания с частотой kf0. При достаточно больших значениях неуравновешенности ротора может возникать амплитудная модуляция колебаний с частотой f0 перекатывания тел качения частотой fr и появлением в спектре составляющих f0 ± fr.
Частоты основных составляющих вибрации при дефектах подшипников качения с вращающимся внутренним и неподвижным наружным кольцами.

• Дефекты подшипников качения • 9 — 4 •

f f0 — частота возбуждения при изменении формы внешней дорожки:

f rrol - резонансная частота тел качения:

где:
f r — частота вращения внутреннего кольца (ротора) подшипника;
z го1 — число тел качения в подшипнике;
d го1 — диаметр тел качения в подшипнике;
d cg — диаметр сепаратора (делительной окружности, окружности проходящей
через центры тел качения) подшипника качения;
a — угол контакта тел и дорожек качения в подшипнике;
k, k 1 , k 2 — натуральные числа 1, 2, ...;
Е — модуль упругости;
r — удельная плотность шариков.
Влияние дефектов изготовления и сборки на вибрацию.
Дефектами изготовления подшипников качения являются отклонения геометрических размеров и формы деталей подшипника от конструктивных (несоблюдения допусков изготовления колец, сепаратора и тел качения, овальность и гранность дорожек и тел качения, равномерность тел качения) и нарушение шероховатости поверхности качения.
Дефектами сборки подшипникового узла являются появление радиального натяга в подшипнике, перекос внутреннего и наружного колец подшипника, принудительное центрирование валов при стыковке узлов агрегата и перекос соединительных муфт.
Характерные частоты дефектов изготовления и сборки приведены в табл.1.
Если отсутствует радиальный зазор в подшипнике, вследствие нарушения посадки или дефектов ротора, появляется вибрация, содержащая комбинации частот составляющих, вызываемых всеми дефектами, имеющимися в подшипнике, причем увеличивается уровень вибрации, создаваемый дефектами наружного кольца.
Для радиальных подшипников, имеющих осевую нагрузку характерно отсутствие радиального зазора и высокая чувствительность к качеству сборки подшипникового узла. Небольшие перекосы колец, всегда появляющиеся при сборке подшипника, перераспределяют нагрузку на тела качения преимущественно в две противоположные точки кольца. Радиальный натяг, вызываемый осевой нагрузкой, может приводить к появлению комбинационных частот дефектов.
Влияние дефектов износа поверхностей качения на вибрацию.
Дефекты износа поверхностей качения влияют на характер вибрации во всем частотном диапазоне, поскольку в процессе износа увеличивается коэффициент трения и при взаимодействии дефектных поверхностей возникают периодические удары, что приводит к росту интенсивности высших гармоник и увеличению случайных составляющих в сигнале вибрации. Для проявления дефектов износа характерно наличие инкубационного периода, т.е. их развитие, сопровождающееся высокой скоростью износа, хорошо заметно на последних этапах эксплуатации подшипника.
• Дефекты подшипников качения • 9 — 6 •
вибрации (широкополосный шум) появляется при значительном нарушении геометрических размеров подшипника. При повышении вибрации подшипника или анализе причины его преждевременного выхода из строя следует установить с чем она связана: с износом, нарушениями смазки, избыточной статической нагрузкой или повышенной вибрацией. Дефекты смазки, избыточная статическая нагрузка и повышенная вибрация многократно ускоряют темп износа подшипника.
Высокочастотная вибрация сильно затухает при распространении, что позволяет разделять сигналы подшипников разных подшипниковых узлов.

Рис. 9—01. Формы и спектры сигналов вибрации подшипника в процессе развития дефектов колец ( f rol =3,73 f r , f i =10,73 f r , f cg =0,435 fr , f 0 =8,27 f r , f r = 49,4Гц).
• Дефекты подшипников качения • 9 — 8 •
ударные импульсы, возникающие при перекатывании шариков по сильно развитому локальному дефекту внутреннего кольца с периодом 3,8 мс.
Большое значение амплитуды и коэффициента пика 4,2 говорят о значительном развитии дефекта.
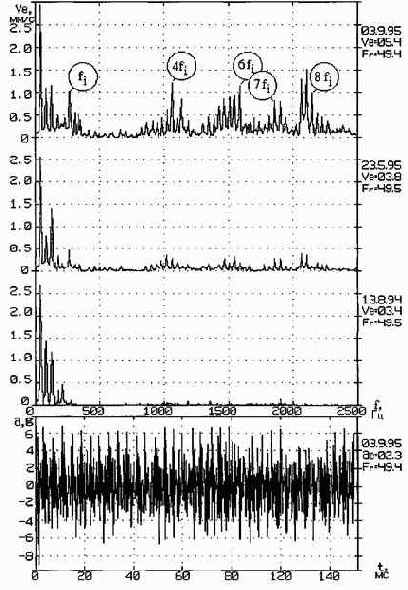
Рис. 9—02. Форма и спектры сигналов вибрации подшипника в процессе развития дефекта внутреннего кольца frol=2,64 f r , f i=5,ЗЗ f r , f cg =0,41 f r , f0 =7,67fr , fr =49,41Гц (SКF 1700)).
В спектре виброскорости подшипника наиболее отчетливо проявляется (из "подшипниковых" частот) составляющая на частоте возбуждения внутреннего кольца с частотой fi = 5,ЗЗfr (приблизительно 263 Гц) и ее 4 —я, 6 —я, 7 —я и 8 —я гармоники, помеченные стрелками. При этом величина вибрации на частоте возбуждения сопоставима по величине с вибрацией на ее гармониках. Вокруг составляющей с частотой fi и ее гармоник наблюдаются боковые частотные составляющие mfi ± nfr . Их достаточно большие (по отношению к fi ) величины и количество говорят о значительной степени развития дефектов внутреннего
• Дефекты подшипников качения • 9 — 10 •

Рис. 9—03. Форма и спектр (с фрагментом) сигнала вибрации подшипника с дефектом внутреннего кольца ( f rо1=9,65 f r , f i=29,5 f r , f cg=0,475 f r , f 0=26,9 f r , f r =24,75Гц).
Одним из наиболее достоверных и удобных методов определения вида дефектов и оценки состояния подшипников качения является метод спектрального анализа огибающей высокочастотных составляющих сигнала вибрации, создаваемой ударными импульсами.
• Дефекты подшипников качения • 9 — 12 •
составляющие сигнала вибрации, во избежание чего желательно, по мере возможностей, анализировать составляющие вибрации в полосе 10...15 кГц.
Дефекты сборки и эксплуатации подшипников качения приводят к появлению в спектре огибающей гармонических составляющих с частотами приведенными в Таблице 9 — 01.

Рис. 9—05. Примеры спектров огибающей высокочастотной вибрации подшипника качения асинхронного ЭД при дефектах сборки подшипника (сверху вниз): перекосе внутреннего и внешнего колец, "наклепе" и расцентровке агрегата.
На рис. 9 — 05 приведены несколько примеров спектров огибающей, возникающие при основных дефектах сборки подшипникового узла.
В частности, при перекосе наружного кольца обычно возникает преобладающая составляющая с частотой 2f0 (рис. 9 — 05, позиция 2). При перекосе внутреннего кольца подшипника и большой радиальной нагрузке, в силу того, что появляются две
• Дефекты подшипников качения • 9 — 14 •
Расцентровка узлов агрегата, выражающаяся в сдвиге или изломе осей агрегата, а также расцентровка подшипниковых узлов приводит к появлению в спектре огибающей группы кратных частоте вращения ротора составляющих, причем в большинстве случаев частотная составляющая fr является преобладающей (рис. 9 — 05, позиция 4).
На рис. 9 — 06. приведены спектры огибающей высокочастотной вибрации подшипника качения асинхронного ЭД по мере выработки ресурса в течение примерно 30000 часов непрерывной эксплуатации.
Нижний спектр записан практически после ремонта через несколько дней работы агрегата. В этот период дефекты сборки и износа подшипника отсутствуют, а спектр огибающей высокочастотного сигнала содержит только одну, достаточно часто встречающуюся даже в бездефектных подшипниках, гармоническую составляющую малой интенсивности с частотой перекатывания тел качения по наружному кольцу f0 = fcg zrol . Модуляция высокочастотной вибрации этой частотой определяется тем, что число тел качения, контактирующих с обоими кольцами подшипника, изменяется на единицу с частотой f0.
Спектры, записанные в течение последующих 14 месяцев (примерно 9000 часов работы агрегата) содержат небольшие составляющие fг, 2fr, 3fr и fгоl говорящие о развитии небольших дефектов: перекоса внутреннего кольца и/или расцентровки, а также нарушении и/или износе тел качения.
После двух лет эксплуатации (16.01.92) в спектре огибающей появляются признаки дефектов (износа) колец (частотные составляющие fi , f0) в начальной стадии развития. Скорость развития дефектов невелика, но неуклонно увеличивается. Примерно через 25000 часов с начала эксплуатации обнаруживается быстроразвивающийся дефект сепаратора (частотные составляющие fсg и 2fсg , причем частотная составляющая fсg становится преобладающей в спектре.
К моменту времени последнего замера она достигает максимально допустимого значения. Для завершающего периода развития дефектов характерно появление весьма интенсивных боковых частотных составляющих kfcg и kfr вокруг частот fго1, fi и f0 и их гармоник.
Разрушение подшипника чаще всего происходит при предельном износе сепаратора, быстро развивающемся при износе и выкрашивании тел качения. Поэтому глубина модуляции случайной вибрации частотой fcg в значительной степени определяет ресурс подшипника качения и может успешно использоваться для решения задачи оценки и прогноза технического состояния подшипника качения.
• Вибрация электрических машин электромагнитного происхождения • 10 — 2 •
эксплуатации. Низкое качество первых двух факторов может привести к асимметрии электрических и магнитных цепей, с переходом на нелинейные участки кривой намагничивания в различных режимах работы машины, а также проявлением нелинейности сопротивления магнитных цепей. Например, отклонения формы статора и ротора, перекосы подшипников (опор) и другие дефекты изготовления и сборки, вызывающие статический и динамический эксцентриситет (т.е. неравномерность воздушного зазора), могут приводить к появлению значительной магнитной асимметрии и изменению характера вибрации. С другой стороны, параметры вибрации машины могут существенно зависеть от условий эксплуатации (например, числа пусков ЭД) и качества напряжения сети.
При диагностике дефектов, сопровождающихся повышенной вибрацией электрических машин, в первую очередь необходимо установить, является ли ее причина электромагнитного происхождения или механического. Между последними не всегда можно провести четкую грань: трещина в стержне ротора АЭД может привести к его местному нагреву и, как следствие, тепловому дисбалансу (в этом случае первопричина — дефект электрического происхождения).
В электромеханических системах, особенно при наличии электромагнитных и механических дефектов, одновременное существование и взаимодействие различных вызывающих вибрацию сил может приводить к возникновению сложных сигналов вибрации: модуляции и биениям.

Рис. 10—01. Формы и спектр модулированного сигнала вибрации ЭД с поврежденными стержнями ротора. Несущая частота — частота вращения ротора АЭД (период Тп), период модуляции (Тт) — скольжение.
• Вибрация электрических машин электромагнитного происхождения • 10 — 4 •
Однако, если регистрируется форма сигнала вибрации, бросив на нее даже беглый взгляд, специалист при анализе, может легко обнаружить признаки модуляции или биений, после чего легко применить спектральный анализ с высоким разрешением по частоте или другие специальные виды анализа сигнала для определения конкретного дефекта.
На рисунках 10 — 01 и 10 — 02 приведены формы сигналов вибрации (в т.ч. расширенные фрагменты сигналов) и спектры вибрации возникавшие при модуляции и биениях. Характер кривой вибрации приведенных двух сигналов весьма схож и не позволяет отличить модуляцию от биений. Спектр сигнала вибрации при модуляции содержит три гармонических составляющих: преобладающую несущую с частотой вращения ротора и две боковые с частотами fг + 2s и fг— 2s. Спектр сигнала вибрации при биениях содержит две частотные составляющие: 2fг и 2fс.
Всегда следует помнить, что биения в электромеханических системах могут быть связаны не только с электромагнитными дефектами.
Например, два электродвигателя, особенно расположенные на одном основании, могут иметь близкие частоты вращения роторов, что приводит к биениям чисто механического происхождения. Другой пример: на одном из компрессорных агрегатов с частотой вращения компрессора близкой к пятой гармонике частоты вращения ротора ЭД наблюдались признаки биений, вызываемых неудачной конструкцией агрегата. Модуляция бывает характерна для ряда дефектов зубчатых передач, некоторых дефектов подшипников качения и др.
Валено, что у машин в исправном техническом состоянием, в отличии от имеющих электрические дефекты, изменение величины электрического тока в обмотках при изменении нагрузки в основном не изменяет уровни электромагнитной вибрации.
Вибрация электромагнитного происхождения обладает общим свойством: ее уровень скачкообразно падает при отключении машины от сети в момент начала останова, особенно останова под нагрузкой.
Величина скачка вибрации по отношению к ее исходной величине говорит о "вкладе" механических и электромагнитных дефектов в общую величину вибрации.
Иллюстрацией этому служит пример, приведенный на рис. 10 — 03. На форме кривой сигнала вибрации стрелкой 1 помечен момент выключения питания асинхронного ЭД (в дальнейшем АЭД). На спектре вибрации, полученном до выключения питания АЭД, стрелкой 2 помечена вибрационная составляющая электрического дефекта, на величину которой в момент выключения питания уменьшилась вибрация. На фрагменте кривой сигнала вибрации группой стрелок 3 помечена вибрация до выключения питания: три последовательно идущих максимума имеют признаки биений (амплитуда флуктуирует), группой стрелок 4 помечена вибрация после выключения питания: вибрация снизилась, признаки биений пропали (амплитуда максимумов примерно равна).
При возникновении дефектов электромагнитного происхождения, в отсутствии других дефектов машины, уровень случайной вибрации (шумовой компоненты) практически не изменяется, а высокочастотные гармонические составляющие, как правило, имеют сравнительно небольшие значения.
В текущей главе рассмотрены некоторые примеры вибрации электромагнитного происхождения, связанной с ротором и статором машины, которую могут вызывать следующие, наиболее часто встречающиеся, причины:
• несимметрия электрических цепей (ротора и/или статора) машины;
• несимметрия и нелинейность магнитных цепей (ротора и/или статора) машины;
• низкое качество электроэнергии.
• Вибрация электрических машин электромагнитного происхождения • 10 — 6 •

• Вибрация электрических машин электромагнитного происхождения • 10 — 8 •
Поскольку при появлении дефектов стержней ротора меняются многие параметры АЭД, применяют различные методы их обнаружения, из которых наиболее распространены анализ форм и спектров сигналов вибрации и спектральный анализ токов в питающих цепях с использованием токовых клещей.

Рис. 10—04. Форма сигнала виброускорения и спектр виброскорости асинхронного ЭД с частотой вращения ротора 49,38 Гц (одна пара полюсов), измеренные на переднем подшипнике в горизонтально—поперечном направлении.
Спектр вибрации в полосе частот 0...600 Гц содержит 400 линий.
На рис. 10 — 04 приведены форма и спектр сигнала вибрации АЭД имевшего растрескивание стержня ротора, вызывавшее несимметрию электрических цепей (несимметрию токов в цепях ротора). Частотное разрешение спектра невелико и не позволяет сделать заключение о наличии электрического дефекта, поскольку боковые частотные составляющие (fг±2s), являющиеся диагностическими признаками этого дефекта, лежащие вокруг частоты вращения ротора, практически сливаются с ней. На кривой сигнала вибрации заметны признаки модуляции (помечены стрелками) встречающейся при электрических дефектах АЭД. Случайная вибрация практически отсутствует. Присутствие признаков модуляции на осциллограмме привело к необходимости дополнительных измерений с увеличенным частотным разрешением. Один из спектров приведен на рис. 10 — 05. На верхнем спектре можно наблюдать боковые частотные составляющие (помечены цифрой 2) вокруг преобладающей вибрации на частоте вращения ротора (помечена цифрой 1). Боковые частотные составляющие расположены с интервалами равными ±2ns (примерно 1,24 Гц).
В качестве параметра при распознавании технического состояния машины (степени развития этих дефектов) можно использовать отношение величин вибрации на частотах fr±2s и fr . В частности, если величина вибрации на боковых частотах менее чем на 20 дБ (в 10 раз) отличается от величины вибрации на
• Вибрация электрических машин электромагнитного происхождения • 10—10 •
составляющей на частоте вращения ротора, помеченной цифрой 1. Поскольку величина этой боковой частотной составляющей отличается от величины вибрации на частоте вращения ротора менее чем на 20 дБ, предположили наличие развитых дефектов стержней ротора, обнаруженных и устраненных в дальнейшем, при проведении ремонта.

Рис. 10—06. Форма и спектр сигнала вибрации асинхронного ЭД с частотой вращения ротора 49,56 Гц (одна пара полюсов), измеренные на заднем подшипнике в вертикальном направлении. Спектр вибрации в полосе частот 0...2000 Гц содержит 400 линий.
На рис. 10 — 06 приведены форма и спектр сигнала вибрации АЭД с поврежденным стержнем ротора. Частотное разрешение спектра мало и не позволяет сделать заключение о наличии электрического дефекта, поскольку вибрация на боковых частотах, лежащих вокруг частоты вращения ротора, (являющаяся диагностическим признаком этого дефекта) практически сливается с ней в один спектральный пик. На осциллограмме заметны признаки биений или модуляции, помеченные стрелками.
Присутствие признаков биений или модуляции на осциллограмме привело к необходимости дополнительных измерений с высоким частотным разрешением и анализу тангенциальной вибрации статора.
Фрагмент спектра вибрации той же контрольной точки с высоким частотным разрешением приведен на рис. 10 — 07. На фрагменте спектра можно наблюдать преобладающую вибрацию на удвоенной частоте сети (помечена цифрой 1), вибрацию на удвоенной частоте вращения ротора (помеченной цифрой 2) и небольшие по значению боковые частотные составляющие. Боковые частотные составляющие размещены с интервалом примерно 0,88 Гц, что соответствует удвоенной частоте скольжения.
Весьма вероятно, в этом электродвигателе изменения в распределениях токов, текущих в цепях ротора с поврежденными стержнями, привели к
• Вибрация электрических машин электромагнитного происхождения • 10—12 •
На рис. 10 — 08 приведены форма и спектр сигнала вибрации АЭД с двумя поврежденными стержнями ротора.

Рис. 10—08. Форма и спектр (с фрагментом) сигнала вибрации асинхронного ЭД с частотой вращения ротора 23,69 Гц (две пары полюсов), измеренные на заднем подшипнике в вертикальном направлении. Спектр вибрации в полосе частот 0...1000 Гц содержит 400 линий.
На кривой сигнала вибрации заметны признаки биений или модуляции. Спектр вибрации включает составляющую в районе 600...800 Гц, помеченную горизонтальной стрелкой. На расширенном фрагменте этого же спектра можно наблюдать преобладающую составляющую на частоте 663,3 Гц (помечена Zr ),
• Вибрация электрических машин электромагнитного происхождения • 10—14 •
Подставив данные, полученные из приведенного выше токового спектра АЭД под нагрузкой получим:
N = 4 х 28 / [ 1189 : 18,9 + 4 ] = 1,67 ;
Это достаточно точное совпадение расчетных данных с практикой, поскольку при обследовании остановленного агрегата в ходе ревизии ротора и проведении электрических испытаний было выявлено два поврежденных стержня.

Рис. 10—09. Токовые спектры одной из фаз АЭД с поврежденными стержнями ротора на холостом ходу и при номинальной нагрузке.
Несимметрия электрических цепей статора асинхронных и синхронных электрических машин.
Электрическая несимметрия статора электрических машин приводит к появлению моментов и тангенциальных колебаний ротора, пульсирующих с частотой 2fС. Даже незначительная несимметрия фазовых токов (в пределах 2...3%)
• Вибрация электрических машин электромагнитного происхождения • 10 — 16 •
вследствие малой величины воздушного зазора. Статический эксцентриситет зазора АЭД вызывает появление амплитудной модуляции низкочастотных составляющих вибрации (kfr) и зубцовых частот (kzrfr) частотой 2fc . Динамический эксцентриситет приводит к амплитудной модуляции основных электромагнитных составляющих (kfс) частотой fr .
При насыщении зубцовой зоны АЭД наблюдается значительное увеличение глубины амплитудной модуляции зубцовых гармоник (kzrfr) сигнала вибрации. В спектре появляются боковые составляющие с частотами 2fс + (qzг±k)fr или (qzг±k)fг при динамическом эксцентриситете и qzrfr ± 2kfc при статическом эксцентриситете воздушного зазора (где q = 0, 1, 2 ...).
Интегральной характеристикой эксцентриситета воздушного зазора и насыщения зубцовой зоны машины является кепстр вибрации с частотами анализа (применительно к спектру) 600...4000 Гц.
В синхронных электрических машинах и машинах постоянного тока в силу достаточно больших зазоров воздействие динамического эксцентриситета на вибрацию сказывается слабо. При статическом эксцентриситете воздушного зазора, диагностические признаки которого совпадают с соответствующими для асинхронных ЭД, часто наблюдается насыщение зубцовой зоны.
При этом наблюдается амплитудная модуляция зубцовых гармоник вибрации частотой 2рfг.
Проиллюстрировать эксцентриситет ротора АЭД можно на следующем примере: признаки модуляции во временном сигнале вибрации, характер тангенциальной и радиальной вибрации и анализ спектров и кепстров (см. рис. 10—10) указывают на рассматриваемый дефект. В частности, на приведенном фрагменте спектра АЭД преобладает вибрация на зубцовой частоте ротора zr (частота 1894,6 Гц), кратная частоте вращения ротора fr (49,86 Гц). Горизонтальными стрелками помечены боковые частотные составляющие, лежащие с интервалом 99,98 Гц (удвоенная частота сети), говорящие о наличии статического эксцентриситета. Вертикальными стрелками помечены боковые частотные составляющие, лежащие с интервалом 49,85 Гц (частота вращения ротора), говорящие о наличии динамического эксцентриситета.
Кепстр является эффективным средством анализа сигнала с амплитудной модуляцией и выделения составляющей, создаваемой непосредственно источником вибрации. В частности, кепстр позволяет непосредственно определять глубину модуляции сигнала при сложной форме модулированного сигнала. Составляющая кепстра со сачтотой 10 мс говорит о статическом эксцентриситете, составляющая со сачтотой примерно 20 мс указывает на наличие динамического эксцентриситета, а их величина — глубина модуляции. Глубина модуляции может использоваться в качестве параметра оценки степени развития дефекта.
• Вибрация электрических машин электромагнитного происхождения • 10—18 •

Рис. 10—11. Спектры тангенциальной вибрации статора и радиальной вибрации подшипнике синхронной машины при замыкании между витками обмотки ротора (частота вращения ротора 50 Гц).
Выделяющаяся теплота часто вызывает дисбаланс ротора. В качестве диагностических параметров в этом случае можно использовать уровни вибрации статора в тангенциальных направлениях на частотах 6kfr при определенной линейной нагрузке.
Наиболее частой причиной тепловой нестабильности ротора синхронных двигателей и генераторов являются витковые замыкания в их обмотках.
В качестве примера можно привести графики спектров вертикальной вибрации опоры и тангенциальной вибрации статора синхронного двигателя при работе под номинальной нагрузкой, измеренные непосредственно после пуска и через 6 часов эксплуатации магистрального насосного агрегата.
• Дефекты зубчатых передач • 11 — 1 •
Дефекты зубчатых передач
Нормально функционирующая зубчатая передача даже при отсутствии дефектов может обладать весьма заметной виброактивностью. Колебания при этом возникают в широком диапазоне частот и могут иметь весьма сложный состав и характер.
Возбуждение колебаний в зубчатых передачах, в том числе и нормально функционирующих, вызывается проявлением двух основных факторов — погрешностями изготовления и сборки (монтажа) зубчатых колес и периодическим изменением жесткости зубьев по фазе зацепления.
Погрешности изготовления складываются из постоянных и переменных погрешностей в шаге зубьев. Погрешности монтажа проявляются в виде нарушений соосности валов и перекосе их осей, нарушении боковых зазоров и др.
Периодическое изменение жесткости зубьев и постоянная погрешность шага зацепления вызывают появление в вибрации зубчатой передачи колебаний на зубцовой частоте и ее гармониках:

где z1 , z2 — числа зубьев и fr1 , fr2 - частоты вращения сопряженных колес.
Переменная погрешность в шаге зацепления и нарушения соосности (перекосы осей валов) вызывают вибрацию на частотах вращения валов обоих колес и/или на модуляционных частотах:

Часто в спектре вибрации зубчатой передачи могут возникать т.н. "промежуточные" частотные составляющие (fm) , появляющиеся обычно у мультипликаторов приблизительно посередине между частотой вращения ротора быстроходного колеса и зубцовой частотой. "Промежуточные" частотные составляющие представляют собой серию компонентов, кратных или некратных частоте вращения зубчатых колес. Эта вибрация имеет недостаточно ясную механическую природу: хотя имеется несколько теорий, объясняющих ее возникновение, однако, по мнению авторов этой книги, ни одна и них не объединяет всех фактов, связанных с особенностями поведения "промежуточных" частотных составляющих.
Наиболее предпочтительно предположение, что
• Дефекты зубчатых передач • 11 — 3 •
осциллограмме сигнала вибрации меняется соотношение компонентов периодической и случайной вибрации.
Равномерный абразивный износ ( ухудшение состояния контактирующих поверхностей) всегда сопровождается ростом общего уровня спектральных составляющих вибрации практически во всем измеряемом диапазоне частот вибропроцесса. Общее увеличение уровней спектральных компонентов, особенно в высокочастотной области, определяет степень развития износа поверхностей зубьев, что при сильном износе приводит к появлению в спектре широкополосных областей с высоким уровнем шума, которые могут поглощать составляющие основных частот возбуждения. Однако каждая зубчатая пара характеризуется своими частотами возбуждения: частотами вращения роторов, "промежуточными" частотами и зубцовой частотой и их гармониками. Для подчеркивания последних иногда бывает целесообразно использовать синхронное накопление или синхронную гребенчатую фильтрацию.
Выкрашивание зубьев (питтинг) зубчатых колес.
Появление локального повреждения в виде ямки выкрашивания (питтинг), одного из наиболее распространенных дефектов, приводит к увеличению деформации зубьев, а точнее росту ее контактной составляющей. В силу этого жесткость зацепления передачи в момент контактирования зуба, имеющего дефект, уменьшается, что происходит раз за оборот вала (fr). Питтинг приводит также к флуктуации давления в упругогидродинамическом контакте в момент контактирования поврежденного зуба, что приводит к увеличению глубины амплитудной модуляции в виброакустическом сигнале. Эти явления вызывают рост амплитуд гармоник оборотной частоты kfг , рост амплитуд комбинационных частот mfz ± nfr . Достаточно часто наблюдается появление и/или существенный рост (флуктуации) амплитуд "промежуточных" частот (fm и fm ± nfr ).
В качестве диагностических признаков питтинга часто используют появление и развитие боковых частотных составляющих mfz ± nfr вокруг зубцовой частоты fz и/или боковых частотных составляющих fm ± nfr вокруг "промежуточных" частотных составляющих fm , и диагностического параметра их амплитуды в спектре вибрации или, аналогично, частотных составляющих kfr и их амплитуд в спектрах амплитудной огибающей узкополосной вибрации с центральными частотами kfz и fm .
Трещины и излом зубьев зубчатых колес.
Эти дефекты являются весьма опасными, поскольку разрушение зубьев (скол, поломка) часто приводит к отказу агрегата при попадании продуктов разрушения в зону зацепления или подшипники.
Появление локального повреждения в виде трещины или скола зубьев может приводить к увеличению деформации собственно зубьев и, достаточно редко, деформации ободьев зубчатых колес, как изгибной, так и контактной ее составляющих. Как и в случае питтинга, жесткость зацепления передачи в момент контактирования зуба, имеющего дефект, уменьшается, что происходит раз за оборот вала (fr), а также происходят флуктуации давления в упругогидродинамическом контакте в момент контактирования поврежденного зуба, что приводит к увеличению глубины амплитудной модуляции в виброакустическом сигнале. Эти явления вызывают рост шумового компонента виброакустического сигнала и амплитуд гармоник оборотной частоты kfr , рост амплитуд комбинационных частот mfz ± nfr и флуктуацию амплитуд резонансных частот (достаточно часто наблюдается появление и/или существенный рост "промежуточных" частот).
Поскольку при появлении трещины или излома зуба жесткость зацепления в момент контакта дефектного зуба резко уменьшается, следующая пара зубьев
• Дефекты зубчатых передач • 11 — 5 •
Однако исследуя частотную модуляцию на зубцовых частотах, а точнее изменение уровней (глубину модуляции) спектральных составляющих на частотах вращения роторов, возможно распознавать заедание на начальном этапе.

Рис. 11—01. Спектры вибрации мультипликатора (индекс С) со стороны тихоходного (индекс 0) и быстроходного (индекс I) валов в вертикальном (индекс V) и горизонтально—осевом (индекс А) направлениях при нарушении соосности валов.
На рис. 11 — 01 приведены спектры вибрации установленного между ЭД и компрессором компрессорного агрегата мультипликатора с косозубой шевронной зубчатой передачей, состоящей из двух колес, с частотой вращения тихоходного
• Дефекты зубчатых передач • 11 — 7 •

Рис. 11—02. Спектр вибрации мультипликатора со стороны тихоходного вала в вертикальном направлении при увеличенном боковом зазоре между зубчатыми колесами.
Можно отметить также сравнительно высокий уровень шумов в широкой полосе частот (практически по всему спектру), характерный для нарушений жесткости.
На рис. 11 — 03 приведен спектр вибрации (и его фрагмент) редуктора с прямозубой зубчатой передачей, состоящей из двух колес (Z1=30; Z2 = 76), установленного между ЭД и специализированным поршневым компрессором, с частотой вращения быстроходного колеса примерно 24,8 Гц (fг1) и тихоходного колеса примерно 9,8 Гц (fr2). При ревизии редуктора обнаружен 75% —и от предельно допустимого износ поверхностей зубчатых колес.
• Дефекты зубчатых передач • 11 — 9 •
поверхностей зубьев, привело к появлению в спектре широкополосных областей с достаточно высоким уровнем шума.
Приведенные ниже данные измерения вибрации измерены на мультипликаторе, установленном между ЭД и центробежным компрессором агрегата, зубчатая пара прямозубой передачи которого была подвержена развитому питтингу. Тихоходное колесо (частота вращения примерно 49,46 Гц (fг1)) имеет 91 зубьев, быстроходное (частота вращения примерно 166,69 Гц (fr2)) — 27. Передаточное отношение — 3,37, зубцовая частота (fz) составляет примерно 4501 Гц.
На рис. 11 — 04 приведена форма сигнала вибрации, измеренная на крышке подшипника быстроходного колеса в горизонтально — поперечном направлении. Пиковое значение виброускорения достигает 30 д. Сам сигнал — амплитудно модулированный процесс с несущей "промежуточной" составляющей имеющей частоту примерно 2003 Гц (12 —я гармоника частоты вращения быстроходного колеса).

Рис. 11—04. Форма сигнала вибрации мультипликатора с развитым, питтингом контактирующих поверхностей зубчатых колес.
На рис. 11—05 приведен спектр (с фрагментами) вибрации мультипликатора измеренный в той же контрольной точке. Спектр вибрации имеет сложный характер: наблюдается виброактивность в широкой полосе частот.
В частности, он содержит преобладающую составляющую на частоте 2003 Гц (fm), составляющие на частотах вращения обоих колес и их гармоники, зубцовую частоту (fz ) и др. На расширенных фрагментах спектра вибрации вертикальными стрелками помечены интенсивные боковые частоты (комбинационные частоты), являющиеся гармониками частоты вращения ротора тихоходного колеса и наклонными стрелками — быстроходного в окрестностях fm и fz . Интенсивная общая вибрация и высокие значения уровней боковых частот относительно уровней fm и fz говорят о наличии развитого повреждения. Следует отметить, что с течением времени и при изменении нагрузки уровень вибрации значительно изменялся, при этом наблюдались флуктуации "промежуточных" составляющих как по амплитуде, так и по частоте (на 11 и 12 гармониках частоты вращения быстроходного колеса).
Уровень шумов невысок.
Перечисленные факты позволяют утверждать, что имеется эксплуатационный дефект зубчатой пары, связанный с обширным износом или поломкой зубьев. Наиболее вероятным следует считать питтинг, однако анализ спектров не позволяет сделать однозначного заключения.
• Дефекты зубчатых передач • 11 — 11 •

Рис. 11—06. Спектры амплитудной огибающей узкополосной вибрации мультипликатора с несущими частотами 2500 Гц (верхний график) и 4500 Гц (нижний график) с развитым питтингом контактирующих поверхностей зубчатых колес.
На рис. 11—06 показаны спектры амплитудной огибающей узкополосной вибрации той же контрольной точки мультипликатора с несущими частотами 2500 Гц (верхний график) и 4500 Гц (нижний график). Наибольшей информативностью обладает спектр амплитудной огибающей в окрестности зубцовой частоты fz = 4501 Гц. Появление ямки выкрашивания даже на одном зубе вызывает значительный рост (более 10 дБ) амплитуд гармоник (особенно второй) частот вращения колес, что позволяет диагностировать этот вид повреждения на стадии зарождения. Можно утверждать также, что поскольку вибрация, кратная частоте вращения быстроходного колеса интенсивнее, степень его повреждений больше.
Хорошую информативность при выявлении питтинга имеет кепстр: наблюдение за изменением (ростом) амплитуд рахмоник кепстра (в качестве диагностического параметра), соответствующих частотам вращения колес, также может применяться с успехом для оценки состояния зубчатых колес, особенно на ранней стадии развития питтинга.
Методы диагностирования выкрашивания вполне пригодны для диагностирования скола или поломки зубьев. При таких дефектах глубина модуляции растет еще больше (по сравнению с питтингом). Кроме того, при появлении трещины или скола зуба жесткость в момент зацепления резко падает и происходит "преждевременный" вход в зацепление следующей за дефектными пары зубьев, сопровождающийся ударом. На кривой вибросигнала появляются импульсы, амплитуда которых зависит от степени развития дефекта.
Иллюстрацией этому служит приведенный ниже пример.
• Дефекты зубчатых передач • 11 — 13 •
вращения колес kfг , составляющие на зубцовой (mfz) и комбинационных частотах mfz±nfr и заметный уровень шумов.
Вторая гармоника частоты вращения ротора указывает на расцентровку. В то же время некоторые боковые частотные составляющие, помеченные горизонтальными стрелками, по величине превосходят вибрацию на зубцовой частоте, что говорит о высокой амплитудной модуляции (и/или, возможно, частотной модуляции). Такая же картина наблюдается и вокруг второй гармоники зубцовой частоты.
Параметры процесса модуляции и периодические ударные импульсы на кривой сигнала вибрации являются простым и надежным способом диагностирования трещин, сколов и поломок зубьев. Их количественный анализ еще более упрощается при применении синхронного накопления и кепстральном анализе.
Методы диагностирования заедания аналогичны методам диагностирования выкрашивания зубьев и основаны на исследовании частотной модуляции основных частот возбуждения. При заедании на кривой виброускорения наблюдаются нерегулярные выбросы, но они мало изменяют спектр сигнала и сходны с выбросами, которые могут быть вызваны некоторыми другими дефектами зацепления.
Приведенные ниже данные измерения вибрации (рис. 11 — 08) собраны на мультипликаторе, установленном между ЭД и центробежным компрессором агрегата, зубчатая пара косозубой передачи которого была на момент последнего измерения в процессе прогрессирующего заедания. Это было установлено непосредственно после измерений и останова агрегата при ревизии мультипликатора. Тихоходное колесо (частота вращения примерно 50,0 Гц (fr1)) имеет 41 зуб, быстроходное (частота вращения примерно 73,2 Гц (fr2)) — 28. Зубцовая частота (fz) составляет примерно 2050 Гц.
Кривая сигнала вибрации (рис. 11 — 08) имеет характерные признаки модуляции и выбросы, величина некоторых из них превышает 10 д. Коэффициент пика достигает 4,4.
Спектр вибрации имеет признаки эксплуатационного износа зубьев: комбинационные частотные составляющие fz±nfr вокруг зубцовой частоты fz , "промежуточные" частотные составляющие также с боковыми частотами и заметный уровень шумов. Наклонными стрелками помечены некоторые боковые частоты вокруг fz , величина и количество которых говорят о возможной частотной модуляции. Однако на основе анализа формы и спектра сигнала вибрации затруднительно выявить конкретный вид дефекта — заедание.
Как говорилось выше, для диагностирования этого повреждения колес эффективно исследовать частотную модуляцию на одной из частот возбуждения зубчатых колес с применением преобразования Гилберта. Нижние спектры — спектры частотной модуляции первой гармоники зубцовой частоты fz = 2050 Гц измерены непосредственно в начале развития процесса заедания (спектр от 02.04.95) и в процессе развития дефекта (спектр от 09.04.95). По мере развития заедания в приведенном случае произошел значительный рост уровней спектральных составляющих на частотах вращения роторов и их гармониках как тихоходного, так и быстроходного колес.
• Нарушения гидро и газодинамики потока и пульсации давления • 12 — 1 •
Нарушения гидро и газодинамики потока и пульсации давления
Причинами нарушения динамики потока являются потокосоздающие и потокопроводящие элементы; распределительная, регулирующая и запорная арматура; приводная (движущаяся в потоке) и направляющая часть оборудования, уплотнения и др.
Источниками вибрации при этом является турбулентность движущегося потока, создающего случайные пульсации давления в пристеночном слое; вихреобразования, возникающие вокруг препятствий распределительной, регулирующей, запорной арматуры, изгибов потокопроводов и элементов изменения их сечения, на кромках всасывающих и нагнетающих патрубков, рабочих и направляющих лопаток; неоднородности потока на выходе и входе направляющих лопаток на входе и выходе рабочего колеса и языка спирали; гидродинамической неуравновешенности рабочего колеса насосов; кавитации в потоке жидкости насосов; помпажа в компрессоре и др. В проточной части турбин и компрессоров существует множество возможных источников возникновения сил аэродинамического возмущения, из которых наиболее существенные обусловлены окружной динамической неравномерностью зазоров в уплотнениях из —за изгибных колебаний роторов.
Пульсации давления при турбулентности потока и вихреобразовании.
Пульсации давления в потоке и создаваемая ими вибрация преимущественно носят случайный характер. Величина пульсаций давления в потоке зависит от конструкции проточной части и скорости потока. Связь вибрации и конструктивных параметров устанавливается экспериментально.
Интенсивность пульсаций пропорциональна плотности и 2...3 степени
• Нарушения гидро и газодинамики потока и пульсации давления • 12 — 3 •
На предприятии имелось еще два таких вентилятора, работающих удовлетворительно. На рис.12 —01 приведена схема агрегата и расположения контрольных точек.

Рис. 12—01. Схема контрольных точек на вентиляторе, установленном на тонкостенном основании.

Рас. 12—02. Изменение вибрации по контрольным точкам на вентиляторе.
На рис. 12 — 02 приведено распределение вибрации по основным контрольным точкам на вентиляторе. Высокий уровень вибрации наблюдается на всех подшипниковых опорах и щитах агрегата, а также опорной системе агрегата
• Нарушения гидро и газодинамики потока и пульсации давления • 12 — 5 •
возникновения резонансных колебаний опорной конструкции вентилятора на частоте 16,14 Гц (см.
графики на рис. 12 — 02 и 12 — 03).
Для проверки предположения о возникающих резонансных колебаниях сварной конструкции корпуса вентилятора и основания агрегата, вентилятор остановили и были использованы резонансный метод и вибро — акустический метод свободных колебаний, выявивший наличие резонанса опорной сварной тонкостенной конструкции на частоте 16,2 Гц.
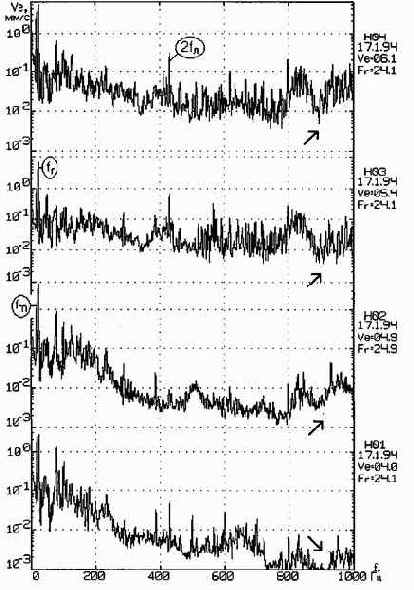
Рис. 12—04. Спектры вибрации подшипниковых опор вентилятора и щитов ЭД в горизонтально—поперечном направлении.
Наиболее вероятной причиной возбуждения резонансных колебаний было нарушение газодинамики потока, вызванное применением рабочего колеса вентилятора со спрямленными лопатками (в этом случае происходит повышение вихреобразования). Для вибрации, вызываемой пульсациями давления и вихреобразованием характерно наличие в спектре широкополосных областей
• Нарушения гидро и газодинамики потока и пульсации давления • 12 — 7 •
широкополосной случайной вибрации возможно также и при некоторых других дефектах агрегатов, например, при дефектах подшипников качения.
Для высокочастотной вибрации характерно затухание колебаний по мере удаления от источника колебаний, что и наблюдается на примере приведенных на рис. 12 — 05 спектров вибрации заднего подшипника ЭД, заднего подшипника вентилятора и корпуса вентилятора в районе выходного патрубка в горизонтально —поперечном направлении (см. области, помеченные наклонными стрелками). На корпусе вентилятора и его подшипниковых опорах наблюдается вибрация на лопастной частоте (fл). Также следует обратить внимание на то, что вибрация на резонансной частоте 16,2 Гц (1m) на корпусе вентилятора, т.е. в непосредственной близости от источника нарушений газодинамики потока в районе выходного патрубка, выше, чем в других точках горизонтально — поперечного направления измерений. В этой области корпуса вентилятора проявление достаточно интенсивной высокочастотной вибрации, которая могла бы вызываться дефектами подшипников качения (или другими дефектами механического происхождения), маловероятно, поскольку расстояние от подшипниковых опор насоса до выходного патрубка более двух метров.
Таким образом пульсации давления, вызываемые вихреобразованием потока в области рабочего колеса и выходного патрубка, возникающие из — за нарушения формы лопаток рабочего колеса, вызванной несоблюдением технологии изготовления, приводят к опасным резонансным низкочастотным колебаниям опорной части этого агрегата и существенному уменьшению его межремонтного интервала, хотя сами по себе очень малы по уровню.
Неоднородность потока в проточной части центробежных агрегатов.
Неоднородность потока в проточной части — один из наиболее характерных и интенсивных источников гидродинамических колебаний центробежных насосов, газодинамических колебаний вентиляторов и реже (меньше) компрессоров и турбин. Причина этих колебаний — гидро и газодинамические силы от неоднородности потока на входе (при наличии направляющих лопаток) и выходе из рабочего колеса, т.е. неравномерность поля скоростей и давлений по шагу между лопастями колеса.
При вращении рабочего колеса (на примере насоса) присходят циркуляции рабочей среды вокруг лопасти, а также "провалы" скорости при обтекании вращающихся лопастей, обусловленные вязкими средами. Механизм возникновения вибрации от неоднородности потока за колесом, вызываемый приведенными факторами, срабатывает при наличии в потоке препятствия в виде языка спирального отвода.
Первичным явлением в потоке жидкости следует считать импульсы давления (неуравновешенность распределения давлений) при прохождении лопастей рабочего колеса мимо языка или входных лопаток (в проточных каналах). По частотному составу пульсации этих сил являются сложными колебаниями, содержащими компоненты на частоте вращения ротора, лопастной частоте и их гармоники, а также боковые частоты вокруг лопаточных частот. Эти импульсы давления носят гармонический характер. Частота следования лопастных импульсов зависит от частоты вращения ротора, числа лопастей рабочего колеса и количества лопаток направляющего аппарата на входе и выходе.
В простейшем случае она определяется по формуле:
fл = kZЛ fr ;
где fЛ — лопастная частота; ZЛ — число рабочих лопастей колеса; fr — частота вращения ротора, k — натуральное число.
• Нарушения гидро и газодинамики потока и пульсации давления • 12 — 9 •

Рис. 12—06. Форма и спектр сигнала виброскорости при колебаниях скоростей потока в насосе в области малых подач (инфразвуковые колебания).
На рис. 12 — 06 приведены форма и спектр сигнала виброскорости насоса, работавшего при малых подачам, и возникающих при этом колебаниях скоростей потока (инфразвуковые колебания). Вибродатчик крепился к корпусу подшипника при помощи шпилечного соединения, обеспечивавшего достаточную жесткость соединения, при этом в области частот от 25 Гц и ниже заметно появление низкочастотной вибрации (участок спектра, помеченный стрелкой) — начальная стадия инфразвуковых колебаний.
Агрегат при этом способен работать достаточно продолжительное время, если отсутствуют резонансные колебания его частей и работоспособны подшипники, но ускоренный износ рабочих поверхностей колеса (особенно при возникновении начальной формы кавитации) и несколько меньше подшипников, вала, и, что часто наблюдается, уплотнений (особенно при возникновении инфразвуковых колебаний) приводят к повышенным издержкам. Например, СКЗ
• Нарушения гидро и газодинамики потока и пульсации давления • 12—11 •
составляющими mfЛ±kfr , где k и m натуральные числа. Статический эксцентриситет в большинстве случаев не влияет на уровень вибрации центробежных агрегатов и существенно может проявляться лишь в случае малых зазоров между рабочим колесом и языком спирального отвода.
При неравномерном эксплуатационном износе лопаток может появляться вибрация на частоте вращения ротора и ее гармониках (kfr , вызываемая появлением дисбаланса), лопаточных частотах (mfЛ) и боковых частотах (mfЛ±kfr). Однако надежных статистических данных о количественных изменениях вибрации на боковых частотных составляющих (в качестве диагностических параметров) вокруг лопаточной частоты (с учетом нагрузки, расхода и др.), с помощью которых можно было бы сделать однозначное заключение об опасности дефекта, в настоящее время не имеется.
В качестве примера лопастной вибрации можно привести следующий. Одноступенчатый центробежный насос (количество лопаток — 7) с выносными подшипниковыми опорами и подшипниками качения, приводимый асинхронным электродвигателем мощностью 250 кВт, работает с частотой ротора 49,8 Гц при номинальной нагрузке. До момента приведенных измерений находился в эксплуатации 12 лет. Текущий ремонт, включающий замену подшипников, производился за 11 месяцев до приведенных данных измерения вибрации.
На рис. 12 — 07 представлены спектры вибрации подшипниковых опор насоса (индекс РI — внутренняя подшипниковая опора насоса, индекс РО — внешняя, индексы V, Н, А — соответственно вертикальное, горизонтально — поперечное и осевое направления измерений). На представленных спектрах вибрация в радиальной плоскости (контрольные точки РIН;РIV;РОН;РОV) превышает вибрацию в осевом направлении (контрольные точки РIА;РОА), и горизонтально — поперечная вибрация (контрольные точки РIН;РОН) выше осевой и вертикальной. Составляющая спектра вибрации на частоте вращения ротора (помечена fr) преобладает и достигает 3 мм/с, наблюдается вибрация на высших гармониках частоты вращения ротора. На графиках спектров имеется вибрация на лопастной частоте и ее гармониках (помечены fЛ=7fr , 2fЛ=14fr). На всех контрольных точках наблюдается также заметная вибрация на частотах 616,8 Гц, 666,7 Гц, 716,7 Гц, 766,7 Гц, некратных частоте вращения ротора (одна из них помечена fi — дефект внутреннего кольца подшипника, остальные — боковые частоты). Уровень вибрации обеих опор примерно равен по величине.
На рис. 12 — 08 приведены форма и спектр сигнала точки с максимальной вибрацией — передняя подшипниковая опора, горизонтально — поперечное направление (РIН). На приведенном спектре видно, что СКЗ виброскорости на частоте вращения ротора составляет 3 мм/с, на седьмой и четырнадцатой ее гармониках (лопастные частоты) — 1,76 и 1,35 мм/с. Остальные, достаточно значимые по величине частотные составляющие, молено разделить на три группы: боковые частоты вокруг седьмой и четырнадцатой гармоник частоты вращения ротора (mfЛ±kfr помечены стрелками), высшие гармоники частоты вращения ротора (вторая гармоника помечена индексом 2fr), составляющие на частотах, некратных частоте вращения ротора, наиболее значимые из которых на частотах 215, 380, 616, 666, 716, 766 Гц, связанные с дефектами подшипников качения, вклад которых в СКЗ виброскорости достаточно велик и составляет более 15%.
На осциллограмме виброскорости вертикальными пунктирными линиями помечены временные интервалы, соответствующие одному обороту ротора. На кривой вибрации в продолжение одного оборота наблюдается примерно 7 и более пиков, амплитуда в течение нескольких оборотов изменяется вдвое по величине, и пиковое значение достигает 14,1 мм/с.
• Нарушения гидро и газодинамики потока и пульсации давления • 12 — 13 •
(и выходного kZЛZ и fг) лопаточного аппарата, а иногда, хотя и достаточно редко, и
на суммарных и разностных частотах, kfЛ±mfи ( fи= Zи fr ; k, m — натуральные числа), и других комбинационных частотах.
В качестве примера можно привести спектры вибрации центробежного компрессора (см. рис. 12 — 09), имевшего дефекты направляющего лопаточного аппарата с изменяемым углом установки лопаток на входе рабочего колеса первой ступени.

Рис. 12—09. Спектры вибрации центробежного компрессора при дефекте направляющего лопаточного аппарата с изменяемым, углом установки лопаток на входе рабочего колеса первой ступени.
Из —за загрязнения и возникших дефектов в механизме поворота входных лопаток при изменении угла установки лопаток происходило заклинивание, в результате которого нарушалась пространственная симметрия положений направляющих лопаток, а также имелся некоторый эксплуатационный износ подвижных и неподвижных лопаток компрессора. В результате этих дефектов происходило нарушение динамики потока и, как следствие, увеличивалась вибрация, на определенных режимах работы компрессора (при изменении положения входных лопаток). Нижний спектр измерен при пространственно симметричном положении лопаток, верхний — при заклинивании и несимметричном положении лопаток, которому соответствовала и большая нагрузка. Наклонными стрелками помечены частоты 2fЛ±mfи. Если рассмотреть графики, то можно отметить, что при увеличении нагрузки и пространственной несимметрии положений входных лопаток, вибрация на частоте вращения ротора (fr) изменилась мало, однако на лопаточной частоте и ее гармониках (fЛ, 2fЛ), боковых частотах вокруг лопаточной (fЛ±mfг), а также комбинационных частотах (2fЛ±mfи) многократно увеличилась.
• Нарушения гидро и газодинамики потока и пульсации давления • 12 — 15 •

Рис. 12—10. Спектр виброскорости, измеренный на корпусе насоса в районе входного патрубка при газовой фазе кавитации.
Вибрация при кавитации носит случайный характер, составляющие случайные колебания лежат в области средних и высоких частот и могут быть велики по значению. Обычно максимум широкополосной вибрации находится в зоне 500...10000 Гц, причем, по мере развития кавитационного процесса, смещается в зону высоких частот. При совпадении собственных частот колебаний рабочих лопастей или деталей насоса с частотами колебаний, возникающих при кавитации, особенно при малых подачах, возможно появление интенсивных автоколебаний лопаток и даже ротора, обвязки и корпуса, что чрезвычайно опасно и может привести к быстрому разрушению насоса, однако, такие ситуации встречаются крайне редко.
На рис. 12—10 приведен спектр виброскорости, измеренный на корпусе насоса в районе входного патрубка при газовой фазе кавитации. Можно видеть, что максимум широкополосной вибрации находится в зоне 700...1200 Гц
Весьма удобно выявлять признаки ранней кавитации с помощью анализа спектра огибающей высокочастотной вибрации. При этом использование высокочастотных составляющих вибрации выше 15 кГц может оказаться нецелесообразным, поскольку в центробежных насосах отсутствуют потоки очень малых сечений, и максимум спектральной плотности случайной вибрации может быть ниже 10 кГц. Однако для того, чтобы в полосу анализируемых частот не попадали "механические" гармонические составляющие, в большинстве случаев более целесообразно проводить анализ огибающей сигнала в полосе 10...15 кГц. При этом в спектре всегда появляется лопастная составляющая (fЛ).
При больших расходах наличие интенсивных вихрей в отводах и колесе способствует тому, что давление в вихревых областях понижается, способствуя
• Нарушения гидро и газодинамики потока и пульсации давления • 12 — 17 •

Рис. 12—12. Спектры огибающей высокочастотной вибрации при статическом, эксцентриситете рабочего колеса насоса на корпусе, входном, и выходном патрубках насоса.

Рис. 12—13. Спектры огибающей высокочастотной вибрации при динамическом, эксцентриситете рабочего колеса насоса на корпусе, входном и выходном патрубках насоса.
• Нарушения гидро и газодинамики потока и пульсации давления • 12 — 19•
частотах в паровых турбинах имеет намного меньшую величину, чем в компрессорах и газовых турбинах.
В процессе проведения мониторинга вибрации в области высоких частот во многих случаях вовремя удается обнаружить дефекты лопаток, приводящие к возрастанию неоднородности (турбулентности) потока, и, поскольку при этом возникают скорее не количественные, а качественные изменения характера вибрации в высокочастотной области спектра, решающую роль здесь играет квалификация специалиста.
Примером может служить случай с паровой турбиной Чешского производства, применявшейся для привода центробежного компрессора. На предприятии впервые был применен высокочастотный виброанализ на этом агрегате примерно за четыре месяца (см. рис. 12—14, спектр от 12.6.91 г.) до запланированного по программе ППО ремонта.

Рис. 12—14. Спектры виброускорения паровой турбины в процессе развития дефектов лопаток.
Во время проведения следующего измерения, при номинальном режиме работы агрегата, в спектре от 14.9.91 г. было обнаружено качественное изменение характера вибрации: высокая виброактивность в области частот 10...18 кГц, в том числе на гармониках частоты вращения ротора. Это могло говорить о нарушении динамики потока и возможных дефектах лопаток.
Администрация приняла решение о продолжении эксплуатации агрегата и проведении ремонта через две недели при плановой остановке производства на профилактику. При этом нагрузка агрегата была ограничена.
После останова агрегата при проведении ревизии проточной части были обнаружены четыре деформированные лопатки, имевшие также трещины. В дальнейшем было установлено, что на одном из режимов работы агрегата при
• Нарушения гидро и газодинамики потока и пульсации давления • 12 — 21 •

Рис. 12—15. Спектры вибрации однотипных компрессоров с нормальным (нижний спектр) и дефектным (верхний спектр и временной сигнал) состоянием лопаток.
• Приложение 1 • а1 — 1 •
Приложение 1 Термины и определения
Абсолютная погрешность Разность между измеренным и истинным значением (ускорения). (акселерометра по входу)
Абсолютное измерение Измерение, основанное на прямых измерениях одной или
нескольких основных величин и (или) использовании значений физических констант.
Автобалансирующее Устройство, автоматически компенсирующее изменение устройство дисбалансов ротора в эксплуатационных условиях.
Автоколебания Колебания системы, возникающие в результате самовозбуждения.
Акселерометр Измерительное устройство, предназначенное для измерения
ускорений
Активная виброзащита Вибрационная защита, использующая энергию дополнительного
источника.
Амплитуда (гармонических Максимальное значение величины (характеризующей вибрацию) колебаний (вибрации)) при гармонических колебаниях (вибрации) (см. термин "гармонические
колебания").
Амплитудно — фазовая Зависимость комплексной амплитуды вынужденных колебаний (частотная) характеристика (вибрации) системы от частоты гармонического возбуждения с постоянной
амплитудой.
Амплитудно-частотная Зависимость амплитуды вынужденных колебаний или вибрации характеристика системы от частоты гармонического возбуждения с постоянной амплитудой.
Амплитудно-частотная Зависимость отношения амплитуды выходного сигнала характеристика акселерометра акселерометра к амплитуде задаваемого гармонического ускорения от частоты
последнего.
Амплитудный спектр Спектр колебаний, в котором величинами, характеризующими
гармонические составляющие колебаний, являются их амплитуды.
Аналоговый измерительный Измерительный прибор, показания которого являются прибор [Аналоговый прибор] непрерывной функцией изменений измеряемой величины.
Антифазные (гармонические) Два синхронных гармонических колебания (вибрации), у которых колебания (вибрации) сдвиг фаз в любой момент времени равен p.
Балансировка ротора Процесс определения значений и углов дисбалансов ротора и [Балансировка] уменьшение их корректировкой его масс. Операции определения и уменьшения
дисбалансов могут выполняться одновременно или последовательно.
Балансировка на месте Балансировка ротора в собственных подшипниках и опорах без установки на
балансировочный станок.
Балансировка по n - й форме Балансировка гибких роторов в заданном диапазоне частот вращения для
изгиба уменьшения переменных нагрузок на опорах, вызванных неуравновешенностью
по n - й форме изгиба.
Балансировочный комплект Измерительные приборы, позволяющие получать информацию о дисбалансах
ротора при балансировке на месте.
Балансировочный станок Станок, определяющий дисбалансы ротора для уменьшения их
корректировкой масс. Некоторые станки имеют встроенные приспособления для корректировки масс. При серийном и массовом производстве определение и уменьшение дисбалансов могут быть совмещены.
Балансировочный цикл Цикл, включающий измерительный цикл и операции, необходимые для
корректировки масс.
Бегущая волна [Волна] Распространение возмущения в среде. Величину, служащую мерой
состояния среды (перемещение, напряжение, деформацию и т. п.) в случае постоянной скорости распространения волны можно представить в виде функции F = F1(q) * F2(q-ct) , где q — криволинейная пространственная координата, вдоль которой происходит распространение волны; t — время; с — постоянная скорость распространения волны.
Биения Колебания, размах которых - периодически колеблющаяся величина и которые
являются результатом сложения двух гармонических колебаний с близкими частотами.
Взаимное влияние плоскостей Изменения показаний индикаторов в одной плоскости коррекции
коррекции данного ротора при изменении дисбаланса в другой плоскости коррекции.
Вибрационная диагностика Техническая диагностика, основанная на анализе вибрации объекта
диагностирования.
• Приложение 1 • а1 — 3 •
Гармонический анализ Представление анализируемых колебаний (вибрации) в виде суммы
колебаний (вибрации) гармонических колебаний. Слагаемые гармонические колебания называют гармоническими составляющими. Периодические колебания представляют в виде ряда Фурье, почти периодические — в виде суммы гармонических колебаний с несоизмеримыми частотами, а непериодические колебания — в виде интеграла Фурье, определяющего спектральную плотность.
Генератор опорного сигнала Устройство для получения сигнала, определяющего угловое положение ротора.
Гибкий ротор Ротор, который сбалансирован на частоте вращения, меньшей первой критической в двух произвольных плоскостях коррекции и у которого значения остаточных дисбалансов могут превышать допустимые на иных частотах вращения вплоть до наибольшей эксплуатационной.
Это определение неприменимо к роторам с изменяющейся геометрией.
Главная центральная ось Центральная ось твердого тела или механической системы, относительно
инерции которой центробежные моменты инерции тела или системы равны нулю.
Главный вектор дисбалансов Вектор, перпендикулярный оси ротора, проходящий через центр его
ротора [Главный вектор масс и равный произведению массы ротора на ее эксцентриситет.
дисбалансов] Главный вектор дисбалансов ротора равен сумме всех векторов
дисбалансов ротора, расположенных в различных плоскостях, перпендикулярных оси ротора. Угол главного вектора дисбалансов ротора определяет положение центра масс ротора в системе координат, связанной с осью ротора.
Главный момент дисбалансов Момент, равный геометрической сумме моментов всех дисбалансов ротора [Главный момент ротора относительно его центра масс. Главный момент дисбалансов дисбалансов] перпендикулярен главной центральной оси инерции оси ротора и вращается
вместе с ротором. Главный момент дисбалансов ротора полностью определяется моментом пары равных по значению антипараллельных дисбалансов, расположенных в двух произвольных плоскостях, перпендикулярных оси ротора. Модуль главного момента дисбалансов равен произведению одного из дисбалансов указанной выше пары на плечо этой пары. Угол главного момента дисбалансов определяет положение этого вектора в системе координат, связанной с осью ротора.
Градуировочная Зависимость между значениями величин на выходе и входе средства характеристика средства измерений, составленная в виде таблицы, графика или формулы. измерений Двухкомпонентный Акселерометр с двумя взаимно препендикулярными измерительными акселерометр осями.
Действительной значение Значение физической величины, найденное экспериментальным путем и (физической) величины настолько приближающееся к истинному значению, что для данной цели
может быть использовано вместо него.
Декадная полоса частот Полоса частот, у которой отношение верхней граничной частоты к нижней [Декада] равно 10.
Демпфер Виброзащитное устройство или его часть, создающая демпфирование вибрации.
Демпфирование вибрации Уменьшение вибрации вследствие рассеяния механической энергии. [Демпфирование]
Детерминированные колебания Колебания (вибрация), представляющие собой детерминированный процесс. (вибрация)
Диагностическая модель Формальное описание изделия, подвергаемого диагностированию,
(изделия) необходимое для решения задач диагностирования (в аналитической, табличной, векторной, графической и др. форме), учитывающее возможные изменения в его исправном и неисправном состоянии..
Диагностическое обеспечение Комплекс взаимоувязанных диагностических параметров, методов, правил, изделия СТД, указанных в технической документации, необходимых для
осуществления диагностирования изделия.
Диаграмма направленности Диаграмма, отображающая свойство преобразователя излучать или преобразователя принимать упругие волны в одних направлениях в большей степени, чем в
других.
Диапазон измерений Область значений измеряемой величины, для которой нормированы (акселерометра) допускаемые погрешности средства измерений (акселерометра).
Диапазон показаний Область значений шкалы показывающего акселерометра, ограниченная акселерометра конечным и начальным значениями шкалы.
• Приложение 1 • а1 — 5 •
Измерительная ось Прямая, определяемая конструкцией акселерометра, проекция ускорения
акселерометра на которую измеряется акселерометром. В процессе градуировки
акселерометра ускорения задают в направлении этой оси.
Измерительная система Совокупность средств измерений (мер, измерительных приборов, измерительных преобразователей) и вспомогательных устройств, соединенных между собой каналами связи, предназначенная для выработки сигналов измерительной информации в форме, удобной для автоматической обработки, передачи и (или) использования в автоматических системах управления.
Измерительная цепь средства Совокупность преобразовательных элементов средства измерений, измерений [Измерительная цепь] обеспечивающая осуществление всех преобразований сигнала измерительной информации.
Измерительная установка Совокупность функционально объединенных средств измерений (мер, измерительных приборов, измерительных преобразователей) и вспомогательных устройств, предназначенная для выработки сигналов измерительной информации в форме, удобной для непосредственного восприятия наблюдателем, и расположенная в одном месте.
Измерительный Средство измерений, предназначенное для выработки сигнала измерительной преобразователь информации в форме, удобной для передачи, дальнейшего преобразования, [Преобразователь, Датчик] обработки и (или) хранения, но не поддающейся непосредственному
восприятию наблюдателем.
Измерительный прибор Средство измерений, предназначенное для выработки сигнала измерительной [Прибор] информации в форме, доступной для непосредственного восприятия
наблюдателем.
Измерительный сигнал См. термин "Сигнал измерительной информации"
Изохронизм колебаний Свойство независимости частоты свободных колебаний (вибрации) системы (вибрации) от размаха.
Интегрирующий Измерительный прибор, в котором подводимая величина подвергается (измерительный) прибор интегрированию по времени или по другой независимой переменной.
Истинное значение Значение физической величины, которое идеальным образом отражало бы в физической величины качественном и количественном отношениях соответствующее свойство [Истинное значение величины] объекта.
Квазистатическая Динамическая неуравновешенность ротора, при которой ось ротора и его неуравновешенность ротора главная центральная ось инерции пересекаются не в центре масс ротора. При [Квазистатическая квазистатической неуравновешенности: главный вектор дисбалансов ротора неуравновешенность] перпендикулярен оси ротора, проходит через центр его масс и лежит в
плоскости, содержащей главную центральную ось инерции и ось ротора, а главный момент дисбалансов ротора перпендикулярен этой плоскости; дисбалансы ротора лежат в одной плоскости, содержащей ось ротора и его центр масс.
Кинематическое возбуждение Возбуждение вибрации системы сообщением каким-либо ее точкам заданных (вибрации) движений, не зависящих от состояния системы.
Класс точности балансировки Класс точности балансировки определяется по нормированным предельным значениям произведения удельного дисбаланса на наименьшую частоту вращения ротора в эксплуатационных условиях. Международный стандарт МС 1940 разделяет весь диапазон точности балансировки на 11 классов.
Колебания скалярной Процесс поочередного возрастания и убывания обычно во времени значений величины какой-либо величины.
В области вибрации термин "колебания" применяется
только для случаев изменения величины во времени. Величина, значения которой колеблются, называется колеблющейся величиной.
Колебательная система. Система, способная совершать свободные колебания.
Комплексная амплитуда Комплексная величина, модуль которой равен амплитуде, а
гармонических колебаний аргумент — начальной фазе гармонических колебаний Аеij (см. термин [Комплексная амплитуда] "гармонические колебания").
Консольный ротор Ротор, существенная часть массы которого расположена за одной из крайних
опор.
Контрольная точка Выходы изделия, с которых снимаются средствами технического [Измерительная точка] диагностирования ответы изделия (на рабочие или тестовые воздействия).
Выходы могут быть: основные — необходмые для применения изделия по назначению или дополнительные, специально организованные для целей диагностирования.
Контрольный груз Груз определенной массы, применяемый для проверки остаточного дисбаланса ротора.
• Приложение 1 • а1 — 7 •
Моментная Неуравновешенность ротора, при которой ось ротора и его главная неуравновешенность ротора центральная ось инерции пересекаются в центре масс ротора. Моментная {Моментная неуравновешенность полность определяется: главным моментом дисбалансов неуравновешенность} ротора или двумя равными по значению антипараллельными векторами
дисбалансов, лежащими в двух произвольных плоскостях, перпендикулярных оси ротора.
Нарастающие колебания Колебания (вибрация) с увеличивающимися значениями размаха.
(вибрация)
Начальная фаза Фаза гармонических колебаний (вибрации) в начальный момент времени (гармонических колебаний (см.
термин "гармонические колебания").
(вибрации))
Начальный дисбаланс Дисбаланс в рассматриваемой плоскости, перпендикулярной оси ротора, до
корректировки его масс.
Непрерывный спектр Спектр колебаний или частот, в котором частоты гармонических составляющих колебаний образуют непрерывное множество.
Неравножесткий ротор Ротор, у которого жесткость неодинакова в различных направлениях какого
—либо сечения, перпендикулярного оси ротора.
Неуравновешенная (точечная) Условная точечная масса с заданным эксцентриситетом, вызывающая во масса время вращения ротора переменные нагрузки на опорах и его изгиб.
Неуравновешенность ротора Состояние ротора, характеризующееся таким распределением масс, которое [Неуравновешенность] во время вращения вызывает переменные нагрузки на опорах ротора и его
изгиб.
Неуравновешенность по n-й Состояние гибкого ротора, характеризующееся таким распределением масс, форме изгиба которое во время вращения вызывает деформации упругой линии,
характерные для n-й формы изгиба.
Низкочастотная балансировка Баланисировка на такой частоте вращения, при которой балансируемый (применительно к гибким гибкий ротор еще можно рассматривать как жесткий. При низкочастотной роторам) балансировке частота вращения ротора значительно меньше
эксплуатационной. Низкочастотная балансировка обычно недостаточна для обеспечения нормальной работы гибкого ротора на эксплуатационной частоте вращения.
Низшая собственная частота Низшая из собственных частот измерительного преобразователя ускорения, закрепленного измерительного закрепленного на объекте, полное механическое сопротивление которого преобразователя ускорения значительно больше полного механического сопротивления измерительного
преобразователя.
Номер гармоники Целое число, равное отношению частоты гармоники к частоте анализируемых
периодических колебаний.
Нормальные условия Условия применения средств измерений, при которых влияющие величины применения средств имеют нормальные значения или находятся в пределах нормальной области измерений [Нормальные значений. При нормальных условиях определяется основная погрешность условия] средства измерений.
Однокомпонентный Акселерометр с одной измерительной осью.
акселерометр
Октавная полоса частот Полоса частот, у которой отношение верхней граничной частоты к нижней [Октава] равно 2.
Основная погрешность Погрешность акселерометра, используемого в нормальных условиях. акселерометра
Остаточный дисбаланс Дисбаланс в рассматриваемой плоскости, перпендикулярной оси ротора,
который остается в ней после корректировки его масс.
Ось вращения Линия, вокруг которой вращается тело.
Отметка угла Отметка на роторе, от которой ведут отсчет угла дисбаланса. Отметка может
быть магнитной, оптической, механической, радиоактивной и т. п.
Относительная погрешность Отношение абсолютной погрешности акселерометра по входу (выходу) к акселерометра по входу значению величины на входе (выходе).
(выходу)
Относительное измерение Измерение отношения величины к одноименной величине, играющей роль
единицы, или изменения величины по отношению к одноименной величине, принимаемой за исходную.
Параметр См. термин "Структурный параметр"
Параметр (физической Постоянная характеристика зависимости от времени физической величины, величины, характеризующей) описывающей колебания.
колебания
Параметрические колебания Колебания (вибрация) системы, вызванные и поддерживаемые
(вибрация) параметрическим возбуждением.
• Приложение 1 • а1 — 9 •
Преобразовательный элемент Элемент средства измерений, в котором происходит одно из ряда
средства измерений последовательных преобразований
[Преобразовательный элемент] величины. Преобразовательный элемент не всегда конструктивно
выделен (один и тот же элемент конструкции средства измерений может содержать два и более преобразовательных элемента).
Преобладающая частота Частота, которой соответствует глобальный максимум энергетического или
амплитудного спектра колебаний с различными частотами.
Приведенная погрешность Отношение погрешности акселерометра к нормирующему значению. Акселерометра Нормирующее значение — условно принятое значение, могущее быть
равным верхнему пределу измерений, диапазону измерений и т. д.
Принцип действия средства Физический принцип, положенный в основу построения средств измерений измерений данного вида.
Принцип измерений Совокупность физических явлений, на которых основаны измерения.
Приспособленность к Свойство изделия, характеризующее его пригодность к проведению диагностированию контроля заданными методами и средствами технического
диагностирования.
Продолжительность Время, необходимое для проведения балансировочного цикла, включая балансировки время установки и снятия ротора с балансировочного станка.
Продольная волна Волна, направление распространения которой коллинеарно траекториям
колеблющихся точек среды.
Пространственная вибрация Вибрация точки по пространственной траектории.
точки
Прямолинейная вибрация Вибрация точки по прямолинейной траектории.
точки
Пучность колебаний Точка среды при стоячей волне, в которой размах перемещений имеет [Пучность] максимум. Совокупность таких точек может образовать линию пучности
и поверхность пучности.
n - опорный ротор Ротор, имеющий n опор.
n - я критическая частота Частота вращения, равная n -й собственной частоте системы, при
которой возникают небольшие перемещения системы или ее элементов.
n - я критическая частота Частота вращения гибкого ротора, при которой наблюдается наибольший вращения гибкого ротора прогиб ротора по n -й форме изгиба, превышающий деформацию его
опор.
n - я собственная форма Форма упругой линии ротора при соответствующей n -й собственной изгиба ротора частоте изгибных колебаний системы ротор — опоры. Собственная [n - я форма изгиба] форма изгиба может быть первой, второй, ..., n -й. При высоких частотах
вращения ротора форма изгиба должна определяться с учетом гироскопического момента, действующего на ротор.
Рабочая поверхность Поверхность преобразователя, через которую принимаются упругие (преобразователя) колебания.
Рабочие условия (применения Условия применения средств измерений, при которых значения средств измерений) влияющих величин находятся в пределах рабочих областей.
Разрешающая способность Минимальное изменение измеряемого ускорения, вызывающее акселерометра закономерное изменение выходного сигнала акселерометра.
Размер (физической) величины Количественное содержание в данном объекте свойства,
соответствующего понятию "физическая величина".
Размерность физической Выражение, отражающее связь величины с основными величинами величины [Размерность] системы, в котором коэффициент пропорциональности принят равным 1.
Размерность величины представляет собой произведение основных величин, возведенных в соответствующие степени. Размерность производной величины отражает, во сколько раз изменяется ее размер при изменении размеров основных величин,
например, если размерность величины х равна LaMbTg и длина изменяется от I до I' , масса — от m до m' и время — от t до t', то новый размер величины будет больше прежнего в (I/I')a??m'/m?b??t'/t?g? раз. Например, сила в системе величин LМТ имеет размерность
LМТ-2 , теплоемкость в системе величин LМТQ (Q — размерность
температуры) имеет размерность L2MT-2Q-1 , магнитный поток в системе величин LMTI (I — размерность силы электрического тока)
имеет размерность L2 MT-2 I-1
• Приложение 1 • а1 — 11 •
Спектр колебаний (вибрации) Совокупность соответствующих гармоническим составляющим значений [Спектр] величины, характеризующей колебания (вибрацию), в которой указанные
значения располагаются в порядке возрастания частот гармонических составляющих. Периодическим и почти периодическим колебаниям соответствует дискретный спектр, непериодическим — непрерывный спектр. Примеры спектров колебаний: амплитудный, фазовый, энергетический.
Спектр собственных частот Совокупность собственных частот линейной системы, расположенных в (системы) порядке возрастания. Собственные частоты нумеруют в порядке возрастания.
Спектр частот Совокупность частот гармонических составляющих колебаний,
расположенных в порядке возрастания.
Спектральный анализ Определение спектра колебаний (вибрации) или спектра частот.
колебаний (вибрации)
Среднее значение модуля Среднее арифметическое или среднее интегральное абсолютных значений колеблющейся величины колеблющейся величины в рассматриваемом интервале времени. Если [Среднее значение модуля], имеется n дискретных значений ri колеблющейся величины, то среднее [Среднее значение] значение модуля ra = 1/n S |ri |.
Среднее квадратическое Квадратный корень из среднего арифметического или среднего интегрального значение колеблющейся значения квадрата колеблющейся величины в рассматриваемом интервале величины [Среднее времени. Если имеется п дискретных значений xi колеблющейся величины, то квадратическое значение], среднее квадратическое значение
[СКЗ]

Среднегеометрическая частота Квадратный корень из произведения граничных частот полосы.
(полосы)
Средняя оперативная Средняя суммарная оперативная продолжительность операций, необходимых продолжительность данного для определения технического состояния изделия при данном виде вида диагностирования диагностирования.
Средняя оперативная Средняя суммарная оперативная трудоемкость операций, необходимых для трудоемкость данного вида определения технического состояния изделия при данном виде диагностирования диагностирования.
Средство измерений Техническое средство, используемое при измерениях и имеющее
нормированные метрологические свойства.
Стабильность средства Качество средства измерений, отражающее неизменность во времени его измерений метрологических свойств.
Статическая балансировка Балансировка, при которой определяется и уменьшается главный вектор
дисбалансов ротора, характеризующий его статическую неуравновешенность. Статическую балансировку проводят в одной плоскости коррекции; определенную для этой плоскости корректирующую массу иногда удобно разносить в несколько параллельных плоскостей.
Статическая градуировочная Зависимость между значениями выходных величин акселерометра и характеристика акселерометра постоянных ускорений, представленная в виде таблицы, графика или
формулы.
Статическая Неуравновешенность ротора, при которой ось ротора и его главная неуравновешенность ротора центральная ось инерции параллельны. Статическая неуравновешенность [Статическая полностью определяется: главным вектором дисбалансов, или неуравновешенность] эксцентриситетом центра массы ротора, или относительным смещением
главной центральной оси инерции и оси ротора, равным значению эксцентриситета его массы.
Стоячая волна Состояние среды, при котором расположение максимумов и минимумов
перемещений колеблющихся точек среды не меняется во времени. Стоячую волну можно рассматривать как результат наложения двух одинаковых бегущих волн, распространяющихся навстречу одна другой.
Структурный параметр Параметр, непосредственно характеризующий существенное свойство детали [параметр] или узла изделия (износ, размер детали, зазор, натяг в сопряжении, рабочие
характеристики и др.).
Субгармонические колебания Вынужденные колебания (вибрация) нелинейной системы, частота которых (вибрация) в целое число раз меньше частоты гармонического возбуждения.
Супергармонические колебания Гармонические составляющие вынужденных колебаний (вибрации) (вибрация) нелинейной системы, частоты которых кратны частоте
гармонического возбуждения.
• Приложение 1 • а1 — 13 •
Форма колебаний (вибрации) Конфигурация совокупности характерных точек системы, совершающей системы [Форма колебаний периодические колебания (вибрацию), в момент времени, когда не все (вибрации)] отклонения этих точек от их средних положений равны нулю. Для
сплошных ограниченных тел форма колебаний соответствует конфигурации стоячей волны.
Фронт гармонической волны Односвязная поверхность в среде, представляющая собой геометрическое [Фронт волны] место синфазно колеблющихся точек среды при гармонической бегущей
волне.
Физическая величина Свойство, общее в качественном отношении многим физическим объектам [Величина] (физическим системам, их состояниям и происходящим в них процессам), но в
количественном отношении индивидуальное для каждого объекта. Индивидуальность в количественном отношении следует понимать в том смысле, что свойство может быть для одного объекта в определенное число раз больше или меньше, чем для другого. Термин допускается применять только для свойств, изучаемых не только в физике, если для сравнения их количественного содержания в разных объектах требуется применение физических методов. Не следует применять термин "величина" для выражения только количественной стороны рассматриваемого свойства, например писать "величина массы", "величина давления", "величина силы" и т.д., так как эти свойства (масса, давление, сила) сами являются величинами. В этих случаях следует применять термин "размер величины".
Центральные оси Система взаимно перпендикулярных осей, имеющих начало в центре масс тела
или механической системы.
Цифровой измерительный Измерительный прибор, автоматически вырабатывающий дискретные сигналы прибор [Цифровой прибор] измерительной информации, показания которого представлены в цифровой
форме.
Частота вращения при Частота вращения ротора, при которой измеряют дисбаланс.
балансировке
Частота биений Частота колебаний значений размаха при биениях, равная разности частот
суммируемых колебаний.
Частота периодических Величина, обратная периоду колебаний (вибрации).
колебаний (вибрации)
[Частота]
Частотный диапазон Диапазон частот измеряемых ускорений, в котором нормированы
измерений акселерометра допускаемые погрешности акселерометра.
Чувствительность Отношение изменения сигнала на выходе измерительного прибора к
измерительного прибора вызывающему его изменению измеряемой величины. Различают
[Чувствительность] абсолютную и относительную чувствительность. Абсолютная
чувствительность определяется формулой: S = Dl/Dx . Относительная чувствительность определяется формулой: S0 = Dl/(Dx/x) , где D1 —
изменение сигнала на выходе, х — измеряемая величина, Dх — изменение измеряемой величины.
Чувствительный элемент Часть первого в измерительной цепи преобразовательного элемента, средства измерений находящегося под непосредственным воздействием измеряемой величины (акселерометра) (ускорения).
Широкополосные случайные Случайные колебания (вибрация) со спектром частот, расположенным в колебания (вибрация) широкой полосе частот. Понятие широкой полосы частот зависит от
исследуемой проблемы. Если возможны различные толкования, необходимо дать соответствующее указание.
Шумодиагностический метод Метод акустическго неразрушающего контроля, основанный на анализе шумов, возникающих при работе объекта контроля.
Эксцентриситет массы Радиус — вектор центра рассматриваемой массы относительно оси ротора.
Рассматриваемой массой может являться масса ротора или любая другая локально расположенная масса. Модуль эксцентриситета массы равен расстоянию от оси ротора до центра рассматриваемой массы, а угловое положение радиуса — вектора этой массы удобно определять в цилиндрической системе координат, связанной с осью ротора. Для n - опорного ротора можно рассматривать эксцентриситет массы части ротора, расположенной между двумя соседними опорами.
Энергетический спектр Спектр колебаний, в котором величинами, характеризующими
гармонические составляющие колебаний, являются квадраты амплитуд скорости, характеризующие удельную энергию указанных составляющих.
• Приложение 2 • а2 — 2 •

Рис. а2—01. График движения точки при синусоидальных колебаниях.
• период (Т) — наименьший промежуток времени, по истечении которого повторяется каждое значение изменяющейся величины и направление ее изменения, измеряется в единицах времени — с, мс (1/1000 с), мкс (1/1000000 с);
• частота (f) — число полных циклов движения тела за единицу времени, т.е. за секунду и является величиной обратной периоду, f=1/Т, измеряется в Герцах (или циклах в секунду). Один Герц есть частота такого периодического колебания, период которого равен одной секунде;

Полигармонические колебания.
Полигармонические колебания — периодические колебания величины, характеризующей колебания, которые можно представить в виде суммы гармонических колебаний (гармонических составляющих)

где roi , wi t , ji — амплитуда, частота и начальная фаза 1-й гармонической составляющей.
Вибрация.
Вибрация — движение точки или механической системы, при котором происходят колебания характеризующих его скалярных величин (виброускорения, виброскорости и виброперемещения). Другими словами вибрация — колебания тела или отдельных его частей относительно нейтрального положения, меняющиеся во времени в определенных пределах.
Различают абсолютную и относительную вибрации.
Абсолютная вибрация — колебания тела около положения своего равновесия (например, вибрация корпусов машин, фундаментов, трубопроводов относительно Земли), другими словами, колебания тела в абсолютной системе координат, см. рис. а2 —03.
Относительная вибрация — колебания одного тела относительно другого (например, вибрация вала относительно корпуса подшипника, см. рис. а2 —02).
• Приложение 2 • а2 — 4 •

Рис. а2—04. Кривые синусоидальной и полигармонической вибрации.
На основе лишь амплитудно — временного графика нельзя определить ни величину, ни частоты отдельных составляющих сложного колебательного процесса.
Параметры вибрации и единицы их измерения.
Для количественной оценки механических колебаний молено использовать разные параметры: размах, пиковое значение, среднее значение, среднеквадратическое значение.
Размах, rr(sr ,vr ,ar) — разность между наибольшим и наименьшим значениями колеблющейся величины, равный для моногармонической вибрации двойной амплитуде.
Пиковое значение rp(sp ,vp ,ap) — наибольшее абсолютное значение максимальных отклонении колеблющейся величины. Различают также положительное и отрицательное пиковые значения.
Среднеквадратическое значение ге (sе,vе,aе) — величина, определяется выражением:

Для полигармонической вибрации:

Для моногармонической rе = 0,707 rа.
Среднее значение для моногармонической вибрации — 0,637 rа.
Размах колебаний является важным параметром, например, в случаях когда смещение механических колебаний детали машины является критическим с точки зрения максимально допустимых механических напряжений и зазоров.
Пиковое значение (амплитуда) эффективно при оценке кратковременных механических ударов и т.д. Однако пиковое значение отображает только максимальное значение исследуемых колебаний, а не их временное развитие.
• Приложение 2 • а2 — 6 •
— максимум перемещения вниз и ускорения вверх. Стрелка 4 — максимум восходящей скорости.
Амплитуды смещения, скорости и ускорения колебаний синусоидального сигнала взаимно связаны математическими функциями частоты и времени, приведенными ниже. Пренебрегая фазовыми соотношениями, скорость механических колебаний можно определить путем деления их ускорения на пропорциональный частоте фактор, а смещения молено аналогично получить делением ускорения на фактор, пропорциональный возведенной в квадрат частоте:

Для упрощения расчетов можно пользоваться номограммой, приведенной на рис. а2 — 07.

Рис. а2—07. Номограмма пересчета виброперемещения, виброскорости и виброускорения связанных одной частотой.
Описанные выше операции автоматически осуществляются электронными интеграторами, встроенными в современные виброизмерительные приборы.
Виброускорение, виброскорость и виброперемещение обычно выражаются в единицах международной системы единиц, соответствующих требованиям рекомендации ИСО 1000, приведенными в таблице а2 —01.
• Приложение 2 • а2 — 8 •
Для выделения полезного сигнала используют фильтры верхних и нижних частот (ФВЧ и ФНЧ), полосовые фильтры (ПФ), гребенчатые фильтры (ГФ), синхронные фильтры(СФ). Например, идеальный полосовой фильтр является фильтром, пропускающим без ослабления все составляющие с частотами внутри полосы пропускания и совершенно заграждающим все составляющие, частоты которых находятся вне этой полосы.
Однако, практические пассивные и активные фильтры несколько отличаются от идеального фильтра, в частности в отношении менее крутого наклона их кривой частотной характеристики и, следовательно, пониженного заграждения вне полосы пропускания.
Существует два основных способа определения полосы пропускания фильтров. Наиболее широко принято определение ширины полосы пропускания практического фильтра через ширину полосы пропускания идеального фильтра, пропускающего идеальную мощность белого шума как и практический фильтр. Согласно второму способу ширина полосы пропускания фильтра равна интервалу частот, определяемому точками спада частотной характеристики фильтра на 3 дБ относительно уровня в полосе пропускания. Отметим, что оба эти способа определения ширины полосы пропускания фильтра дают отличающиеся существенно друг от друга результаты только в случае фильтров с относительно низкой разрешающей способностью.

Рис. а2—08. Эффективная ширина полосы пропускания на основе мощности белого шума (слева) и ширина полосы пропускания на уровне 3 дБ (справа).
Временная реализация (форма сигнала).
На рисунке а2 —09 кривые с индексами 1, 2, 4, 6 представляют синусоидальные колебания с одинаковой амплитудой и различными периодами и фазами. Причины, вызывающие такие колебания могут быть очень разнообразны: в частности, при дисбалансе ротора неизбежно появления колебаний на частоте вращения ротора, при расцентровке возможно появление колебаний на второй гармонике частоты вращения ротора, при дефектах подшипника качения возможно появление колебаний на частотах, некратных частоте вращения ротора и, наконец, при дефектах рабочих колес исполнительных механизмов, например, рабочего колеса насоса с семью лопастями, возможно появление колебаний на седьмой гармонике частоты вращения ротора.
Так, например, периоды таких колебаний могут быть связаны отношениями 1:2: 3,7 : 7 , а начальная фаза второй синусоиды может быть
• Приложение 2 • а2 — 10 •
Достаточно часто при ударном возбуждении колебаний на осциллограмме, синхронизированной с частотой вращения ротора, можно выделить момент появления удара, его длительность, частоту заполнения импульса, период следования и форму импульса, если эти импульсы не накладываются друг на друга. Таким способом можно выявить, например, появление раковин на одной из контактирующих поверхностей: на зубе шестерни или беговой дорожке подшипника качения.
Влияние кинематических погрешностей изготовления или монтажа сказывается на глубине модуляции колебательных процессов, что также может быть использовано в качестве диагностического признака состояния механизма.
В общем же случае вибрационные процессы в агрегатах являются случайными процессами, поэтому для получения неслучайных закономерностей изменения виброакустического сигнала в большинстве ситуаций следует анализировать его статистические характеристики.
Синхронное накопление (синхронное усреднение во временной области). Для выделения периодических компонентов виброакустического сигнала на фоне шумовой помехи применяют метод синхронного накопления.

Рис. а2—10. Принцип выделения периодических компонентов виброакустического сигнала на фоне шумовой помехи методом синхронного накопления.
Идея метода заключается в том, что при суммировании временных реализаций сигналов на периодах детерминированной (например, оборотной частоты ротора) составляющей процесса амплитуда детерминированной составляющей растет пропорционально числу усреднений (n), в то время как уровень случайной составляющей вибрации остается прежним. Таким образом, отношение сигнал/помеха на выходе синхронного накопителя в п раз превышает то же отношение на входе устройства.
• Приложение 2 • а2 — 12 •
Разложение сложных механических колебаний в индивидуальные частотные составляющие производится в цифровых анализаторах спектра с помощью математического преобразования Фурье (БПФ), а анализ спектров называется частотным анализом.
Частотный анализ является основным методом вибродиагностики.
Частотный анализ механических колебаний машин и механизмов позволяет обнаружить ряд выраженных частотных составляющих периодического характера, непосредственно связанных с основными движениями отдельных узлов и деталей исследуемой машины или механизма.
Следовательно, частотный анализ дает возможность обнаружения отдельных источников механических колебаний.
Большие возможности анализа виброакустического сигнала открываются при использовании в диагностических целях динамического спектра — трехмерного представления спектральной плотности мощности в зависимости от частоты и времени. Динамическая спектрограмма, называемая также каскадным спектром, позволяет получить представление об изменении не только возмущающих сил, но и амплитудно-частотной характеристики механической системы на переходных режимах: в условиях пуска агрегата (на подъеме оборотов) или в режиме выбега (на спуске оборотов).
Выделение огибающей.
Выделение огибающей производится либо с помощью специальных электронных устройств — амплитудных детекторов, фазовых детекторов, либо с помощью преобразования Гилберта в цифровых виброанализаторах. При выделении огибающей временной сигнал фильтруется в области частоты, с которой связано появление диагностических признаков дефекта, с помощью полосового фильтра. Такими составляющими виброакустического сигнала могут быть зубчатые (или "промежуточные") частоты или одна из их высших гармоник зубчатой передачи или зубчатой муфты, частоты возбуждения подшипника качения, лопаточные частоты насоса, компрессора или турбины, пазовые частоты электрических машин, а также случайная вибрация при кавитационных процессах и газодинамических процессах и др.
Фильтрация, проводящаяся на первом этапе обработки виброакустического сигнала при выделении огибающей, оставляет только высокочастотный сигнал (см. рис. а2— 11), например, содержащий возбужденные импульсами колебания корпуса подшипника с отсутствием почти всех паразитных составляющих.
Профильтрованный сигнал выпрямляется, проходит через фильтр нижних частот с частотой среза, соответствующей приблизительно половине ширины полосы пропускания фильтра. Выходной сигнал похож; на исходные импульсы подшипника, но что более важно, он дает возможность восстановления частоты повторения этих импульсов. Путем частотного (спектрального) анализа можно точно определить частоту повторения импульсов. Период повторения импульсов может быть сопоставлен с одной из частот дефектов подшипника и таким образом определен дефект подшипника.
• Приложение 2 • а2 — 14 •
В качестве диагностических признаков используются амплитуды кепстральных компонентов (рагмоники, анаграмма слова гармоники), для временного отсчета — сачтоты (анаграмма слова частоты), соответствующей периоду основной частоты возбуждения.
Итак, кепстральный анализ используется для идентификации серий гармоник и/или боковых частот спектров для оценки их относительной мощности. В основном, кепстр мощности, при его использовании в системах мониторинга машинного оборудования, образно говоря, является результатом частотного анализа результатов частотного анализа.

Рис. а2—12. Частотные спектры и кепстры мультипликатора с изношенной зубчатой парой.
Серия импульсов во временной области (временном сигнале) отображается в частотной области (спектре) в виде дискретной составляющей (линии спектра) на частоте повторения импульсов и ее гармоник в соответствии с формой исходных импульсов. Подобно этому, серия "периодических" дискретных составляющих частотного спектра отображается в кепстре в виде дискретной линии (серии дискретных линий). Вдоль оси ординат кепстра откладывают единицы 1/Гц или секунды, а положение первой линии соответствует обратной величине просвета боковых полос или гармоник соответствующего спектра.
На рис. а2—12 приведены спектры и кепстры вибрации измеренные на мультипликаторе, имеющем дефекты зубчатой пары. Анализируя спектр, показанный в верхней части рис. а2—12 слева, содержащий множество частотных составляющих сложно определить, что он содержит две серии гармоник, свидетельствующие о наличии двух отдельных дефектов.
В то же время кепстр, соответствующий этому спектру (справа вверху), и содержащий две преобладающие составляющие, позволяет легко определить наличие групп
• Приложение 3 • аЗ — 1 •
Приложение 3 Список литературы
Бендат Дж., Пирсол А. Применения корреляционного и спектрального анализа. Пер. с англ. М.: Мир, 1983. 312 с.
Бендат Дж., Пирсол А. Измерение и анализ случайных процессов. Пер. с англ. М.:Мир, 1974. 464 с.
Браун, Датнер. Анализ вибраций роликовых и шариковых подшипников. Пер. с англ. Конструирование и технология машиностроения, 1979, т.101, N1, с. 65 — 82.
Васильева Р.В., Рунов Б.Т. Надежность контроля вибрации турбоагрегатов. Электрические станции, 1971, N2, с. 44 — 47.
Вибрация и вибродиагностика судового электрооборудования. Александров А. А., Барков А.В., Баркова Н.А., Шафранский В.А. Л.: Судостроение, 1986. 276 с.
Вибрации в технике. Справочник /Под ред. Генкина. М.: Машиностроение. Т.1—Т5. 1981.
Виброакустическая диагностика зарождающихся дефектов. Балицкий Ф.Я., Иванова М.А., Соколова А.Г., Хомяков Е.И. М.: Наука, 1984. 129 с.
Гольдин А.С. Устранение вибрации турбоагрегатов на тепловых электростанциях. М.:Энергия, 1980. 96 с.
Диментберг Ф.М., Шаталов К.Т., Гусаров А.А. Колебания машин. М.Машиностроение, 1964. 308 с.
Иориш. Ю.И. Виброметрия. М.: Машиностроение, 1965. 773 с.
Карасев В.А., Максимов В.П., Сидоренко М.К. Вибрационная диагностика газотурбинных двигателей. М.: Машиностроение, 1978. 132 с.
Карасев В.А., Ройтман А.Б. Доводка эксплуатируемых машин. Вибродиагностические методы. М.: Машиностроение, 1986. 192 с.
Гемке Р.Г. Неисправности электрических машин. Л., Энергия, 1980.
Исакович М.М., Клейман Л.И., Перчанок Б.Х. Устранение вибраций электрических машин. Л.: Энергия, 1979.
Коллакот Р.А. Диагностирование механического, оборудования. Пер. с англ. Л.: Судостроение, 1980. 296 с.
Попков В.И. Виброакустическая диагностика и снижение виброактивности судовых механизмов. Л.: Судостроение, 1974. 224 с.
Рунов Б.Т. Исследование и устранение вибрации паровых турбоагрегатов. М.: Энергоиздат, 1982. 352 с.
Рунов Б.Т., Дон Э.А. Влияние эксплуатационных режимов на работу опорных подшипников мощных паровых турбин. Энергомашиностроение, 1970, N1, с. 15—17.
Смирнов Н.В., Дунин —Барковский И.В. Курс теории вероятностей и математической статистики для технических приложений. М.: Наука, 1969. 511 с.
Цеханский К.Р. Исследования качества крепления пьезодатчиков на их технические характеристики. В кн.: Вибрационная техника, вып.1. М.: МДНТП, 1969. с. 123—128.
Mitchell J.S. "An Introduction to Machinery Analysis and Monitoring". 1981. Mourbray J. "Reliability - Centered Maintenance". 1991.
• Приложение 2 • а2 — 15 •
гармоник и/или боковых частот соответствующих этим составляющим с интервалами в 49,6 (сачтота 20,16 мс) Гц и 121,5 Гц (сачтота 8,23 мс) соответственно.
В нижней части рис. а2—12 слева показан тот же спектр но обработанный так, что частоты, которые находятся ниже приблизительно половины зубчатой частоты, удалены (зубчатая частотная составляющая помечена индексом fz ). Путем обработки этого спектра определен соответствующий кепстр, который не содержит составляющую на сачтоте 8,23 мс (121,5 Гц), помеченную наклонной стрелкой на кепстре, помещенном в верхней части рисунка. Это указывает на то, что она образуется из среднечастотной области спектра (см. группу гармоник, помеченных наклонными стрелками), точнее той области спектра частоты которой были удалены, и связана с дефектами, проявляющимися в этом диапазоне. Однако, наличие составляющей на сачтоте 20,16 мс (49,6 Гц — fr1 , частота вращения ведущей шестерни) говорит о том, что она связана с высокочастотными составляющими виброакустического сигнала и соответствующими дефектами. Из этого можно заключить, что шестерня, вращающаяся на частоте 49,6 Гц ( fr1, частота вращения ведущей шестерни), может иметь зарождающийся дефект, в то время как вал, вращающийся с частотой 121,5 Гц (помечена индексом fr2 — частота вращения ведомой шестерни), вероятно имеет неуравновешенность ротора или другой развитый дефект, проявляющийся в области средних частот.
Наконец, кепстральный анализ в значительной степени нечувствителен к изменениям фазы исследуемых сигналов и к особенностям путей распространения механических колебаний. Например, кепстры механических колебаний одинаковых подшипников качения, зубчатых передач и др., в различных агрегатах с одинаковой частотой вращения ротора, практически идентичны по сачтотному составу.
• Приложение 2 • а2 — 13 •

Рис. а2—9. Принцип определения и анализа огибающих.
Измерения вибрации при выделении огибающей следует производить тщательно, поскольку многие факторы, такие как колебания кабеля датчика или дрожание руки при измерениях с применением щупа могут привести к значительному искажению виброакустического сигнала и неверному диагнозу.
Кепстр.
Агрегаты с вращающимся ротором в большинстве случаев имеют полигармонический спектр возбуждения колебаний. Например, при некоторых дефектах зубчатого зацепления или подшипников качения иногда характерно присутствие десятков гармоник основных частот возбуждения. В этом случае используя лишь спектральное представление сигнала трудно найти информативный диагностический признак. Для сжатия полученной информации иногда прибегают к нелинейным преобразованиям, например логарифмированию, что довольно часто используется при спектральном анализе вибропроцессов. При решении задач вибродиагностики роторных агрегатов информативной характеристикой может оказаться кепстр (анаграмма слова спектр).
Существуют различные способы определения кепстра: квадрат косинусной или синусной трансформации Фурье логарифмического спектра либо сумма квадратов косинусной и синусной трансформации Фурье. Наибольшей помехоустойчивостью обладает кепстр, определяемый как косинусная трансформация Фурье логарифмического спектра (псевдокорреляция).
• Приложение 2 • а2 — 11 •
В правой части рис. а2—10 приведены временные сигналы, которые обработаны с применением синхронного накопления при 1, 15 и 50 усреднениях. При n = 1 значительно преобладает случайная составляющая вибрации, причиной которой является износ подшипника качения, в то время как при n = 50 (справа внизу) можно видеть детерминированную составляющую на частоте вращения ротора, вызываемую неуравновешенностью ротора.
Спектр.
Рассмотрим приведенное на рис. а2— 11 изображение сигналов вибрации в трехмерной системе координат. В плоскости ЕFGН изображен временная реализация 7 (см. рис. а2 —09), слева от ее, в порядке возрастания частоты, расположены четыре составляющие ее синусоиды, которые развиваются во времени вдоль оси 0t. Их проекция на плоскость АВСD называется частотным спектром (в осях Амплитуда — Частота А0t). Вдоль оси 0f можно видеть четыре пика этих составляющих с частотными отношениями 1:2: 3,7 : 7 и единичной амплитудой. Иначе говоря спектр вибрации это совокупность соответствующих гармонических составляющих значений величины характеризующих вибрацию, в которой указанные значения расположены в порядке возрастания номеров гармонических составляющих.

Рис. а2—11. Трехмерное изображение виброакустического сигнала.
Различают частотный спектр, амплитудный спектр, фазовый спектр и мощности спектр (спектр квадратов амплитуд скорости).
Преобладающей частотой спектра, fосн, называют частоту которой соответствует глобальный максимум соответствующего спектра. Одним из применений понятия преобладающей частоты является то, что при выполнении условия

полигармоническая вибрация может характеризоваться параметрами моногармонической вибрации.
• Приложение 2 • а2 — 9 •
сдвинута относительно первой на 90 градусов, а четвертой соответственно на 180 градусов.

Рис. а2—09. Суммирование вибраций одинаковой амплитуды с разными фазовыми соотношениями и периодами.
Если один достаточно развитый дефект из приведенных выше имеется у исполнительного механизма в отсутствие других (и при этом колебательный процесс близок к детерминированному), то по параметрам почти синусоидального колебания в некоторых случаях можно его распознать (т.е, диагностировать грубые отказы в работе). Однако, во многих других ситуациях, в частности, например, когда агрегат имеет несколько развитых дефектов одновременно, различить исходные источники даже гармонических колебаний затруднительно.
Кривая с индексом 3 является суммой синусоидальных колебаний с индексами 1 и 2, кривая 5 — сумма кривых 1, 2 и 4 (или 3 и 4), а кривая 7 — сумма 1, 2, 4, и 6 (или 5 и 6).
Кривая с индексом 7 сходна с достаточно часто встречающимся на практике характером временного сигнала вибрации. В таком сигнале сложно выделить исходные частотные составляющие, и сигнал, на первый взгляд, непериодический.
И все же в ряде случаев, когда в колебательном процессе, сопровождающем работу агрегата, в состав которого, например, входит поршневой насос или двигатель внутреннего сгорания, необходимо сохранить фазовые соотношения, несущие основную информацию о параметрах технического состояния, бывает необходимо обратиться к анализу временных сигналов процесса. Выделение импульсов, формируемых тем или иным узлом, осуществляется временной селекцией. Диагностическими признаками в данном случае могут служить смещение соответствующего импульса по фазе и его амплитуде.
• Приложение 2 • а2 — 7 •

Ускорение механических колебаний также часто измеряется в единицах силы тяжести (g), хотя эта единица и не входит в международную систему единиц, согласно ИСО. Весьма удобно, что единицы g и м/с2 взаимно связаны коэффициентом приблизительно равным 10 (9,81), так, что легко в уме производить преобразования с точностью до 2%.
Условия выбора одного из параметров механических колебаний.
Применение вибродатчика, генерирующему сигнал пропорциональный ускорению, дает возможность измерения и анализа не только виброускорения, а также виброскорости и виброперемещения. Нужное преобразование виброускорения в виброскорость и виброперемещение обеспечивают электронные интеграторы, которыми снабжено большинство виброизмерительных приборов.
При измерении вибрации в широком частотном диапазоне играет важную роль определяемый параметр, в частности тогда, когда подлежащий измерению процесс содержит много составляющих с разными частотами. Измерение виброперемещения приводит к подчеркиванию составляющих сигнала с низкими частотами, в то время как измерение виброускорения приводит к подчеркиванию составляющих сигнала с высокими частотами.
Опытом подтверждено, что СКЗ виброскорости, измеряемое в частотном диапазоне 10...1000 Гц, наиболее точно отображает опасность механических колебаний.
Возможным объяснением этого эмпирического правила является соответствие определенного уровня виброскорости определенному уровню энергии, так что низкочастотные и высокочастотные составляющие исследуемого процесса имеют с точки зрения энергии колебаний идентичные значения ("вес").
Условно будем называть вибрацию в диапазоне лежащем ниже частоты вращения ротора низкочастотной, соответственно от частоты вращения ротора до ее 20 гармоники — среднечастотной, а выше — высокочастотной.
Свободными колебаниями системы называют вибрацию системы проходящую без переменного внешнего воздействия. Свободные колебания системы характеризуются собственной частотой системы
fс = 1/То,
где Т0 — период свободных колебаний (определяется как интервал времени между двумя соседними максимальными значениями колеблющейся величины).
Некоторые операции по обработке виброакустичекого сигнала.
Фильтрация (частотная селекция) виброакустического сигнала.
Назначением операции фильтрации (частотной селекции) является выделение информативных компонентов виброакустического сигнала в ограниченной полосе частот. Основание для фильтрации сигнала — присутствие помех, маскирующих компоненты вибрации, содержащие информацию о состоянии диагностируемого узла агрегата. Выделение компонентов гармонического ряда частот вынужденных колебаний, выделение резонансных частот, отделение оборотных компонентов от высокочастотных — некоторые: из задач, требующих применения фильтрации виброакустического сигнала.
• Приложение 2 • а2 — 5 •
Среднее значение отображает временное развитие исследуемых колебаний, но его практическое применение ограничено ввиду того, что оно не имеет непосредственной связи ни с какой физической величиной этих колебаний.
Среднеквадратическое значение (СКЗ) является самым важным, так как в нем учитывается временное развитие исследуемых колебаний и оно непосредственно отображает значение, связанное с энергией сигнала и, следовательно, разрушающей способностью этих колебаний.
Параметры вибрации на примере колебаний камертона.
При рассмотрении камертона можно амплитуду волны колебаний считать равной физическому смещению (виброперемещению) концов его плеч относительно положения покоя.

Рис. а2—05. Параметры колебаний камертона.
Однако, в основой описания движения камертона может служить не только смещение, а также скорость или ускорение колебаний. Главное различие этих трех параметров заключается во взаимном фазовом сдвиге их кривых, отображающих зависимость амплитуды от времени (см. рис. а2 —05).

Рис. а2—06. Взаимосвязь виброускорения, виброскорости и виброперемещения.
На рисунке а2 - 06 стрелкой с индексом 1 помечен максимум перемещения плеча камертона вверх и соответственно максимум ускорения вниз, при этом скорость равна нулю. Стрелкой 2 — максимум нисходящей скорости. Стрелкой 3
• Приложение 2 • а2 — 3 •

Рис. а.2—02. Шейка вала в подшипнике скольжения колеблется относительно оси вкладыша подшипника (или корпуса подшипника).

Рис. а2—03. Опора подшипника и точка на роторе колеблются в абсолютной системе координат.
Источником вибрации в простейшем случае является условная точечная масса А с заданным эксцентриситетом (приводящая к появлению при вращении центробежной силы), вызывающая во время вращения ротора переменные нагрузки на опорах и его изгиб, называемая неуравновешенной массой (точечной неуравновешенной массой). Фазы вибрации связывают с угловым положением ротора. В простом случае разберем фазу вибрации на частоте вращения ротора. Для определения точки начала отсчета фазы на ротор наносится метка В (см. рис. а2 —03). Фазой вибрации принято считать угловое положение метки в момент максимального положительного отклонения вибрирующей поверхности от положения равновесия. Как видно из рис. а2 — 03
начальная фаза вибрации ф определяет положение неуравновешенной массы А относительно метки на роторе В.
Встречающиеся на практике вибрации обычно являются сложными полигармоническими вибрациями, т.е. содержат гармонические составляющие различной частоты.
• Приложение 2 • a 2 – 1 •
Приложение 2
Общие сведения о вибрации.
Колебания.
Колебаниями скалярной величины называют процесс поочередного возрастания и убывания обычно во времени значений какой —либо величины (в области вибрации термин "колебания" применяется только для случаев изменения величины во времени, а величина, значения которой колеблются, называется колеблющейся величиной).
Механическими колебаниями называют колебания значений кинематической или динамической величины, характеризующей механическую систему.
Гармонические колебания.
В простом случае вибрирующая поверхность (точка поверхности, тело) совершает колебания содержащие составляющую лишь одной частоты, при этом координаты колеблющейся точки определяются уравнением

где положительная величина А (иногда обозначают r, rа) называется амплитудой гармонического колебания (максимальное значение колеблющейся величины),
(wt+j) — называется фазой гармонического колебания (аргумент синуса, которому пропорционально значение колеблющейся величины), j —называется начальной фазой (фаза гармонического колебания в момент времени t = 0), w — называется циклической или круговой частотой (производная по времени от фазы гармонических колебаний).
Такие колебания называются синусоидальными (гармоническими) и определяются рядом следующих параметров:
Приложение 1 • а1 — 12 •
Текущий ударный спектр Ударный спектр, определенный по откликам резонаторов во время
ударного воздействия.
Термическая нестабильность Изменение дисбалансов ротора вследствие изменения его
дисбалансов ротора температуры. Термическая нестабильность дисбалансов ротора
может быть постоянной или временной.
Точка ввода [точка измерений] Точка пересечения акустической оси преобразователя с
поверхностью объекта контроля.
Точность балансировки Точность балансировки характеризуется произведением удельного
дисбаланса на наибольшую частоту вращения ротора в эксплуатационных условиях.
Третьоктавная полоса частот Полоса частот, у которой отношение вехней граничной частоты к
[Треть октавы] нижней равно кубическому корню из 2.
Трехкомпонентный Акселерометр с тремя взаимно перпендикулярными
акселерометр измерительными осями.
Угловая вибрация Вибрация твердого тела при его вращательном движении.
Угловая частота Производная по времени от фазы гармонических колебаний
(гармонических колебаний) (вибрации), равная частоте, умноженной на 2 p (см. термин
(вибрации) "гармонические колебания").
Угол дисбаланса Угол, определяющий положение вектора дисбаланса в системе
координат, связанной с осью ротора.
Угол коррекции Угол, определяющий положение корректирующей массы в системе
координат, связанной с осью ротора.
Ударное движение Движение, возникшее в результате однократного взаимодействия
тела (среды) с рассматриваемой системой, при условии, что наименьший период собственных колебаний системы или постоянная времени ее соизмеримы или больше времени взаимодействия.
Ударный спектр Зависимость пиковых откликов ряда резонаторов, возбуждаемых
рассматриваемым ударным воздействием, от собственных частот резонаторов. Откликом является ускорение, скорость или перемещение. Под резонатором понимается линейная консервативная колебательная система с одной степенью свободы.
Удельная суммарная Отношение средней суммарной оперативной трудоемкости
оперативная трудоемкость диагностирования изделия за цикл периодического технического
диагностирования обслуживания к заданной наработке изделия.
Удельный дисбаланс Отношение модуля главного вектора дисбалансов к массе ротора.
Удельный дисбаланс определяет значение эксцентриситета центра массы ротора.
Узел колебаний [Узел] Неподвижная точка среды при стоячей волне. Совокупность таких
точек может образовать узловую линию и узловую поверхность.
Узкополосные случайные Случайные колебания (вибрация) со спектром частот,
колебания (вибрация) расположенным в - узкой полосе частот. Понятие узкой полосы
частот зависит от исследуемой проблемы. Если возможны различные толкования, необходимо дать соответствующее указание.
Упругая линия Первоначальная ось тела, деформированная под действием
нагрузок.
Установившиеся колебания Периодические или почти периодические колебания (вибрация)
(вибрация) системы, которые устанавливаются в системе по прошествии
некоторого времени после начала колебаний.
Устройство сопряжения Устройство, предназначенное для соединения и разъединения
(присоединения) изделия и СТД (электрический соединитель, переходник, штуцер и
АР-)
Фаза гармонических колебаний Аргумент синуса, которому пропорционально значение
(вибрации) [Фаза] колеблющейся величина (характеризующей вибрацию) при
гармонических колебаниях (вибрации) (см. термин "гармонические
колебания").
Фазо — частотная Зависимость сдвига фаз межуд вынужденными колебаниями
характеристика (вибрацией) системы и гармоническим возбуждением с постоянной
амплитудой от частоты последнего.
Фазо — частотная Зависимость сдвига фазы между выходным сигналом акселерометра
характеристика акселерометра и задаваемым гармоническим ускорением от частоты последнего.
[ФЧХ]
Фазовый спектр Спектр колебаний, в котором величинами, характеризующими
гармонические составляющие колебаний, являются их начальные фазы.
• Приложение 1 • а1 — 10 •
Размах колебаний [Размах] Разность между наибольшим и наименьшим значениями колеблющейся величины в рассматриваемом интервале времени.
Регистрирующий Измерительный прибор, в котором предусмотрена регистрация показаний
(измерительный) прибор
Режимное изменение Изменение дисбалансов ротора, вызываемое различными условиями
дисбалансов ротора работы (влажность, давление и др.) и режимами нагружения.
Резонансная частота См. термин "Низшая собственная частота закрепленного
акселерометра измерительного преобразователя ускорения"
Резонансная частота колебаний Частота, при которой осуществляется резонанс. В системе с
системы [Резонансная частота] демпфированием резонансные частоты перемещения, скорости и ускорения различны.
Резонансные колебания Вынужденные колебания (вибрация) системы, соответствующие
(вибрация) [Резонанс] одному из максимумов амплитудно-частотной характеристики.
Резонансный вибро — Метод вибро — акустического неразрушающего контроля,
акустический метод основанный на возбуждении вынужденных упругих колебаний
[Резонансный метод] в объекте контроля или его части и анализе параметров
колебаний системы "объект контроля — преобразователь" при резонансах или вблизи них.
Ротор Тело, которое при вращении удерживается своими несущими поверхностями
в опорах. Под несущими поверхностями подразумеваются поверхности цапф или поверхности их заменяющие. Несущие поверхности ротора передают нагрузки на опоры через подшипники качения или скольжения, газовые или жидкостные потоки, магнитные или электрические поля и так далее.
Самовозбуждение колебаний Возбуждение колебаний (вибрации) системы поступлением энергии от (вибрации) [Самовозбуждение] неколебательного источника, которое регулируется движением самой
системы.
Свободные колебания Колебания (вибрация) системы, происходящие без переменного внешнего (вибрация) воздействия и поступления энергии извне.
Сдвиг фаз синхронных Разность фаз двух синхронных гармонических колебаний (вибраций) в гармонических колебаний любой момент времени.
(вибраций) [Сдвиг фаз]
Сигнал вибро - акустического Электрический или вибро —акустический сигнал, функционально
прибора (неразрушающего связанный с контролируемыми параметрами объекта контроля.
контроля)
Сигнал измерительной Сигнал, функционально связанный с измеряемой физической величиной.
информации [Измерительный
сигнал]
Силовое возбуждение Возбуждение вибрации системы вынуждающими силами и (или) (вибрации) моментами.
Синфазные (гармонические) Синхронные гармонические колебания (вибрации) с равными в любой колебания (вибрации) момент времени фазами.
Синхронные колебания Два или более одновременно совершающихся периодических колебания (вибрации) (вибрации), имеющие равные частоты.
Скольжение Разность между частотой вращения магнитного поля, создаваемого
токами статора и ротора прямой последовательности и частотой вращения ротора
Случайные колебания Колебания (вибрация), представляющие собой случайный процесс. (вибрация)
Собственная форма колебаний Форма колебаний (вибрации) линейной системы, колеблющейся с одной (вибрации) системы из собственных частот.
Собственная частота Любая из частот свободных колебаний (вибрации) линейной системы. колебаний (вибрации) Если возможны различные толкования, необходимо дать линейной системы соответствующее уточнение: "собственная частота консервативной [Собственная частота] системы" или ' собственная частота системы с линейным
демпфированием".
Собственная частота См. термин "Низшая собственная частота закрепленного измерительного преобразователя ускорения преобразователя ускорения"
Согласующее устройство Средство измерений, входящее в состав акселерометра, предназначенное для акселерометра согласования полных сопротивлений первичного измерительного
преобразователя ускорения и регистрирующего устройства. Согласующее устройство может одновременно выполнять функции масштабного измерительного преобразователя.
• Приложение 1 • а1 — 8 •
Параметрическое возбуждение Возбуждение колебаний (вибрации) системы не зависящим от состояния
(колебаний (вибрации)) системы изменением во времени одного или нескольких ее параметров
(массы, момента инерции, коэффициента жесткости, коэффициента сопротивления).
Пассивная виброзащита Вибрационная защита, не использующая энергию дополнительного
источника.
Первая гармоника Гармоника, номер которой равен единице.
Первичный (измерительный) Измерительный преобразователь, к которому подведена измеряемая преобразователь величина, т. е. первый в измерительной цепи.
Переходные колебания Процесс перехода от установившихся колебаний (вибрации) к другим (вибрация) установившимся колебаниям (вибрации).
Вместо установившихся
колебаний может быть состояние равновесия.
Период колебаний (вибрации) Наименьший интервал времени, через который при периодических [Период] колебаниях (вибрации) повторяется каждое значение колеблющейся
величины (характеризующей вибрацию).
Периодические колебания Колебания (вибрация), при которых каждое значение колеблющейся (вибрация) величины (характеризующей вибрацию) повторяется через равные
интервалы времени.
Пиковая ударная скорость Наибольшая абсолютная ударная скорость.
Пиковое значение Наибольшее абсолютное значение экстремумов колеблющейся величины (колеблющейся величины) в рассматриваемом интервале времени.
Пиковое ударное перемещение Наибольшее абсолютное ударное перемещение. Пиковое ударное ускорение Наибольшее абсолютное ударное ускорение.
Плоская вибрация точки Вибрация точки по плоской траектории.
Плоская волна Волна, фронт которой представляет собой плоскость, перпендикулярную к
направлению распространения волны.
Плоскость измерения Плоскость, перпендикулярная оси ротора, в которой измеряют значение (вибрации (дисбаланса)) виблации (и угол дисбаланса).
Плоскость коррекции Плоскость, перепендикулярная оси ротора, в которой расположен центр корректирующей массы.
Плоскость приведения Плоскость, перпендикулярная оси ротора, в которой задают значение и дисбаланса угол дисбаланса.
Поверхность ввода Поверхность объекта контроля, через которую вводятся упругие колебания.
Погрешность акселерометра Погрешность акселерометра при измерении переменных во времени в динамическом режиме ускорений.
Показание средства измерений Значение величины, определяемое по отсчетному устройству и выраженное в принятых единицах этой величины.
Полностью сбалансированный Ротор, у которого главный вектор и главный момент дисбалансов равны ротор нулю. В жестком полностью сбалансированном роторе главная
центральная ось инерции совпадает с осью ротора.
Полоса частот Совокупность частот в рассматриваемых пределах.
Полуоктавная полоса частот Полоса частот, у которой отношение верхней граничной частоты к [Полуоктава] нижней равно корн квадратному из 2.
Поперечная волна Волна, направление распространения которой ортогонально траекториям колеблющихся точек среды.
Порог чувствительности Минимальное значение измеряемого ускорения, вызывающее акселерометра закономерное изменение выходного сигнала акселерометра от его нулевого значения.
Поступательная вибрация Вибрация твердого тела при его поступательном движении.
Почти гармонические Колебания (вибрация), при которых значения колеблющейся величины колебания (вибрация) (характеризующей вибрацию) изменяются во времени по закону: Аsin(wt+j),
где t — время; А, w, j — медленно меняющиеся функции времени (в частности, некоторые из них могут быть постоянными). Примечание: указанные медленно меняющиеся функции удовлетворяют неравенствам: |dА/dt| £ Aw???|dw/dt| £ w2 , |dj/dt| £ w
Почти периодические Колебания (вибрация), при которых каждое значение колеблющейся колебания (вибрация) величины почти повторяется через некоторые постоянные интервалы
времени.
Предел измерений Наибольшее или наименьшее значение диапазона измерений (акселерометра) (акселерометра).
• Приложение 1 • а1 — 6 •
Корректировка масс ротора Процесс изменения или перемещения корректирующих масс для уменьшения дисбалансов ротора.
Корректирующая масса Масса, используемая для уменьшения дисбалансов ротора. Корректирующая масса может добавляться или удаляться из тела ротора, а также перемещаться по нему.
Коэффициент безразборного Отношение числа контролируемых параметров изделия данного вида диагностирования диагностирования, для измерения которых не требуются демонтажно —
монтажные работы, к общему числу контролируемых параметров изделия данного вида диагностирования.
Коэффициент демпфирования Отношение коэффициента сопротивления к удвоенной массе или
(системы) удвоенному моменту инерции. Определение дано для системы с одной степенью свободы.
Коэффициент жесткости Взятая с противоположным знаком производная характеристики [Жесткость] восстанавливающей силы или момента. Определение дано для системы с
одной степенью свободы.
Коэффициент преобразования Отношение изменения сигнала на выходе акселерометра к вызывающему его акселерометра изменению ускорения, направленного вдоль измерительной оси.
Коэффициент преобразования Отношение сигнала на выходе измерительного преобразователя, измерительного отображающего измеряемую величину, к вызывающему его сигналу на входе
преобразователя преобразователя.
Коэффициент податливости Величина, обратная коэффициенту жесткости. Определение: дано для [Податливость] системы с одной степенью свободы.
Коэффициент сопротивления Взятое с противоположным знаком отношение диссипативной силы или [Сопротивление] момента к соответствующей обобщенной скорости для линейной системы.
Определение дано для системы с одной степенью свободы.
Кратно - частотная вибрация Вибрация с частотой, кратной частоте вращения и не зависящей от неуравновешенности ротора. Такая вибрация может быть вызвана различными причинами, например анизотропией ротора.
Логарифмический декремент Натуральный логарифм отношения двух последовательных максимальных или (колебаний) минимальных значений величины при затухающих свободных колебаниях.
Логарифмический уровень Характеристика колебаний, сравнивающая две одноименные физические колебаний [Уровень величины, пропорциональная десятичному логарифму отношения колебаний] оцениваемого и исходного значений величины. Для энергетических величин
(энергии, мощности и т. п.) уровень, измеряемый в белах L = lg(а/ао), измеряемый в децибелах L= 10 lg(а/ао), где а — оцениваемое значение энергии (мощности и т. п.), ао— исходное значение энергии (мощности и т. п.). Для скорости, ускорения, силы и т. п. уровень, измеряемый в белах L = 2lg(b/bо), измеряемый в децибелах L = 20lg(b/bо), где b — оцениваемое значение скорости (ускорения и т. п.), bо— исходное значение скорости (ускорения и т. п.). Принятые при вычислении исходные значения ао, bо должны быть указаны в каждом конкретном случае.
Масштабный измерительный Измерительный преобразователь, предназначенный для изменения преобразователь [Масштабный величины в заданное число раз. Примеры: измерительный трансформатор тока, преобразователь] делитель напряжения, измерительный усилитель.
Межопорный ротор Двухопорный ротор, существенная часть массы которого расположена между опорами.
Метод измерений Совокупность приемов использования принципов и средств измерений.
Механические колебания Колебания значений кинематической или динамической величины, характеризующей механическую систему.
Механический импеданс Отношение амплитуды гармонической вынуждающей силы к комплексной [Импеданс] амплитуде скорости при гармонической вынужденной вибрации линейной
системы.
Моментная балансировка Балансировка, при которой определяется и уменьшается главный момент дисбалансов ротора, характеризующий его моментную неуравновешенность. Моментную балансировку проводят не менее чем в двух плоскостях коррекции.
• Приложение 1 • а1 — 4 •
Динамическая Неуравновешенность ротора, при которой ось ротора и его главная неуравновешенность ротора центральная ось инерции пересекаются не в центре масс или [Динамическая перекрещиваются. Динамическая неуравновешенность состоит из неуравновешенность] статической и моментной неуравновешенностей. Динамическая
неуравновешенность полностью определяется: главным вектором и главным моментом дисбалансов ротора или двумя векторами дисбалансов, в общем случае разных по значению и непараллельных, лежащих в двух произвольных плоскостях, перпендикулярных оси ротора ("крест дисбалансов").
Динамическое гашение Метод вибрационной защиты посредством присоединения к защищаемому вибрации [Динамическое объекту системы, реакции которой уменьшают размах вибрации объекта в виброгашение] точках присоединения системы.
Динамическая балансировка Балансировка, при которой определяются и уменьшаются дисбалансы ротора, характеризующие его динамическую неуравновешенность. Динамическую балансировку жесткого ротора достаточно проводить в двух плоскостях коррекции. Балансировку гибкого ротора проводят обычно более чем в двух плоскостях коррекции. При динамической балансировке уменьшаются как моментная, так и статическая неуравновешенности ротора одновременно.
Дисбаланс Векторная величина, равная произведению неуравновешенной массы на ее эксцентриситет. Вектор дисбаланса перпендикулярен оси ротора, проходит через центр неуравновешенной массы и вращается вместе с ротором.
Направление вектора дисбаланса совпадает с направлением эксцентриситета неуравновешенной массы.
Длина гармонической волны Расстояние между двумя соседними максимумами или минимумами [Длина волны] перемещения точек среды.
Длительность действия Интервал времени от момента появления до момента исчезновения ударного ударного ускорения ускорения. Моменты появления и исчезновения ударного ускорения
определяются на условном нулевом значении под которым понимается определенная часть пикового значения измеряемой физической величины.
Длительность фронта Интервал времени от момента появления ударного ускорения до момента, ударного ускорения соответствующего его пиковому значению.
Дискретный спектр Спектр колебаний или частот, в котором частоты гармонических составляющих колебаний образуют дискретное множество.
Диссипативная сила (момент) Сила (момент), возникающая при движении механической системы и вызывающая рассеяние механической энергии.
Добротность системы Величина, обратная удвоенному относительному демпфированию системы. [Добротность] Определение дано для системы с одной степенью свободы.
Дорезонансные колебания Вынужденные колебания (вибрация) системы, частота которых меньше (вибрация) резонансной. Определение дано для системы с одной степенью свободы.
Дополнительная погрешность Изменение погрешности (акселерометра) по входу, вызванное отклонением (акселерометра по входу) одной из влияющих величин от ее нормального значения или выходом ее за
пределы нормальной области значений.
Допустимый дисбаланс Наибольший остаточный дисбаланс в рассматриваемой плоскости, перпендикулярной оси ротора, который считается приемлемом.
Жесткий ротор Ротор, который сбалансирован на частоте вращения, меньшей первой критической в двух произвольных плоскостях коррекции и у которого значения остаточных дисбалансов не будут превышать допустимые на всех частотах вращения вплость до наибольшей эксплуатационной. Ротор должен балансироваться на опорах, жесткость которых максимально приближается к жесткости его опор в эксплуатационных условиях. Жестким иногда называют ротор, критическая частота вращения которого намного выше его эксплуатационной частоты вращения.
Зарезонансные колебания Вынужденные колебания (вибрация) системы, частота которых больше (вибрация) резонансной. Определение дано для системы с одной степенью свободы.
Затухающие колебания Колебания (вибрация) с уменьшающимися значениями размаха.
Значение дисбаланса Числовое значение, равное произведению неуравновешенной массы на модуль ее эксцентриситета.
Значение физической Оценка физической величины в виде некоторого числа принятых для нее величины [Значение величины] единиц. Отвлеченное число, входящее в значение физической величины,
называется числовым значением.
Измерение Нахождение значения физической величины опытным путем с помощь специальных технических средств.
Измерительная информация Информация о значениях измеряемых физических величин.
• Приложение 1 • а1 — 2 •
Вибрационная защита Совокупность средств и методов уменьшения вибрации, воспринимаемой [Виброзащита] защищаемыми объектами.
Вибрационная техника Совокупность методов и средств возбуждения, полезного применения и [Вибротехника] измерения вибрации, вибрационной диагностики, вибрационной защиты и
вибрационных испытаний.
Вибрационная устойчивость Свойство объекта при заданной вибрации выполнять заданные функции и [Виброустойчивость] сохранять в пределах норм значения параметров.
Вибрационно - Метод акустического неразрушающего контроля, основанный на анализе диагностический параметров вибрации, возникающей при работе объекта контроля.
(акустический) метод
Вибрационные испытания Испытания объекта при заданной вибрации.
[Виброиспытания]
Вибрация Движение точки или механической системы, при котором происходят
колебания характеризующих его скалярных величин.
Вибро - акустический Неразрушающий контроль, основанный на применении упругих колебаний, неразрушающий контроль возбуждаемых или возникающих в объекте контроля.
[Вибрационный контроль]
Вибро - акустический метод Метод вибро - акустического неразрушающего контроля, основанный на свободных колебаний [Метод возбуждении свободно затухающих упругих колебаний в объекте контроля свободных колебаний] или его части и анализе параметров этих колебаний.
Вибро - акустический прибор Вибро - акустическое средство неразрушающего контроля, состоящее из неразрушающего контроля электронного блока и преобразователей, вспомогательных и регистрирующих [Виброизмерительный прибор] устройств, использующее методы вибро — акустического неразрушающего
контроля.
Вибровозбудитель Усторойство, предназначенное для возбуждения вибрации и используемое самостоятельно или в составе другого устройства.
Виброизоляция Метод вибрационной защиты посредством устройств, помещаемых между источником возбуждения и защищаемым объектом.
Виброизолятор [Изолятор] Устройство, осуществляющее виброизоляцию.
Виброперемещение Составляющая перемещения, описывающая вибрацию.
Виброметрия Совокупность средств и методов измерения величин, характеризующих вибрацию.
Виброскорость Производная виброперемещения по времени.
Виброускорение Производная виброскорости по времени.
Восстанавливающая сила Сила (момент), возникающая при отклонении системы от состояния (момент) равновесия и направленная противоположно этому отклонению.
Входной сигнал средства Сигнал, поступающий на вход средства измерений. Пример: напряжение на измерений [Входной сигнал] входных зажимах усилителя.
Вынужденные колебания Колебания (вибрация) системы, вызванные и поддерживаемые силовым и (вибрация) (или) кинематическим возбуждением.
Вынуждающая сила (момент) Переменная во времени (внешняя) сила (момент), не зависящая от состояния системы и поддерживающая ее вибрацию.
Высокочастотная балансировка Балансировка на такой частоте вращения, при которой балансируемый гибкий (применительно к гибким ротор уже не может рассматриваться как жесткий. При высокочастотной роторам) балансировке частота вращения ротора близка к эксплуатационной.
Высокочастотную балансировку обычно проводят более чем в двух плоскостях коррекции.
Высшая гармоника Гармоника, номер которой больше единицы.
Выходной сигнал средства Сигнал, получаемый на выходе средства измерений. Пример: усиленное
измерений [Выходной сигнал] напряжение на выходе измерительного усилителя.
Гармоника Гармоническая составляющая периодических колебаний.
Частоты гармоник
кратны частоте анализируемых периодических колебаний.
Гармоническая волна Волна, при которой все точки среды совершают гармонические колебания.
Гармонические колебания Колебания (вибрация), при которых значения колеблющейся величины (вибрация) (характеризующей вибрацию) изменяются во времени по закону: Аsin(wt + j),
где t — время; А, w, j — постоянные параметры; А — амплитуда; wt+j — фаза; j — начальная фаза; w?— угловая частота.
• Нарушения гидро и газодинамики потока и пульсации давления • 12 — 20
определенной частоте вращения ротора турбины возникали интенсивные колебания лопаток на собственной частоте, что привело к из повреждению. Как можно видеть из анализа спектров, приведенных на рис. 12—14, изменения вибрации были скорее не количественные, а качественные. Уровень высокочастотной вибрации не был опасным, однако в спектре вибрации появились широкополосные области, содержащие компоненты на лопаточной частоте, боковые частоты, случайная вибрация.
Как выяснилось в дальнейшем, на аналогичной установке другого предприятия произошло разрушение лопатки турбины этого типа практически без изменения характера вибрации в низкочастотной и среднечастотной области спектра.
Одна из основных проблем, возникающих при мониторинге компрессорного оборудования и турбоагрегатов, заключается в необходимости обнаружения дефектов лопаток по характеру вибрации и оценки степени развития дефекта при сравнении текущего и "эталонного" спектра: т.е. решения вопроса, связано ли увеличение вибрации на лопаточных частотах и боковых частотах и в других областях спектра с дефектами лопаток. Во многих случаях на этот вопрос можно ответить утвердительно.
Примером успешного обнаружения дефектов лопаток при использовании типичного спектра могут служить приведенные на рис. 12—15 спектры вибрации однотипных компрессоров с нормальным (нижний спектр, индекс Коt — 01) и дефектным (верхний спектр и временной сигнал, индекс Nur —02) состоянием лопаток.
Нижний — типичный спектр вибрации одного из восьми охваченных вибромониторингом однотипных газоперекачивающих агрегатов, работающего при номинальной нагрузке, который можно считать "эталонным". Верхний — первый спектр и форма сигнала, полученные при расширении программы мониторинга вибрации на один из ранее неконтролируемых агрегатов. Вибрация обоих агрегатов на лопаточной частоте fл1 сопоставима, а одно из главных отличий двух спектров: вибрация на боковых частотах вокруг нее (fЛ1±кfr) весьма существенна. Однако по уровню вибрации на боковых частотах трудно дать какое —либо заключение о степени развития и серьезности дефекта. При ревизии, после останова "подозрительного" агрегата, были обнаружены поврежденные лопатки первой ступени.
Более достоверные сведения о степени развития подобных дефектов можно получить используя спектральный анализ огибающей высокочастотной вибрации вокруг лопаточной частоты и кепстральный анализ.
Важнейшим условием для получения достоверных результатов при сравнении "эталонного" и рабочего спектров, особенно в высокочастотной области, следует считать равные технологические (эксплуатационные) условия работы однотипных агрегатов, особенно по нагрузке.
• Нарушения гидро и газодинамики потока и пульсации давления • 12 18 •
Окружная динамическая неравномерность зазоров в уплотнениях из-за изгибных колебаний роторов.
Силы, возникающие при этом можно разделить на три группы: так называемые "венцовые", связанные с изменением окружных усилий на рабочих лопатках вследствие неравномерных протечек среды по окружности уплотнений; "бандажные" силы, связанные с окружной неравномерностью давления среды, образующейся при колебаниях ротора в канале уплотнений проточной части вследствие неконцентричности ротора и статора; "лабиринтные" силы, имеющие туже природу, возникающие в каналах развитых промежуточных и концевых уплотнений. Эта группа сил способствует самовозбуждающимся колебаниям ротора, рассмотренным в разделе низкочастотной вибрации главы о дефектах подшипников скольжения.
При относительном смещении осей ротора и статора в проточной части турбины или компрессора может происходить изменение зазоров у венцов лопаток и в уплотнениях, распределенное по закону косинуса, приводящее к окружному перераспределению протечек среды через уплотнения, расходов и скоростей среды через межлопаточные каналы рабочих колес, давлений в межвенцовом зазоре, входных углов потока перед лопатками и др. Результирующая возникающих при этом дополнительных окружных сил, распределенных по закону косинуса, направлена в сторону вращения ротора перпендикулярно его прогибу, способствует неустойчивости ротора (см. главу "Дефекты подшипников скольжения") и ее зависимости от расхода среды и радиальных зазоров. "Венцовые" и "бандажные" силы пропорциональны плотности среды и перепаду давления на ступень.
Неоднородность потока в проточной части агрегатов с осевым потоком.
Вибромониторинг и изучение влияния неоднородности потока в проточной части агрегатов с осевым потоком на вибрацию представляют весьма сложную задачу и требует высокого профессионализма при измерениях в силу ряда причин, некоторые из которых: высокая частота колебаний на лопаточных частотах (8...20 кГц), т.е. необходимость применения высокочастотных пьезодатчиков и специальных способов их установки, нередко высокие температуры корпуса турбины (компрессора), затухание высокочастотных колебаний и др.
Как и в центробежных агрегатах, причина этих колебаний — газодинамические силы от неоднородности потока вокруг рабочего колеса, т.е. неравномерность поля скоростей и давлений по шагу между лопастями колеса, возникающие при вращении рабочего колеса, и происходящие при этом циркуляции рабочей среды вокруг лопасти, а также "провалы" скорости при обтекании вращающихся лопастей. Турбулентность и неоднородность потока приводит к возникновению сложной по частотному составу вибрации, включающей в том числе компоненты на частоте вращения ротора и ее гармониках, на лопаточных частотах и их гармониках (mfл), боковых частотах mfЛ±kfr , вибрации некратной частоте вращения ротора (например на собственной частоте лопаток), а также к широкополосной случайной вибрации.
Хотя частотный состав спектра и значения компонентов высокочастотной вибрации большинства агрегатов индивидуальны в силу их сильной зависимости от множества конструктивных и эксплуатационных параметров, а также особенностей распространения всокочастотных колебаний, в большинстве случаев возможно создание обобщенных "эталонных" спектров по типам и маркам агрегатов. Статистические данные показывают, что вибрация на лопаточных
• Нарушения гидро и газодинамики потока и пульсации давления • 12 — 16 •
возникновению кавитационных процессов. При малых расходах наблюдается неоднородная работа межлопаточных каналов колеса (сопровождающаяся колебаниями на лопастных частотах), что также может приводить к кавитационным процессам и соответствующей вибрации.

Рис. 12—11. Спектры огибающей высокочастотной вибрации при низкочастотных колебаниях скоростей потока на входе рабочего колеса насоса в области малых подач (инфразвуковые колебания) на корпусе, входном и выходном патрубках насоса.
В областях подач близких к нулевым, наряду с лопаточной частотой, сильно возрастает низкочастотная вибрация (см. рис. 12—11), которая крайне опасна. Инфразвуковые колебания часто вызывают резонансы крупных частей и деталей агрегата, быстро разрушающие агрегат в целом.
При статическом эксцентриситете в спектре огибающей высокочастотной вибрации появляются лопастные частоты, fЛ (см. рис. 12— 12).
При динамическом эксцентриситете, неравномерном износе и различных дефектах изготовления лопаток рабочего колеса (см. рис. 12—13) присутствуют частота вращения ротора (fг), лопастная частота (fЛ) и боковые частоты вокруг лопастной частоты (fл±kfr , см. также неоднородность потока в рабочей части и гидродинамическая неуравновешенность).
• Нарушения гидро и газодинамики потока и пульсации давления • 12 — 14 •
Гидродинамическая неуравновешенность.
Ротор насоса, механически уравновешенный, при работе насоса может оказаться гидродинамически неуравновешенным. Это происходит, например, при нарушении технологии изготовления: когда рабочее колесо изготовлено недостаточно точно и различается по шагу и углу между лопастями, по длине, толщине и углам установки лопастей или при их эксплуатационном износе.
Различие в размерах межлопастных каналов рабочего колеса приводит к различному заполнению их жидкостью и, как следствие, к несовпадению центра массы жидкости, заполняющей колесо, с осью вращения ротора. При этом неуравновешенные силы, обычно небольшие, действующие на отдельные лопасти рабочего колеса, приводят к вибрации на частоте вращения ротора. Этот эффект усиливается при кавитации из —за появления газовой фазы в кавернах, возникающих у входных кромок лопастей рабочего колеса. Оценка гидродинамической неуравновешенности рабочих колес различных типов насосов свидетельствует, что она выше у литых колес.
Диагностические признаки гидродинамической неуравновешенности при спектральном анализе совпадают с признаками дисбаланса ротора, однако силы ее вызывающие существенно меньше, в силу чего на практике гидродинамическая неуравновешенность ротора обнаруживаются крайне редко: только когда ротор отбалансирован с высокой степенью точности. Измеряя фазу вибрации на частоте вращения ротора относительно метки на вале молено определить дефектное место рабочего колеса (лопасть).
В тоже время гидродинамическая неуравновешенность в отличие от механической создает на входе и выходе рабочего колеса периодически пульсирующий с частотой вращения ротора поток (даже при отсутствии кавитации), т.е. спектр огибающей высокочастотной случайной вибрации может содержать составляющую на частоте вращения ротора, а глубина модуляции высокочастотной вибрации может соответствовать общему вкладу гидродинамической неуравновешенности ротора.
Кавитация.
Специфический источник колебаний насоса — кавитация, возникающая при местном понижении давления в тех областях потока где скорость ее достигает максимального значения, т.е. при обтекании тел или в районе ядер вихрей.
Кавитация в насосе может возникнуть по следующим причинам: отличие режимов работы насоса от номинального, особенно когда усиливается влияние вихреобразования; флуктуации скоростей потока; дефекты изготовления лопастей и монтажа рабочего колес, износ лопастей и др.
По мере развития процесса, различают четыре стадии кавитации: газовую фазу, парогазовую фазу, паровую фазу и срывную фазу.
В начальной стадии кавитация обычно возникает в области рабочего колеса, затем распространяется на всасывающий патрубок и в развитом режиме может появиться в области кромок нагнетающего патрубка. На практике наиболее часто встречается газовая фаза кавитации.
• Нарушения гидро и газодинамики потока и пульсации давления • 12 — 12•


Рис. 12—08. Форма и спектр сигнала вибрации передней подшипниковой опоры насоса в горизонтально—поперечном направлении (точка РIН).
Приведенные выше факты (преобладающая вибрация на частоте вращения ротора в горизонтально — поперечном направлении, вибрация на лопастных частотах и боковых частотах вокруг них, вибрация на частотах дефектов колец подшипников и боковые частоты вокруг них, характер кривой виброскорости) свидетельствовали в пользу эксплуатационного износа рабочего колеса и подшипников качения. В процессе обследования проточной части насоса на кромках лопастей рабочего колеса были обнаружены выбоины, а сами лопасти имели неравную толщину, поверхность лопастей имела следы локального износа (раковины), подшипники качения имели развитые дефекты колец.
Как говорилось выше, наличие входного и выходного лопаточного аппарата может приводить к появлению в сигнале вибрации составляющих не только на лопаточной частоте (и ее гармониках), но и на лопаточной частоте входного kZи fг
• Нарушения гидро и газодинамики потока и пульсации давления • 12 — 10 •
виброскорости 1 мм/с на частоте 1 Гц соответствует размаху виброперемещения 450 мкм, что может превышать зазор в уплотнениях и приводить к их ускоренному фрикционному износу.
В разделе "Кавитация" текущей главы помещен спектр огибающей высокочастотой вибрации, измеренный на этом агрегате.

Рис. 12—07. Спектры виброскорости подшипниковых опор насоса.
Разброс гидродинамических (газодинамических) характеристик лопастей, выражающийся в нарушении расчетной формы лопаток может приводить к вибрации на лопастной частоте и появлении вокруг нее боковых частотных составляющих fл±kfг , При динамическом эксцентриситете рабочего колеса относительно языка или направляющего аппарата на входе или выходе (в основном, при очень малых значениях зазора) также появляется амплитудная модуляция вибрации на лопастной частоте с боковыми частотными
• Нарушения гидро и газодинамики потока и пульсации давления • 12 — 8 •
Если имеются направляющие лопатки на выходе рабочего колеса, то приведенное выше выражение принимает вид :

где ZИ — число неподвижных направляющих лопаток.
Если имеются лопатки на входе рабочего колеса, то возможно также появление вибрации на лопаточной частоте (и ее гармониках) входного лопаточного аппарата kZиfr и/или на суммарных и разностных частотах,
например, kfл±mfи (fи = Zиfr ; k , m - натуральные числа), а также других частотах.
Могут быть два типа источников лопастных колебаний, действующих с основной лопастной частотой: нестационарный возбуждающий момент и пульсация давления газа или жидкости. При проходе лопаток мимо языка возникает пульсация давления, воздействующая на стенки корпуса и вызывающая их колебания на лопастных частотах. При этом могут возникать также крутильные колебания корпуса под действием нестационарного крутящего момента. Динамические силы могут иметь радиальное и осевое направление.
Уровень вибрации механизмов на лопастной частоте и ее гармониках зависит от окружной скорости рабочего колеса и расстояния от внешней кромки лопастей до языка. Увеличение расстояния относительно номинального в два раза снижает уровень вибрации на 4...6 дБ, однако с ростом зазора падает производительность. Вибрация на лопастной частоте пропорциональна второй — третьей степени частоты вращения (в зависимости от конструктивных особенностей). В настоящее время отсутствуют достаточно простые выражения расчета пульсации давления на лопастных частотах, что связано с их сильной зависимостью от множества конструктивных параметров. Но можно сказать, что вибрация выше у механизмов с рабочими колесами, имеющими параллельные торцевые поверхности рабочих колес относительно языка спирального отвода.
Неоднородности потока в проточной части могут вызывать несоблюдение расчетных (нормативных) технологических режимов эксплуатации центробежных агрегатов, нарушение технологии изготовления и сборки деталей проточной части (разброс гидродинамических характеристик лопастей, статический и динамический эксцентриситеты между рабочим колесом и корпусом и др.) и эксплуатационный износ деталей проточной части (в основном лопастей рабочих колес).
Статистические данные показывают (см. гл. "Методология нормирования вибрации и распознавания технического состояния оборудования"), что при отсутствии дефектов изготовления, монтажа, эксплуатационного износа и соблюдении номинальных (оптимальных) технологических режимов эксплуатации вибрация на лопаточных частотах центробежных агрегатов в основном не определяет уровень вибрации агрегата и в спектре виброскорости редко является преобладающей.
При несоблюдении номинальных (оптимальных, расчетных) технологических режимов эксплуатации насосов, например, работе в области малых подач, часто возникает неоднородность потока, которая может сопровождаться начальной ("мягкой") формой кавитации. В этом случае типично присутствующая вибрация на лопастной частоте (иногда при этом появляется вибрация на боковых частотных составляющих) может значительно превосходить вибрацию на частоте вращения ротора. Иногда могут появляться колебания в инфразвуковой области спектра.
• Нарушения гидро и газодинамики потока и пульсации давления • 12 — 6 •
случайной вибрации и вибрации на лопастной частоте. При этом силы возбуждения и вызываемая ими вибрация как правило невелики.
На рис. 12 — 04 приведены спектры вибрации подшипниковых щитов ЭД и опор вентилятора в горизонтально — поперечном направлении (графики приведены снизу вверх по мере приближения к корпусу вентилятора).

Рис. 12—05. Спектры виброускорений заднего подшипника ЭД, заднего подшипника вентилятора и корпуса вентилятора в районе выходного патрубка в горизонтально—поперечном направлении.
На графиках спектров индексом fr помечена частота вращения ротора, индексом fm — резонансная частота основания, индексом 2fЛ — вторая гармоника лопастной частоты, а наклонными стрелками — области широкополосной случайной вибрации свыше 500 Гц. По мере удаления от контрольных точек от вентилятора вибрация в этой области затухает. В тоже время, появление
• Нарушения гидро и газодинамики потока и пульсации давления • 12 — 4•
и корпусе вентилятора и достигает максимальных значений в осевом направлении. СКЗ виброскорости превышает 36 мм/с (передний подшипниковый щит ЭД в осевом направлении, точка А02) и превосходит предельно допустимое значение вибрации для эксплуатации такого типа вентиляторов примерно в 5 раз.
На рис.12 —03 приведены форма и спектр сигнала вибрации контрольной точки А02 (передний подшипник ЭД в поперечно — осевом направлении) с максимальным значением вибрации.
СКЗ виброскорости на частоте вращения ротора (24,1 Гц), помеченной на графике спектра индексом fr , составляет примерно 5 мм/с. В низкочастотной области спектра присутствует составляющая на частоте 16,14 Гц, помеченная индексом fm , значение которой составляет приблизительно 36 мм/с (примерно в 7 раз превышает вибрацию на частоте вращения ротора). Наблюдаются татке высшие гармоники этой частотной составляющей и частоты вращения ротора, их значения сравнительно малы.

Рис. 12—03. Форма и спектр сигнала виброскорости в контрольной точке А02 (передний подшипник ЭД в осевом направлении).
На осциллограмме вибросигнала вертикальными линиями помечены временные интервалы, соответствующие одному обороту ротора. Пиковое значение виброскорости достигает 64 мм/с. Форма кривой вибрации и амплитуда нестабильны, пиковое значение флуктуирует в интервале от 64 до 45 мм/с (изменения до 30%).
Сравнение уровней вибрации по направлениям измерения на различных подшипниках агрегата (например, в контрольной точке 02 вибрация в осевом направлении превышает вибрацию в горизонтально— поперечном и вертикальном направлениях более, чем в 6 раз) и наличие характерных признаков нарушений жесткости системы на форме сигнала вибрации свидетельствовали в пользу
• Нарушения гидро и газодинамики потока и пульсации давления • 12 — 2 •
скорости потока. Вибрация в спектре пульсаций имеет вид случайной и проявляется в широкой полосе частот с приблизительно постоянным уровнем до 1000 ... 2000 Гц и дальнейшим снижением при возрастании частоты на 6...12 дБ на октаву.
Пульсации давления в подавляющем большинстве случаев не определяют уровень вибрации агрегата, достаточно малы и сами по себе неопасны. Однако они, несмотря на малую величину, во многих случаях возбуждают резонансные колебания корпусов, трубных обвязок и крепежных систем агрегата.
Турбулентность движущегося потока.
Турбулентность движущегося потока — основной источник вибрации прямых трубопроводов постоянного сечения прямоугольной или круглой формы, длина которых много больше диаметра. Как и пульсации давления в потоке, турбулентные пульсации давления в пристеночном слое обычно невелики и не определяют уровень вибрации механизмов.
Пульсации давления в пристеночном слое передаются на стенки трубопровода, и возникающая вибрация при этом зависит от плотностей стенок трубы и среды, от скоростей звука в среде и трубе, от толщины стенки трубы и ее радиуса и, наконец, от величины пульсаций давления (квадрата скорости потока).
Вихреобразование в потоке.
При изменении сечения трубопровода, поворотах труб, прохождении потоком распределительной и регулирующей арматуры, на кромках лопастей, входных и выходных патрубков в движущемся потоке возникают вихри, приводящие к случайным пульсациям давления, вызывающим колебания корпусов, труб (обтекаемых препятствий) и рабочих лопаток. Интенсивность пульсаций давления при вихреобразовании и неизменных характеристиках перекачиваемой среды зависит от коэффициента сопротивления препятствия и куба скорости потока, а также некоторых других, в том числе конструктивных и эксплуатационных параметров.
Известно, что при изгибах труб и локальных препятствиях пульсация давления ниже, чем на линейных участках. Однако при движении рабочих лопаток относительно перекачиваемой среды ситуация существенно меняется. Кроме того при вихреобразовании источник пульсаций давления можно считать определенной точкой пространства, от которой идет шум и вибрация, в отличие от турбулентности потока, при которой источник колебаний, хоть и более интенсивный, но случайный в пространственном отношении.
В качестве примера резонансных колебаний агрегата, вызванных пульсациями давления при турбулентности потока и вихреобразовании в проточной части центробежного агрегата можно привести изложенный ниже. Воздушный вентилятор французского производства, с консольным ротором и выносными подшипниками качения, приводимый асинхронным ЭД мощностью 450 кВт, обычно работал с частотой вращения ротора 24,1 Гц при номинальной нагрузке, и к моменту измерений находился в эксплуатации 8 лет. В результате естественного износа за год до приведенных в примере данных измерения вибрации вышло из строя "фирменное" рабочее колесо вентилятора и было заменено на колесо собственного заводского изготовления со спрямленными лопатками. Количество лопаток — 9. Корпус вентилятора и основание агрегата выполнены из листовой стали, имеющей ребра жесткости и соединен в общую несущую конструкцию общей высотой до 4 м. По окончании ремонтных работ (в т.ч. замены рабочего колеса) и выводе агрегата из ремонта была обнаружена вибрация, многократно превышающая допустимые значения (до 30 ... 40 мм/с). Впоследствии межремонтный период резко сократился: с интервалом в несколько месяцев, стали выходить из строя подшипники качения вентилятора и двигателя.
• Дефекты зубчатых передач • 11 – 14•

Рис. 11—08. Форма и спектр сигнала вибрации и спектры частотной модуляции первой гармоники зубцовой частоты для нормального (преддефектного) и дефектного состояний при заедании зубчатых колес.
Таким образом, применяя этот метод молено диагностировать заедание на ранней стадии развития.
• Дефекты зубчатых передач • 11 – 12•

Рис. 11—07. Форма и спектр сигнала вибрации редуктора при поломке зуба одного из зубчатых колес.
Приведенные в этом примере вибросигналы измерены на редукторе клети прокатного механизма, имеющей зубчатую пару с прямозубой передачей. При ревизии зубчатого зацепления клети был обнаружен износ подшипников скольжения и зубчатой пары, нарушение соосности валов и разрушение зуба одного из колес.
Частота вращения колес примерно 8, 2 Гц, колеса имеют по 21 зубу. Зубцовая частота (fz) составляет примерно 172 Гц, т.е. зубья входят в контакт примерно через каждые 122 мс.
Вертикальными стрелками на кривой сигнала вибрации (рис. 11—07) помечены следующие один раз за оборот зубчатого колеса (каждые 122 мс) ударные импульсы, величина некоторых из них превышает 13 мм/с. Коэффициент пика достигает 4,7.
Спектр вибрации имеет все диагностические признаки, присущие эксплуатационному износу зубьев: гармонические составляющие частоты
• Дефекты зубчатых передач • 11 - 10 •

Рис. 11—05. Спектр вибрации (с фрагментами) мультипликатора с развитым питтингом контактирующих поверхностей зубчатых колес.
Как говорилось ранее, определить и разграничить по спектру появление различных видов повреждений, особенно на ранней стадии развития, бывает очень сложно. Более эффективен метод, основанный на анализе амплитудной огибающей узкополосного вибросигнала в области зубцовой частоты вибрации зубчатого зацепления и ее гармоник или, иногда, "промежуточных" частот. В качестве диагностических параметров питтинга молено использовать уровни спектральных составляющих на комбинационных (модуляционных) частотах.
• Дефекты зубчатых передач • 11 – 8 •

Рис. 11—03. Спектр вибрации (с фрагментом) редуктора в горизонтально—поперечном направлении при равномерном абразивом износе зубчатых колес.
Спектр вибрации имеет частотные составляющие, характерные для износа колес: в результате увеличения (относительно номинального значения) бокового зазора происходит отрыв профилей зубьев в зацеплении и ударный режим возбуждения вибрации, что вызывает появление спектральных составляющих кратных частоте зацепления зубьев 744, 1488, 2232, 2976, 3720 и 4464 Гц (kfz). В спектре присутствует также "промежуточная" составляющая на частоте 485 Гц. На расширенном фрагменте спектра (нижний спектр) отчетливо наблюдаются гармоники частоты вращения ротора быстроходного колеса, причем не имеется тенденции убывания амплитуд с возрастанием номера гармоники.
Рост общего уровня спектральных составляющих вибрации имеется практически во всем диапазоне частот спектра. Общее увеличение уровня спектра, особенно его высокочастотной области, определяющее степень развития износа
• Дефекты зубчатых передач • 11—6 •
колеса примерно 24,6 Гц и быстроходного колеса примерно 197,5 Гц. Монтаж был выполнен с нарушением соосности валов, вызвавшей перекос осей зубчатых колес.
Измерения проводились со стороны тихоходного (индекс 0) и быстроходного (индекс I) колес в вертикальном (индекс V) и горизонтально — осевом (индекс А) направлениях.
В принципе, нарушение соосности валов зубчатых колес имеет те же диагностические признаки, что и расцентровка валов узлов агрегата, с той лишь разницей что в сигнале вибрации могут присутствовать гармонические составляющие частот вращения обоих валов расцентрованных колес.
В приведенном примере практически на всех спектрах вибрации наблюдаются частотные составляющие, характерные для нарушений соосности (перекоса осей валов) — составляющие на оборотной частоте и гармониках обоих колес kfг1 и kfr2 , причем, в большинстве случаев, существенно преобладают первая и/или вторая гармоники. В качестве диагностических параметров можно использовать уровни амплитуд вибрации на первой и второй гармониках частоты вращения обоих колес.
При нарушениях соосности количественные характеристики частотных составляющих (для различных точек измерения и пространственных компонентов вибрации) могут отличаться в значительных пределах в зависимости от взаимного положения осей валов, как и при нарушении центровки узлов агрегата. Кроме того они зависят от множества других параметров, связанных с нагрузкой, характеристикой смазки и т.д.
В качестве дополнительного диагностического признака нарушения соосности валов колес можно рассматривать изменение величин частотных составляющих kfг1 и kfr2 при пуске холодного агрегата и его дальнейшей работе при неизменной нагрузке. В процессе прогрева колес величины этих составляющих могут непрерывно меняться в течение сравнительно короткого (до двух часов) промежутка времени в значительных пределах, после чего вибрация стабилизируется.
На рис. 11— 02 приведен спектр вибрации мультипликатора с прямозубой зубчатой передачей, состоящей из двух колес, установленного между ЭД и компрессором компрессорного агрегата, с частотой вращения тихоходного колеса примерно 24,6 Гц (fr1) и быстроходного колеса примерно 195,5 Гц (fr2). Монтаж был проведен с нарушением установки бокового зазора (превышено номинальное значение бокового зазора).
В принципе, нарушение (превышение) бокового зазора имеет те же диагностические признаки, что нарушения жесткости, с той лишь разницей, что в сигнале вибрации могут присутствовать гармонические составляющие частот вращения обоих валов.
Спектр вибрации имеет частотные составляющие, характерные для нарушений жесткости — составляющие на оборотной частоте и ее гармониках обоих колес mfг1 и nfr2 , причем, в большинстве случаев, наблюдаются достаточная интенсивность гармоник с номерами до 20 и более. При нарушениях бокового зазора величины частотных составляющих (для различных мест и направлений измерения вибрации) и их соотношения между собой могут отличаться и зависят от тех же параметров, что и нарушения жесткости.
В приведенном спектре вибрации вертикальными стрелками помечены гармоники частоты вращения ротора быстроходного колеса и наклонными стрелками — гармоники тихоходного колеса. Гармоническая активность велика: например, интенсивность гармонических составляющих частоты вращения ротора тихоходного колеса в области 50...80 —й гармоник не ниже, чем в области 2...20 - й.
• Дефекты зубчатых передач • 11—4•
входит в зацепление преждевременно, и момент входа сопровождается ударом. Амплитуда ударного импульса пропорциональна степени развития дефекта (трещины или излома). Частота заполнения импульса, вероятнее всего, — собственная частота зубчатого элемента. Таким образом, рассматривая форму сигнала передачи с подобным дефектом иногда возможно обнаружить следующие раз за оборот ударные импульсы, подчеркивающиеся при синхронном накоплении. Частоты основных составляющих вибрации при дефектах зубчатых передач.
Таблица 11- 1.
Частота |
Вид дефекта изготовления |
Вид дефекта сборки |
Вид дефекта износа |
fr |
Дисбаланс |
||
kf
г1 и kf г2 k= 1,2 реже 3 и 4 mfz±nfr k, n, m = 1, 2… |
Переменная погрешность шага зацепления |
Нарушение соосности (перекос валов) |
|
kfr k = 1, 2…20 и выше |
Повышенный боковой зазор между колесами |
||
fz |
Постоянная погрешность шага зацепления |
||
kfz kfr рост шумового компонента mfm±nfr ; n = 0,1,2, ... |
Абразивный износ |
||
kfr mfz±nfr mfm±nfr (флуктуация амплитуд), n = 0,1,2, ... |
Выкрашивание зубьев |
||
kfr mfz±nfr mfm±nfr (флуктуация амплитуд), n = 0,1,2, ... рост шумовой компоненты |
Трещины и/или излом зубьев |
При заедании происходит молекулярное соединение контактирующих поверхностей зубьев под действием высокого давления при разрыве масляной пленки. В результате возникает адгезионный износ, происходящий в несколько этапов: начальной фазы и натира (характеризующихся схватыванием и разрушением локальных участков контактирующих поверхностей зубьев) и прогрессирующего этапа, завершающегося заеданием с пластическими деформациями (часто имеющего скоротечный экспоненциальный вид).
Заедание зубчатых колес обычно сопровождается изменением амплитуд гармоник зубцовой частоты kfz, ростом амплитуд комбинационных частот mfz±nfr , флуктуациями амплитуд "промежуточных" частот, расширением полосы спектральных компонентов kfz и нерегулярными выбросами во временном сигнале. Важно, что вышеперечисленные признаки, присущие и другим дефектам, крайне усложняют процесс диагностики с помощью спектрального анализа вибрации и не позволяют однозначно установить заедание, особенно на начальной стадии.
• Дефекты зубчатых передач • 11 — 2 •
первопричинами возникновения этих частотных составляющих являются собственные частоты зубчатых элементов, и, весьма вероятно, что они являются результатом резонансного возбуждения, например, при виброударных процессах в зацеплении. В ряде случаев мониторинг амплитуд "промежуточных" частотных составляющих может служить весьма чувствительным первичным индикатором зарождения различных дефектов в зубчатой передаче. В то же время амплитуды "промежуточных" частотных составляющих очень чувствительны к изменениям условий работы агрегата, особенно нагрузки агрегата, причем реакция увеличения вибрации на увеличение нагрузки может быть нелинейной и неповторяющейся по величине. В связи с этим использование амплитуд "промежуточных" частот в качестве параметра для оценки состояния и остаточного ресурса зубчатой передачи может оказаться труднореализуемым.
Ошибка зубонарезания каждого из колес зубчатой пары приводит к вибрации, связанной с числом зубьев делительного колеса зубонарезного станка:

где zg — число зубьев делительного колеса зубонарезного станка, k = 1, 2, ...
Обычно в спектре вибрации зубчатой передачи содержится шумовой компонент, дисперсия которого меняется с наработкой в соответствии с развитием локального износа, т.е. уменьшается в процессе приработки колес, практически неизменна при нормальной работе в достаточно длительном интервале времени и растет по экспоненте в процессе интенсивного износа. Шумовой компонент в спектре вибрации может иметь вид белого шума, который накладываясь на дискретные собственные частоты деталей зубчатой передачи может вызывать резонанс и появление новых спектральных составляющих. К этому же может приводить, например, возникновение параметрического резонанса в прямозубых передачах, при появлении отрывных виброударных колебательных режимов.
Эксплуатационные дефекты зубчатой передачи условно можно разделить на следующие виды: абразивный износ зубчатого зацепления, выкрашивание зубьев (питтинг) зубчатых колес, трещины и излом зубьев зубчатых колес и заедание зубчатых колес.
Поскольку они являются возмущающими факторами, свойства вибросигнала (форма сигнала и спектр вибрации, в т.ч. особенно спектр огибающей, кепстр и др.) при их наличии всегда меняются. В частности, в спектре могут меняться соотношения между основными частотами возбуждения, появляться новые спектральные составляющие, значительно изменяется уровень шумового компонента. На кривой сигнала вибрации могут появляться ударные импульсы и изменяться соотношение между периодическим и шумовым компонентами. В то же время следует учитывать, что существенные изменения формы и спектра сигнала вибрации в основном наблюдаются при развитых повреждениях. На ранней стадии развития дефектов целесообразно использовать другие методы анализа виброакустического сигнала, такие как кепстральный анализ, анализ спектра узкополосной огибающей и др.
Абразивный износ зубчатого зацепления.
Обычно при выборке материала поверхности зубьев колес нарушается микро и макрогеометрия контактирующих зубьев. Это приводит к увеличению трения и росту шумового компонента.
Абразивный износ вызывает увеличение бокового зазора, что может приводить к отрыву профилей зубьев в зацеплении и ударному режиму возбуждения вибрации. Ударный режим возбуждения достаточно часто приводит к росту спектральных составляющих гармонического ряда частот, кратных частоте зацепления зубьев (kfz), появлению "промежуточных" частотных составляющих (fm) и перераспределению энергии в сторону высокочастотных составляющих. На
• Вибрация электрических машин электромагнитного происхождения • 10—19 •
Средний спектр (рис. 10—11) измерен на задней подшипниковой опоре ЭД в вертикальном направлении практически непосредственно после пуска агрегата и ввода его на номинальный режим работы (точка МОV, время 9.38).
Верхний спектр измерен в той же точке спустя 6 часов работы агрегата после установления стабильного теплового режима (точка МОV, время 15.40).
Нижний спектр — тангенциальная вибрация статора (точка МSН) при стабильном тепловом режиме.
На опоре наблюдается рост вибрации на частоте вращения ротора, связанный с развитием теплового прогиба ротора (частотные составляющие помечены горизонтальными стрелками). Наклонными стрелками помечены 1 — я и 2-я гармоники вибрации с частотой 6kfr. Для тангенциальной вибрации характерны составляющие с частотами 6kfr , среди которых преобладает первая гармоника. Поскольку условия эксплуатации предприятия допускали включение другой машины, наиболее простым способом подтверждения подозрений о магнитной несимметрии (витковых замыканиях в роторе) стала запись вибрации подшипника и статора при останове агрегата на холостом ходу.
На рис. 10—12 приведена осциллограмма тангенциальной вибрации статора электродвигателя (точка МSН) в процессе отключения питания и выбеге. Наклонными стрелками помечено изменение вибрации в момент отключения питания. Вибрация скачкообразно уменьшилась примерно в три раза. Сумма фактов свидетельствует в пользу витковых замыканий в роторе, приводящих к тепловой нестабильности.

Рис. 10—12. Осциллограмма тангенциальной вибрации статора синхронной машины при замыкании, между витками обмотки ротора в процессе отключения питания и выбеге.
Для выявления дефектов ротора были проведены измерения сопротивления обмоток, а последовавший за исследованиями ремонт ЭД полностью подтвердил сделанное заключение.
• Вибрация электрических машин электромагнитного происхождения • 10—17•

Рис. 10—10. Спектры и кепстры сигнала вибрации однотипных АЭД с равномерным зазором и при эксцентриситете ротора (с частотой вращения 49,86 Гц).
Замыкание между витками обмотки ротора в синхронных машинах может произойти в результате воздействия влаги, грязи при монтаже (укладке) и при перемещении обмотки в пазу. При этом возможно возникновение несимметрии магнитопровода и высокого локального нагрева, который, в свою очередь, может дополнительно привести к нарушению изоляции корпуса и изоляции меди обмотки.
• Вибрация электрических машин электромагнитного происхождения • 10—15 •
приводит к значительному возрастанию компонентов вибрации с частотой 2fс под воздействием пульсирующего крутильного момента. Это воздействие проявляется в возрастании уровня вибрации, связанной с этим дефектом, на указанной частоте как для радиальной, так и для осевой составляющих. В качестве диагностического признака наиболее удобно использовать характеристики тангенциальных колебаний статора с той же частотой, которые мало зависят от нагрузки. Поскольку к таким же колебаниям приводят несимметрия напряжений питающей сети и наличие короткозамкнутых витков в обмотках активной стали, для выявления рассматриваемого дефекта необходимо удостовериться в симметричности фазных параметров сети. Устранению причин должна предшествовать их конкретизация, а именно: измерение и сравнение параметров питающей сети; измерение и сравнение сопротивления обмотки статора, а та:кже проверка правильности подключения обмоток (для случая диагностики после ремонта статора).
В качестве параметра при оценке степени развития электрической несимметрии можно использовать отношение амплитуд тангенциальной и радиальной вибрации на частоте 2fС. При этом для разделения механической и электрической вибрации для АЭД следует применять достаточно высокое разрешение по частоте. Выбирая контрольные точки, следует учитывать, что в АЭД из —за несовпадения осей инерции ротора и статора их колебания отличаются по форме, приводя к появлению в колебаниях статора радиальной составляющей при тангенциальных колебаниях ротора, и наоборот.
В качестве примера молено привести данные измерения вибрации, измеренные на АЭД, имевшем недопустимую несимметрию сопротивления обмоток постоянному току. Спектры и формы сигналов вибрации приведены на рис. 10-02 и рис. 10-03.
Несимметрия магнитных цепей электрических машин.
На этапе проектирования распределение магнитного потока по цепям электрической машины строится пространственно симметричным. Однако при изготовлении, сборке и эксплуатации машины симметрия магнитных цепей может нарушаться из —за нарушений технологии изготовления и сборки деталей и узлов, анизотропии магнитных материалов, нарушений технологических зазоров в стыках и сочленениях, износе и других причин.
Далее при высоком технологическом уровне изготовления машины магнитные силы могут вызывать деформацию статора АЭД и неравномерность зазора, приводя к магнитной несимметрии.
Из причин, вызывающих магнитную несимметрию, наиболее часто встречающиеся: неравномерность воздушного зазора и витковые замыкания. Другие причины — насыщение отдельных участков магнитопровода, двойное замыкание на землю и др.
Неравномерность воздушного зазора в большинстве случаев возникает из-за неточности изготовления и сборки машины и эксплуатационных износов вала и/или подшипникового узла. Смещение оси вала относительно оси статора (при совпадении осей вращения и симметрии ротора и отклонение от этой оси симметрии статора) вызывает статический эксцентриситет, который может появиться, например, при неправильной проточке статора или сборке двигателя, а также при деформации статора при нагревании. Смещение оси ротора от оси пакета стали (совпадении оси симметрии статора с осью вращения и отклонении от этой общей оси линии симметрии внешней поверхности ротора) вызывает динамический эксцентриситет, который может возникнуть при эксцентричном расположении пакета ротора относительно оси, неточной установки прокладок под сердечником полюсов, при смещении отверстия вала в сердечнике ротора.
Эксцентриситет зазора приводит к появлению радиальных сил (магнитной вибрации), что более характерно для асинхронных электрических машин
• Вибрация электрических машин электромагнитного происхождения • 10 — 13 •
являющуюся 28 гармоникой частоты вращения ротора (23,69 Гц) и боковые частоты (помечены горизонтальными стрелками). Боковые частотные составляющие размещены с интервалом 99,98 Гц, что соответствует удвоенной частоте сети. Поскольку число пазов (стержней) ротора составляет 28, вероятно вибрация на пазовой частоте говорит о несимметрии токов ротора и дефектах стержней и/или ослаблениях стержней и пазовой изоляции ротора. Возможна также магнитная несимметрия АЭД.
Характер тангенциальной вибрации статора ЭД говорит о высокой вероятности электрической несимметрии, поскольку для магнитной несимметрии тангенциальная вибрация нехарактерна.
Уточнение диагноза можно сделать либо применением токовых клещей, либо при обследовании остановленного агрегата.
На рис. 10 — 09 приведены токовые спектры одной из фаз этого же АЭД на холостом ходу и при номинальной нагрузке.
На спектре помечены преобладающий токовый компонент на частоте сети 49,98 Гц (fс) , боковые частотные составляющие 34,38, 39,58, 44,78, 55,18 и 60,38 Гц (стрелками и индексом fc1 ) и частота вращения ротора 23,69 Гц (fr), а остальные непомеченные составляющие (свыше 10 Гц) также являются комбинационными частотными составляющими.
Интенсивность токов на боковых (модуляционных) частотных составляющих и их отношение к величине токового компонента на частоте сети в токовом спектре АЭД с электрическими дефектами сильно зависит от нагрузки.
Наиболее важные частотные составляющие токового спектра — составляющая на частоте сети и ближняя к ней боковая частотная составляющая слева (fС1), частота которой определяется по формуле:

где Р — число полюсов.
В качестве критерия при оценке степени развития дефектов можно использовать отношение величин токов на частотах fС1 и fс , если нагрузка АЭД составляет не менее 90% от номинальной.
В частности, если разница между величинами токов на частотных составляющих спектра fС1 и fС составляет более чем 55 дБ, то с большой вероятностью можно утверждать, что в роторе отсутствуют стержни с дефектами.
Если эта разница менее 46 дБ, вероятность наличия поврежденных стержней очень высока.
Если разница величин составляющих fС1 и fC. лежит в интервале от 55 до 46 дБ однозначного вывода о наличии или отсутствии повреждений сделать нельзя.
Приближенно число дефектных стержней ротора АЭД можно оценить, по формулам:

где: N — предполагаемое число поврежденных стержней в роторе АЭД; zr — число пазов в роторе АЭД; Ifc — сила тока на частоте сети в амперах; 1fс1 — сила тока на боковой частотной составляющей fс1 в амперах; LIfc — сила тока на частоте сети в дБ; LIfс1 — сила тока на боковой частотной составляющей fс1 в дБ; Р — число полюсов АЭД.
• Вибрация электрических машин электромагнитного происхождения • 10—11 •
индуцированию тока в обмотке статора на гармониках частоты сети и ее гармониках nfС и достаточно заметной вибрации на частоте сети, что говорит о наличии развивающегося дефекта. В тоже время появление вибрации на удвоенной частоте сети может говорить о наличии электрической несимметрии статора АЭД. Уточнение диагноза можно сделать либо применением токовых клещей, либо при обследовании остановленного агрегата и измерении характеристик его цепей.

Рис. 10—07. Фрагмент спектра виброскорости, асинхронного ЭД с частотой вращения ротора 49,56 Гц (одной парой полюсов), полученный с заднего подшипника в вертикальном направлении. Спектр вибрации в полосе частот 0...400 Гц содержит 3200 линий.
Следует добавить, что если имеется модуляция и/или биения, период которых может составлять несколько секунд и значительно превышать временную длительность временной реализации измерения, для повышения достоверности распознавания технического состояния оборудования следует не только оптимизировать длительность временной реализации и спектральное разрешение, но и по возможности увеличивать количество усреднений спектров при проведении вибромониторинга.
• Вибрация электрических машин электромагнитного происхождения • 10 — 9 •
частоте вращения ротора, то налицо значительная электрическая несимметрия ротора, говорящая о развитом дефекте.

Рис. 10—05. Фрагмент спектра вибрации при линейном, и логарифмическом масштабе оси амплитуд асинхронного ЭД с частотой вращения ротора 49,38 Гц (одна пара полюсов), измеренный на переднем подшипнике в горизонтально—поперечном направлении. Спектр вибрации в полосе частот 0...600 Гц содержит 3200 линий.
На нижнем спектре (рис. 10 — 05), ось амплитуд которого для удобства приведена в логарифмическом масштабе, молено наблюдать составляющую на боковой частоте fr + 2s , помеченную цифрой 2, рядом с преобладающей
• Вибрация электрических машин электромагнитного происхождения • 10 — 7 •
Несимметрия электрических цепей (ротора и/или статора) машины.
Несимметрия электрических цепей машин ( в основном дефекты изготовления) вызывается неравномерным распределением сопротивления обмоток по фазам, катушкам обмоток возбуждения и секциям якорных обмоток, приводящие к несимметрии фазных токов.
Несимметрия электрических цепей ротора АЭД.
Электрическая несимметрия ротора АЭД (обрыв стержня, растрескивание стержня, повышение электрического сопротивления в месте его соединения с короткозамыкающим кольцом) — дефект, занимающий второе место после подшипников в ряду причин, приводящих к отказу АЭД. Обнаружение электрической несимметрии ротора возможно на ранней стадии развития.
В большинстве случаев пусковые токи, хотя и кратковременные, текущие в цепях АЭД (особенно при пуске под нагрузкой), многократно превосходят номинальные и приводят к высоким напряжениям в стержнях ротора, вследствие чего возникновение дефектов стержней ротора по достижении критического числа пусков АЭД неизбежно. Локальный нагрев ротора в месте дефекта мелеет приводить к деформации ротора и появлению теплового дисбаланса (в таких случаях нередко ошибочно проводят постоянную подбалансировку ротора, не разбираясь в действительной природе дефекта). На определенной стадии развития дефект стержня в итоге может приводить к образованию дуги, вызывающей дополнительный нагрев и деформацию ротора. При нагреве ротора изменение его линейных размеров, в частности длины, может вызывать избыточную осевую нагрузку на подшипники (качения): их перегрев и преждевременный выход из строя. Помимо этого, радиальное расширение и изгиб ротора иногда приводят к задеваниям (особенно при работе АЭД под нагрузкой). Поскольку через соседние с поврежденным стержни течет больший электрический ток, превышающий номинальный, подвергающий их дополнительным механическим и тепловым нагрузкам, ускоренный выход их из строя неизбежен.
В результате этого процесса возможно появление остаточных тепловых деформаций и выбраковка ротора.
При электрической несимметрии ротора АЭД в его полном моменте присутствует пульсирующая составляющая 2sfс. Однако эта составляющая имеет достаточно низкую частоту (единицы Гц), и вибрация АЭД на частоте 2nsfс проявляется слабо и практически трудно обнаруживаема. В то же время угловые колебания ротора под действием пульсирующего момента приводят к достаточно заметной угловой модуляции частоты вращения ротора, легко обнаруживаемой при анализе формы вибросигнала. Угловая модуляция частоты вращения ротора АЭД приводит к появлению в спектре вибрации вокруг частоты вращения ротора и ее гармоник (kfr ) заметных боковых составляющих kfr ±2ns .
Изменения в распределениях токов, текущих в цепях АЭД при поврежденном стержне, в итоге приводят к индуцированию тока в обмотке статора на гармониках частоты сети nfс. Иногда наблюдается заметная вибрация на пазовой частоте ротора zrfr с боковыми составляющими удвоенной частоты сети вокруг нее zrfr±2fc , реже проявляется вибрация на частотах kzrfr±2nfc.
Характер и значения вибрации при дефектах стержней ротора, особенно развитых, зависят от токов, протекающих в цепях ротора, т.е. от нагрузки.
Поскольку при увеличении нагрузки АЭД скольжение увеличивается, можно утверждать в этом случае: чем ниже частота вращения ротора относительно частоты вращающегося поля, тем сильнее изменение характера вибрации.
• Вибрация электрических машин электромагнитного происхождения • 10 — 5 •
Характерные частоты составляющих вибрации, возникающей при различных дефектах электрических машин приведены в таблице 10—1.

Рис.10—03. Формы и спектр сигнала вибрации расцентрованного агрегата, имеющего электромагнитный дефект статора АЭД, при выключении питания и останове агрегата под нагрузкой.
Характерные частоты составляющих вибрации при электромагнитных дефектах электрических машин.
Таблица 10-1.
Частота |
Вид дефекта |
Примечания |
![]() |
Электрическая несимметрия ротора АЭД (обрыв, растрескивание стержня; повышение электрического сопро-тивления в месте его соединения с короткозамыкающим кольцом) |
Угловые колебания ротора под действием пульсирующего момента приводят к значительной угловой модуляции частоты вращения ротора и появлению вокруг нее боковых частотных составляющих ±2ns. Величина вибрации зависит от нагрузки |
• Вибрация электрических машин электромагнитного происхождения • 10 — 3 •
Процессы модуляции колебаний и биения в электрических машинах (в т.ч. если они вызваны электромагнитными дефектами) несут большую информацию о ее техническом состоянии. Наличие этих процессов, определенным образом изменяющих форму сигнала вибрации, приводит к возникновению характерных признаков, во многих случаях легко определяемых визуально.
По форме кривой сигнала вибрации, особенно полигармонической, весьма сложно отличить биения от модуляции, т.е. классифицировать электромагнитные дефекты машины. Однако, в принципе, это и не требуется: уточнение вида неисправности можно провести с применением спектрального и других видов анализа. Обычно в процессе вибромониторинга состояния оборудования при измерении и запоминании данных измерения вибрации ся минимизировать частотное разрешение спектра с целью экономии памяти сборщика данных, памяти дискового накопителя компьютера и ускорения процессов сбора и обработки информации. Это часто приводит к тому, что на графике спектра (например, при модуляции) боковые частоты сливаются с несущей частотной составляющей в одну спектральную линию, что иногда значительно затрудняет распознавание некоторых электрических дефектов. Аналогичная ситуация возникает и при биениях. Часто, особенно если в процессе мониторинга не записываются и не анализируются формы сигналов вибрации, это приводит к тому, что электрические дефекты вовремя на обнаруживаются.

Рис. 10—02. Формы и спектр сигнала биений при вибрации расцентрованного агрегата имеющего электромагнитный дефект статора АЭД. Несущая частота — удвоенная частота вращения ротора АЭД (период Тп), период биений — Тb.
• Вибрация электрических машин электромагнитного происхождения • 10—1 •
Вибрация электрических машин электромагнитного происхождения
Хотя природа вибрации электромагнитного происхождения является общей для машин всех типов (среди которых асинхронные электродвигатели имеют наиболее сложный вид электромагнитного поля), особенности процессов взаимного преобразования электрической и механической энергии и индивидуальные конструктивные особенности как типа, так и каждой конкретной машины могут оказывать существенное влияние на характер ее вибрации.
Вследствие этого диагностические признаки дефектов цепей в различных типах машин могут существенно различаться.
В электрических машинах присутствуют два основных вида сил возбуждения электромагнитного происхождения:
• радиальные силы, возникающие при временных и пространственных изменениях магнитного поля в воздушном зазоре между ротором и статором;
• тангенциальные силы, возникающие при взаимодействии магнитного поля с линейной токовой нагрузкой машины.
Характер этих сил определяется изменением МДС обмоток и магнитной проводимостью воздушного зазора машин, т.е. индукцией магнитного поля и линейной токовой нагрузкой в обмотках машины. При этом электромагнитные силы могут вызывать значительные деформации магнитопровода, возбуждая пространственные колебания статора и изгиб кольца статора, а также изгиб ротора. Источники электромагнитных сил распределены в пространстве и не имеют конкретной точки приложения.
При проектировании электрических машин распределение электрических и магнитных сил и потоков по цепям стремятся создать пространственно симметричным. Их вклад в общую вибрацию машин в исправном состоянии в большинстве случаев невелик.
Основное влияние на характер вибрации оказывают уровни технологии изготовления электрической машины, сборки (ремонта) и особенности
• Дефекты подшипников качения • 9 — 13 •
точки контакта колец с телами качения, часто возникает преобладающая составляющая с частотой 2fr (рис. 9 — 05, позиция 1).

Рис. 9—06. Спектры огибающей высокочастотной вибрации подшипника качения асинхронного ЭД по мере выработки ресурса.
Вследствие нарушений условий транспортировки агрегата или его узлов в сборе может образовываться "наклеп" подшипника, который в начале эксплуатации агрегата сопровождается появлением ударных импульсов с частотой f0 (рис. 9 — 05, позиция 3), причем наличие ударных импульсов вызывает появление в спектре огибающей интенсивных высших гармоник kf0 (рис. 9 — 05, позиция 3).
• Дефекты подшипников качения • 9 — 11 •

Рис. 9—04. Форма и спектр ( с фрагментом) сигнала вибрации подшипника с нарушением смазки ( frol=2,38 fr , fi=8,34 fr , fcg=0,4fr , fo=5,63fr , fr =49,61Гц).
Наиболее существенным недостатком этого метода можно считать высокие потери при распространении вибрации, что требует максимального приближения датчика к подшипнику качения. В качестве диагностического признака весьма удобно использовать амплитудную модуляцию высокочастотной случайной вибрации подшипникового узла, а диагностического параметра — парциальные глубины модуляции случайного сигнала. Опыт показывает, что глубина модуляции случайной вибрации слабо зависит от частоты вращения подшипника и его габаритов, что позволяет устанавливать обобщенные уровни тревог, не зависящие от вида подшипника и агрегата. Установлено также, что чем шире полоса фильтра демодулятора, тем выше чувствительность измерительного тракта при обнаружении модуляции гармоническим сигналом случайного сигнала, спектральная плотность которого постоянна в пределах полосы пропускания фильтра. Из-за резонансов в подшипниковых узлах спектральная плотность сигнала не бывает постоянной в широкой полосе частот, что приводит к появлению ошибок измерения глубин модуляции. Поэтому наиболее целесообразно использовать фильтры с относительно небольшой полосой пропускания, например, треть октавные. Ошибки измерения появляются также когда в полосу пропускания фильтра демодулятора попадают гармонические
• Дефекты подшипников качения • 9 — 9•
кольца. Вибрация на частоте f0 = 7,67fr (приблизительно 380 Гц) практически не наблюдается, поэтому можно предположить, что дефекты внешнего кольца менее развиты. Характерно, что уровень шумов по мере развития дефектов возрастает и в верхнем спектре наибольший. За счет появления высокочастотной вибрации (если сравнивать нижний и верхний спектры) СКЗ виброскорости возросло белее чем в полтора раза, хотя вибрация на преобладающей частоте (частоте вращения ротора) практически не изменилась.
Этот пример показывает, что для повышения достоверности контроля состояния подшипников качения необходимо стараться расширять по мере возможностей частотный диапазон измерений вибрации и анализировать характер вибрации в высокочастотной области спектра.
На рис. 9 — 03. приведены форма сигнала виброскорости и спектр сигнала виброускорения подшипника, имеющего кроме износа, раковин и трещины внутреннего кольца износ остальных деталей, особенно внешнего кольца и шариков. Спектр вибрации подшипника включает составляющие на всех основных частотах возбуждения при работе подшипников, свидетельствующие о наличии дефектов всех деталей подшипника.
Составляющая спектра на частоте fi = 29,51fr (приблизительно 731 Гц) является преобладающей, но имеется весьма значительная вибрация на частоте 1/3f0 (приблизительно 222 Гц).
Поскольку вибросигнал (при сходном развитии дефектов колец) при возбуждении колебаний внутреннего кольца всегда проходит путь до точки измерений больший, чем от внешнего, и, следовательно, затухает сильнее, можно утверждать, что дефект внутреннего кольца развит сильнее. На фрагменте спектра помечены: горизонтальной стрелкой боковая частотная составляющая fi + fr , вертикальной стрелкой боковая частотная составляющая fi + (fr - fcg). Большие значения вибрации на этих частотах, присутствие в спектре частоты возбуждения сепаратора и высокий уровень шумов также говорят о предельном состоянии подшипника.
Кривая виброскорости имеет непериодический, "случайный" характер, амплитуда отдельных импульсов достигает 8 д, а значение коэффициента пика — 3,1.
На рис. 9 — 04. показаны форма и спектр сигнала вибрации подшипника, имевшего нарушение смазки. В приведенном примере произошло старение смазки, выразившееся в практически полном отсутствии нормальной смазки в подшипнике: ее коксовании и появлении твердых частиц. В течение некоторого времени обслуживающий персонал наблюдал рост температуры подшипника, которая к моменту измерения приведенных формы и спектра сигнала вибрации достигла предельно допустимого значения, а также роста общего уровня вибрации.
В спектре вибрации в диапазоне 1000...2000 Гц наблюдается несколько частотных составляющих следующих с интервалом 122,8 Гц. Ни одна из группы этих частотных составляющих не кратна частоте вращения ротора и частотам дефектов подшипника качения ( frol, fi, fcg, fo ).
Кривая вибрации имеет непериодический, "случайный" вид, амплитуда отдельных импульсов достигает 8,2g. Большие значения амплитуды вибрации и коэффициента пика 4,6 говорят об опасности дефекта.
Непосредственно после измерений агрегат был кратковременно остановлен и проведена замена смазки подшипника. После пуска агрегата температура нормализовалась и высокочастотная вибрация полностью исчезла. Следует отметить, что подобные спектры вибрации подшипника при нарушениях смазки встречаются не всегда.
• Дефекты подшипников качения • 9 — 7 •
На рис. 9 — 01. приведена динамика изменения вибрации подшипника за период в 14 месяцев по мере появления износа и дефектов колец.
Усталостное разрушение подшипников проявлялось в виде выкрашивания материала дорожек колец и тел качения. В процессе ремонта агрегата произвели замену подшипников, однако, вызывающий повышенную вибрацию дефект электромагнитного происхождения не был устранен. Это приводило к тепловому расширению ротора и, как следствие, возникновению чрезмерно большой нагрузки на подшипники и их ускоренному выходу их строя.
Нижние форма и спектр сигнала измерены практически после ремонта.Для этого периода характерно отсутствие дефектов подшипников выразившееся в почти периодическом характере кривой виброускорения с невысокой амплитудой, сколько-нибудь заметные ударные импульсы отсутствуют. Спектр виброскорости включает преобладающую составляющую на частоте вращения ротора с высоким значением амплитуды, вызванную неуравновешенностью ротора. Уровень шумов сравнительно низок (случайная вибрация практически отсутствует).
Следующие (снизу —вверх) форма и спектр сигнала получены после года эксплуатации агрегата. Заметны значительные изменения формы сигнала вибрации: кривая вибрации непериодическая, появились ударные импульсы и случайная вибрация. Однако пиковое значение виброускорения пока еще невелико по величине — не превышает 1,5 g . Спектр виброскорости также изменился: появились составляющие на частотах возбуждения внутреннего и наружного колец, существенно повысился уровень шумов.
Этому периоду соответствует появление локальных дефектов на наружном кольце подшипника.
Верхние форма и спектр сигнала измерены перед выводом агрегата в плановый ремонт. Кривая виброускорения имеет непериодический, "случайный вид", амплитуда отдельных импульсов достигает 3,5 g. Спектр виброскорости подшипника включает составляющие с частотой возбуждения внешнего и внутреннего колец. Составляющая спектра с частотой f0 = 8,27fr (приблизительно 411 Гц) выше других. Вертикальными стрелками помечены боковые частотные составляющие f0±kfr . Их достаточно большие (по отношению к f0) значения говорят о значительной степени развития дефектов внешнего кольца. Величина вибрации на частоте fi = 10,73fr (приблизительно 533 Гц) примерно на 20 дБ ниже, чем на частоте f0, поэтому можно предположить, что дефекты внутреннего кольца менее развиты. Об этом же свидетельствуют более низкие значения амплитуд вибрации на боковых частотах fi±kfr (помеченные наклонными стрелками) по отношению к fi .
Этот пример иллюстрирует достаточно высокую чувствительность формы сигнала виброускорения к изменению состояния деталей подшипника качения.
На рис. 9 — 02. приведены форма сигнала виброускорения и спектры сигналов виброскорости подшипника агрегата, первый из которых (нижний спектр) собран после 2,5 лет безремонтной эксплуатации агрегата. Износ подшипника проявлялся в виде выкрашивания материала дорожек колец (кроме других на внутреннем кольце был обнаружен развитый локальный дефект) и тел качения.
Нижний спектр виброскорости содержит составляющие, кратные частоте вращения ротора, вызванные некоторым износом подшипника. Уровень шумов низок, случайная и высокочастотная вибрация сравнительно невелика.
Следующий (снизу —вверх) спектр получены после появления локальных дефектов внутреннего кольца подшипника. Заметны значительные изменения спектра виброскорости: появились высокочастотные составляющие на гармониках частоты возбуждения (и боковых частотах) внутреннего кольца, существенно повысился уровень шумов.
Верхние форма и спектр сигнала измерены перед выводом агрегата в ремонт. Кривая вибрации имеет непериодический, случайный вид, амплитуда отдельных импульсов достигает 9,5 g . Отчетливо наблюдаются периодические
• Дефекты подшипников качения • 9 — 5•
Наличие ударных импульсов и случайной вибрации приводит к сложному составу спектра сил возбуждения. Сопровождающие такое возбуждение резонансные колебания отдельных узлов и деталей агрегата могут определять его уровень вибрации. При развитии дефектов на нескольких поверхностях качения колебания имеют сложную структуру, приводя к модуляции и появлению вибрации с комбинационными (суммарные и разностные частоты fгоl, fi, fcg , f0, fг и их гармоники) и субгармоническими частотами.
Основным свойством дефектов износа, в отличие от дефектов изготовления поверхностей, является более сильное проявление в сигнале вибрации кратных гармоник в области низких и средних частот, высокий уровень случайной вибрации и наличие ударных импульсов.
Влияние нарушения смазки при эксплуатации.
В принципе, отклонение количества смазки от номинальной величины можно отнеси к дефектам сборки подшипникового узла, а ухудшение качества (коксование, появление твердых частиц и др.) к дефектам износа. Нарушения смазки — наиболее распространенная причина выхода из строя изначально бездефектного подшипника. Уровень высокочастотной вибрации и температуры подшипника существенно зависит от состояния смазки. Кроме того, иногда нарушения смазки могут приводить к появлению в спектре вибрации 3...4 пиков с интервалом в 80...130 Гц в области 900...1600 Гц.
Наибольшее распространение для определения оценки состояния подшипников качения и дефектов нашли две группы методов. Первая группа основана на выделении и анализе дискретных составляющих на основных частотах возбуждения колебаний в подшипнике (см. таблицу 9 — 01).
Диагностическими признаками дефектов служат частотные составляющие спектра и характеристики импульсов, следующих с частотой перекатывания тел качения по локальным дефектам (например, местам выкрашивания): амплитуда импульса, соотношение энергии импульса в уровню шума, амплитуды спектральных составляющих на частоте повторения импульсов и ее гармониках.
Для выделения этих параметров из сложного сигнала используют спектральные и корреляционные методы, выделение огибающей и др. Вторую группу составляют методы диагностирования технического состояния подшипника в целом. При потере работоспособности агрегата не имеют значения дефекты, вызвавшие выход из строя подшипника. Важно, что его необходимо заменить. В силу этого состояние подшипника оценивается по степени развития деградационных процессов. Широкое распространение нашел метод ударных импульсов (SРМ), нашедший воплощение в оборудовании объединения SKF.
Дефектам подшипников качения присущи некоторые особенности В частности, характерно появление в сигнале вибрации гармонических частотных составляющих некратных частоте вращения ротора. Обычно на ранней стадии развития дефектов подшипника появляются признаки дефектов только одного из колец и, затем, другого. При одинаковой степени развития дефекта вибрация, вызываемая внутренним кольцом, имеет более низкую интенсивность, чем наружным. По мере износа подшипника далее появляются дефекты тел качения и, наконец, сепаратора. На осциллограмме вибросигнала (особенно виброускорения) имеются ударные импульсы и выбросы, кривая вибрации обычно имеет случайный непериодический характер, однако некоторые импульсы могут быть периодичны. В спектре достаточно часто частотные составляющие, характерные для дефектов колец, модулируются частотой вращения ротора, приводя к появлению боковых частотных составляющих. С увеличением износа поверхностей качения: и количества локальных дефектов количество и уровень гармонических составляющих, боковых частот и разностных частот возрастают. Появление составляющих вибрации на резонансных частотах других деталей и узлов агрегата обычно говорит о сильном износе подшипника. Высокий уровень случайной
• Дефекты подшипников качения • 9 — 3 •
Частота |
Вид дефекта изготовления |
Вид дефекта сборки |
Вид дефекта износа |
2f0 |
Перекос наружного кольца |
||
kf0 и/или k1f0 ± k2fcg |
Равномерность тел качения |
Дефекты (раковины, трещины, износ) наружного кольца |
|
k1f0 ± k2fr |
Появляется в подшипниках со статической осевой нагрузкой при перекосе внутреннего кольца и дефектах (раковины, трещины) наружного кольца |
||
fi |
Нарушение центровки валов |
||
2fi |
Перекос внутреннего кольца |
||
kfi и/или kfi ± k2fr |
Дефекты (раковины, трещины, износ) внутреннего кольца |
||
k1fi ±k2(fr -fcg ) |
Появляется в подшипниках со статической осевой нагрузкой при перекосе внутреннего кольца и дефектах (раковины, трещины) внутреннего кольца |
||
ffrol |
Нарушение формы тел качения |
Нарушение формы тел качения |
|
ffi |
Нарушение формы внутренней дорожки |
Нарушение формы внутренней дорожки |
|
ff0 |
Нарушение формы внешней дорожки |
Нарушение формы внешней дорожки |
|
frrol |
Резонансная частота тел качения |
Подшипниковые частоты, приведенные в таблице определяют по формулам, приведенным ниже.
fcg - частота вращения сепаратора:

• Дефекты подшипников качения • 9 — 1 •
Дефекты подшипников качения
Ресурс основной части энергомеханического оборудования малой и средней единичной мощности определяется в основном ресурсом подшипников качения. Наиболее эффективный и экономичный метод оценки состояния подшипников — виброанализ. Хотя дефекты изготовления, сборки и эксплуатации подшипников влияют на сигнал вибрации различным образом и имеют разные диагностические признаки, правильно составленный их комплекс позволяет обнаруживать, разделять на начальной стадии развития все виды дефектов, определять состояние подшипника и обеспечивать достаточно достоверный его прогноз.
Параметры вибрации агрегатов с подшипниками качения в значительной мере определяются конструктивными особенностями подшипникового узла (например, радиальные, радиально —упорные, спаренные подшипники) и самого агрегата (например, с горизонтальным и вертикальным положением ротора, соотношением статических нагрузок и др.). Кроме того, влияние на вибрацию подшипников качения оказывают три группы факторов: влияние нелинейной жесткости подшипников на колебания опор, влияние дефектов изготовления и сборки подшипниковых узлов и влияние дефектов эксплуатации (разрушения от усталости материала, повреждения от повышенного износа, разрушения, вызываемые изменением зазоров и посадок между деталями подшипников и опорами ротора и повреждения из —за нарушений смазки). Последние две группы факторов охватывают всевозможные дефекты колец, тел качения и сепараторов, нарушения и ослабления жесткости в местах посадок и превышения зазорами номинальных значений, перекосы подшипника, недостаточность, прекращение или изменение качества смазки, возникновение которых может быть взаимосвязанно. Например, усталостное разрушение подшипников качения появляется в виде выкрашивания материала дорожек колец и тел качения и может происходить из — за чрезмерно больших нагрузок.
Износ деталей подшипника выше допустимого, особенно тел качения и поверхностей колец, приводит к увеличению радиальных зазоров и смещению ротора. Выход сепаратора из строя происходит вследствие нарушений сборки подшипников, действия больших осевых нагрузок, выкрашивания дорожек качения, усталостного разрушения и др. Проскальзывание внутреннего кольца подшипника относительно тел качения приводит к износу поверхностей качения. Недостаток и нарушения качества смазки приводят к оплыванию тел качения, наволакиванию материала на поверхности дорожек и износу сепаратора.
Проводимый на одном из предприятий входной контроль подшипников показал, что в зависимости от партии дефекты изготовления могут содержать от 10 до 90% подшипников партии. Опыт эксплуатации оборудования показывает, что если на агрегат монтируется бездефектный подшипник, то основные причины его выхода из строя распределяются приблизительно следующим образом: 40% —
• Дефекты подшипников скольжения • 8 — 17 •
Важнейшим диагностическим признаком в этом случае оказался рост температуры упорного подшипника, величина которой достигала уровня, отграничивающего срок эксплуатации агрегата.
Поскольку температура упорного подшипника достигала предельно допустимого значения и наблюдалась преобладающая вибрация на частоте вращения ротора компрессора, особенно на задней подшипниковой опоре в осевом направлении предположили наличие дефекта сборки и подгонки упорного подшипника компрессора, а точнее нарушение величины номинального осевого зазора в подшипнике и/или неудовлетворительную площадь контакта. Агрегат был остановлен и проведена ревизия подшипника, в результате которой были обнаружены обе причины: в частности, прилегание поверхностей составляло примерно 60% площади. После устранения дефекта и пуска агрегата в эксплуатацию уровень вибрации снизился до 2,5 мм/с.
Иллюстрацией эксплуатационного износа и нарушения величины номинального осевого зазора в подшипнике может служить следующий пример.

Рис. 8—16. Изменение СКЗ виброскорости опор компрессорного агрегата под влиянием эксплуатационного износа и нарушения величины номинального осевого зазора в подшипнике.
М — электродвигатель, GВ —мультипликатор, V,Н,А — направление измерения вибрации, О — внешняя и I — внутренняя подшипниковые опоры.
Распределение вибрации по опорам компрессорного агрегата приведено на рис. 8—16. Вибрация опор ЭД в осевом направлении значительно превышает вибрацию других опор агрегата.
Установить причину осевой вибрации можно рассмотрев спектры вибрации опор ЭД, приведенные на рис. 8—17. Если спектр вибрации в точке МIА весьма характерен для расцентровки, то спектр вибрации в точке МОА больше характерен для нарушений жесткости. О нарушениях жесткости свидетельствуют также отношения величины вибрации в осевом направлении к радиальному на первой и второй гармониках частоты вращения ротора. Наибольшая вибрация наблюдается на заднем подшипнике ЭД. Кроме того температура заднего упорного подшипника ЭД достигала уровня "предупреждения". Если рассмотреть спектр вибрации заднего подшипника ЭД в осевом направлении (точка МОА), приведенный на рис. 8—18, то можно отметить наряду с высоким уровнем гармонической активности наличие частотных составляющих на дробных гармониках частоты вращения ротора 1,5fr, 2,5fr, 3,5fr, ... , помеченных н графике спектра вертикальными стрелками. Все эти факты говорят о возможном нарушении осевого зазора в упорном подшипнике и его эксплуатационном износе.
В процессе проведения обследования остановленного агрегата и его дальнейшего ремонта эти дефекты были установлены и устранены.
После вывода агрегата из ремонта при полной нагрузке уровень вибрации ЭД не превышал 1,5 мм/с.
• Дефекты подшипников скольжения • 8 — 15 •
Дефекты упорных подшипников.
Упорные подшипники воспринимают осевое усилие на ротор и фиксирует осевое положение ротора относительно неподвижной проточной части корпуса и лабиринтных уплотнений компрессоров насосов, турбин и вентиляторов, в электродвигателе — статора и др.
Основные причины выхода из строя упорных подшипников (как и опорных) следующие: повышенное давление в осевом направлении из —за нарушений технологических или расчетных режимов, у компрессоров из —за износа уплотнений думмиса при повышенной вибрации (вызванной другими причинами); нарушение подачи масла и качества масла; загрязнение подшипников; дефекты сборки и подгонки; эксплуатационный износ; мгновенный выход из строя при попадании в компрессор даже небольших количеств жидкости.
Дефекты сборки и подгонки подшипников включают в себя:
• перекос по вертикали или горизонтали поверхности вкладыша опорного подшипника относительно упорного диска, перекос вкладыша при креплении крышки подшипника: в этих случаях шейка ротора работает по кромке вкладыша и рабочие колодки только частью комплекта;
• угловое смещение упорного диска, корпуса упорного подшипника, вызывает вибрацию в осевом направлении;
• нарушение величины номинального осевого зазора в подшипнике (как правило в пределах 0,25...0,35 мм) вызывает вибрацию в осевом направлении;
• неудовлетворительная площадь контакта (прилегание не менее 70%) вызывает вибрацию в осевом направлении и рост температуры в подшипнике.
Ослабление крепления деталей упорного подшипника вызывает вибрацию в осевом направлении и имеет диагностические признаки нарушений жесткости и рассматривается в соответствующей главе.

Рис. 8—14. Изменение СКЗ виброскорости опор ЦКМ под влиянием неудовлетворительной площади контакта и нарушения величины номинального осевого зазора в заднем подшипнике компрессора. Индексы 1,2 — задний и передний подшипники компрессора, 3,4,5,6 —задний и передний подшипники быстроходного и тихоходного валов мультипликатора, 7,8 — передний и задний подшипники ЭД, V,Н,А — направление измерения вибрации.
В большинстве случаев дефекты упорных подшипников вызывают увеличение вибрации в осевом направлении, при этом нередко наблюдается рост температуры.
В качестве примера можно привести следующий. При выводе из ремонта компрессорного агрегата в процессе испытаний была обнаружена вибрация, превышающая допустимые значения, установленные для длительной эксплуатации агрегата. На рис. 8—14 приведено распределение вибрации по подшипниковым
• Дефекты подшипников скольжения • 8 — 13 •

Рис. 8—12. Форма и спектры сигнала абсолютной а относительной вибрации подшипниковой опоры, наблюдавшиеся при повышенном зазоре (эксплуатационном износе) подшипника.
На рис. 8—12 приведены форма и спектр (средний график) сигнала абсолютной, а также спектр относительной вибрации (верхний) подшипниковой опоры, наблюдавшиеся при повышенном зазоре (эксплуатационном износе) подшипника.
На обоих спектрах наблюдается значительная активность гармоник частоты вращения ротора в области высоких и средних частот. Однако гармоническая активность в области средних частот абсолютной вибрации выше, чем относительной в основном в силу нелинейности влияния масляного клина и последующих разъемных соединений. Распространение колебаний через масляный клин и разъемные соединения подшипника приводит также с существенному возрастанию уровня случайной вибрации. Наблюдаемая при этом форма сигнала вибрации характерна для нарушений жесткости.
• Дефекты подшипников скольжения • 8—11•
сохранение диагностических признаков небольших нарушений подгонки и приработки у агрегата после нескольких месяцев эксплуатации.
Приработка подшипника обычно сопровождается повышенной виброактивностью в области средних и высоких частот.
Следует помнить, что подобные симптомы, зафиксированные с помощью датчиков относительной вибрации, могут говорить о наличии царапин или других дефектов поверхности вала.

Рис. 8—10. Траектория движения ротора в подшипнике скольжения наблюдавшаяся в процессе приработки подшипника.
Наиболее надежными диагностическими признаками нарушений подгонки и приработки являются достаточно характерные изменения формы кривой сигнала виброперемещения и траектории движения вала в подшипнике.
На рис. 8—10 приведена траектория движения вала в подшипнике скольжения, наблюдавшаяся в процессе приработки подшипника ЭД при выводе компрессорного агрегата из ремонта. Весьма характерно в этом случае наличие участков с прямолинейным движением вала в подшипнике, помеченных вертикальными и горизонтальными стрелками. Наклонной стрелкой указано направление вращения ротора.
На рис. 8—11 приведены форма сигнала виброскорости и спектр сигнала виброперемещения подшипниковой опоры ЭД, полученные с помощью датчика абсолютной вибрации. На кривой вибросигнала имеется "площадка", как и на кривой орбиты. В спектре виброускорения бывает высока активность в области высоких и средних частот.
• Дефекты подшипников скольжения • 8—9•
ротора. Цифрой 1 на кривой помечено начало первого оборота ротора, цифрой 2 завершение первого оборота и начало второго оборота ротора, цифрой 3 — завершение второго оборота ротора (а также цикла вращения состоящего из двух оборотов ротора). Таким образом за временной интервал, соответствующий одному обороту ротора можно увидеть половину одного цикла вращения. Петля неподвижна.

Рис. 8—08. Траектории движения вала в подшипнике скольжения при возникновении "сухого вихря".
На рис. 8 — 09 представлен спектр вибрации, возникший при перекосе оси вкладыша подшипника и оси вращения ротора (нарушение верхнего и боковых зазоров подшипника) в результате чего возникла неравномерная смазка и разрывы масляной пленки, приводящие также к небольшим резонансным колебаниям опоры.
Вертикальными стрелками (частоты 16,65 и 24,99 Гц) помечены субгармонические составляющие спектра на 1/2 и 1/3 частоты вращения ротора. Горизонтальными стрелками (74,99, 125,0, 174,99, ... Гц) помечены "дробные" гармонические частоты 1,5, 2,5, 3,5 ... fr, наклонными стрелками помечены колебания на резонансных частотах колебаний опор (29,7, 52,2 Гц). В спектре наблюдается высокая виброактивность на гармониках частоты вращения ротора, в частности на 7 гармонике частоты вращения ротора (350 Гц) пиковое виброперемещение значением 3,5 мкм соответствует СКЗ виброскорости 5,4 мм/с. Высок также уровень шумов. Температура подшипника достигала практически предельно допустимого значения.
Возникновение "сухого вихря" иногда бывает связано с высокой вибрацией (иногда низкочастотной резонансной вибрацией труб).
• Дефекты подшипников скольжения • 8—7•
примерно на 8 МВт. По мере снижения нагрузки низкочастотный компонент вибрации уменьшался: пиковое значение виброперемещения на первой критической частоте ротора (помечен вертикальной стрелкой) снизилось с 61 до 2,5 мкм. Т.е. нагружение агрегата и превышение нагрузкой некоторой пороговой величины в районе 80% от номинальной приводило к резкому увеличению низкочастотной вибрации, а разгружение агрегата и снижение нагрузки до 65...70% от номинальной приводило к снижению вибрации на частоте 15,54 Гц примерно на 40 дБ.
Характерно также и то, что при снижении нагрузки амплитуда и фаза вибрации на частоте вращения ротора и ее второй гармонике практически не изменялись.

Рис. 8—06. Каскадный спектр вертикального компонента вибрации опоры N6 турбоагрегата К— 300— 240— ТВВ— 320— 2 при снижении нагрузки с 290 МВт до 200 МВт под влиянием, "взбиваемой смазки " .
Ротора генераторов обычно имеют неодинаковую жесткость в двух главных взаимно перпендикулярных направлениях (т.н. неравножесткие ротора). При вращении такого ротора его собственная частота из — за пространственной анизотропии жесткости и, следовательно, неодинакового прогиба в течение одного оборота немного циклически меняется с частотой вращения ротора, что приводит к появлению суммарных и разностных частот вокруг частоты вращения ротора и ее гармоник. На рис. 8 — 06 наклонными стрелками помечены боковые частотные составляющие вокруг частоты вращения ротора и вторая гармоника собственной частоты ротора, которые практически исчезают с падением нагрузки.
"Взбиваемая смазка", вызывающая вибрацию на критической частоте ротора паровой турбины или центробежного компрессора часто возбуждается аэродинамическими циркуляционными силами (например, "паровыми") силами. Для возбуждения аэродинамическими циркуляционными силами весьма характерно наличие некоторой пороговой нагрузки, при которой возникает
• Дефекты подшипников скольжения • 8 — 5 •
составляющих той —же частоты, собранных в процессе последовательного измерения и обработки восьми спектров.
Переход от режима работы виброанализатора с "среднеарифметическим усреднением" к режиму с "максимальным пиком" привел к возрастанию низкочастотной составляющей вибрации почти на 50%. Т.о. неустойчивость вибрации на частоте 21,02 Гц, помеченной на рисунке наклонными стрелками очевидна. Следует также обратить внимание на то, что "масляная" вибрация и вибрация на частоте вращения ротора соизмеримы по величине. Вибрация других контрольных точек (ТОV, ТОА, GIН, GIА) имеет подобный характер.
Эти факты говорят о наличии значительной проблемы.
На графиках спектров стрелками помечены третьи гармоники низкочастотной вибрации, лежащие между первой и второй гармониками частоты вращения ротора. Их не следует путать с дробными гармониками частоты вращения ротора (1,5fr, 2,5fr ...), которые могут сопровождать нарушения жесткости, в частности от износа подшипников скольжения. Значительный износ подшипников скольжения также может приводить к потере устойчивости.

Рис. 8—04. Форма сигнала виброскорости опоры N4 турбоагрегата К—200—130 в горизонтально— поперечном направлении под влиянием нарушения центровки и "вихревой смазки".
На рис. 8 — 04 приведена форма сигнала виброперемещения опоры №4 в горизонтально — поперечном направлении. Временные интервалы между вертикальными пунктирными линиями, нанесенные на график через каждые 20 мс соответствует одному обороту ротора. Кривая виброскорости от оборота к обороту меняется: через каждые два или три оборота ротора следует максимум, вызываемый "масляной" вибрацией. На 20 оборотов ротора приходится примерно восемь таких максимумов, что и соответствует вибрации на частоте 0,42fr .
Значительное снижение общего уровня вибрации и полное устранение низкочастотной вибрации было достигнуто путем правильной центровки турбоагрегата с учетом тепловых деформаций фундамента.
• Дефекты подшипников скольжения • 8 — 3 •
вращается в направлении движения ротора (направление движения ротора помечено горизонтальной стрелкой) и, обычно, поворачивается на 360 градусов и возвращается в примерно исходное положение за 12...50 оборотов ротора или 6...25 циклов вращения (что зависит от отношения частот колебаний составляющей "вихревой смазки" и вращения ротора). В приведенном примере цифрой 5 помечено начало, а цифрой 4 — окончание одного из последовавших далее циклов вращения.
В приведенном ниже примере показано влияние "вихревой смазки' на характер вибрации.

Рис. 8—02. Изменение гармонического состава вибрации 4...7 опор турбоагрегата К—200—130 под влиянием нарушения центровки и "вихревой смазки".
Условные обозначения: Т — турбина, G — генератор, V,Н,А — пространственные компоненты вибрации.
При пуске в эксплуатацию турбоагрегата К —200— 130 была обнаружена низкочастотная вибрация в районе опор 4...7 ротора низкого давления и генератора. Частотный состав вибрации, включающий полосу низких частот 10...48
• Дефекты подшипников скольжения • 8—1 •
Дефекты подшипников скольжения
Дефекты подшипников скольжения и причины их выхода из строя можно условно разделить на две группы, в соответствии с которыми будет изложен материал текущей главы:
• низкочастотная вибрация подшипников1, возникающая вследствие потери динамической устойчивости вращения ротора и нарушения условий смазки;
• вибрация, связанная с дефектами изготовления, сборки и эксплуатации опорных и упорных подшипников скольжения, включающих различные дефекты сборки и подгонки подшипников и отклонение их геометрических размеров от номинальных, эксплуатационный износ подшипников, дефекты состояния шеек, нарушение качества поверхности материала вкладыша и др.
Различные дефекты подшипников скольжения часто бывают взаимосвязанны между собой. Например, повышенная вибрация и износ подшипника могут приводить к потере динамической устойчивости.
Характерные черты вибрации при зарождении и развитии различных дефектов подшипников скольжения могут быть весьма разнообразны и зависят от множества факторов. Основные из них: величина и место приложения сил возбуждения, перераспределение реакций, нагруженность опор, крутящий момент, свойства, качество смазочного слоя и условия работы смазочного слоя в подшипниках, частота вращения ротора, степень развития дефектов подшипников, в том числе приводящих к неустойчивости ротора (например, перераспределение реакций опор при эксплуатационных расцентровках) и др. В вибрационном сигнале могут присутствовать колебания с частотой вращения ротора, возможно ее гармониками, субгармониками и дробными гармониками, некратная частоте вращения ротора низкочастотная и среднечастотная вибрация, случайная вибрация.
Низкочастотная вибрация подшипников.
Низкочастотная вибрация подшипников в большинстве случаев связана с потерей динамической устойчивости вращения ротора. Потеря динамической устойчивости вращения ротора возникает, когда циркуляционные силы масляной пленки и/или аэродинамические циркуляционные силы превосходят силы демпфирования. Это явление характерно для подшипников, имеющих цилиндрическую или эллиптическую расточку вкладыша, и часто встречается у быстроходных агрегатов с легкими роторами, агрегатов с вертикально расположенной осью вращения роторов, машин с малой нагрузкой на подшипники или относительно большой длиной (площадью) опорной части подшипника. Потере динамической устойчивости способствует снижение нагрузки (т.е. разгрузка) подшипника, повышение вязкости смазывающей жидкости, проблемы и применение маслоперепускной канавки, повышение зазоров в подшипнике, перекосы оси вкладыша по отношению к оси вращения (шейки) ротора, разгружающее неуравновешенное паровое усилие и др.
• Нарушения жесткости опорной системы • 7—23 •
подшипников в других направлениях измерении имеет сходный характер. Сравнение уровней вибрации по подшипникам насосного агрегата указывает на локализацию дефекта на насосе, вероятней в области переднего подшипника. Анализ спектров выявляет характерную для нарушений жесткости высокую гармоническую активность, спектры имеют сложный частотный состав, а также наблюдается достаточно высокий уровень шумов (см. участки спектров, помеченные стрелками).

Рис. 7—23. Спектры вибрации подшипниковых опор насосного агрегата в вертикальном направлении при нарушении посадки насадного кольца на вале насоса.
На рис. 7 — 24 приведены спектры вибрации передней подшипниковой опоры насоса в вертикальном направлении до (спектр от 11.10.93) и после (спектр от 25.11.93) возникновения нарушения посадки насадного кольца на валу насоса.
• Нарушения жесткости опорной системы • 7—21 •
Приведенные ниже данные измерения вибрации измерены на насосном агрегате, имевшем дефект муфты, в т.ч.
нарушение посадки муфты, разрушение шпоночной канавки, отслоение металла и трещины в металле вала.

Рис. 7—21. Распределение СКЗ виброскорости по точкам измерения вибрации на насосном агрегате (индексы "01" и "02" соответствуют контрольным точкам заднего и переднего подшипниковых узлов ЭД, а, соответственно, "03" и "04" переднего и заднего подшипниковых узлов насоса).
Сравнение уровней вибрации по подшипникам насосного агрегата явно указывает на локализацию дефекта на насосе, вероятней в области переднего подшипника рис. 7 — 21, где текущие значения вертикального и осевого компонентов вибрации многократно превысили допустимые значения.
На спектрах вибрации заметна характерная для нарушений жесткости высокая гармоническая активность: наблюдается до шести интенсивных гармоник частоты вращения ротора. Имеется также вибрация на "промежуточной" частотной составляющей fm (не совпадающей с подшипниковыми частотами). Подробней о "промежуточных" частотах рассказано в главе "Дефекты зубчатых передач". Вокруг "промежуточной" частотной составляющей fm имеются многочисленные боковые частотные составляющие fm±kfr , говорящие о возможной связи нарушений жесткости с зубчатой муфтой.
Формы сигналов вибрации также весьма характерны для ослаблений жесткости. Примечательны двойные ударные импульсы, встречающиеся раз за оборот (некоторые из них помечены двойными стрелками), возникающие в результате нарушения посадки.
Нарушение посадки вращающихся с валом насадных деталей может приводить к сложным процессам одновременного существования и взаимодействия различных источников возбуждения, появляющихся при
• Нарушения жесткости опорной системы • 7—19 •
Нагрузочный вектор вибрации Вi1Вi — при различных пусках приводит к малому увеличению вибрации без какой —либо системы.
0°

Рис. 7—19. Векторная диаграмма с результатами, балансировки компрессорного агрегата.
Это говорит о возможном ослаблении жесткости опоры А.
Поскольку значения радиальных зазоров заднего подшипника были близки к предельно допустимым, то сначала предположили, что ослабление жесткости связано именно с большим зазором. Однако, поскольку в спектре поперечного компонента вибрации уровни высших гармоник частоты вращения ротора по отношению к первым двум были невелики, предположили нарушение жесткости одного из разъемных соединений.
После останова была произведена ревизия заднего подшипника, обнаружено и устранено ослабление резьбовых соединений крепления крышки вкладыша подшипника, после чего установили корректирующие массы и пустили агрегат. Верхний спектр на рис. 7 — 20 измерен при номинальной нагрузке. Можно отметить значительное снижение вибрации на частоте вращения ротора и 3...16 ее гармониках, а также снижение уровня шумов. Верхний спектр характерен для расцентровки с параллельным смещением осей, нижний — для нарушений жесткости и расцентровки.
Этот пример подтверждает необходимость и обязательность использования для диагностики всех имеющихся данных: анализа спектров в комбинации с анализом формы сигнала, анализом влияния на вибрацию места и направления проводимых измерений, крутящего момента, корректирующих масс, расширения опор при прогреве, начальных зазоров в подшипниках после проведения ремонта и любой другой имеющейся информации.
• Нарушения жесткости опорной системы • 7—17 •
между рамой и плитой фундамента, произошедший между контрольными точками Н35 и Н36.
В процессе проверки прилегания рамы и поверхностей фундаментной плиты было обнаружено отставание по краям рамы в области обеих опор насоса и коробление фундаментной плиты в районе опорной поверхности вследствие систематического попадания смазывающей жидкости и воды.

Рис. 7—18. Формы и спектры сигналов вертикального компонента вибрации подшипниковой опоры насоса при дефекте соединительной трехкулачковой муфты.
• Нарушения жесткости опорной системы • 7—15 •

Рис. 7—15. Спектры вибрации подшипников насоса насосного агрегата.
Приведенные на рис. 7—16 спектры вибрации переднего подшипника насоса в горизонтально — поперечном и осевом направлении измерены практически в одной пространственной точке: расстояние между точками ввода (измерений) примерно 1 см, однако разница в характере вибрации существенна.
Вибрация в поперечном направлении в 2,7 раза выше, чем в осевом, в то время как уровень шумов верхнего спектра в 5...10 раз выше, чем нижнего (см. точки, помеченные вертикальными стрелками), а уровни высших гармоник частоты вращения ротора в верхнем спектре в 8...12 раз выше, чем в нижнем (см. точки, помеченные наклонными стрелками). Кроме того, в верхнем спектре преобладают первые четыре гармоники частоты вращения ротора, в нижнем только две (точки, помеченные горизонтальными стрелками).
Нижний спектр характерен скорее для расцентровки узлов агрегата, в то время как верхний — для ослабления жесткости опоры. Совместный анализ
• Нарушения жесткости опорной системы • 7—13 •

Рис. 7—12. Контурная характеристика вибрации задней опоры ЭД и правой стойки фундамента.
Позднее в стойке фундамента была обнаружена трещина, приводящая к снижению жесткости опорной системы.
При некачественной подливке бетона или его разрушении в процессе эксплуатации (например, вследствие попадания масла и др.), короблении фундаментной плиты возникает неплотность прилегания (отставание), легко обнаруживающаяся при снятии контурной характеристики.
Как говорилось выше, при отставании основания подшипника от рамы, в средней части обычно возрастает вертикальная вибрация, если имеется отставание по краям подшипника, то в этом случае соответственно возрастает горизонтальная вибрация, в случае одностороннего неплотного прилегания направление максимальной вибрации будет зависеть от особенностей возбуждения.
Иллюстрацией вышеизложенным двум абзацам служит следующий пример: вибрация насосного агрегата, перекачивающего бензин, с ЭД мощностью 75 кВт, подшипниками качения и зубчатой муфтой превышает норму, проведенный ремонт подшипников и замена рабочего колеса насоса не привели к уменьшению вибрации и изменению ее характера. Из соседних семи агрегатов у двух схожее вибросостояние.

Рис 7—13. Схема расположения контрольных точек на насосном агрегате.
Рассматривая распределение вибрации агрегата по контрольным точкам (см.
рис. 7 — 14 и рис. 7—13) можно отметить превышение допустимого значения
• Нарушения жесткости опорной системы • 7—11 •
МS3 наблюдается активность гармоник с номерами до 10, и преобладанием первых трех, спектр точки НF8 — только 1 — ю и 2 — ю, а точки НF9 — только 1 — ю гармоники частоты вращения ротора.
По мере удаления контрольных точек от ротора падает как уровень вибрации, так и интенсивность относительно первой высших гармонических составляющих частоты вращения ротора.
В процессе измерений вибрации в каждой из контрольных точек была присуща флуктуация амплитуд частотных составляющих спектра: от кадра к кадру на экране анализатора на "картинках" спектра амплитуды 1 и 2 гармоник оборотной частоты ротора изменялись на 15...30 %.

Рис. 7—10. Спектры вибрации ряда контрольных точек в области правой стойки фундамента в районе заднего подшипника ЭД с трещиной в фундаментной стойке.
Горизонтальными стрелками помечена 3 гармоника частоты вращения ротора, присутствующая в основном на опоре подшипника, наклонными стрелками
• Нарушения жесткости опорной системы • 7—9 •
ротора). Текущее значение вибрации при этом значительно превышало допустимое.
Очень важно помнить, что анализ форм сигналов необходимо проводить только в комбинации с анализом спектров, и выводы, если имеются какие—либо особенности формы сигнала, использовать только как дополнительный довод о вероятности наличия того или иного дефекта!
Обычно, при нарушениях жесткости вибрация анизотропна (один из пространственных компонентов вибрации по значению существенно превышает другие) и максимальным бывает, в большинстве случаев, в направлении перпендикулярном плоскости ослабления жесткости: при горизонтальном положении ротора встречается несколько чаще в вертикальном направлении, поскольку большинство разъемных соединений и плоскостей крепления перпендикулярны именно вертикальному направлению. Обычно, но не всегда, так как, например, при отставании основания подшипниковой опоры от рамы в средней части, возрастают вертикальные вибрации, поскольку вместо нормальной деформации стойки на сжатие возникает изгиб основания подшипника, но если имеется отставание не в середине, а по краям подшипниковой опоры, то в этом случае ослабляется жесткость установки в горизонтальном направлении и соответственно возрастают горизонтальные вибрации, а в случае одностороннего неплотного прилегания опоры жесткость будет зависеть от многих факторов.
Необходимо сравнивать отношение значений вибрации по горизонтали и вертикали: если оно превышает 4, то это может говорить о чрезмерной гибкости опоры в одном из направлений.
Важнейший надежный диагностический признак нарушений жесткости — изменение характера вибрации при переходе через границу дефектного сопряжения. Для обнаружения последних снимают контурную характеристику в различных точках агрегата или структурного элемента, измеряя амплитуду и фазу вибрации на первой (и, иногда, высших) гармонике.
Если смежные части агрегата или его узла имеют значительно отличающиеся значения амплитуд и фаз вибрации, то имеются относительные движения этих частей (элементов), и имеет место нарушение жесткости. При достаточной жесткости системы опора — фундамент вибрация должна плавно уменьшаться (без скачков амплитуды и фазы) от крышки подшипника до фундамента в 2...5 раз (в среднем 2.5...3).
При ослаблениях жесткости фундамента часто наблюдается повышенная вибрация не только подшипниковых опор, но и статора электромашины, корпусных деталей, возможно фундаментной плиты, болтов и др. В спектре значительно преобладают первая, вторая и реже третья и четвертая гармоники частоты вращения ротора. Для локализации ослабления снимается контурная характеристика.
Проиллюстрировать это можно приведенным ниже примером. У питательного насоса мощностью 8 МВт с частотой вращения ротора 50 Гц в течение 3 месяцев наблюдался рост вибрации с превышением допустимых значений. Было также обнаружено некоторое снижение вибрации при уменьшении крутящего момента (при ступенчатом разгружении агрегата). Проведение среднего ремонта и балансировки ротора ЭД в собственных подшипниках не привели к снижению вибрации до нормативных уровней.
Рассматривая распределение вибрации агрегата в пространстве (рис. 7 —08 и рис. 7 — 09) можно отметить высокую вибрацию в контрольных точках на статоре ЭД и фундаментных болтах в районе ЭД и нормальную вибрацию на фудаментных болтах в районе насоса. Вибрация группы контрольных точек заднего подшипника ЭД выше, соответствующих по направлению контрольных точек на других подшипниках агрегата.
Разделив контрольные точки на группы V01—V02 —VОЗ —
• Нарушения жесткости опорной системы • 7—7 •
Форма сигнала виброскорости может иметь более "упорядоченный" характер (по сравнению с сигналом виброускорения), однако амплитуда сигнала обычно бывает нестабильна от оборота к обороту (или в продолжение нескольких оборотов) и может меняться иногда даже
в несколько раз.

Рис. 7—05. Формы сигналов (верхний график — виброускорение, нижний — виброскорость) вертикального компонента вибрации, измеренные на подшипнике электродвигателя насосного агрегата с частотой вращения ротора 50 Гц (20мс/об), имевшего дефект прокладки виброизолятора.
Примером этому служат две формы сигнала вибрации, приведенные на рис. 7 — 05, измеренные с интервалом в несколько секунд на подшипнике электродвигателя (частота вращения ротора 50 Гц, 20мс/об) насосного агрегата в вертикальном направлении, над имевшей дефект прокладкой виброизолятора. Вертикальными стрелками помечены некоторые нерегулярные пики сигнала виброускорения, количество и величина которых от оборота к обороту значительно меняется. Форма сигнала виброскорости менее (по сравнению с сигналом виброускорения) "хаотична". На кривой виброскорости парами вертикальных, горизонтальных и наклонных стрелок помечены периодические максимумы, следующие с соответствующим одному обороту временным интервалом (примерно 20 мс). Флуктуации значений помеченных максимумов достаточно велики.
Если в предыдущем примере флуктуации значений помеченных максимумов на кривой сигнала виброскорости могли вызываться накладывающимися на них высокочастотными составляющими вибрации, то на изображенной на рис. 7 — 06 форме сигнала высокочастотный компонент вибрации невелик. Вертикальными пунктирными линиями помечены временные интервалы соответствующие одному обороту ротора насосного агрегата, имевшего ослабление жесткости в виде несимметричного отставания опоры насоса от рамы насосного агрегата.
• Нарушения жесткости опорной системы • 7—5 •

Рис. 7—03. Спектры вибрации иллюстрирующие развитие во времени ослабления резьбовых соединений в подшипнике насосного агрегата, перекачивающего нефтепродукты.
• Нарушения жесткости опорной системы • 7—3 •

Рис. 7—01. Траектория движения ротора мощного электродвигателя за один оборот при износе подшипника скольжения и ослаблении резьбовых соединений.
Часто наблюдается "пустая точка" (помечена наклонными стрелками) — большой разрыв траектории и/или изменение направления движения ротора в момент завершения ротором одного оборота и прохождения отметки угла на роторе мимо датчика[2].
В правой части графика заметна небольшая повторная петля, также наблюдающаяся иногда при нарушениях жесткости.
В спектре вибрации почти всегда можно наблюдать сравнительно интенсивную вибрацию на нескольких высших гармониках частоты возбуждения, число которых колеблется от 2...3 до 10 и более. Типично в спектре наблюдается сравнительно высокий уровень шумов[3], что обусловлено значительной долей случайной вибрации в вибросигнале (особенно виброускорения).
Примером такого спектра может служить приведенный на рис. 7 — 02. Горизонтальными стрелками помечены некоторые из гармоник частоты вращения ротора.
По мере изменения состояния оборудования (развития дефекта: уменьшения жесткостисистемы) в спектре между высшими гармоническими составляющими могутпоявляться дробные гармоники частоты возбуждения kfr±(1\m)fr , где m — натуральное число, (например, 1,5fr, 2,5fr, 3,5frг,... и др.). При этом также возрастает и уровень шумов.
• Нарушения жесткости опорной системы • 7—1 •
Нарушения жесткости опорной системы1
Как известно, в устойчивом режиме вращения колебания идеально уравновешенного ротора отсутствуют, однако на реальный ротор воздействуют различные неуравновешенные силы, возбуждая вибрацию. Поскольку сами по себе нарушения жесткости являются не источниками возбуждения вибрации, а лишь нелинейным откликом системы (агрегата) на воздействие неуравновешенных сил, вызывающих вибрацию, то в этом классе дефектов можно объединить те, которые приводят к нерасчетному изменению жесткости опорной системы (в т.ч.
уменьшению общих расчетных масс, колеблющихся вместе с источниками возбуждения) и повышению вибрации оборудования. С появлением дефектов этой группы вибрация иногда может многократно превышать допустимые значения.
Влияние жесткости опорной системы на вибрацию очевидно. Амплитуда вибрации обратнопропорциональна динамической жесткости:

где А — амплитуда вибрации; Сd — динамическая жесткость;
Р0 — амплитуда вынуждающей силы.
Существенно снижается динамическая жесткость в области резонанса. При резонансе даже небольшие вынуждающие силы приводят к чрезмерной вибрации опор. Для устранения этой проблемы необходима отстройка опорной системы от резонанса изменением ее жесткости, обычно в сторону увеличения, или массы.
Реальные опоры в вертикальном и горизонтально —поперечном направлениях обладают различной жесткостью. Это свойство опор называется анизотропностью. При анизотропности частотные характеристики для вертикального и горизонтально — поперечного направлений различны. Например, при некоторой небольшой неуравновешенности ось вращающегося ротора имеет не круговую орбиту, а эллиптическую, причем большая ось эллипса лежит в направлении, близком к горизонтальному. Соответствующие колебания совершают точки поверхности подшипника, при этом на симметричном относительно вертикальной плоскости подшипнике возникает асимметричная вибрация. Не следует, таким образом, сразу связывать асимметричную вибрацию с
• Нарушения жесткости опорной системы • 6 —15 •

Рис. 6—11. Спектры и формы сигналов вибрации внешней опоры возбудителя в горизонтально— поперечном и осевом направлениях.
На формах сигналов виброускорения вертикальными пунктирными линиями помечены периоды времени, соответствующие одному обороту ротора. Вертикальными стрелками на кривой вибрации помечены локальные максимумы в течение двух последовательных оборотов ротора. Можно отметить, вибрация носит почти периодический характер. Число локальных максимумов за оборот ротора практически не меняется. Случайная вибрация невелика.
Такая форма кривой виброускорения, обычная для развитой расцентровки, нетипична для нарушений жесткости.
Таким образом, на возбудителе наблюдалась нелинейная жесткость опорной системы3, не связанная с какими — либо дефектами. В дальнейшем, после останова агрегата, была обнаружена и устранена расцентровка генератора и возбудителя.
• Нарушения соосности валов (расцентровка) • 6 — 13 •
Характерно, что эти вектора параллельны и разнонаправленны. Их величина отличается из —за различной жесткости и динамической податливости опор.
На рис. 6 — 09 приведены спектры вибрации тех же контрольных точек при номинальной нагрузке до и после центровки с учетом тепловых расширений и положения ротора. Вибрация компрессора существенно уменьшилась: на частоте вращения ротора в 1,6 раза, а на ее второй и третьей гармониках — в 6 раз. На мультипликаторе уменьшения вибрации не произошло: уменьшение в несколько раз вибрации, связанной с расцентровкой, на второй и третьей гармониках частоты вращения ротора сопровождалось увеличением вибрации на частоте вращения ротора, поскольку имелась вибрация, вызываемая другой причиной, которая ранее компенсировалась: складывалась с вибрацией, вызванной расцентровкой (синхронные колебания).
Таким образом появление векторов вибрации А2А3 и В2В3, вызванных расцентровкой и складывающихся с векторами вибрации ОА3 и ОВ3, вызванными другими причинами, на мультипликаторе приводили к незначительному уменьшению вибрации, а на компрессоре к значительному увеличению. В целом по агрегату максимальная вибрация снизилась с 3,6 до 2,6 мм/с., т.е. почти на треть.
Следует добавить, что использование взаимных фазовых спектров должно происходить с определенной осторожностью. Хотя имелись очевидные признаки расцентровки мультипликатора и компрессора, вектора вибрации на частоте вращения ротора не антифазны — угол между ними составляет около 80 градусов (см. угол между векторами ОА2 и ОВ2 рис. 6 —07 и разность фаз между первыми гармониками, помеченную наклонной стрелкой на рис. 6 — 08).
Это говорит о наличии значительной, по отношению к вибрации, вызванной расцентровкой, вибрации, связанной с другими причинами (синхронные колебания). Таким образом, чем больше отношение вибрации, вызванной расцентровкой, к вибрации, вызванной другими причинами, тем ближе этот угол к 180 градусам.
В процессе вибромониторинга, сравнивая характер вибрации опор, вполне возможно отличить расцентровку от ослаблений жесткости, обладающих различными наборами диагностических признаков. В этом случае полезно сравнивать одновременно со спектрами вибрации и осциллограммы сигналов.
На рис. 6—10 приведены спектры вибрации, измеренной на подшипниковых опорах генератора (индекс Т) и возбудителя (индекс В) парового турбоагрегата. Состав частотных компонентов спектра вибрации опор генератора характерен для расцентровки и не вызывает сомнений — вибрация существенно преобладает на первых двух гармониках частоты вращения ротора практически на всех контрольных точках, как в поперечном, так и в осевом направлениях, уровень шумов низок. На первый взгляд характер вибрации подшипниковых опор возбудителя свойственен для ослаблений жесткости в совокупности с расцентровкой: в спектрах вибрации обеих опор как в горизонтально —поперечном и вертикальном, так и в осевом направлениях наблюдается достаточно интенсивная вибрация на частоте вращения ротора и гармониках с номерами до 6...8, причем в спектрах вибрации контрольных точек ВIV и ВОН преобладает третья гармоника частоты вращения ротора.
Рассмотрим одновременно спектры (наиболее характерные для нарушений жесткости) и формы сигналов вибрации задней подшипниковой опоры возбудителя в горизонтально —поперечном и осевом направлениях, представленные на рис. 6—11.
• Нарушения соосности валов (расцентровка) • 6 — 11 •

Рис. 6—07. Векторная диаграмма вибрации при прогреве и погружении агрегата.
Кроме того, на рис. 6 — 08 приведен взаимный фазовый спектр вибрации вышеупомянутых контрольных точек после нагружения. Однонаправленными стрелками на второй и третьей гармониках частоты вращения ротора отмечено, что они находятся практически в противофазе, что также указывает на возможную расцентровку.

Рис. 6—08. Взаимный фазовый спектр вибрации при номинальной нагрузке.
После останова агрегата в течение нескольких минут с помощью лазерного центровочного оборудования были проведены измерения положения осей, значения которых составили: осевой сдвиг по вертикали V=0,14мм, по горизонтали Н = 0,16мм, излом осей по вертикали V=0,04мм/100мм, по горизонтали V = 0,02мм/100мм. Т.о. если смотреть со стороны "неподвижного" мультипликатора, то ротор компрессора сдвинулся в сторону тихоходного колеса и вниз. На следующее утро вновь произвели измерения положения осей "холодного"
• Нарушения соосности валов (расцентровка) • 6 — 9 •
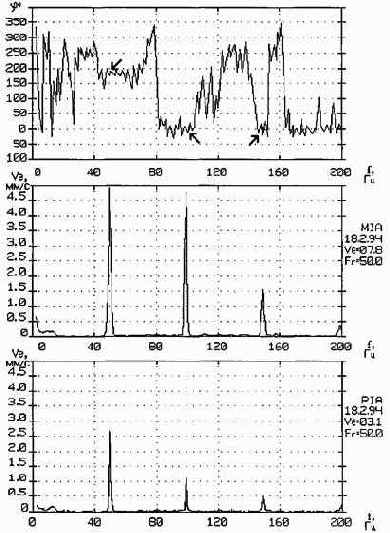
Рис. 6—06. Амплитудные спектры вибрации и взаимный фазовый спектр вибрации измеренные в осевом направлении на внутренних подшипниковых опорах ЭД и насоса при изломе осей.
Необходимо помнить, что для увеличения достоверности диагностирования необходимо основываться не только на данных спектрального анализа: в случае расцентровки ценную дополнительную информацию можно почерпнуть, сравнивая фазы вибрации гармонических составляющих на частоте вращения ротора, измеренные на разных подшипниковых опорах.
Очевидно, что если разность фаз вибрации на частоте вращения ротора (или ее второй гармоники) двух смежных подшипниковых опор различных узлов агрегата в осевом направлении составляет 0 или 180 градусов (т.е. вектора вибрации синфазны или антифазны), то дефектное сопряжение локализуется между подшипниками. Например, для жестких или заклиненных муфт: если на работающем оборудовании при сравнении параметров осевой вибрации (измеренных с помощью датчиков относительной вибрации) обнаружится, что вектора вибрации на частоте вращения ротора синфазны, то, наиболее вероятно, что муфта заклинена, а если осевые колебания вала не совпадает по фазе, то
• Нарушения соосности валов (расцентровка) • 6 — 7 •
При расцентровке может встречаться как поперечная, так и высокая осевая вибрация, которая в ряде случаев значительно (в два и более раз) превышает поперечную.
Для торцевой расцентровки характерна высокая осевая и/или поперечная вибрация на первой гармонике частоты вращения ротора, но при этом может быть значительная вибрация на второй, третьей и высших гармониках.
На рис. 6 — 04 приведены спектры виброскорости измеренные на задних подшипниковых опорах ЭД и центробежного насоса в вертикальном, горизонтально — поперечном и осевом направлениях. На спектрах помечены преобладающая вибрация на частоте вращения ротора и некоторые ее гармоники превышающие по значению 1 мм/с. Ось амплитуд приведена в логарифмическом масштабе: обратите внимание на соотношение и уровень гармонических составляющих и шумового компонента.
После останова агрегата была установлена расцентровка со следующими значениями: осевой сдвиг по вертикали V = 0,05мм, по горизонтали Н = 0,03мм, излом осей по вертикали V = 0,34мм/100мм, по горизонтали V = 0,59мм/100мм.
При развитой радиальной расцентровке, как в случае горизонтального осевого сдвига, так и вертикального, вибрации в поперечной плоскости обычно бывают несколько больше осевой, как на первой, так и на второй гармонике частоты вращения ротора. При этом вибрация на второй гармонике часто преобладает в спектре. Примечательно, что в некоторых случаях наибольшей вибрация бывает в направлении, перпендикулярном наибольшему смещению осей: например при больших значениях осевого сдвига по горизонтали преобладает вертикальный компонент вибрации.
На рис. 6 — 05 приведены спектры виброскорости измеренные на передних подшипниковых опорах электродвигателя и центробежного насоса магистрального насосного агрегата в вертикальном, горизонтальном — поперечном и осевом направлениях. На спектрах стрелками помечена преобладающая вибрация на второй гармонике частоты вращения ротора и лопаточная частота рабочего колеса насоса (7 лопаток). После останова агрегата была установлена расцентровка со следующими значениями: осевой сдвиг по вертикали V = 0,29мм, по горизонтали Н = 0,52мм, излом осей по вертикали V = 0,09мм/100мм, по горизонтали V=0,02мм/100мм.
• Нарушения соосности валов (расцентровка) • 6 — 5 •
вибрации на частоте вращения ротора, то расцентровка представляет серьезную проблему, которая, вероятно, приведет к ускоренному износу муфты и, в конечном счете, выходу ее из строя".
На рис. 6 — 03 приведен пример развития расцентровки насосного агрегата, увеличивающейся вследствие неравномерной осадки свайного фундамента в течение трех весенних месяцев по мере изменений характеристик грунта.

Рис. 6—03. Динамика изменения спектров вертикальной компоненты вибрации заднего подшипника ЭД при торцевой расцентровке насосного агрегата, развивающейся вследствие неравномерной осадки свайного фундамента.
Апрель (нижний спектр) — вибрация в пределах, допускающих не ограниченную по времени эксплуатацию агрегата, в спектре преобладают 1 и 4 гармоники частоты вращения ротора.
Май (средний спектр) — вибрация существенно возросла и находится в пределах, допускающих ограниченную по времени эксплуатацию агрегата, в спектре по —прежнему преобладают 1 и 4 гармоники частоты вращения ротора,
• Нарушения соосности валов (расцентровка) • 6 — 3 •
форма кривой вибрации, т.е. практически неизменные временные интервалы соответствующие одному обороту ротора между локальными максимумами (минимумами) кривой вибрации1 . Количество преобладающих локальных максимумов за оборот неизменно и обычно составляет один— два, а их пиковое значение может флуктуировать от оборота к обороту в 1,2...2 раза и составляет обычно 0,3...1g при развитом дефекте, редко превышая 2g (при частоте вращения ротора 50 Гц).
Форма сигнала виброскорости обычно имеет более "упорядоченный" (по сравнению с формой сигнала виброускорения) характер: флуктуации значений локальных максимумов кривой от оборота к обороту заметно меньше.
• Кривая сигнала может быть асимметрична, положительные и отрицательные значения амплитуд могут отличаться в 1,2...1,5 раз2.
На рис. 6 — 02 приведены формы и спектры сигналов виброускорения и виброскорости, измеренные с интервалом в несколько секунд на крышке задней подшипниковой опоры ЭД расцентрованного насосного агрегата в вертикальном направлении.
На спектрах горизонтальными стрелками помечены первая и вторая гармоники частоты вращения ротора. На спектре виброускорения кратная частоте вращения ротора вибрация, хотя и низкая по уровню, проявляется наглядней, чем на спектре виброкорости. Уровень шумов невысок.
На формах сигнала вибрации вертикальными пунктирными линиями помечены временные интервалы, соответствующие двум оборотам ротора. Сигнал вибрации почти периодический, за один оборот ротора наблюдается два максимума (минимума) кривой, в сигнале виброскорости пиковые значения локальных максимумов (от оборота к обороту ротора) практически неизменны, в сигнале виброускорения флуктуируют в пределах 15% (см. максимумы, помеченные однонаправленными стрелками). Случайная вибрация практически отсутствует.
После останова агрегата была установлена расцентровка со следующими значениями: осевой сдвиг по вертикали V=0,32мм, по горизонтали Н = 0,47мм, излом осей по вертикали V = 0,12мм/100мм, по горизонтали V = 0,09мм/100мм. Следует отметить отличное техническое состояние агрегата: после проведения центровки с применением лазерного центровочного оборудования вибрация опор не превышала 1,1 мм/с.
Очень важно помнить, что анализ форм сигналов необходимо проводить только в комбинации с анализом спектров, и выводы, если имеются какие—либо особенности сигнала, использовать только как дополнительный довод о вероятности наличия того или иного дефекта!
По мере развития дефекта и изменения состояния оборудования (увеличения расцентровки и/или изменения состояния муфты) в спектре обычно возрастает вибрация на первой и/или второй гармонике частоты вращения ротора. Величину и соотношения последних используют в качестве диагностических параметров степени нарушений соосности валов.
• Нарушения соосности валов (расцентровка) • 6 — 1 •
Нарушения соосности валов (расцентровка)
Характер вибрации оборудования при нарушениях соосности валов (расцентровке) в большинстве случаев определяется конструкцией применяемых соединительных муфт.
Например, если гибкие или подвижные муфты способны компенсировать значительные нарушения соосности валов практически без изменения вибросостояния агрегата за счет ухудшения условий работы собственных элементов, то жесткие муфты при этом, испытывая лишь повышенные напряжения в болтовых соединениях, полностью передают изменившиеся условия работы валов на опоры, вызывая значительное изменение их реакций и вибросостояния агрегата. Зубчатые и полужесткие муфты допускают определенные нарушения соосности соединяемых валов при малозаметном изменении вибросостояния агрегата, но при этом для зубчатых муфт расцентровка может иметь различные неблагоприятные последствия: ускоренный износ, деформация или излом зубьев. Бывают случаи, когда муфта оказывается прочнее, чем смежный подшипник, что может приводить к повреждению последнего.
В некоторых случаях влияние на вибрацию конструкции и состояния муфты выражается в подавлении диагностических признаков расцентровки на смежных подшипниках, т.е. признаки расцентровки проявляются на внешних (относительно муфты) подшипниках дефектно сопряженных валов.
Таким образом, вибрации опор при расцентровке, хотя и не являются линейной функцией степени развития последней, достаточно адекватно характеризует способность агрегата, как системы, справляться с ней.
Характер вибрации при расцентровке зависит от величины и места приложения неуравновешенных сил, крутящего момента, свойств и качества смазочного слоя в подшипниках, а также состояния муфты. В вибрационном сигнале обычно присутствуют колебания с частотой вращения ротора, возможно ее гармониками, при определенных условиях вследствие расцентровки возможно появление низкочастотной вибрации.
Влияние расцентровки на траекторию движения ротора в подшипнике выражается в том, что ее форма по сравнению, например, с формой при дисбалансе несколько усложняется: если при дисбалансе обычно это эллипс, то при расцентровке кривая становится менее "округлая" и может наблюдаться, например, сильно вытянутый эллипс, "деформированный" эллипс, "бананообразная" или "восьмеркообразная" кривые.
На рис. 6 — 01 приведены
• Неуравновешенность ротора • 5 — 22 •

Рис. 5—18. Схема водопровода и размещения контрольных точек насосного агрегата и гармонический состав вибрации опор при задеваниях ротором статора. V, Н, А — вертикальные, горизонтально—поперечные и осевые компоненты вибрации.
Рис. 5—19 приведены форма и спектр сигнала вибрации задней подшипниковой опоры электродвигателя в горизонтально — поперечном направлении. Хорошо заметны ударные импульсы, возникающие вследствие задеваний, наложенные на практически синусоидальную кривую вибрации и следующие с временным интервалом, соответствующим одному обороту. Один из импульсов помечен стрелкой. Следует отметить, что возбуждающаяся в момент задевания широкополосная случайная вибрация не проявилась в виде сколько-нибудь заметного возрастания шумовой компоненты на графике спектра, что бывает достаточно часто.
По мере нагрева участка ротора, касающегося статора нарастает прогиб и, соответственно, неуравновешенность ротора. Этот процесс может стать лавинообразным, особенно для крупных роторов, и потребовать экстренного
• Неуравновешенность ротора • 5 — 20

Рис. 5—16. Изменение в полярной системе координат амплитуды и фазы вибрации газовой турбины на частоте вращения ротора под влиянием разъединения посадки диска и переориентации теплового дисбаланса ротора.
Задевания.
Задевания, особенно в уплотнениях, одна из распространенных причин теплового изгиба ротора. Основные причины, приводящие к задеваниям, связаны с недостаточными радиальными зазорами, плохой центровкой уплотнительных колец, расцентровкой уплотнений при тепловых деформациях статорных узлов, большим начальным эксцентриситетом ротора, интенсивной (особенно низкочастотной) вибрацией статора или ротора, превышающей зазор в уплотнениях и др. Во многих случаях первоначальный тепловой прогиб вызывает усиление задеваний и повышение тепловыделения в местах контакта вследствие сухого трения.
• Неуравновешенность ротора • 5 — 18 •

Рис. 5—14.
Один цикл изменения в полярной системе координат амплитуды и фазы вибрации опоры электродвигателя на частоте вращения ротора под влиянием разъединения посадки и переориентации теплового прогиба ротора.
Эти же данные, воспроизводящие полный цикл переориентации теплового прогиба ротора, представленные в полярной системе координат (слева) и схема векторов (справа), приведены на рис. 5—14. А1 и А2 — вектора вибрации на частоте вращения ротора, которым соответствуют точки 1 и 2, DАm — вектор начальной механической неуравновешенности, которому соответствует точка 3, DА1 и DА2 — тепловые вектора. Вектор А1 заканчивается в точке 1 (амплитуда 13,6, фаза 30°), вектор А2 заканчивается в точке 2 (амплитуда 12,2, фаза 180°), вектор DАm заканчивается в точке 3 (амплитуда 6,1, фаза 110°), таким образом в точках с максимальной вибрацией, иначе в точках с максимальным тепловым прогибом, к вектору механической неуравновешенности за цикл добавляются поочередно тепловые почти антифазные вектора DА1 и DА2 .В промежуточных положениях величина теплового прогиба ротора и тепловых векторов меняется от нуля до максимума.
Изменение фазы вибрации на частоте вращения ротора не всегда сопровождается существенным изменением амплитуды вибрации. Иллюстрацией этому служит случай, связанный с нарушением горячей посадки облопаченного массивного диска газовой турбины, возникавшим в процессе эксплуатации вследствие нерасчетной температуры при нарушении охлаждения.
• Неуравновешенность ротора • 5—16 •
на частоте вращения ротора. Следует обратить внимание, что вектора вибрации разных опор на частоте вращения ротора при пуске агрегата могут и не бьпъ в противофазе, например, если имеются другие причины приводящие к вибрации на этой частоте, однако при нагреве изменение величины фазовых углов происходит в одну сторону с постоянным углом между векторами на частоте вращения ротора.
Диагностическим признаком асимметрии охлаждения является зависимость вибрации от интенсивности процессов теплообмена, или от разности температур между ротором и охлаждающим газом.
При этом вибрация меняется как при повышении нагрузки, так и в случае резкого изменения температуры охлаждающего газа. От температуры ротора вибрация при этом практически не зависит.
Тепловой дисбаланс у барабанных роторов может возникать из —за протечек пара или газа внутри роторов через неплотности в технологических заглушках и в сварке. При этом горячий газ нагревает ротор несимметрично в соответствии с расположением мест его входа и выхода, что приводит к тепловому прогибу ротора.
Тепловые деформации возникают при попадании масла в центральное отверстие ротора через неплотности заглушки. Масло засасывается за счет понижения давления внутри ротора при его охлаждении во время остановок и накапливается. Наконец его количество становится достаточным для конвективного теплообмена внутри ротора, при котором тепло переносится в осевом направлении от горячих поверхностей к холодным. Этот процесс может протекать несимметрично относительно оси и прогрессировать, вызывая увеличение вибрации.
Термическая нестабильность дисбалансов ротора.
Термической нестабильностью дисбалансов ротора называют изменение дисбалансов ротора вследствие изменения его температуры. Термическая нестабильность дисбалансов ротора может быть постоянной или временной. Например, по достижении критического числа пусков электродвигателя вследствие протекания в роторе пусковых токов, многократно превышающих номинальные или при некачественной термомеханической обработке ротора могут возникать остаточные напряжения, вызывающие перераспределение масс относительно оси ротора и его прогиба даже при совершенно равномерном прогреве. Для этих дефектов характерно изменение неуравновешенности ротора при изменении температуры ротора, независимо от причины изменения температуры. Например, амплитуда и/или фаза вибрации на частоте вращения ротора электродвигателя с таким дефектом будет непредсказуемо меняться при изменении нагрузки, т.е. токов в роторе, температуры охлаждающего воздуха, а иногда и масла подшипников и многих других, в том числе не поддающихся учету параметров.
Устранить такую причину вибрации агрегата возможно только термообработкой ротора или его заменой, поскольку балансировка положительных результатов во многих случаях не дает.
Таким же образом проявляются недостаточные осевые зазоры в пазовых клиньях роторов электрических машин, например, генераторов.
Разъединение (ослабление) посадки деталей ротора.
Разъединение (ослабление) посадки деталей, например, железа ротора, более часто встречается при работе электрической машины под нагрузкой, когда расширение пакета железа ротора происходит от выделенных в роторе тепловых потерь. Другая возможность — нерасчетное (недостаточное) охлаждение деталей ротора (массивных дисков). Обе эти причины за счет изгибов ротора и перекосов приводят к статической и моментной неуравновешенности ротора. Характерной чертой этих дефектов является циклическое изменение во времени амплитуды и/или фазы вибрации на частоте вращения ротора при неизменном режиме работы агрегата — постоянной нагрузке, давлении, температуре и др.
• Неуравновешенность ротора • 5-14 •

Рис. 5—12. Влияние нагрузки на характер изменения вибрации на частоте вращения ротора при тепловом, дисбалансе. А0 — вибрация на холостом ходу, А1 — вибрация при промежуточной нагрузке; а2 — вибрация при номинальной нагрузке; DА 1 , Dа2 — тепловые вектора.
Изменение вибрации происходит не одновременно с изменением активной нагрузки, а постепенно по мере изменения теплового состояния металла. Таким образом, например, изменяется величина амплитуды и/или фазы вибрации на частоте вращения ротора при пуске агрегата (двигателя) по мере нагрева ротора до рабочей температуры, а затем возможна стабилизация вибрации.
Другим важнейшим диагностическим признаком тепловой неуравновешенности ротора является существенный рост вибрации на первой
• Неуравновешенность ротора • 5-12 •

Рис. 5—11. Влияние корректирующей массы в районе возбудителя на спектры и частотные характеристики (на частоте вращения ротора) колебаний передней подшипниковой опоры электродвигателя магистрального насосного агрегата в горизонтально—поперечном направлении (до установки — графики с индексом 1, после графики с индексом 2).
В верхней части рис. 5— 11 приведены спектры виброскорости одной из контрольных точек электродвигателя до (графики с индексом 1) и после (графики с индексом 2) установки корректирующей массы в районе возбудителя. Вибрация: на частоте вращения ротора (помечена индексом гг) уменьшилась практически в два раза. В нижней части рис. 5—11 приведены частотные характеристики (зависимость СКЗ виброскорости на частоте вращения ротора от частоты вращения ротора) колебаний той же точки до и после балансировки при останове агрегата под нагрузкой. Вибрация на критической частоте ротора (примерно 2200 об/мин) также значительно уменьшилась.
У некоторых типов генераторов, электродвигателей и других узлов агрегатов, как и в приведенном выше случае, достаточно часто наблюдается
• Неуравновешенность ротора • 5-10 •
критической частотой вращения примерно 2200 об/мин и консольно расположенный возбудитель, см. схему на рис. 5 – 08.

Рис. 5—08. Схема валопровода и размещения контрольных точек магистрального насосного агрегата, и гармонический состав вибрации опор при дисбалансе в районе возбудителя. Снизу вперх первая (график 1), вторая (график 2) и третья (график 3) гармоники частоты вращения ротора, V, Н, А — вертикальные, горизонтально—поперечные и осевые компоненты вибрации.
На рис. 5 — 08 приведен гармонический состав вибрации подшипниковых опор. Наибольшая вибрация наблюдается на опорах электродвигателя, и максимальные значения имеют осевые компоненты, причем в частотном составе преобладает вибрация на частоте вращения ротора.
На рис. 5 — 09 приведены форма сигнала виброускорения и спектр сигнала виброскорости контрольной точки с максимальным уровнем вибрации — задней подшипниковой опоры электродвигателя в осевом направлении. Уровень преобладающей на частоте вращения ротора вибрации (помечена индексом fr) превышает уровни вибрации второй и третьей гармоник частоты вращения ротора примерно в 10 раз (20 дБ), а уровень шумов примерно на 40 дБ.
Кривую (форму сигнала) виброускорения периодической назвать нельзя, однако высокочастотные составляющие вибрации относительно невелики.
В продолжение интервала времени, соответствующего одному обороту ротора (вертикальные пунктирные линии через каждые 20 мс) на кривой виброускорения наблюдается один следующий от оборота к обороту почти периодически расположенный преобладающий максимум, хотя и изменяющийся по величине (помечен наклонными стрелками).
Исходя из характера имеющейся вибрации и опыта эксплуатации этого типа синхронных электродвигателей было высказано предположение о возможном дисбалансе возбудителя и было предложено провести балансировку на месте под нагрузкой.
• Неуравновешенность ротора • 5 —8 •
дисбаланс в результате ошибки специалиста по балансировке или ошибка ремонтного персонала, приведшая к вероятной деформации ротора при монтаже или транспортировке.
Следует отметить, что весьма важно проводить виброизмерения непосредственно перед выводом агрегата в ремонт, и, по возможности (если нет необходимости замены изношенных частей ротора), проводить балансировку только в случае необходимости, обоснованной наличием диагностических признаков дисбаланса и повышенной вибрации агрегата, т.е. не балансировать ротор без особой нужды. Важно также фиксировать случаи установки значительных корректирующих масс при балансировке и, при этом, удовлетворительного вибросостояния агрегата до вывода в ремонт и анализировать причину таких фактов.
Диагностирование и оценка технического состояния ротора по величине неуравновешенности, которая во многих случаях определяет уровень вибрации узлов агрегата на частоте вращения ротора, достаточно простой и, поэтому, широко применяемый способ мониторинга. В этом случае известно или легко определимо пороговое значение величины неуравновешенности, превышение которой означает отказ агрегата. При этом характер вибрации агрегата зависит от расположения дисбаланса: с одной стороны ротора, в середине или по краям или на консоли, что хотя и важно для решения задач балансировки, при потере работоспособности агрегата существенного значения не имеет.
Следует учитывать, что использование количественных характеристик вибрации на частоте вращения ротора в качестве диагностического признака места расположения дисбаланса на роторе во многих случаях бывает затруднено из —за значительного разброса их значений во времени и по множеству агрегатов, особенно не имеющих достаточно развитой неуравновешенности в силу многих, часто не поддающихся учету факторов.
Учитывая изложенное выше, авторы все же считают необходимым привести пример влияния расположения дисбаланса на валопроводе на вибрацию опор агрегата, измеренную в процессе эксплуатации оборудования.
На рис. 5 — 07 приведены вертикальные, горизонтально — поперечые и осевые компоненты вибрации опор насосных агрегатов одного типа, времени выпуска и условий эксплуатации при различном расположении дисбаланса. Данный тип агрегатов имел жесткие ротора насоса и двигателя. Доля первой гармоники частоты вращения ротора, характеризующая уравновешенность ротора, в любой из контрольных точек, составляла не менее 80% общего гармонического состава.
Верхний график (совокупность данных измерения вибрации и плоскость расположения дефекта, помеченные индексом 1) был получен перед остановом электродвигателя, в результате ревизии которого были обнаружены деформированные лопасти крыльчатки (см. схему). Наибольшая вибрация наблюдается в районе задней опоры электродвигателя.
Данные измерения вибрации с индексом 2 были измерены на электродвигателе, имевшем распределенный вдоль бочки ротора дисбаланс в результате дефекта пазовой изоляции.
Данные измерения вибрации с индексом 3 были измерены на агрегате, у которого дисбаланс зубчатой полумуфты со стороны электродвигателя возник в результате нарушения технологии изготовления и сборки соединительной муфты.
• Неуравновешенность ротора • 5 —6 •
В качестве примера проявления неуравновешенности жесткого ротора при выводе агрегата из ремонта, сопровождающейся повышенной вибрацией непосредственно по завершении ремонта и/или монтажа оборудования, можно привести следующий.
В соответствии с планом — графиком проведения ремонтных работ после наработки установленного количества часов ротор насоса магистрального насосного агрегата был демонтирован, отремонтирован, отбалансирован на станке и смонтирован в насосе. В ходе испытаний при выводе агрегата из ремонта была обнаружена вибрация, превышающая допустимое значение в несколько раз. Результаты проведенного после ремонта обследования приведены на рис. 5 — 04.

Рис. 5—05. Спектры вибрации передней и задней подшипниковых опор насоса под влиянием неуравновешенности ротора.
Очевидно, что дефект, приводящий к повышенной вибрации связан с насосом. Колебания опор насоса преобладают в горизонтально — поперечном
• Неуравновешенность ротора • 5 —4 •
достаточно интенсивной средне— и высокочастотной и случайной вибрации (во многих случаях возбуждаемой даже исправными подшипниками качения и другими источниками) и наглядней проявляющейся в сигнале виброускорения, чем виброскорости.

Рис. 5—03. Форма и спектр сигнала вибрации подшипникового щита электродвигателя, имевшего неуравновешенность ротора.
В амплитудном спектре вибрации составляющая на частоте вращения ротора является преобладающей и, в большинстве случаев, ее величина, при отсутствии других, кроме дисбаланса дефектов, значительно (в два и более раз) превышает величину вибрации на ее высших гармониках, а уровень шумовых компонент спектра на 40...50 дБ.
В качестве примера на рис. 5 — 03 приведен спектр виброскорости подшипникового щита небольшого электродвигателя, имевшего неуравновешенность ротора. Стрелками помечены гармоники частоты вращения
• Неуравновешенность ротора • 5 —2 •
Дисбаланс, связанный с прогибом (во многих случаях остаточным) вала, также может вызываться дефектами изготовления (остаточные деформации, неоднородность поковки вала, тепловая нестабильность в электрических машинах и др.), дефектами монтажа (в торцевых гаечных соединениях, перекосы в шпоночных соединениях, нарушение натяга дисков и др.) и дефектами эксплуатации (задевания, в результате неравномерного охлаждения или нагрева ротора или нарушения зазоров, нарушений режима пуска и др.).
Статическую неуравновешенность ротора может вызывать, например, нарушение соосности бочки и шеек ротора, прогиб ротора, различие в массе одинаковых диаметрально противоположных элементов (пример: полюсов синхронных машин или секций обмоток якоря), смещение масс пропиточного лака при сушке и др.
Причиной моментной неуравновешенности могут быть перекосы насаживаемых на вал узлов: коллектора, контактных и бандажных колец, рабочих облопаченных колес и многие другие причины.
Диагностические признаки неуравновешенности ротора.
Траектория движения ротора в подшипнике при неуравновешенности ротора в большинстве случаев имеет форму эллипса, а не круга, что связано с различной жесткостью подшипника в вертикальном и горизонтально — поперечном направлениях. На рис. 5 — 01 приведена типичная траектория движения шейки ротора в подшипнике скольжения при дисбалансе, при этом отношение размахов виброперемещений в вертикальном и горизонтально — поперечном направлениях примерно соответствует отношению жесткостей подшипника в тех же направлениях.

Рис. 5—01. Траектория движения шейки вала в подшипнике скольжения при дисбалансе.
Кривые (формы сигнала) виброперемещения и виброскорости при неуравновешенности ротора и отсутствии других развитых дефектов агрегата во
• Методология нормирования вибрации и распознования состояния оборудования • 4 —21 •

· для агрегатов с опорными подшипниками качения см. данные, приведенные в таблице 4-6 ;

В качестве исходной величины допустимых значений для заполнения таблицы выбирается клетка со значением "1". В эту клетку подставляется допустимое значение СКЗ виброскорости, регламентируемое требованиями завода —изготовителя, отраслевыми РД или стандартами России в зависимости от частоты вращения ротора, высоты оси вращения, мощности, массы ротора или других характеристик агрегата. Значения виброскоростей в остальных клетках таблицы получаются путем умножения коэффициента, помещенного в соответствующей клетке на подставленное в клетку "1" значение.
При возможности авторы настоятельно рекомендуют устанавливать дополнительные частотные полосы контроля вибрации, связанные с газо— и гидродинамическими дефектами (лопаточные частоты), дефектами подшипников качения, дефектами зубчатых соединений и др.
Предварительные (начальные) допустимые значения в этих полосах могут быть установлены не выше значений в полосе, включающей 10 гармонику частоты вращения ротора.
В дальнейшем, по мере накопления сведений об особенностях вибрации конкретного оборудования, следует разделить агрегаты по типам и подвергнуть полученные данные статобработке для определения индивидуальных частотных полос и допустимых значений для типа или даже для конкретного агрегата. Только после проведения этой работы достоверность автоматизированной оценки состояния оборудования будет достаточно высока. Опыт показывает, что экономия времени при автоматизированном распознавании состояния оборудования в этом случае с лихвой покрывает трудозатраты на предварительную статобработку.
• Методология нормирования вибрации и распознования состояния оборудования • 4 —19 •
Другая крайность — применение единого (единственного) набора критериев и предельных значений для оценки состояния всего парка оборудования предприятия. В этом случае чувствительность системы мониторинга к изменению вибросостояния агрегата хотя и выше, чем при оценке состояния агрегата по общему уровню вибрации, но неоптимальна.
Каждый специалист, исходя из специфики предприятия и собственного опыта, должен выбирать компромиссное решение между трудозатратами на выполнение работ по статобработке виброданных, коррекцией в базе данных критериев, частотных полос и предельных значений с одной стороны, и чувствительностью системы к изменению состояния оборудования с другой.
При развертывании системы вибромониторинга на предприятии или расширении системы на неохваченные мониторингом агрегаты возникает необходимость предварительного выбора критериев, частотных полос и предельных значений в полосах. Приведенное выше исследование имело целью оптимизацию критериев, количества частотных полос предельных значений на начальном этапе вибромониторинга на предприятии.
Частотные полосы вибрации при организации вибромониторинга.
С точки зрения авторов, основанной на приведенном выше исследовании, при выборе критериев и частотных полос для мониторинга состояния роторных агрегатов на начальном этапе (при развертывании системы вибромониторинга) рекомендуется пользоваться данными, приведенными в таблице 4 — 4 (сокращения: ПСА — подшипник скольжения, ПК — подшипник качения).

Для мониторинга вентиляторов, компрессорных и насосных агрегатов с частотой вращения ротора 25...50 Гц и подшипниками скольжения оптимально проводить в частотной полосе с нижним пределом измерений виброскорости 2 Гц (при применении вибродатчиков со щупами от 10 Гц) и верхним пределом,
• Методология нормирования вибрации и распознования состояния оборудования • 4 —17 •
этой группе компрессоров проявляется в основном на первых трех гармониках
частоты вращения ротора.

Рис. 4—11. Пример гармонического состава вибраций группы центробежных насосов одного типа.
На рис. 4—11 приведены границы распределения вибраций свыше 85% ("предупреждение") и 95% ("опасность") совокупности данных измеренных 56 центробежных насосах мощностью 150...250 кВт с подшипниками качения. Для этой группы насосов примечательна виброактивность в частотных полосах 1—5, 6— 10 и 11—40, а также присутствие некоторой виброактивности на лопаточных частотах.
На рис. 4—12 приведены (усредненные по трем направлениям измерений вибрации на корпусе подшипника) границы распределения вибраций свыше 85% ("предупреждение") и 95% ("опасность") сходных по конструктивным (примерно одинаковые подшипники, муфты и др.), эксплуатационным и мощностям характеристикам групп центробежных компрессоров (1), асинхронных электродвигателей (2) центробежных насосов (3), воздушных вентиляторов(4) расположенные в порядке возрастания значений вибротревог. Очевидно, что величина граничных значений существенно зависит от типа агрегата.
Анализ вибрации позволил установить как повышенный уровень колебаний отдельных опор в определенных направлениях у однотипных агрегатов, так и неравномерное распределение вибрации в различных направлениях у различных типов агрегатов: это событие достаточно распространенное, хотя и не является правилом. Во многих случаях статистический анализ данных показывает, что уровень вибрации в вертикальном направлении несколько меньше чем в горизонтальном, а осевая вибрация у большей части электродвигателей вентиляторов и самих вентиляторов в большинстве случаев преобладала над вертикальной и горизонтальной, чего не наблюдалось у ЦКМ.
• Методология нормирования вибрации и распознавания состояния оборудования • 4—15 •
• СКЗ виброскорости в низкочастотной области (область 2 Гц ... 0,9fr), (индекс S);
• СКЗ виброскорости в полосе частот, включающей каждую из первых десяти гармоник частоты вращения ротора ([n — 0,5...n + 0,5] fr, где n —номер гармоники), (индексы 1,2,3,4,5,6,7,8,9,10);
• СКЗ виброскорости в полосе частот, включающей с 1 по 5 гармоники частоты вращения ротора (0,5...5,5 fr), (индекс 1—5);
• СКЗ виброскорости в полосе частот, включающей с 6 по 10 гармоники частоты вращения ротора (5,5...10,5 fr), (индекс 6—10);
• СКЗ виброскорости в полосе частот, включающей с 11 по 40 гармоники частоты вращения ротора (10,5...40 fr) (индекс 11—40).
При анализе было установлено, что у большинства исследованных типов агрегатов и их узлов наблюдаются разные уровни вибрации опор по разным направлениям, а также существуют различия в гармонической активности. Кроме того вибрации узлов с одинаковой мощностью и частотой вращения также различается.

Рис. 4—08. Пример гармонического состава вибраций группы электродвигателей одного типа.
В качестве примера на рис. 4 — 08 приведены границы распределения вибраций свыше 85% ("предупреждение") и 95% ("опасность") совокупности данных измеренных на 80 асинхронных ЭД мощностью 150...250 кВт с подшипниками качения. Налицо существенные отличия границ — как по гармоникам, так и по направлению измерения. Можно отметить существенную виброактивность в горизонтально — осевом направлении.
• Методология нормирования вибрации и распознавания состояния оборудования • 4—13 •
Таблица 4—3.
Измерение |
Параметр |
||||||
СКЗ |
Пар.1 |
Пар.2 |
Пар.З |
Пар. 4 |
Пар. 5 |
Пар. 6 |
|
НПС 1 |
|||||||
НА1 -V1 - 20.03.95 - 16:32 |
3.807 |
0.738 |
2.691 |
0.409 |
0.623 |
2.443 |
|
НА1 -V1 -11.04.95-15:47 |
4.812 |
0.651 |
2.716 |
0.633 |
3.101 |
1.383 |
6.156 |
НА1 -V1 -26.10.95- 10:26 |
6.263 |
0.129 |
1.315 |
3.77 |
0.085 |
7.375 |
|
НА4- V1 -20.03.95- 16:52 |
2.422 |
0.512 |
1.786 |
1.011 |
0.293 |
1.067 |
|
НА4- V1 -11.04.95- 16:22 |
4.49 |
0.496 |
1.432 |
0.648 |
3.696 |
1.017 |
3.219 |
НА4 - V1 - 30.05.95 - 13:59 |
2.827 |
0.332 |
1.873 |
1.178 |
1.451 |
0.881 |
1.875 |
НА4 - V1 - 20.06.95 - 12:59 |
2.51 |
0.233 |
1.935 |
0.936 |
1.098 |
0.58 |
1.688 |
НА4 - V1 - 02.07.95 - 12:48 |
4.525 |
0.409 |
1.935 |
0.98 |
3.721 |
0.924 |
3.266 |
НА4 - V1 - 24.07.95 - 14:33 |
2.923 |
0.194 |
1.997 |
1.774 |
0.874 |
0.682 |
2.078 |
НА4 - V1 - 20. 10.95 - 15:26 |
2.541 |
0.2 |
1.935 |
0.471 |
1.017 |
1.141 |
1.914 |
НА4- V1 -30. 10. 95- 14:20 |
2.348 |
0.15 |
1.898 |
0.484 |
0.961 |
0.85 |
1.688 |
НА4-V1-13.11.95-13:15 |
4.32 |
0.245 |
2.022 |
0.623 |
3.473 |
0.924 |
1.555 |
НА4- V1 -08. 12. 95-05:30 |
3.061 |
0.276 |
1.687 |
0.251 |
1.873 |
1.6 |
2.078 |
НПС 2 |
|||||||
НА4- V1 -20.03.95- 15:42 |
2.785 |
1.104 |
0.812 |
0.881 |
1.575 |
||
НА4- V1 -11. 04. 95- 14:29 |
3.67 |
0.515 |
2.406 |
0.747 |
1.271 |
2.084 |
0.563 |
НА4- V1 -30.05.95- 14:08 |
4.56 |
0.419 |
3.001 |
0.305 |
0.626 |
3.299 |
1.242 |
НА4 - V1 - 02.06.95 - 14: 19 |
3.605 |
0.899 |
1.898 |
0.592 |
2.294 |
0.732 |
3.906 |
НА4- V1 -31. 10.95- 14:52 |
5.485 |
0.667 |
2.195 |
0.38 |
3.721 |
3.175 |
1.555 |
Среднее арифм. (хср) |
3.719 |
0.415 |
2.030 |
0.752 |
1.930 |
1.357 |
2.677 |
Дисперсия (s) |
1.112 |
0.219 |
0.453 |
0.381 |
1.252 |
0.851 |
1.812 |
Верхняя гр. (хмакс,tb = 1,5) |
5.387 |
0.744 |
2.71 |
1,323 |
3,808 |
2,634 |
5.395 |
Верхняя гр. (хмакс,tb = 2) |
5,943 |
0.853 |
2.936 |
1,514 |
4,434 |
3,059 |
6.301 |
Верхняя гр. (хмакс, tb = 3) |
7.056 |
1.074 |
3.391 |
1.898 |
5.687 |
3.913 |
8.114 |
хср
+ 4 Дб: |
5.895 |
0.658 |
3.217 |
1.193 |
3.059 |
2.152 |
4.243 |
хср
+ 8 Дб: |
9.336 |
1.043 |
5.095 |
1.889 |
4.844 |
3.408 |
6.719 |
хср
+ 12 Дб: |
14.80 |
1.654 |
8.079 |
2.995 |
7.682 |
5.404 |
10.65 |
Для определения точности, с которой эти оценки отражают искомую статистическую характеристику, следует определить верхние границы доверительного интервала оценок:

где хср — среднее арифметическое результатов измерений; а — дисперсия результатов измерений; tb — число квадратических отклонений, которое нужно отложить вправо от центра рассеивания для того, чтобы вероятность попадания в полученный интервал значений была равна р. При подсчетах выбиралась
доверительная вероятность b = 0,95 и b = 0,85, чему соответствовало tb примерно равно 2 и 1,5.
Сопоставление верхней границы доверительного интервала и распределения частот встречаемости вибраций опор по каждому компоненту колебаний однотипных агрегатов показало, что подавляющее большинство значений вибраций находятся в границах доверительного интервала.
• Методология нормирования вибрации и распознавания состояния оборудования • 4—11 •
Граница нормального состояния определяется обычно на 4 дБ выше исходного (или средне —нормального), или по сумме средне — нормальной величины и дисперсии, взятой с некоторым коэффициентом.
Выбор того или иного типа определения границы нормального состояния зависит от статистического разброса данных замеров.
Методология определения допустимых значений вибрации и частотные полосы.
Авторами и их коллегами было проведено исследование вибрации 630 различных агрегатов нескольких предприятий Минтопа и МНХП, в результате чего была составлена база данных включающая 8455 спектров вибрации 16 различных типов ЦНА, 5676 спектров вибрации 14 типов ЦКМ и 2748 спектров вибрации 10 типов ЦВ.
При обработке экспериментальных данных (для получения упорядоченных статистик значений вибраций в предположении, что одинаковые компоненты колебаний одних и тех же подшипников однотипных агрегатов принадлежат соответственно единым генеральным совокупностям) для формирования сводных протоколов значений параметров в базе данных выбирались группы агрегатов со сходными техническими характеристиками и одноименные измерительные точки.
В первую очередь из данных, предназначенных для анализа, были исключены вызывающие сомнение в их достоверности. Для проверки компактности выборки, характеризующей достоверность статистических выводов, и исключения из дальнейшей обработки резко выпадающих данных, связанных с ненормальной работой отдельных исследованных агрегатов, целесообразно использовать критерий грубых ошибок наблюдений при допущении, что полученный экспериментальный ряд значений вибраций (выборка) подчиняется нормальному законы распределения, при этом верхнюю границу допустимых результатов измерений можно определить из выражения

где хср — среднее арифметическое результатов измерений; s — дисперсия результатов измерений; qq,n — квантиль распределения величины, взятый из таблиц для уровня 99% (qq,n =3).
Расчеты и анализ проверки компактности выборки осуществлялись в автоматизированном режиме с применением программ "MasterTrend" фирмы СSI и обработки статданных, разработанной СП "Дельфин —Диагностика". При этом была исключена возможность ошибок при ручных расчетах, и реализовывалась возможность редактирования исходных данных в ручном режиме (например, исключать данные соответствующие измерениям на агрегатах, работающих не в нормальных условиях или вызывающих сомнение в их достоверности) и выводить итоговый протокол расчета. Программа проводила расчеты по приведенной выше формуле в автоматическом режиме, и при этом на экран выводились значения по соответствующим данным: среднего арифметического, дисперсии, суммы среднего арифметического и утроенной дисперсии, уровней +4, +8 и + 12 дБ относительно среднего. После окончания работы программы проводилась ручная корректировка данных.
В приведенном ниже примере (см. таблицы 4 — 2 и 4 — 3) произведено исключение вызывающих сомнение данных и расчет предварительных допустимых значений вибрации по данным измерений вибрации магистральных насосных агрегатов (НА) СТД—8000/НМ—12000 двух нефтеперекачивающих станций (НПС) для измерительных точек V1 (задний подшипник электродвигателя, вертикальное направление).
• Методология нормирования вибрации и распознавания состояния оборудования • 4 — 9 •
на лопаточной частоте насоса говорит о нарушении гидродинамики потока, на дробных гармониках частоты вращения ротора о нарушениях жесткости и т.д. Таким образом производя разбиение частотного диапазона измерений на сравнительно узкие, возможно перекрывающиеся частотные полосы и применяя индивидуальные для каждой полосы допустимые значения и критерии (см. рис. 4 — 04) можно распознавать появление ряда зарождающихся дефектов.

Рис. 4—04. Спектр виброскорости, разделенный на 7 частотных полос с индивидуальными допустимыми значениями.
Индивидуальные допустимые значения в частотных полосах могут быть установлены как для "высокоэнергетических" составляющих колебательного процесса, сопровождающих дисбаланс или расцентровку (обычно диапазоны 0.5...1.5 fr и 1,5...2,5 fr), так и для сравнительно "низкоэнергетических" составляющих колебательного процесса, сопровождающих дефекты подшипника качения (обычно диапазон 7,5...15,5 fr). Другие полосы могут быть размещены для предупреждения о нарушениях жесткости (обычно диапазон 2,5...10,5 fr), "масляных" дефектов подшипников скольжения (диапазон 0,1...0,9 fr), зубчатых муфт и зубчатых передач, электрических дефектов электроприводов и др. В общем случае, распознавание состояния по частотным полосам является (как модифицированный метод оценки состояния оборудования по огибающей спектра) наиболее точным и надежным среди других, поскольку обладает рядом достоинств метода огибающей и лишен некоторых ее недостатков.
Перед приобретением того или иного пакета программ по вибромониторингу необходимо тщательно изучить его возможности, поскольку многие программные пакеты не содержат возможности установки допустимых значений по выбранной частотной полосе.
Использование современных компьютерных систем мониторинга технического состояния оборудования (например, пакет "MasterTrend" фирмы
• Методология нормирования вибрации и распознавания состояния оборудования • 4 — 7 •
опытных специалистов по вибродиагностике используют оценку состояния агрегата по общему уровню вибрации только для дополнения более чувствительных способов оценки состояния.

Рис. 4—03. Тренды СКЗ виброскорости опоры подшипника ЭД в частотных полосах 10... 1000 и 250...500 Гц.
Вышеизложенное позволяет сделать вывод о невысокой степени достоверности распознавания состояния агрегатов только по общему уровню вибрации.
При использовании современных цифровых виброанализаторов и ЭВМ возможен мониторинг состояния оборудования по уровню вибрации в частотной полосе произвольно заданной ширины и установки индивидуальных допустимых значений вибрации для каждой измерительной точки конкретного агрегата.
Таким образом недостатки, изложенные выше, казалось бы можно исключить, особенно если наблюдается возрастание уровня вибрации от измерения к измерению.
Оценка состояния по огибающей спектра вибрации.
Этот метод определения состояния агрегата основан на диаметрально противоположном (по сравнению с определением по допустимым значениям общего уровня вибрации) способе сравнения текущих параметров вибросигнала с допустимыми значениями: уровень вибрации на каждой частотной составляющей текущего спектра вибрации сравнивается с уровнем соответствующей составляющей "опорного" ("эталонного") спектра. В качестве опорного (эталонного) спектра обычно выбирается огибающая, совпадающая, например, с линиями 400 — линейного частотного спектра. Опорный (эталонный) спектр можно построить двумя способами: подвергнуть статистической обработке ряд измерений
• Методология нормирования вибрации и распознавания состояния оборудования • 4 —5 •
Оценка состояния оборудования по пиковому или среднеквадратическому значению виброскорости (виброперемещения) во всем частотном диапазоне измерений имеет три существенных недостатка:
• никак не могут быть учтены вибрационные проявления технологических и режимных отклонений при эксплуатации оборудования;
• уровень вибрации обычно определяется в фиксированной полосе частот (для большинства виброметров в полосе от 10 Гц до 1 кГц), что, иногда, в принципе не может обеспечить достаточно высокую степень чувствительности параметра на начальной стадии развития дефекта.
• допустимые (предельные) значения вибрации обычно определяются на основе статистического анализа вибросостояния групп оборудования или однотипных агрегатов при нормальных эксплуатационных условиях и установлены одинаковыми для всего класса подобных агрегатов, в то время, как имеются экспериментальные данные о том, что одинаковые дефекты даже на однотипных машинах могут возбуждать на корпусе и подшипниках вибрации, уровни которых могут различаться в 100 раз (40 дБ), за счет различия значений конструкционных передаточных функций.
Однако, самым важным недостатком оценки состояния оборудования по общему уровню вибрации является то, что он практически нечувствителен к изменениям сравнительно низкоуровневых частотных составляющих (составляющих с малыми энергиями в колебательном процессе) вибросигнала, характерных, например, для ряда зарождающихся и развивающихся дефектов подшипников качения, зубчатых передач, электрических и ряда других дефектов.

Рис. 4—01. Тренд СКЗ виброскорости в вертикальном направлении подшипника электродвигателя в частотном диапазоне 10...1000 Гц.
Если оценка состояния агрегата по общему уровню вибрации нацелена на детектирование высокоэнергетических развитых дефектов, таких как нарушение
• Методология нормирования вибрации и распознавания состояния оборудования • 4 - 3 •
сдаточных, периодических, квалификационных, типовых и приемочных испытаниях регламентирует определять:
• для электрических машин с частотой вращения 600 об/мин и выше среднее квадратическое значение виброскорости опор подшипников,
• для электрических машин с частотой вращения менее 600 об/мин пиковое значение виброперемещения,
допустимые значения которых приведены в таблице 4 — 2.
Таблица 4—2.
Частота вращения, об/мин |
Среднее квадратическое значение виброскорости Ve ,мм/с |
|
Способ установки |
||
Упругая подвеска |
Жесткое закрепление |
|
От 600 до 1800 |
2,8 |
2,8 |
Свыше 1800 до 3600 |
4,5 |
2,8 |
Для осевой составляющей вибрации подшипников, не являющихся упорными |
4,5 |
4,5 |
Допустимое значение виброскорости сердечника статора |
4,5 |
4,5 |
Пиковое значение виброперемещения опор подшипников, мкм |
||
Менее 600 |
50 |
50 |
Практически в каждой отрасли разработаны и применяются собственные нормативно — методические рекомендации. Например, Методические рекомендации по проведению диагностических виброизмерений центробежных компрессорных машин и центробежных насосных агрегатов предприятий Министерства химической и нефтеперерабатывающей промышленности (РДИ, утверждены 28.11.91), рекомендуемые в качестве методического документа для руководства при организации вибродиагностики на поднадзорных предприятиях Государственным комитетом по надзору за безопасным ведением работ в промышленности и горному надзору (Госгортехнадзор России, письмо Nо 04 — 35/54 от 20.05.92) предписывают оценку технического состояния узлов ЦКМ по интенсивности абсолютной вибрации корпусов подшипников (Центробежные компрессорные агрегаты, нормы вибрации) определять в соответствии с таблицей 4 — 3.
Таблица 4—3.
Интенсивность вибрации, СКЗ виброскорости (мм/с) |
Оценка технического состояния |
|||
Паропривод |
Электро - привод |
Мульти -пликатор |
Компрессор |
|
до 1,8 |
Отлично |
Отлично |
Отлично |
Отлично |
св. 1,8 до 2,8 |
Хорошо |
Хорошо |
||
св.2, 8 до 4,5 |
Допустимо |
Хорошо |
Хорошо |
Допустимо |
св. 4, 5 до 7.1 |
Требует принятия мер |
Допустимо |
Допустимо |
|
св.7,1 до 11,2 |
Недопустимо |
Требует принятия мер |
Требует принятия мер |
Требует принятия мер |
свыше 11,2 |
Недопустимо |
Недопустимо |
Недопустимо |
• Методология нормирования вибрации и распознавания состояния оборудования • 4 - 1 •
Методология нормирования вибрации и распознавания технического состояния оборудования
Мониторинг технического состояния оборудования, основанный на вибродиагностике, практикуется в различных отраслях промышленности несколько десятилетий. При этом используются многочисленные стандарты, в основе которых лежит нормирование вибрации в зависимости от мощности агрегата, массы и/или определенных частот вращения ротора агрегата, а также высоты оси вращения ротора и др. Поскольку методы ведения вибромониторинга постоянно совершенствуются, происходит периодическое изменение этих стандартов и их приложений.
В общем случае оценка состояния агрегата должна проводиться путем совместного учета всех вредных последствий, вызываемых вибрацией. Однако, в силу недостаточной изученности многих вопросов динамики машин, теоретически строгий вывод общего критерия оценки вибрации и сложность его использования для практического применения делают задачу труднореализуемой. При разработке норм эксплуатационного контроля вибрации в качестве критерия обычно используют один из кинематических параметров (виброускорение, виброскорость или виброперемещение), по которому оценивают техническое состояние агрегата.
Основная цель эксплуатационных норм вибрации оборудования — контроль его технического состояния в процессе эксплуатации, т.е. решение диагностической задачи: создание таких условий эксплуатации, при которых была бы создана возможность своевременного обнаружения любых, даже незначительных повреждений или ненормальностей, т.е. обнаружения повреждений на начальной стадии их возникновения (развивающихся дефектов). Решение этой задачи требует обеспечения минимального уровня вибрации агрегата.
Проблема нормирования вибрации включает решение четырех взаимоувязанных задач нормирования вибрации: опор подшипников, роторов, статоров (корпусов) и фундаментов и трубопроводных обвязок.
Разнообразие методов и критериев оценки состояния оборудования затрудняет сравнение различных отраслевых Руководящих документов и Стандартов.
Весьма характерно, что даже на родственных предприятиях (например, однотипных установках различных НПЗ) специалисты по вибродиагностике нередко применяют для однотипных агрегатов различные критерии для контроля вибрации, не говоря уж об отсутствии близких по величине норм. В некоторых случаях это свидетельствует о том, что существующие отраслевые Руководящие документы и Стандарты не отвечают требованиям специалистов по вибродиагностике промышленных предприятий и последние вынуждены самостоятельно, исходя из накопленного опыта, устанавливать критерии и нормы, соответствующие требованиям конкретного оборудования, и оптимизировать их по мере накопления опыта.
• Организация периодического мониторинга технического состояния оборудования • 3 — 21 •
ЧП, на постоянном устранении проблем с оборудованием и на достижении или
даже превышении установленной изготовителем максимальной
производительности оборудования. На предприятии проводится независимый от
администрации полномасштабный мониторинг технического состояния
практически всего парка энергомеханического оборудования при небольшом
количестве зависимого однособытийного анализа состояния оборудования,
запрашиваемого администрацией.
Оценка экономической эффективности ОНМО.
Результаты и преимущества, получаемые от внедрения программы ОНМО, обеспечивают не только значительное повышение прибыли и надежности страхования предприятия, но и множество нематериальных выгод, таких как престиж предприятия, удовлетворение клиентов и уважение поставщиков, гордость рабочих и ИТР.
Для получения, сохранения и оправдания всемерной поддержки ОНМО со стороны администрации предприятия, необходимо тщательное документирование результатов программы и функционально — стоимостной анализ мероприятий ОНМО. Функционально — стоимостной анализ — это исследование полезного эффекта создаваемой продукции, приходящегося на единицу затрат с целью оптимизации технических решений и значений параметров продукции или ее составных частей. В данном случае под продукцией понимается сама программа ОНМО.
С первого шага реализации программы ОНМО следует утвердить, на уровне руководителя предприятия показатели (индексы), по которым будет происходить оценка ее действенности, и обеспечить регистрацию этих показателей заинтересованными службами предприятия.
Ниже приведены потенциальные показатели для проведения функционально — стоимостного анализа, которые могут быть утверждены к использованию администрацией предприятия:
• среднемесячные (среднегодовые) эксплуатационные затраты по службе ремонта;
• объем (стоимость) производимой ежемесячно продукции;
• затраты на техническое обслуживание, отнесенные к себестоимости продукции;
• объем (стоимость) производимого брака (отходов) ежемесячно;
• процент стоимости отходов или брака в себестоимости произведенной продукции;
• межремонтный интервал (средний, по производствам, по критическим агрегатам), как функция от общего времени использования;
• процент времени использования оборудования по отношению к общему полезному времени;
• процент сверхурочной работы по отношению к общему рабочему времени;
• процент внеплановой работы по отношению к общему рабочему времени;
• процент некачественно отремонтированного оборудования по результатам послеремонтных обследований;
• число машин, досрочно снятых с эксплуатации с подтвержденным при исследовании дефектом, ежемесячно;
• число отремонтированных машин, из досрочно снятых с эксплуатации с подтвержденным при исследовании дефектом, ежемесячно;
• фактический годовой экономический эффект от каждого метода ОФС;
• процент оборудования предприятия, охваченного программой ОФС;
• Организация периодического мониторинга технического состояния оборудования • 3—19 •
• оценка тенденций изменения межремонтных интервалов и ресурса оборудования для нужд возможной модернизации или замены оборудования и ведение и хранение паспортов (истории) агрегатов.
Группа обеспечения надежности (технической диагностики и мониторинга) все усилия сначала направляет на правильную организацию мониторинга технического состояния оборудования, и только спустя некоторое время, по мере развития группы, делает шаги в направлении проактивного обслуживания. Типичная группа обеспечения надежности вначале обычно состоит из одного или двух инженеров — мехников и одного или двух техников. Ее костяк следует составлять из инициативных, добросовестных и высококвалифицированных в ТО инженеров —механиков, способных учиться новым, передовым технологиям обслуживания, основанным на применении микропроцессорной техники и ЭВМ.
Предпочтительней, если группа будет набрана из имеющегося персонала предприятия, хорошо знающего и имеющего опыт работы с оборудованием, мониторинг которого будет проводиться, и затем тщательно обучена до уровня экспертов в области вибродиагностики.

Рис.3—11. Основные функции и структура службы по обеспечению надежности.
На этой стадии важность обучения нельзя недооценивать: грамотное обучение может сократить сроки внедрения программы ОНМО многократно, отсутствие обучения ставит под сомнение возможность реализации программы
• Организация периодического мониторинга технического состояния оборудования • 3—17 •
Кадровое обеспечение ПАО.
Опыт показывает, что производство всей гаммы работ по вибромониторингу, вибродиагностике и анализу причин внеплановых остановов (внезапных отказов), аварий, укороченных межремонтных интервалов, заключающееся в выявлении повторяющихся проблем, возникающих при эксплуатации оборудования, несовместимо для одного лица (инженера). Целесообразно в штат группы, занимающейся мониторингом технического состояния оборудования, включить высококвалифицированного и авторитетного на предприятии инженера — механика только для обеспечения задач ПАО, от энтузиазма которого во многом будет зависеть успех программы.
Программа обеспечения надежности механического оборудования.
Реализация программы ОНМО заключается в определении необходимого баланса объемов выполнения стратегий ППР, ОФС и ПАО.
Эти стратегии повышения надежности отнюдь не являются независимыми. Их рациональное совместное выполнение усиливает результат, компенсируя недостатки каждой из них, и приводит к достижению максимальной и стабильной производительности оборудования. Основой ОНМО является ОФС. Точная информация о состоянии механического оборудования, обеспечиваемая проведением вибромониторинга, делает возможным и рентабельным на основе функционально — стоимостного анализа правильный баланс ППР и ПАО. ОФС на основе вибромонниторинга — ведущая программа ОНМО — убедительный способ демонстрации того, что может быть достигнуто в случае успешного внедрения прогрессивной философии ТО. Кроме экономического, технического и информационного эффекта, который ОФС обеспечивает в достаточно короткий период, современные технические средства контроля и повышение квалификации специалистов, необходимые для осуществления ОФС, обеспечивают прочный фундамент для внедрения других программ ОНМО.

Рис.3—10. Классическая кривая, иллюстрирующая влияние наработки на вероятность отказа сложного оборудования.
• Организация периодического мониторинга технического состояния оборудования • 3—15 •
Принципиально дефекты и отказы (в т. ч. в начале срока службы), классифицируемые по причине возникновения, могут быть связаны с конструкторскими дефектами и неправильным применением, производственными дефектами (изготовления) и дефектами материала, дефектами сборки и эксплуатационными дефектами (нарушения технологии сборки, монтажа и соединения узлов, ненужное ТО, нарушения условий эксплуатации), технологическими дефектами (отклонение рабочих параметров от номинальных).
В качестве примера конструкторской ошибки при проектировании можно привести случай, связанный с недостаточным учетом влияния погодно — климатических условий при эксплуатации оборудования: непродуманная конструкция заградительной решетки воздухозабора воздушного компрессора газовой турбины пропанового центробежного компрессора обуславливала накопление и сброс частиц льда с последующим их периодическим попаданием в турбину, столкновением и ускоренным разрушением лопаток воздушного компрессора.
В качестве примера неправильного применения по вине проектировщика можно привести случай, связанный с периодическим, примерно каждые три месяца, выходом из строя подшипников качения ЭД вертикального насосного агрегата, имевшим место по окончании монтажа в продолжение гарантийной эксплуатации технологической установки. Первый выход из строя подшипника качения был воспринят как нормальное явление, однако после второго внезапного отказа провели анализ причин, в результате которого выяснилось, что опорно — упорный подшипник двигателя, в соответствии с техническими условиями завода —изготовителя, мог быть применим только при горизонтальной ориентации ротора. Издержки были компенсированы фирмой —поставщиком.
В качестве другого примера неправильного применения по вине проектировщика можно привести случай, связанный с необходимостью проведения ремонта каждые 6...9 месяцев винтовых компрессоров компримирования газа в газлифтной системе из —за изменения условий эксплуатации и отклонения рабочих параметров от номинальных по ТУ (эксплуатация на пределе производительности и давления). При анализе причин частых ремонтов оказалось, что для подобной задачи данный тип компрессоров принципиально непригоден и требует замены.
В качестве примера нарушения технологии изготовления деталей (дефект материала) можно привести случай, связанный с коротким сроком службы подшипников скольжения крупных агрегатов нефтехимзавода: примерно после 4000...6000 часов эксплуатации наблюдалось растрескивание и выкрашивание баббита вкладышей. В результате анализа установили, что причина — пережженный баббит в результате дефектной технологии изготовления вкладышей. Небольшая коррекция технологии привела к увеличению среднего срока службы вкладышей более чем в три раза.
Нередко повторяющаяся проблема с оборудованием, лежащая на поверхности, является симптомами более скрытого дефекта: на одном из предприятий подшипники редуктора крупного компрессорного агрегата после многолетней успешной эксплуатации вдруг каждые 2...3 месяца стали внезапно выходить из строя, приводя к внеплановому останову производства.
После проведения анализа персоналом завода было установлено, что причиной оказалось нарушение качества смазочного масла, повлекшее рост температуры подшипника, при этом параметры вибрации практически не превышали допустимых значений.
Безукоризненное соблюдение требований технических условий при монтаже и ремонте агрегата и исследование вибрации при выводе из ремонта могут значительно продлить последующий межремонтный интервал.
Например, две наиболее распространенные операции при завершении монтажа или ремонта агрегата (которые на вспомогательном оборудовании нередко выполняются с низким качеством или вообще игнорируются) —
• Организация периодического мониторинга технического состояния оборудования • 3—13 •
вибромониторинг и вибродиагностику, в случае добросовестного, обоснованного и систематического применения, обычно окупаются за 2...6 месяцев использования. Если предприятие обладает достаточно обширным парком оборудования, то, как правило, сначала группа вибродиагностики состоит из одного или двух специалистов, а плановые обследования распространяются только на самые ответственные и крупные агрегаты. Но спустя год или более, по мере нарастания экономического или технического эффекта от внедрения метода, а также приобретения положительного опыта от реализации программы ОФС, парк оборудования расширяется и на вспомогательное оборудование, именно на котором вибродиагностика и вибромониторинг наиболее эффективны.

Рис.3—08. Удельные эксплуатационные расходы для некоторых отраслей промышленности для основного оборудования.
Анализ эксплуатационных расходов показывает, что переход от "реактивного" обслуживания одного и того же парка оборудования к ППР приводит к снижению затрат в 1,5 раза, а к ОФС — почти в два раза. Это проиллюстрировано рис. 3 — 08: наиболее заметно сокращение удельных эксплуатационных расходов на ТО в нефтехимии и на транспорте, особенно в перекачке нефти и газа.
Таблица 3 - 02.
Метод |
Оборудование |
Вибродиагностика и вибромониторинг |
Энергомеханическое оборудование с движущимися деталями |
Акустико — эмиссионная диагностика |
Сосуды давления, резервуары, трубопроводы, несущие конструкции |
Трибодиагностика (анализ качества смазки (масла) и выявление частиц износа) |
Ответственное энергомеханическое оборудование, в том числе низкооборотное, трансформаторы |
Тепловидение и термография |
Электроэнергетическое оборудование, теплообменное оборудование, теплоизоляция, котлы, печи и др. |
Анализ токов и электроимпульсное тестирование |
Токопроводящая часть и изоляция ЭД, эксцентриситет |
Аэроультразвуковой контроль утечек (вакуумные утечки) |
Компрессионное оборудование |
Ультразвуковая дефектоскопия |
Состояние и толщина стенок трубопроводов, сосудов и резевуаров |
Параметрическая диагностика технологического процесса |
Технологическая или механическая деградация, коррозия стенок |
• Организация периодического мониторинга технического состояния оборудования • 3—11 •
профилактическое обслуживание широко применяется для всего парка оборудования предприятия, то существует высокая вероятность того, что выполняется большой объем работ по обслуживанию бездефектного оборудования, состояние которого на момент проведения ППР не требует проведения ремонта, но проводится с целью гарантировать безотказную работу в межремонтный интервал.
В настоящее время на многих предприятиях применяемся модифицированная система ППР, точнее симбиоз ППР и ОФС (ОФС описываемся далее). В частности, за 4...12 недель до запланированного срока проведения ремонта (технического обслуживания) агрегата по 52 — недельному плану—графику службой ремонта формируется и направляется запрос о его состоянии в группу (службу) Технической Диагностики (Поддержания Надежности). Если результаты проведенного службой ТД обследования показывают, что агрегат находится в исправном работоспособном состоянии и его компоненты нормально функционируют, техническое обслуживание может быть задержано (например, на шесть или двенадцать месяцев). Когда подходят сроки очередного обслуживания агрегата, процедура повторяется до тех пор, пока не будут обнаружены признаки приближения состояния к предельному.
Обслуживание по фактическому состоянию (ОФС).
Основная идея обслуживания по фактическому техническому состоянию состоит в устранении отказов оборудования путем применения методов распознавания технического состояния оборудования по совокупности его виброакустических характеристик, выявления имеющихся или развивающихся дефектов и определения оптимальных сроков проведения
![]() |
ремонтных работ.
Рис.3—07. Классический график изменения уровня вибрации в зависимости от наработки при локальном износе контактирующих поверхностей.
Техническая база ОФС основана на том, что существует взаимосвязь между возможными техническими неисправностями агрегата и диагностическими параметрами, которые молено контролировать.
Другими словами, большинство распознаваемых дефектов, которые могут возникать в агрегате, имеют определенные диагностические признаки и параметры, предупреждающие о том, что дефекты присутствуют, развиваются и могут привести к отказу. Диагностические признаки дефектов могут включать параметры вибрации, технологические и режимные параметры (температуру, нагрузку, давление, влажность и др.), частицы износа в смазке и т. д. В частности, при износе деталей наблюдается изменение уровня вибрации, см. рис. 3 — 07. Следовательно, проводя мониторинг различных параметров, характеризующих работу оборудования, можно вовремя обнаружить изменение технического состояния оборудования и провести техническое обслуживание только тогда, когда возникает реальная возможность ухода его параметров за недопустимые пределы, т.е. когда дальнейшая эксплуатация невозможна.
• Организация периодического мониторинга технического состояния оборудования • 3—9 •
обслуживание по фактическому состоянию, планово-профилактическое обслуживание и реактивное обслуживание.
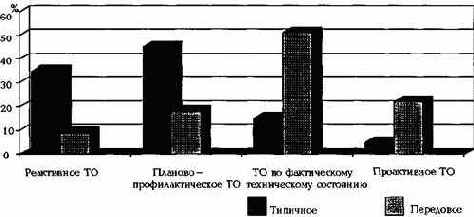
Рис.3—04. Процентное соотношение различных видов ТО (сумма — 100%) на "типичном" предприятии России и "передовом".
На рис. 3 — 04 отображена такая комбинация различных видов ТО, обычно сосуществующих на любом промышленном предприятии, причем каждая пара столбцов соответствует долям этого ТО в общем объеме работ ремонтной службы. Доли различных видов ТО определяются минимизацией затрат на производство продукции. Разница между типичным предприятием и предприятием, реализующим программу ОНМО, очевидна.
Остановимся подробнее на основных видах технического обслуживания оборудования.
Планово—профилактическое обслуживание.
Цель периодического планово — профилактического обслуживания состоит в исключении отказов оборудования и непредвиденных расходов (которые, например, могут произойти при реактивном обслуживании) путем планирования и проведения технического обслуживания ранее момента вероятного среднестатистического отказа.
Базисом деятельности служит обычно 52 —недельный план —график ТО, составляемый службой главного механика (ремонтной службой), которая определяет и отслеживает бюджет и основу повседневной деятельности служ:бы ремонта, а также выполняет многие другие административные функции, такие, как отслеживание списка и пополнение запасных частей для ТО, хранение истории агрегатов, функционально — стоимостной анализ обслуживания и др.
Планово — профилактическое обслуживание является сегодня одним из самых широко применяемых видов ТО, в первую очередь потому, что эта стратегия появилась ранее ОФС и ПАО и наиболее обеспечена методически. Несомненным достоинством планово — профилактического обслуживания является то, что оно обеспечивает более высокий уровень управления обслуживанием, выходящий за рамки реактивного обслуживания. Исследования и опыт работы в промышленности показали, что успешная программа ППР может обеспечить более чем 30% —ное снижение эксплуатационных затрат относительно расходов при реактивном обслуживании.
В процессе эксплуатации детали агрегата деградируют, приводя к постепенному или внезапному отказу (дефекту, изменению технического состояния). Другими словами, изменение технического состояния оборудования связано с постепенной деградацией его частей в результате естественного износа.
• Организация периодического мониторинга технического состояния оборудования • 3—7 •
Организация системы ТО предприятия.
Формы технического обслуживания оборудования.
В различных отраслях промышленности эксплуатационные затраты составляют от 6 до 18% стоимости конечной продукции (см. рис. 3 — 03). Их величина бывает сравнима с прибылью предприятия, особенно в области транспорта, в том числе трубопроводного транспорта нефти и газа.

Рис.3—03. Доля эксплуатационных затрат в стоимости конечной продукции по различным отраслям промышленности.
Опыт показывает, что эксплуатационные затраты являются одной из наиболее регулируемых статей затрат предприятия, и снижение эксплуатационных затрат в итоге повышает производительность.
Последствия нестабильной работы оборудования проявляются в срыве производственной программы, ухудшении качества и, что самое важное, уменьшении прибыли. Важнейшим резервом снижения эксплуатационных затрат, обеспечения безопасности персонала и сохранности оборудования является совершенствование структуры технического обслуживания оборудования предприятий.
Применяемые в настоящее время виды технического обслуживания оборудования описаны ниже.
Реактивное ("реагирующее") техническое обслуживание — такой метод обслуживания, при котором ремонт или замена оборудования производится только в том случае, когда оно выходит из строя или вырабатывает свой ресурс. Реактивное ("реагирующее") обслуживание имеет следующие недостатки: возможность внеплановых простоев из —за внезапных отказов оборудования и дорогостоящий и продолжительный ремонт из —за серьезности и обширности дефектов. Кроме того, имеется вероятность внезапного отказа нескольких различных агрегатов одновременно, вследствие чего необходимость в ремонтных работах может превысить возможности ремонтной службы.
Планово — профилактическое техническое обслуживание (в дальнейшем ППР) — такой метод обслуживания, основой которого является плановое периодическое проведение профилактических работ различного объема на оборудовании, т.е. составление и соблюдение календарного графика выполнения через строго определенные интервалы времени работ по профилактическому ремонту (текущему, среднему или капитальному). Достоинством такого метода, по сравнению с реактивным обслуживанием, является резкое снижение вероятности внезапного отказа оборудования. Недостатком планово — профилактического обслуживания является проведение "излишних" ремонтов, т.е. ремонтов фактически исправного оборудования, и, как следствие, излишний рост эксплуатационных затрат.
Достижения в разработке контрольно — измерительной аппаратуры обеспечили возможность не только выявлять состояние агрегата путем измерения
• Организация периодического мониторинга технического состояния оборудования • 3—5 •
Этот путь может оказаться предпочтительным для небольших предприятий с невысокой численностью персонала, используемого для технического обслуживания, поскольку его реализация не требует приобретения средств измерений, обучения специалистов, обеспечения поверки средств измерений и т. д. Однако, этот путь ведет к материальным издержкам, связанным с накладными расходами и обеспечением прибыли сторонней организации. Большинство средних и крупных предприятий, заключивших договора со сторонними организациями на проведение вибромониторинга состояния оборудования, впоследствии приобретают аппаратуру и создают собственную службу вибродиагностики, как только появляются фонды для оснащения и обучения обслуживающего персонала.
Путь второй — приобретение аппаратуры и создание собственной службы вибродиагностики с интеграцией её в существующую структуру технического обслуживания предприятия. Для успешного внедрения этого варианта обязательно наличие некоторого представления о вибродиагностике хотя бы у части гех руководителей, которые привлечены для реализации программы. Кроме того, одновременно с приобретением виброизмерительного оборудования необходим, как минимум, один обученный высококвалифицированный в области вибродиагностики инженер и один или два техника. К сожалению, предприятия в начале реализации такой программы редко располагают квалифицированными специалистами в области вибродиагностики, и если таковых нет, программа обречена на неудачу.
Путь третий — комбинация первого и второго пути: приобретение собственного оборудования, а для его внедрения и/или для обучения собственных специалистов привлечение сторонней организации, имеющей серьезный опыт работы в области вибромониторинга и обучения. Опыт показывает, что этот путь является наиболее успешным, особенно если предоставить такой организации выбор будущих специалистов в области вибродиагностики из числа работающих на предприятии инженеров —механиков.
Стратегия приобретения аппаратуры.
Любая последовательность или приоритеты в приобретении измерительной аппаратуры в большой степени зависит от целей конкретной программы периодического вибромониторинга.
Ниже предлагается вариант последовательности приобретения измерительной системы для вибромониторинга и вибродиагностики в виде постепенных, легко модифицируемых этапов, или стадий.
Стадия 1.
Проведение измерений общего уровня вибрации с применением виброметров (предпочтительно запоминающих). Формирование системы периодического мониторинга и анализа трендов (предпочтительно с применением ЭВМ) по стандартам, регламентирующим оценку состояния оборудования по общему уровню вибрации. При этом возможно приобретение самых простейших миниатюрных переносных виброанализаторов. Рекомендуется также применение автоматических анализаторов состояния подшипников качения.
Стадия 2.
Добавление возможности одноканального виброанализа и балансировки роторов с применением переносных виброанализаторов — сборщиков данных. Переход на периодический мониторинг параметров вибрации в частотных полосах. Регламентирование индивидуальных уровней предельной вибрации оборудования (например, однотипных групп агрегатов).
Стадия 3.
Обеспечение тестирования и калибровки виброизмерительной системы с применением простейших одночастотных вибростендов. Система калибровки для датчиков виброперемещения, если они имеются.
• Организация периодического мониторинга технического состояния оборудования • 3 — 3 •
• сканирование измеренных данных для поиска превышающих предельно допустимые значения (которые могут указывать на повреждения или проблемы агрегата) и оценка состояния каждого агрегата;
• генерация графических отображений для проведения виброанализа и отчетной документации;
• статистическое накопление данных для построения трендов, хранение отчетной документации, экономический анализ проводимых работ и многие другие функции.
Типичный цикл мониторинга оборудования.
Обычно первый шаг при построении системы вибромониторинга оборудования предприятия состоит в создании компьютерной базы данных по обслуживаемому оборудованию, содержащей детальное описание всех обслуживаемых агрегатов, их измерительных точек, измеряемые параметры для каждой измерительной точки и предварительные предельно допустимые уровни измеряемых параметров (в дальнейшем записи базы данных могут быть расширены, удалены или модифицированы).
Затем создаются маршруты обходов оборудования (установок, агрегатов, измерительных точек), по которым будут следовать техники и производить сбор данных по каждой измерительной точке маршрута. Маршрут определяет последовательность сбора данных (какой агрегат, какой его компонент, какая точка и в какой последовательности должны быть обследованы проводящим измерения техником).
Техник со сборщиком данных в соответствии с Регламентом предприятия проводит периодические измерения вибрации и технологических параметров для оценки состояния оборудования, для чего маршрут обхода оборудования предварительно загружается в сборщик данных.

Рис.3—02. Типичный цикл мониторинга.
В процессе проведения измерений и обследований на экране сборщика данных индицируются штатные измерительные точки агрегата, на которых необходимо установить датчик для проведения измерений. Обычно на измерение параметров вибрации среднестатистической контрольной точки затрачивается около 5 секунд (на агрегате примерно 10...20 точек и более). Далее, после
• Организация периодического мониторинга технического состояния оборудования • 3 —1 •
Организация периодического мониторинга технического
состояния оборудованияПериодический вибромониторинг является основой технического обслуживания по фактическому техническому состоянию (ОФС). Он нацелен на то, чтобы при минимальных затратах дать возможность персоналу предприятий распознавать техническое состояние производственного оборудования и точно идентифицировать возможные проблемы во избежание внепланового останова или отказа, приводящих к простоям и дорогостоящему ремонту. Вибродиагностика представляет собой эффективный метод снижения вероятности внепланового останова или отказа.
На границе семидесятых — восьмидесятых годов мобильная и переносная виброизмерительная аппаратура, хотя и дорогостоящая, громоздкая и неудобная с современной точки зрения, но позволяющая осуществлять вибромониторинг не только основного, но и вспомогательного оборудования на основе частотного анализа, нашла применение в промышленности.
В общем случае для проведения периодического вибромониторинга использовались магнитофоны для сбора и хранения виброизмерительной информации, спектроанализаторы для анализа и плоттеры для распечатки информации. В силу малой автоматизации, высокой стоимости и трудоемкости работ, круг промышленного применения такой виброаппаратуры для периодического мониторинга был достаточно ограничен. Ситуация стала меняться с середины восьмидесятых годов с появлением сравнительно недорогих переносных микропроцессорных сборщиков данных и виброанализаторов, а также с возможностью использования достаточно дешевых ЭВМ при хранении и анализе данных измерения вибрации.
Технология мониторинга с использованием сборщика данных и ЭВМ.
Описание сборщика данных и программного обеспечения для проведения периодического вибромониторинга приведено в главе 2. С помощью современного сборщика данных можно выполнять исследования вибрации оборудования, используя его в качестве инструмента контрольного измерения, либо в качестве общецелевого виброанализатора. Обычно он сконструирован настолько легким в обращении, что не требует техника — оператора высокой квалификации при сборе виброданных. Техник, следуя по хранящимся в памяти сборщика данных маршрутам измерений к соответствующим контрольным (штатным) точкам на агрегате, закрепляет датчик и производит измерение параметров (вибрации, тока, температуры и др.) нажатием одной кнопки на сборщике данных. Большинство сборщиков данных можно использовать в качестве автономных анализаторов, способных функционировать как осциллоскопы и/или одноканальные анализаторы
• Методология проведения диагностических виброизмерений роторных агрегатов • 2 — 27 •
При этом должно обеспечиваться управление графикой, такое, как масштабирование осей, выбор шкалы единиц — линейных или логарифмических и др.
Функция локализации измерительных точек с повышенной вибрацией.
Эта функция позволяет оперативно получать информацию о вибросостоянии измерительных точек всех агрегатов БД.
Отчеты, обеспечиваемые этой функцией, в различных формах указывают на каком из агрегатов вибрация превышает установленные уровни, на каких агрегатах просрочены обследования и т.д.
Она может обеспечивать различные методы для просмотра, фильтрации, сортировки и печати данных, собранных во время измерений, а полученная информация используется, для определения данных, требующих дальнейшего анализа. При этом уменьшается общее число агрегатов, которые должны исследоваться.
Функция архивирования ("истории поломок").
Эта функция служит для систематизации и архивирования документации и отчетов о состоянии и проводимых ремонтах агрегата в процессе эксплуатации. Она должна обеспечивать хранение информации о поставленном диагнозе (установленном дефекте агрегата): текущее состояние, описание дефекта, рекомендации, последовавшие действия по устранению дефекта и их результаты, а также затраты на устранение дефекта и ожидаемый экономический эффект.
В некоторых пакетах ПО также автоматизированно составляются различные отчеты, сортирующие информацию по влияющим факторам и группам для увеличения достоверности распознавания состояния агрегата, эффективности ремонта и анализа затрат.
Функция вычислении частот дефектов.
Эта функция позволяет определять специфические частотные составляющие вибросигнала, являющиеся диагностическими признаками потенциальных дефектов, например, подшипников качения, зубчатых передач, электродвигателей и др., а также предполагаемые комбинационные частотные составляющие. Такие модели частотных составляющих обычно могут накладываться на текущий спектр, что способствует быстрой идентификации дефектов. Как правило, эта программа содержит данные о технических и конструктивных характеристиках подшипников, электрических машин и т.д., позволяющие упростить процесс вычисления характерных частот дефектов. Обычно также обеспечивается возможность взаимного преобразования параметров вибрации (виброускорения в виброскорость или виброперемещеиие и т.д.).
Функция графического редактирования.
Такая функция позволяет создавать и отображать схемы агрегатов, которые необходимы для идентификации размещения контрольных точек измерений. Обычно эти схемы рассматриваются при анализе данных измерения вибрации.
Другой важнейшей задачей может быть описание и унификация узлов при построении схемы агрегата для целей автоматизированной диагностики.
Сервисные функции для ремонта агрегата.
Обычно пакет программ предоставляет возможности балансировки роторов и центровки агрегата.
Программа балансировки, как правило, обеспечивает балансировку роторов с учетом взаимного влияния плоскостей коррекции с различным
• Методология проведения диагностических виброизмерений роторных агрегатов • 2 — 25 •
Удобной и иногда необходимой функцией сборщика данных является способность проведения балансировки роторов в собственных подшипниках и центровки агрегата.
Многоканальные виброанализаторы.
Иногда применение одноканальных виброанализаторов не позволяет однозначно установить причины повышенной вибрации оборудования, и может потребоваться взаимный анализ вибросигналов различных контрольных точек агрегата, причинно — следственный анализ, анализ акустической интенсивности или применение специальных функций по обработке сигнала. В этом случае применяют двух— или многоканальные анализаторы. Однако, подготовка опытных специалистов для работы с таким оборудованием трудоемка и длительна, оборудование это достаточно дорого, исследования и анализ могут потребовать длительного времени. Для решения такой проблемы экономически целесообразно приглашать специализированную организацию, имеющую такое оборудование и опыт работы с ним.
Прикладные программы для вибромониторинга.
В настоящее время ряд зарубежных и отечественных фирм (Bruel & Kjaer, CSI, Palomar, Pruftechnik, ТЕС, ВиКонт, Диамех и др.) выпускают пакеты программ для сбора, накопления и обработки данных по вибрации. Пакеты прикладных программ (в дальнейшем ПО) различных фирм достаточно сходны по идеологии взаимодействия со сборщиком данных, но могут существенно различаться по составу программ, уровню сервиса и количеству выполняемых функций.
С точки зрения авторов для решения основных задач ПО должно содержать следующие функции.
Функция управления базой данных.
Эта функция позволяет устанавливать базу данных и работать с ней. Она должна обеспечивать создание новой базы данных; добавление, удаление или изменение информации в базе данных; и печать текущих установок информации, содержащиеся в базе данных.

• Методология проведения диагностических виброизмерений роторных агрегатов • 2 — 23

Рис. 2—12. Структурная схема виброметра.
Каскад интеграторов обеспечивает измерение виброускорения, виброскорости или виброперемещения. Предусмотренные фильтры верхних и нижних частот можно настраивать согласно требованиям к ширине анализируемой полосы частот и/или диапазону измерений используемого датчика. С выходом усилительного каскада, обеспечивающего нужное усиление сигнала, соединен детектор, отдающий пропорциональное измеряемой величине постоянное напряжение, подающееся затем на индикатор (аналоговый или цифровой). Детектор определяет амплитуду, размах или СКЗ измеряемой величины. Если предусмотрено запоминающее устройство, то измеренные значения вибрации можно просмотреть позднее или переслать в ЭВМ. Запоминающее устройство особенно эффективно при измерении механических ударов и кратковременных (переходных) процессов. Виброметры могут иметь выход для подключения внешних приборов.
Некоторые, наиболее современные модели виброметров, позволяют подключать (или имеют встроенные) датчики температуры, числа оборотов и др., а также определяют состояние подшипников качения (используя метод ударных импульсов) и наличие кавитации (измеряя высокочастотные импульсы, характеризующие кавитацию), сохраняя при этом компактность и длительный срок автономной работы. Ввод собранных данных в ЭВМ (с учетом времени сбора информации) позволяет использовать такие виброметры для автоматизированного анализа тенденций.
Переносные одноканальные виброанализаторы.
Условно одноканальные виброанализаторы (анализаторы) можно разделить на две группы: сборщики данных (коллекторы) и просто анализаторы.
Поскольку их основное различие в том, что в сборщик данных можно загрузить маршруты обхода оборудования и уровни тревог. В дальнейшем будут описаны свойства именно сборщика данных.
• Методология проведения диагностических виброизмерений роторных агрегатов • 2 — 21
соответствующий предусилитель. Основной задачей предусилителя является преобразование высокого выходного импеданса акселерометра в более низкий импеданс, оптимальный с точки зрения относительно низкого входного импеданса измерительной и анализирующей аппаратуры см. рис. 2—10 (1).




Рис. 2—10. Функции предусилителей.
Обычно виброизмерительные приборы для периодического вибромониторинга снабжаются как встроенными предусилителями, так и имеют вход для внешнего предусилителя. Большинство предусилителей обеспечивают не только преобразование импеданса, а также усиление и/или формирование отдаваемого акселерометром электрического сигнала. Предусилители могут иметь калиброванный и регулируемый коэффициенты (в том числе автоматически устанавливаемый) усиления для усиления сигнала до нужного для измерительной, анализирующей или регистрирующей аппаратуры уровня (2). Предусилитель (3) с плавно регулируемым коэффициентом усиления дает возможность нормализации сигнала, отдаваемого акселерометрами с "некруглым" или неудобным значением коэффициента преобразования. Предусилитель (4) имеет внутренний электронный интегратор для преобразования пропорционального виброускорению сигнала в сигнал, пропорциональный виброскорости или вибросмещению. Предусилители могут также быть снабжены внутренними фильтрами, определяющими частотный диапазон измерений системы в области низких и высоких частот и эффективно подавляющими шум и другие помехи, а также влияние резонанса пьезодачика.
Вторичные блоки контроля вибрации.
Вторичные блоки предназначены для первичной обработки сигналов, поступающих от вибродатчиков, устанавливаемых на оборудовании, индикации параметров вибрации, индикации уставок предупредительной и аварийной сигнализации и индикации срабатывания защиты.
Вторичные блоки обычно имеют выходы по току и напряжению, а также "сухие" контакты, срабатывающие при достижении контролируемым параметром вибрации уровня уставок. Часто для повышения надежности работы аппаратуры блоки имеют автономные источники питания и индикаторы состояния измерительной (кабельной) линии. Выходы по переменному и постоянному току могут служить для автоматизации процесса контроля и защиты, а также для подключения анализаторов спектра или ЭВМ.
Во вторичном блоке контроля виброскорости напряжение, пропорциональное виброускорению, усиливается, проходит полосовую фильтрацию, интегрируется. Фильтр нижних частот обеспечивает требуемую
• Методология проведения диагностических виброизмерений роторных агрегатов • 2 — 19 •
разъемов, многокомпонентности направлений измерения вибрации, условий эксплуатации и ряда других факторов. Обычно наиболее выгодные — группа пьезодатчиков "общего назначения", удовлетворяющая требованиям большинства областей измерения и анализа механических колебаний. И все же не рекомендуется замыкаться при приобретении диагностической аппаратуры только датчиками "общего назначения", поскольку все ситуации в процессе проведения периодического вибромониторинга предусмотреть невозможно.
Малогабаритные акселерометры при отличном частотном диапазоне измерений и миниатюрности имеют сравнительно низкий коэффициент преобразования (высокий порог чувствительности) и применяются для измерения колебаний с большими амплитудами и высокими частотами, а также при исследовании легких конструкций, каркасов, панелей и др.
Промышленные акселерометры идеально приспособлены для эксплуатации в стационарных системах для контроля и мониторизации механических колебаний в неблагоприятных условиях окружающей среды, в том числе во взрывоопасных средах. Их отличают прочная конструкция корпуса и разъемов (уплотнений), надежность при непрерывной эксплуатации, нормализованная чувствительность, высокая помехозащищенность, передача сигнала на большие расстояния.
Некоторые имеют встроенный предусилитель.
Как правило, крепятся они с применением трех болтов и в этом их достоинство (для постоянного мониторинга) и недостаток (для периодических измерений).
Высокотемпературные акселерометры, обычно как часть промышленных систем специального назначения, имеют специальный чувствительный элемент (пьезокристалл), как правило, естественного происхождения, позволяющий
работать до 400...500 С° и специальный кабель, соединенный с датчиком без разъема. Эти датчики отличает высокая стоимость и, обычно, более низкий коэффициент преобразования, по сравнению с аналогами по габаритам, за счет применения естественного пьезокристалла.
Многокомпонентные акселерометры содержат в общем уплотненном корпусе реже два, а обычно три пьезоэлемента, измерительные оси которых направлены перпендикулярно друг относительно друга. Такой датчик одновременно воспринимает вибрацию в трех взаимно перпендикулярных направлениях. Его существенное преимущество в том, что для проведения трех измерений датчик необходимо крепить лишь один раз.
Основными параметрами, положительно влияющими на приобретение того или иного типа вибродатчика, являются:
• высокий коэффициент преобразования, т.е. способность при воздействии нормированных колебаний генерировать как можно более высокий электрический сигнал; достигается (при прочих равных условиях) увеличением размеров пьезоэлемента и, следовательно, увеличением размеров и собственной массы частей и акселерометра в целом, что в итоге приводит к снижению верхней границы частотного диапазона измерений;
• широкий частотный диапазон измерений, т.е. способность акселерометра правильно измерять как существенно низкочастотные, так и высокочастотные механические колебания агрегата; верхний предел частотного диапазона измерений определяется частотой установочного резонанса; как эмпирическое правило можно принять, что относительная погрешность акселерометра (при Нормальных Условиях) при принятии верхнего предела рабочего частотного диапазона равным 1/5 от величины резонансной частоты не превышает 6%, а при 1/3 — 12%; нижний предел частотного диапазона измерений определяется двумя факторами: нижней частотой среза предусилителя, применяемого с акселерометром и влиянием быстрых изменений температуры окружающей среды, поскольку все пьезоэлементы к ней чувствительны;
• Методология проведения диагностических виброизмерений роторных агрегатов • 2 — 17 •
Виброметры состоят из первичных вибропреобразователей (датчиков), предусилителей, и вторичных блоков. Вторичный блок позволяет измерять общий уровень вибрации агрегата. Некоторые модели позволяют хранить данные.
Виброанализатор, кроме вышеупомянутых блоков, содержит в себе микропроцессорный блок, содержащий программное обеспечение, которые позволяют измерять, хранить, обрабатывать и отображать информацию на местах измерений, а также пересылать информацию в ПЭВМ.
Составные части комплекта виброизмерительной аппаратуры.
Датчики вибрации.
Датчики предназначены для преобразования механической вибрации в аналоговый электрический сигнал. Наибольшее распространение получили три типа датчиков: пьезодатчики (пьезоэлектрические акселерометры), индукционные датчики и токовихревые датчики.
Пьезодатчики.
Используются для измерения абсолютной вибрации. Принцип действия этих датчиков основан на пьезоэффекте: генерации электрического сигнала, пропорционального ускорению при сжатии или растяжении пьезокристалла.
Положительными качествами этих датчиков являются:
• широкий диапазон частот работы;
• прочность конструкции;
• компактность; Недостатки:
• возможна перегрузка предусилителя.
Индукционные датчики.
Используются для измерения абсолютной вибрации. Принцип действия индукционных датчиков основан на эффекте электрической индукции, т.е. генерации электрического сигнала, пропорционального скорости, в катушке которая движется относительно постоянного магнита.
Положительными качествами этих датчиков являются:
• высокий уровень выходного сигнала, позволяющий не применять предусилители;
• большое отношение сигнал/шум; Недостатки:
• большие, по сравнению с пьезодатчиками, размеры и вес;
• ограниченный частотный диапазон измерений и диапазон рабочих температур;
• относительно высокая стоимость.
Токовихревые датчики.
Используются для измерения относительной вибрации.
Положительными качествами этих датчиков являются:
• возможность непосредственного измерения колебаний и положения ротора относительно подшипников;
• низкий порог чувствительности: возможность измерения малых
уровней колебаний вала; Недостатки:
• сложность установки;
• сложность настройки.
• Методология проведения диагностических виброизмерений роторных агрегатов • 2 — 15 •
уровня вибрации "нормального" состояния, то необходимо провести диагностику и составить заключение о техническом состоянии, с указанием возможных дефектов и путей их устранения.
Виброизмерения на начальном этапе эксплуатации и выходе агрегата на номинальный технологический режим.
В этот период следует провести несколько (3...5) полных контрольных измерений с периодичностью 1...2 недели. Если текущий уровень вибрации остается ниже уровня "нормального" состояния, агрегат оставляют в эксплуатации.
Виброизмерения в процессе эксплуатации.
Периодичность измерений в процессе эксплуатации обычно устанавливают исходя из состояния агрегата и характера трендов вибрации.
Если уровень вибрации ниже уровня "средненормальной" вибрации и тренд вибрации не имеет тенденции к возрастанию, например, для СКЗ виброскорости 1 мм/с в неделю, то полные контрольные измерения вибрации проводят с максимальным интервалом не более 3-х месяцев.
Если текущий уровень вибрации выше уровня "нормального" состояния, но не достиг уровня состояния "еще допустимо", то допускается (только если проводятся текущие контрольные измерения) производить полные контрольные измерения также с интервалом в 1...3 месяца, а уровня "требует принятия мер" не реже одного раза в месяц.
Если текущая вибрация достигла уровня "требует принятия мер", то необходимо производить полные контрольные измерения не реже раза в неделю и, по возможности, планировать ремонт.
Виброизмерения после нарушений технологического режима.
Если агрегат останавливали, даже без разборки, или происходили нештатные изменения технологического режима которые могли повлиять на техническое состояние агрегата, то следует провести полные контрольные измерения вибрации.
Виброизмерения перед плановой остановкой на ремонт.
Перед плановой остановкой агрегата на ремонт за несколько дней, чем меньше, тем лучше, следует провести полные контрольные измерения с пометкой "перед ремонтом". Это поможет в дальнейшем достоверно оценить качество проведенного ремонта.
• Методология проведения диагностических виброизмерений роторных агрегатов • 2 — 13 •
составляется программа и производятся специальное диагностическое обследование работающего агрегата. Обычно она включает в себя:
• измерение вибрации всех узлов и частей агрегата, включая всю трубопроводную обвязку, элементы крепления, раму и фундамент, корпуса узлов агрегата;
• выявления зависимости вибрации от изменения режима работы агрегата; ряд режимов агрегата, необходимых для исследования, может выходить за пределы, определенные правилами нормальной эксплуатации; во всех случаях эксперименты по исследованию вибрации связаны с вмешательством в режим работы производства, поэтому программа исследований должна быть согласована с эксплуатационным персоналом и утверждена техническим руководителем предприятия;
• расширенный анализ вибрации с применением всех возможностей аппаратуры (максимизация частотного диапазона и разрешающей способности, анализ кепстров, спектров огибающих, частотных и фазовых характеристик и др.;
Исследования включает опытное определение влияния на вибрацию различных факторов: теплового состояния, крутящего момента, условий охлаждения и т.д. При этом могут проводиться следующие работы:
• снятие частотных характеристик при пуске и останове агрегата;
• снятие режимных характеристик;
• снятие контурных характеристик;
• определение собственных частот агрегата и трубопроводов;
• снятие вибрационных характеристик продуктопроводов, аппаратов, маслопроводов и др.
• балансировка роторов в собственных подшипниках и др.
Типовые исследование следует минимизировать и проводить в такой последовательности, чтобы по возможности обеспечить проведение всего комплекса намеченных экспериментов за один цикл нагружения и разгружения агрегата.
Обследование остановленного агрегата.
При минимальной разборке это обследование обычно ограничивается ревизией подшипников, проверкой центровки узлов агрегата и состояния муфт, осмотром мест возможных задеваний и доступной части роторов.
При ремонте агрегата могут быть проведены также работы по частичной разборке роторов, их всесторонней проверке, включающей ревизию шпоночных соединений и других монтажных сопряжений. По результатам исследований составляется заключение о причинах повышенной вибрации и методах ее устранения.
Следует учесть, что вибрационное обследование не всегда приводит к однозначному определению причины повышенной вибрации, поэтому в заключении по этому обследованию должны быть указаны все возможные причины вибрации, а намечаемый объем ремонтных работ должен предусматривать устранение всех этих причин.
Иногда трудно предвидеть, окажутся ли достаточными намеченные работы по устранению причины повышенной вибрации. Это относится, например, к низкочастотной вибрации, к работам по изменению жесткости опорной системы и т.п. В таких случаях в заключении должна быть оговорена возможность дополнительных мероприятий по устранению вибрации после выполнения и проверки результатов проведенных работ.
• Методология проведения диагностических виброизмерений роторных агрегатов • 2—11 •
Текущее контрольное измерение.
Задачей текущего контрольного измерения вибрации является:
• определение текущего общего уровня вибрации в контрольных точках;
• сравнения текущего общего уровня вибрации с нормами (уровнями тревог);
• если обнаружено превышение общим уровнем вибрации установленных норм (уровней тревог) или появление тенденции возрастания уровня вибрации (например, более чем 1 мм/с за неделю), необходимо безотлагательное проведение полных контрольных измерений;
Целесообразно проводить контрольные измерения с момента пуска агрегата после ремонта и до остановки агрегата с периодичностью раз в сутки или раз в смену, что должно определяться Регламентом предприятия. Результаты измерений должны регистрироваться в вахтовом журнале или ответственным специалистом, осуществляющим мониторинг.
Для оборудования 4 и 5 категорий число измерительных точек агрегата для текущих контрольных измерений иногда минимизируют, оставив только точку с максимальной вибрацией на каждом подшипниковом узле. Достаточно часто, если проведение полных контрольных измерений не показывает изменения вибросостояния такого оборудования, для текущих контрольных измерений оставляют по одной точке на каждый узел агрегата.
Текущее контрольное измерение позволяет с минимальными трудозатратами обеспечить мониторинг состояния оборудования в период между более дорогими полными контрольными измерениями вибрации и, в большинстве случаев, вовремя обратить внимание на изменение состояния оборудования, если оно происходит.
Полное контрольное измерение вибрации.
Задачей полного контрольного измерения вибрации является:
• определение текущего уровня контролируемого параметра вибрации в контрольных точках;
• распознавание состояния оборудования, включающее сравнение текущего уровня контролируемого параметра вибрации с нормами (уровнями тревог);
• предварительная оценка степени опасности повышенной вибрации (связанных с этим обстоятельств) и локализация мест с максимальной вибрацией, если обнаружено превышение уровнем вибрации норм (уровней тревог);
• принятие немедленного решения о допустимости эксплуатации оборудования: если проблема очень серьезна (в зависимости от особенностей Регламента виброизмерений предприятия), возможно проведение частотного анализа и установление общего характера вибрации на месте измерения; при необходимости измеряется вибрация в дополнительных точках;
• регистрация, запоминание и анализ (при необходимости) результатов измерений;
• составление заключения о текущем состоянии агрегата и возможности его дальнейшей эксплуатации (например, неограниченная по времени эксплуатация, ограниченная по времени эксплуатация, эксплуатация недопустима и др.) и, по возможности, определение объема работ по устранению повышенной вибрации (в том случае, если установлено превышение уровнем вибрации норм, и при этом становятся ясными причины повышенной вибрации).
• Методология проведения диагностических виброизмерений роторных агрегатов • 2 — 9 •
при применении различных типов щупов рабочий частотный диапазон может существенно изменяться.
Обозначение точек контрольных измерений вибрации.
Обозначение точек измерения устанавливается Регламентом измерений предприятия для типов оборудования по единой схеме. Обычно, в буквенно -цифровую комбинацию, составляющую код измерительной точки, могут вносить:
• индекс принадлежности к узлу агрегата (например, М - мультипликатор, Д - двигатель, К - компрессор и т. д.);
• номер или положение подшипника (например, передний подшипник - П или У — упорный и т. д.);
• направление измерения (например, V — вертикальное, Н -горизонтально —поперечное и т. д.);
Обычно карты регистрации уровней вибрации и программы обработки информации содержат наименования узлов агрегата, принятые Регламентом предприятия.
Данные измерения вибрации и способы ведения мониторинга.
При проведении периодического вибромониторинга обычно используют три основных типа данных получаемых при измерении вибрации: общие уровни вибрации, формы и спектры сигнала вибрации. На многих предприятиях проводят измерения только общих уровней вибрации и анализ их трендов, в то время как спектры и формы сигналов вибрации или не собираются вовсе, или собираются лишь с агрегатов, имеющих развитые дефекты.
В частности, "Методические рекомендации по проведению диагностических виброизмерений центробежных компрессорных машин и центробежных насосных агрегатов МНХП" (РДИ, 1991) для роторных машин, не оснащенных стационарными системами контроля, при проведении контрольных измерений устанавливают в качестве контролируемого параметра только СКЗ абсолютной виброскорости или абсолютного перемещения корпусов подшипников узлов агрегата, а сбор форм и спектров виброакустических сигналов только при специальных диагностических исследованиях.
Однако, в послудующих главах настоящей книги показывается, что появление и развитие многих дефектов оборудования может сопровождаться при его работе ростом не столько "высокоэнергетичных" составляющтх вибрации, сколько отдельных частотных составляющих или их групп сравнительно низкой амплитуды. Следовательно можно установить (определить) некоторые полосы частот, соответствующие отдельным дефектам или группам дефектов. Вибрацию в частотных полосах весьма удобно и целесообразно просматривать с целью поиска изменений уровней вибрации, которые могут говорить об изменении состояния агрегата и, в этом случае, проведении более детального анализа. Данный поиск обычно включает как сравнение амплитуд вибрации с фиксированными уровнями тревог, так и статистический анализ изменений и сравнение с исходными значениями. Только в этом случае суждение о текущем состоянии агрегата будет выноситься с учетом его предыдущих состояний.
Для агрегатов с изменяемой частотой вращения ротора необходимо обеспечить измерение фактической частоты вращения и получение соответственно установленных параметров анализа и частотных полос. Эта процедура называется "частотной нормализацией". При использовании такой процедуры, ширина частотных полос определяется как функция частоты
• Методология проведения диагностических виброизмерений роторных агрегатов • 2 — 7 •
• неплоскостность поверхности крепления — 0,01 % .
Оптимальный крутящий момент при креплении датчика на шпильку диаметром 5...7 мм — 1,7...2 Нм.
На рис. 2 — 04 показана амплитудно-частотная характеристика пьезодатчика общего назначения, закрепленного стальной шпилькой на гладкой поверхности объекта. В этом случае резонансная частота пьезодатчика практически совпадает с резонансной частотой полученной при калибровке производителем (примерно 33 кГц).

Рис. 2—04. Амплитудно-частотная характеристика пьезодатчика при применении для крепления датчика стальной шпильки.
Крепление при помощи шпильки имеет неудобства: затраты времени при выполнении крепежа и необходимость проведения слесарных работ.
Альтернативным методом крепления пьезодатчиков является крепление на тонком слое пчелиного воска. При этом незначительно уменьшается его резонансная частота (примерно 29 кГц).

Рис. 2—05. Амплитудно-частотная характеристика пьезодатчика при применении для крепления датчика пчелиного воска.
Недостатками этого метода крепления являются размягчение воска с ростом температуры, так, что его можно применять в температурном диапазоне до 35...40 градусов Цельсия и ненадежность крепления сравнительно крупных датчиков, особенно в направлении измерения, отличном от вертикального. Крепление датчика пчелиным воском на гладкой чистой поверхности при измерении вибрации в вертикальном направлении можно считать допустимым
• Методология проведения диагностических виброизмерений роторных агрегатов • 2 — 5 •
Допускается измерение вертикальной, горизонтальной и осевой составляющих вибрации путем установки на верхнюю часть крышки подшипника трехкомпонентного вибродатчика для измерений вибрации во взаимно перпендикулярных направлениях совпадающих с главными осями агрегата.
В силу экономических соображений при изучении виброконтролепригодности каждого конкретного агрегата и подготовке контрольных точек всегда возникает вопрос о пространственном направлении измерений, оптимальном с точки зрения распознавания состояния определенного узла агрегата. Решающего правила или общего ответа на этот вопрос нет, но если невозможно проведение измерений по трем главным направлениям в зоне одного подшипника или требуется минимизация количества замеров, то допускается измерение вибрации по двум направлениям: осевом и одном из поперечных направлений. Предпочтение отдается поперечному направлению, как правило соответствующему направлению минимальной жесткости системы. Допускается также осевую вибрацию привода, нагнетателя и др. узлов агрегата измерять только у подшипника свободного конца вала.
Измерение вибрации при диагностировании опорных подшипников качения производится на подшипниковых щитах в поперечном направлении, желательно в нижней части щита, как показано на рис. 2 — 02 а).

Рис. 2—02. Направления и точки измерения вибрации электрической машины при диагностировании механической (а) и электромагнитной (б) систем.
Точки и направления измерения сигнала вибрации для диагностирования моделей механической и электромагнитной систем электрических машин различны. На рис. 2 — 02 б) показаны основные точки измерения сигнала вибрации на корпусе машины при вибродиагностировании ее электрической несимметрии. В ряде случаев эти точки при измерении поперечной составляющей вибрации могут совпадать с точками измерения вибрации на подшипниковых щитах.
Нарушения гидродинамики потока, например, кавитацию, во многих случаях следует контролировать, измеряя сигнал вибрации на корпусе в районе входного патрубка насоса.
Места установки датчиков.
Датчик следует закреплять так, чтобы его измерительная ось совпадала с нужным при измерении направлением. Как правило, измерительная ось перпендикулярна плоскости крепления датчика (его рабочей поверхности). Цель измерения и анализа вибрации обычно диктует расположение мест крепления пьезодатчика на исследуемом объекте, см. приведенный на рис. 2 — 03 пример.
• Методология проведения диагностических виброизмерений роторных агрегатов • 2 — 3 •
• агрегаты, находящиеся в труднодоступных местах;
• агрегаты с периодически возникающими отказами;
• агрегаты, на которых в прошлом имели место внезапные отказы, или непонятные процессы вызывают выход агрегата из строя;
• требования производственного процесса.
Периодический вибромониторинг агрегатов второй и третьей категории, если на них не установлена стационарная система контроля рабочих параметров, следует проводить обязательно.
Масштаб охвата периодическим мониторингом (распознаванием состояния) агрегатов четвертой и пятой категорий зависит от многих факторов, индивидуальных для каждого предприятия, немаловажное место среди которых занимают наличие специалистов и виброизмерительного оборудования, а также результаты функционально — стоимостного анализа.
Виброконтролепригодность оборудования.
Виброконтролепригодность — это пригодность агрегата для вибродиагностики. Она должна обеспечиваться при проектировании агрегата, в ходе его доводки, монтажа или эксплуатации конструктивными решениями, выбором диагностических средств и проведением специальных испытаний для отработки диагностических методов и средств.
Пригодность эксплуатируемого агрегата для вибродиагностики определяется возможностями использования штатных и дополнительных средств. При конструировании, доводке, монтаже и эксплуатации агрегатов наибольшие затруднения обычно вызывает определение мест установки вибродатчиков, которые требуется ставить с учетом местонахождения устраняемой неисправности.
Основное правило размещения вибродатчиков — максимально возможное их приближение к диагностируемому узлу и установка на жесткие элементы конструкции с подготовленной поверхностью. Желательно, чтобы число стыков деталей на путях прохождения вибросигналов от диагностируемой детали к месту установки датчика было минимальным. При выборе этого места учитывают также резонансные свойства конструкции в требуемой полосе частот. Направление измерительной оси вибродатчика желательно ориентировать по линии действия силы, вызывающей виброакустический сигнал.
Значительную часть потенциально ненадежных деталей выявляют ускоренными эквивалентными и циклическими испытаниями агрегатов еще в ходе отработки опытных образцов. При доработке конструкции по выявленным "слабым местам" предусматривают конструктивные решения, обеспечивающие требования вибродиагностики. Однако, иногда ненадежные детали со значительно укороченным (по сравнению с другими деталями агрегата) ресурсом проявляются лишь на этапе эксплуатации и требуют особого наблюдения.
Возможность установки вибродатчика обеспечивается созданием соответствующих площадок (на фланцах, бобышках, приливах и т. д.), либо возможностью установок специальных крепежных элементов (болтов, гаек с площадками под вибропреобразователи) взамен штатных, либо возможностью установок специальных кронштейнов.
В вибродиагностике машин широко используют пьезоэлектические вибропреобразователи (пьезодатчики), обычно малогабаритные, что облегчает задачу по выбору мест их установки.
Места установки вибродатчиков, которые будут использоваться только в случаях необходимости для специальных исследований при возникновении неисправностей при эксплуатации, следует указывать в технической
• Методология проведения диагностических виброизмерений роторных агрегатов • 2 — 1 •
Методология проведения диагностических виброизмерений
роторных агрегатов1
Последовательность действий при измерении вибрации и оценке состояния оборудования и выводе оборудования в ремонт должна детально определяться требованиями заводов изготовителей, отраслевыми Руководящими Документами, стандартами России и Регламентом, утвержденным руководителем предприятия, при этом отступления недопустимы. При разработке Регламента предприятия в качестве дополнительной информации следует учитывать приведенные в этой главе сведения. Авторы не несут ответственности за внеплановые отказы оборудования и финансовые издержки, связанные с неправильным применением описанной методологии, поскольку виды, периодичность, необходимая точность измерений для вибрационного диагностирования, решение задач контроля, оценки технического состояния агрегатов, выявления дефектов и причин их образования, а также назначения оптимальных сроков эксплуатации до ремонта определяются в первую очередь спецификой оборудования, уровнем технологии ТО, квалификацией обслуживающего персонала и многими другими факторами, которые должны учитываться в каждом конкретном случае при формировании комплекса работ по вибромониторингу оборудования. В настоящей главе излагается только общий подход, которому, по мнению авторов, рекомендуется следовать при решении данного вопроса.
Организация работ по исследованию вибрации.
Категории оборудования и мониторинг.
В силу того, что организация технического обслуживания оборудования по фактическому техническому состоянию (ОФС) требует значительных исходных вложений трудовых и финансовых ресурсов, целесообразно при его организации рассматривать различные компромиссные варианты, которые могут быть приняты для максимизации экономического эффекта.
Поскольку во многих случаях нерационально затрачивать время и прикладывать
• Методология диагностирования зарождающихся и развитых дефектов • 1 — 20 •
Аналогичная картина наблюдается при возбуждении колебаний в других механизмах с вращающимися деталями и их узлов, содержащих пару трения, например, турбин, насосов, подшипников качения и скольжения. При появлении неисправностей механизма меняется характер взаимодействия элементов кинематической пары, что приводит к изменению энергетического баланса выражения [1.2].
Характер изменения вибрационных процессов, вызванных изменением состояния контактирующих поверхностей, имеет ряд общих черт, несмотря на различие конструкций и назначение кинематических узлов. Это позволяет сформулировать некоторые правила диагностирования дефектов контактирующих поверхностей типа абразивного износа, выкрашивания и задира, общие для пары зубчатых колес, подшипников скольжения и качения, сопряжения втулка цилиндра-поршень и других узлов, содержащих пару трения.
Истирание (абразивное изнашивание) контактирующих поверхностей сопровождается появлением микронеровностей в зоне контакта, нарушением микро- и макрогеометрии деталей, следствием чего является рост шумовой компоненты SN (f), увеличение амплитуд гармонического ряда mfZ основной частоты возбуждения кинематического узла и перераспределение амплитуд между гармониками этого ряда.
Выкрашивание (локальное изнашивание) контактирующих поверхностей, проявляющееся в развитии раковин в зоне контакта, вызывает появление периодических всплесков вибросигнала, модулирующих основной процесс возбуждения колебаний.
Периодическое попадание раковин в зону контакта при вращательном движении элементов агрегата (зубчатых колес, тел вращения, сепаратора или обоймы подшипников качения) приводит к появлению в спектре сигнала комбинационных частот mfZ±kfr в окрестности основных частот возбуждения, вызванных амплитудной модуляцией. Рост числа выбросов при увеличении их амплитуд, вызванных развитием данного дефекта, приводит к увеличению глубины амплитудной модуляции, росту числа комбинационных частот и перераспределению энергии между ними при неизменности амплитуд основных частот возбуждения.
Развитие трещины в теле детали вращения, приводящее к поломке (зубьев колеса редуктора, сепаратора или обоймы подшипника качения), очень сходно по своему проявлению в спектре сигнала с развитием выкрашивания, но скорость развития данного дефекта значительно выше.
Задир контактирующих поверхностей, являющийся следствием увеличения коэффициента демпфирования механической системы, сопровождается мгновенным разогреванием локальных участков, "схватыванием" поверхностей в зоне контакта и последующим наволакиванием металла. Как правило, задир (заедание) развивается при неправильных условиях эксплуатации механизмов: при нарушении условий смазки, при увеличении нагрузки сверх допустимых пределов, при попадании посторонних предметов в зону контакта. Явление задира приводит к нарушению периодичности движения деталей агрегата, к флуктуациям скорости вращения, к появлению выбросов в вибросигнале, к явлению фазовой модуляции на основных частотах возбуждения. С развитием задира вибросигнал становится существенно нестационарным из —за нерегулярности выбросов. В спектре сигнала наблюдается падение амплитуд основных частот возбуждения mfZ при одновременном росте амплитуд комбинационных частот (mfZ±kfr).
Известно, что отклик механической системы на воздействие кратковременного одиночного импульса, имеющего широкополосный спектр, можно наблюдать на собственных частотах системы, но энергия отклика на каждой из этих частот мала даже при воздействии на систему последовательности импульсов, поэтому данные спектрального анализа колебаний при зарождении и
• Методология диагностирования зарождающихся и развитых дефектов • 1 — 18 •

Рис. 1—04. Последовательность равноотстоящих прямоугольных импульсов, имеющих одинаковую длительность и случайную амплитуду (верхний график) и спектр периодической последовательности прямоугольных импульсов, модулированных по амплитуде низкочастотным полигармоническим процессом.
Для формирования диагностического признака используют обычно представление сигнала в достаточно узком диапазоне частот, например в зоне одной из гармоник основной частоты возбуждения механизма (зубцовой, винтовой, лопаточной и др.).
![]() |
Рис. 1—05. Узкополосный случайный процесс (сплошная линия), его огибающая (пунктир) и спектр огибающей.
При этом представляют колебания в виде модуляции высокочастотного гармонического сигнала суммой гармонических же низкочастотных колебаний.
• Методология диагностирования зарождающихся и развитых дефектов • 1 — 16 •
Погрешности изготовления и монтажа деталей, температурные изменения геометрических параметров деталей и зазоров в сочленениях, изменение вязкости смазки, искажение формы и качества поверхностей взаимодействующих деталей с наработкой, наконец, нестабильность оборотов вала двигателя, вызванная, например, нестабильностью частоты сетевого напряжения, и множество других случайных факторов приводят к флуктуациям амплитуд и размытию дискретных линий спектра полигармонических колебаний.
Более адекватной моделью процесса возбуждения колебаний является суперпозиция узкополосных случайных процессов с кратными средними частотами:

где kwr — средняя частота узкополосного процесса, Аk(t) — случайная, медленно меняющаяся огибающая узкополосного процесса, jk(t) — случайная, медленно меняющаяся фаза, y(t) — уровень шумового возбуждения.

Рис. 1—03. Спектры полигармонического и квазиполигармонического процесса.
Энергетический спектр такого процесса (см. рис. 1 — 03) сосредоточен в узких полосах частот в окрестности kfr.
При моделировании возбуждения колебаний в роторных агрегатах изменение состояния агрегата можно оценивать по изменению не только величин амплитуд спектральных составляющих, но и уровня шумового возбуждения y(t) с равномерным спектром SШ (w) в рассматриваемом диапазоне частот. Такая форма представления вибросигнала достаточно хорошо моделирует износ контактирующих поверхностей зубьев колес в редукторе, в подшипниках качения и т. п.
Соотношение энергии периодического и шумового компонентов является информативным параметром вибросигнала, широко используемым при формировании диагностических признаков состояния агрегата.
Импульсная модель акустического сигнала.
Квазиполигармоническая модель колебательного процесса [1.1] мало что говорит о соотношении амплитуд спектра на частотах kfr. Эту информацию может дать модель, базирующаяся на представлении процессов возбуждения колебаний в роторных агрегатах в виде периодической последовательности импульсов
• Методология диагностирования зарождающихся и развитых дефектов • 1 —14 •
такие характеристики виброакустического сигнала, которые мало меняются от эксперимента к эксперименту при задании одних и тех же параметров технического состояния, т. е. имеют наименьшую дисперсию при условии, что средние значения этих признаков для разных дефектных состояний достаточно отличаются друг от друга, иначе говоря, дисперсия по всей совокупности состояний велика.
При выборе диагностических признаков необходимо учитывать ряд требований, вытекающих из задачи оптимизации диагностической системы. Прежде всего признаки должны быть однозначно связаны с состоянием объекта и образовывать достаточную систему для обеспечения достоверного диагноза. Предпочтительны признаки, которые позволяют обнаружить дефекты на возможно более ранних стадиях их развития. Признаки должны обеспечивать требуемую глубину диагноза, не усложняя процедуры и не увеличивая стоимости средств диагностирования.
В виброакустической диагностике часто прибегают к выбору таких признаков состояний, каждый из которых характеризует свой образ (характерные признаки), а минимизация описания объекта производится исходя из физических соображений.
Выбор информативных диагностических признаков тесно связан со структурой виброакустического сигнала агрегата. Именно поэтому в вибродиагностике важнейшая роль отводится модели формирования и изменения виброакустического сигнала при появлении и развитии дефектов.
Больше других разработаны детерминированные модели, в которых колебательные процессы представляются периодическими функциями, связанными с вращением или периодическим соударением элементов узлов механизма.
Информативными диагностическими признаками здесь являются амплитуда, продолжительность и момент появления импульса, а также частота, амплитуда и фаза гармонического сигнала. Модели с детерминированными сигналами оправдали себя и дают хорошие практические результаты для сравнительно низкооборотных (1500...15000 об/мин) агрегатов с малым количеством источников возбуждения колебаний.
Наиболее употребительной характеристикой виброакустического сигнала является энергетический спектр — поставщик информации об амплитудно-частотных изменениях в сигнале при появлении неисправности. В ряде случаев, например, при разработке системы диагностирования работоспособности агрегата, достаточно ограничиться данными спектрального анализа.
Намного сложнее обнаружить зарождающийся дефект высокооборотного (более 15000 об/мин) агрегата с большим числом взаимосвязанных источников возбуждения. Виброакустичесие сигналы в таких объектах, как правило, являются случайными процессами, а информативными признаками служат довольно сложные характеристики сигналов (корреляционные функции, кепстры, биспектры, функции распределения вероятностей, моментные характеристики и др.), получение которых доступно иногда только при использовании многоканальных виброанализаторов.
Перечень характеристик виброакустических процессов, наиболее часто используемых в диагностических целях при проведении мониторинга оборудования с помощью одноканальных сборщиков данных, приведен в приложениях.
Для выявления характерных диагностических признаков виброакустический процесс подвергается предварительной спектральной обработке, позволяющей выявить зоны и характер наибольших изменений сигнала в частотной области. На основании спектрального анализа выбирается способ извлечения из сигнала информативного компонента путем подавления помехи за счет фильтрации, интегрирования, детектирования, усреднения и т. п. Затем составляется перечень (словарь) диагностических признаков, чувствительных к определенному дефекту.
• Методология диагностирования зарождающихся и развитых дефектов • 1 — 12 •
Неисправности элементов конструкции механизма, развитие которых в процессе эксплуатации до критического уровня, т. е. до наступления отказа, не может быть зарегистрировано и проконтролировано средствами диагностирования, условно называются неисправностями, вызывающими внезапный отказ. Как говорилось ранее, такого рода отказы возникают, например, при статическом разрушении от действия мгновенно возникшей нагрузки, превышающей прочность элемента, при усталостном разрушении, возникающем в результате производственных дефектов (трещина, не снятые напряжения). Внезапный характер возникновения таких изменений затрудняет их индивидуальное прогнозирование. Неисправности элементов конструкции механизма, возникновение и развитие которых может быть зарегистрировано на ранней стадии возникновения и проконтролировано до критического уровня, называются неисправностями, вызывающими постепенный отказ. Такого рода отказы являются следствием естественного износа, в результате чего происходит постепенное, монотонное изменение структурных параметров. При этом износ может быть прогрессирующим, ускоряющимся, в случае жесткого сопряжения элементов, либо замедляющимся в случае упругих сопряжений.

Рис. 1—01. Схема характерных процессов изнашивания узлов механизма в зависимости от наработки. 1 — износ упругого сопряжения; 2 — износ жесткого сопряжения; 3 — классическая кривая Лоренца; 4 — усталостный или кавитационный износ; 5 — коррозионный износ.
Для выкрашивания, кавитации, коррозионного и некоторых других видов износа характерно наличие инкубационного периода tИ. Анализируя графики, приведенные на рис. 1 — 01, можно заметить некоторую общность кривых и возможность с достаточной точностью их описания функцией вида:

где х — значение параметра; v — скорость изменения параметра при t=1, уменьшенная в a раз; a — показатель степени; t — наработка.
В настоящее время показатель а экспериментально определен для многих характерных объектов диагностирования. Например, для. изменения теплового зазора клапана двигателя a= 1,1; для износа зубьев шестерен a = 1.5 и т.
д.
В реальных условиях имеет место одновременное существование всех перечисленных типов деградации узлов механизма. Для того чтобы разработать метод и технологию диагностирования какого —либо объекта, необходимо знать закономерности изменения виброакустических характеристик со временем наработки.
• Методология диагностирования зарождающихся и развитых дефектов • 1 — 10 •
Характер изменений при усталостных процессах таков, что существует инкубационный, обычно длительный, период медленного накопления повреждений с постоянной скоростью, после которого происходит резкое увеличение скорости накопления повреждений. Такому закону очевидно должно следовать и изменение интенсивности вибрации, связанной с явлениями усталости. Однако при этом следует учитывать возможное изменение частот и форм колебаний вибрирующих деталей — возможны резкие изменения интенсивности колебаний деталей, вошедших в резонанс. Для нормально работающих деталей (исправное состояние) в инкубационном периоде развития усталостных дефектов изменение вибрации происходит с постоянной скоростью (при этом возможно случайное медленное флуктуирующее изменение интенсивности). На стадии быстрого разрушения увеличивается частота случайных флуктуации и их размах (дисперсия), т.к. увеличивается скорость случайных изменений.
Закономерности ползучести.
В процессе ползучести выделяют три периода: сначала постепенное уменьшение скорости пластической деформации, затем процесс протекает с минимальной постоянной скоростью, причем с ростом напряжения и температуры скорость пластической деформации растет, и при этом продолжительность данного периода с точки зрения эксплуатации агрегата уменьшается, и, наконец, скорость деформации нарастает, пока не наступит разрушение.
Остаточная деформация.
Нагрузки, вызывающие напряжения, которые превышают предел упругости, могут привести к остаточной деформации и появлению трещин. Остаточные деформации изменяют геометрическую форму и размеры деталей, что влияет на вибрационные процессы, генерируемые взаимодействием деталей (кинематических пар).
Износ.
Возможны несколько видов износа, которые появляются в связи с одним или несколькими следующими процессами: микросрезанием, пластической или упругой деформацией, возникающей вследствие высоких местных напряжений, поверхностной усталостью при повторяющихся упругих деформациях поверхности, местным перегревом, окислением, забиванием микротрещин смазкой, что является причиной возрастания давления, которое приводит к повреждению поверхностного слоя. Эти процессы могут происходить одновременно и приводить к ниже перечисленным видам износа.
Абразивный износ. Возникает вследствие истирания трущихся поверхностей и прямо пропорционален удельному давлению на трущиеся поверхности и пути скольжения. Пример — износ подшипников. Истирание трущихся поверхностей, разделенных смазкой вызывает струйный износ, а контактирующих (например, при задеваниях) фрикционный.
Заедание. Возникает вследствие контакта поверхностей в условиях разрушения масляной пленки. Различают следующие стадии этого процесса: увеличение коэффициента трения из —за нарушения режима смазки, резкий нагрев, разрушение поверхностного слоя, сопровождающееся свариванием металла двух поверхностей. Наиболее часто встречается в зубчатых муфтах и зацеплениях, а также поршневых агрегатах.
Усталостный износ (питтинг). Возникает вследствие усталости поверхностного слоя и при относительном скольжении поверхностей и вследствие микрошероховатостей. Наиболее часто встречается в зубчатых парах и подшипниках качения.
• Методология диагностирования зарождающихся и развитых дефектов • 1—8 •
Статистический анализ показателей надежности и затрат на восстановление узлов позволяет получить характеристику и адрес наиболее слабого звена. Кроме указанных выше затрат, объект диагностирования характеризуется непрерывными затратами на поддержание его работоспособности.
Виды отказов и дефектов и их связь с вибропроцессами.
Достоверность оценки состояния агрегата при техническом обслуживании, включающем в качестве необходимой составной части техническое диагностирование, зависит от понимания сущности рабочих процессов, выступающих в качестве носителей диагностической информации, и от знания законов возникновения и развития неисправностей.
Отказы и дефекты связаны с вибрационными процессами в оборудовании различным образом, они могут быть вызываемыми вибропроцессами, вызывающими вибропроцессы или изменяющими их. При разработке методик диагностирования полезно выделять характерные стадии развития дефекта (отказа), поскольку каждая из них может характеризоваться своим комплексом диагностических параметров. Обычно различают следующие стадии:
• появление причин, вызывающих дефект или отказ;
• инкубационный период (накопление повреждаемости, зарождение дефекта и ранняя стадия развития, вызывающая изменение свойств, иногда труднообнаруживаемого используемыми методами диагностики);
• развитый дефект, т. е. дефект, обнаруживаемый методами диагностики, но не вызывающий вторичных повреждений;
• развитие дефекта, вызывающее вторичные повреждения или изменения в оборудовании, характеризующиеся своими диагностическими параметрами;
• внезапное или мгновенное разрушение (имеет место не для всех дефектов), которое может вызывать или не вызывать вторичных разрушений.
Первые две стадии в большинстве случаев диагностируют по параметрам, характеризующим причины дефекта, длительность и степень их воздействия. Развитый дефект обнаруживают по параметрам, характеризующим степень его развития. Развитие дефекта, вызывающее вторичные повреждения, дополнительно обнаруживается по диагностическим параметрам этих повреждений. В задаче диагностики внезапного или мгновенного разрушения, которое необходимо предотвратить при контроле оборудования, следует использовать параметры, характеризующие первые две стадии его развития.
В вибродиагностике следует учитывать тот факт, что дефекты на разных стадиях развития могут быть связаны с вибрационными процессами в оборудовании (колебаниями его деталей или динамическими процессами, их взывающими) различным образом, а переход от одной стадии развития к другой может быть постепенным или скачкообразным.
Дефекты обычно классифицируют по следующим аспектам, учитываемым при разработке и использовании методов и средств диагностики:
• по виду разрушения (усталость, износ, ползучесть, коррозия, термодеформации и т. д.);
• по моментам проявления ( в процессе работы, при осмотрах и техническом обслуживании, при разборке);
• по временному характеру проявления (внезапные, постепенные, сбои, перемежающиеся отказы);
• по причинам возникновения (конструктивные, технологические, производственные, эксплуатационные, дефекты материала);
• по степени опасности;
• Методология диагностирования зарождающихся и развитых дефектов • 1—6 •
диагностики следует отнести уточнение и изменение границ по мере получения дополнительной информации о процессе.
Основной подход к решению поставленных задач состоит в следующем.
Используя упрощенные математические модели колебаний в динамических системах, ранее накопленный опыт и широкие, достаточно тонкие экспериментальные исследования единичных объектов, получают информацию о диагностических признаках, например опасных колебаниях. На этой основе оценивают состояние всего парка эксплуатируемых машин. В дальнейшем используют статистику парка машин и результаты их диагностирования, проводя коррекцию критериев оценки состояний исследуемой системы, параметров ее состояний и их диагностических признаков, т. е. реализуют обратную связь на основе диагностирования парка машин.
Решение указанной общей задачи складывается из поэтапного решения нескольких задач более низкого уровня.
Признаками состояний диагностируемых элементов агрегатов служат характеристики переменных напряжений в деталях, характеристики колебаний деталей, геометрические погрешности изготовления деталей и сборки узлов, параметры рабочих процессов, протекающих в агрегатах, и т. п. Признаки состояния могут быть количественными или качественными, ранговыми или качественными классификационными (не связанными с естественным упорядочением). Характер признаков распознаваемых состояний в значительной степени определяет особенности методов выявления диагностических параметров и методов принятия решений при диагностировании.
С точки зрения вибрационной прочности в агрегатах наиболее опасны колебания периодического характера, имеющие спектры с явно выраженными дискретными составляющими. Подобные опасные колебания в основном являются сильными диагностическими сигналами (т. е. хорошо выделяется на фоне помех).
При возникновении и развитии дефектов с малой виброактивностью возбуждаются колебания, которые, как правило, являются слабыми диагностическими сигналами. Неисправности порождают узкополосные и широкополосные сигналы стационарного и нестационарного характера.
Ввиду сложности определения неисправностей и дефектов в машинах и необходимости анализа слабых сигналов в качестве диагностических параметров используют большое число количественных характеристик сигналов и их комбинаций. К ним относятся все общеизвестные количественные характеристики детерминированных и случайных процессов, спектральная плотность, кепстр (спектр логарифмированного спектра), выделение огибающей и т. д. Кроме того, в качестве диагностических параметров используют различные комбинации количественных характеристик процессов, например, уровни отдельных составляющих в спектрах детерминированных и случайных сигналов, а также характеристики изменения перечисленных выше параметров.
Для обоснования выбора диагностических параметров в каждом конкретном случае необходимы экспериментальные исследования агрегатов в рабочем и неисправном состояниях. При этом следует учитывать, что дефекты обычно характеризуются комплексом диагностических параметров.
Вибрация агрегатов, рассматриваемая при диагностических исследованиях в широком диапазоне частот и амплитуд, является комплексным диагностическим сигналом, представляющим собой совокупность аддитивных и мультипликативных комбинаций сложных слабых и сильных "элементарных" диагностических сигналов, возбуждаемых различными источниками колебаний. При этом частотный состав большинства "элементарных" сигналов может значительно изменяться даже на установившихся режимах работы агрегата.
• Методология диагностирования зарождающихся и развитых дефектов • 1 — 4 •
Первое подмножество ( работоспособные состояния) включает множество состояний, различающихся запасом работоспособности, который характеризуется приближением агрегата к предельно допустимому. Переход из одного состояния в другое может объясняться возникновением неисправностей, не приводящих к потере работоспособности. Такие неисправности называют зарождающимися дефектами.
Второе подмножество — предельные состояния (аварийные, отказ), соответствующие возникновению в оборудовании неисправностей, характеризуется мощностью, определяющейся количеством неисправностей, подлежащих обнаружению.
Для того, чтобы правильно поставить диагноз, все возможные состояния оборудования разбивают на некоторое конечное число классов, подлежащих распознаванию. Число классов может определяться, например, количественной мерой контролируемых параметров работы оборудования с одной стороны и числом возможных отказов (неисправностей) с другой. Такая классификация состояний оборудования позволяет разделить процесс диагностирования на несколько этапов.
На первом этапе устанавливают принадлежность данного агрегата по состоянию к одному из подмножеств: работоспособное состояние или предельное (аварийное) состояние, соответствующие возникновению в агрегате неисправностей. Этот этап называют определением работоспособности.
На втором этапе устанавливают состояние агрегата в подмножестве работоспособных состояний, т.е. проводят анализ характера изменения его работоспособности и в ряде случаев предсказание момента перехода агрегата в предельные состояния, и, следовательно, прогнозирование состояния оборудования. На данном этапе происходят деградационные процессы в узлах агрегата и связанные с ними изменения свойств вибропроцессов. Диагностирование состояния оборудования на данном этапе называют диагностированием зарождающихся дефектов или диагностированием дефектов на ранней стадии развития.
На третьем этапе определяют, в каком из предельных (аврийных) состояний находится диагностируемый агрегат.
Этот этап называют обнаружением возникшей неисправности (дефекта).
Поиск диагностических признаков технического состояния эксплуатируемого оборудования — важнейшая задача вибромониторинга и вибродиагностики. От способа построения системы диагностических признаков и конкретизации перечня этих признаков существенно зависит успех последующей классификации технических состояний объекта.
В качестве диагностических признаков могут фигурировать различные характеристики колебательных процессов: частота и амплитуда спектрального компонента, компонент кепстра, модуляционные характеристики, характеристики временных реализаций вибрации и ряд других.
В большинстве ситуаций распознавание технического состояния оборудования осуществляется в условиях ограниченной информации при большом уровне помех, источником которых являются: несоблюдение постоянства внешних условий, неполнота описания классов состояний, неопределенность границ между классами состояний и соответствующих им классов диагностических признаков.
Совокупность последовательных действий при постановке диагноза называется алгоритмом диагностирования. Алгоритм диагностирования опирается на диагностическую модель, которая устанавливает связь между состояниями агрегата и их отображениями в пространстве диагностических признаков. Диагностическая модель процессов возбуждения и распространения колебаний в агрегате в ряде случаев помогает сформировать систему характерных диагностических признаков.
Алгоритмы диагностирования включают формирование системы информативных диагностических признаков, построение эталонных изображений
• Методология диагностирования зарождающихся и развитых дефектов • 1 — 2 •
и может быть отделено от момента внедрения длительным временем (1 — 2 года и больше);
• ускорить процесс восстановления эксплуатационной надежности парка машин и управлять им;
• облегчить взаимодействие изготовителя машин и ее заказчика (эксплуатационника) в конфликтных ситуациях, особенно в начальном периоде массового проявления дефектов и организации действия по их устранению.
В то же время использование диагностики может вызвать некоторый отрицательный эффект. Отрицательные факторы при внедрении системы вибромониторинга на предприятии следующие:
•• увеличение досрочных (временных) выводов изделий из эксплуатации;
•• неизбежность "необоснованных" съемов изделий с эксплуатации вследствие ложных диагнозов;
•• возможность пропуска в дальнейшую эксплуатацию некоторой части ненадежных изделий (особенно на начальном этапе использования диагностики);
•• вероятность чисто экономической неэффективности внедрения диагностики (например, при малом парке эксплуатируемых изделий);
•• необходимость проведения сложных и трудоемких исследований для разработки методик и средств диагностирования конкретных дефектов.
Данные отрицательные факторы, снижающие эффективность диагностики, обусловлены следующими причинами:
••• обычно встречающимся на практике неполным представлением о дефекте, его причинах, условиях возникновения и факторах, влияющих на его появление и развитие, а также началом разработки методик диагностики конкретного объекта по конкретному дефекту при неполном представлении о дефекте в целях сокращения сроков обеспечения надежности парка оборудования;
••• необходимостью диагностирования по параметрам, являющимся лишь частью комплекса факторов, связанных с дефектом, а также технической невозможностью проведения исследований для разработки методик диагностирования в объеме, дающем полную информацию;
••• необходимостью принятия компромиссных решений при установлении границ (норм) в условиях недостаточно четкой и полной оценки альтернативных факторов, а также недостаточно полной информацией о возможных альтернативах и их последствиях (особенно это относится к информации интуитивного характера), выдаваемой при постановке задачи диагностики и подготовке решений лицами, ставящими задачу и принимающими решения;
Для повышения эффективности диагностики при ее практическом использовании важно, чтобы лица, принимающие решения и ставящие задачи диагностики, ясно понимали тот факт, что диагностика проводится в условиях неполноты и неопределенности информации, и поэтому неизбежен компромисс между пропусками дефекта и необоснованными заключениями о неисправности объекта.
Для обеспечения эффективной диагностики необходима реализация основных принципов получения и использования информации в условиях ее неполноты, в том числе последовательное уточнение методик и установленных границ по мере накопления информации, постепенное ужесточение границ (норм) с учетом того факта, что проявление дефектов в парке машин растянуто во времени, разделение парка изделий по степени ненадежности и выделение группы изделий по очередности доработок, обеспечение контролепригодности машин.
Оглавление
Часть 1. Виброакустический неразрушающий контроль и Стр. вибрационно —диагностический методГлава 1.Методология диагностирования зарождающихся и 1 — 1...1 — 22 развитых дефектов
Глава 2.Методология проведения диагностических 2—1...2 —28 виброизмерений роторных агрегатов
Глава 3.Организация мониторинга технического состояния 3—1...3 — 22 оборудования
Глава 4.Методология нормирования вибрации и 4— 1...4 —22 распознавания технического состояния
оборудования
Часть 2. Зарождающиеся и развитые дефекты: практика
распознавания
Глава 5. Неуравновешенность ротора 5—1...5 —24
Глава 6. Нарушения соосности валов (расцентровка) 6—1...6—16
Глава 7. Нарушения жесткости опорной системы 7—1...7 —24
Глава 8. Дефекты подшипников скольжения 8—1...8—18
Глава 9. Дефекты подшипников качения 9—1...9—14
Глава 10.Вибрация электрических машин электромагнитного 10—1...10 —20 происхождения
Глава 11. Дефекты зубчатых передач 11 —1...11 —14
Глава 12.Нарушения гидро и газодинамики потока 12—1...12 —22
Приложение 1. Термины и определения. а1 — 1...а1 — 12
Приложение 2. Общие сведения о вибрации и операции по а2— 1...а2— 16 обработке вибросигнала.
Приложение 3. Список литературы. аЗ—1...аЗ—1
УДК 621.833
Редактор: Р.В.Васильева
Александр Рудольфович Ширман Александр Борисович Соловьев
Практическая вибродиагностика
и мониторинг состояния механического оборудования
Ил. 166. Табл.12. Библиогр. 276 с. Москва, 1996.
Книга включает описание методологии вибродиагностирования зарождающихся и развитых дефектов, сведения о вибрации и надежности работы оборудования, современных методик вибромониторинга технического состояния оборудования, средств сбора, обработки и анализа данных, принципов определения норм вибрации и оценки технического состояния оборудования и практическое руководство по выявлению дефектов оборудования на основе частотного анализа виброакустического сигнала. Рассмотрены диагностические признаки основных дефектов машин и механизмов, иллюстрированные более чем 60 —ю реальными примерами.
Книга предназначена для инженерно — технических работников предприятий транспорта нефти и газа, химической и нефтеперерабатывающей промышленности, электроэнергетики, металлургии и целлюлозно-бумажной промышленности.
Все права защищены. Настоящее произведение (книга) в целом или часть данного произведения не может быть перепечатано, воспроизведено, сохранено в любой информационной системе, изменено или переведено в любой другой вид любыми электронными, механическими, фотокопировальными, записывающими или другими средствами или использовано в коммерческих целях без письменного разрешения авторов.
[1] Настоящая глава основана на материалах, заимствованных из книг "Виброакустическая диагностика зарождающихся дефектов", Балицкий Ф.Я., Иванова М.А., Соколова А.Г., Хомяков Е.И. М.: Наука, 1984, 129 с., Карасев В.А., Ройтман А.Б. "Доводка эксплуатируемых машин.
Вибродиагностические методы." М.: Машиностроение, 1986, 192 с. Иногда это заимствование носило частичный характер, иногда мы брали материал целиком, ничего не изменяя в удачно написанном тексте.
1 В настоящей главе использованы материалы, заимствованные из книги: Гольдин А.С. "Устранение вибрации турбоагрегатов на тепловых электростанциях" М.:Энергия, 1980, 96 с. Иногда это заимствование носило частичный характер, иногда мы брали отдельный материал целиком, ничего не изменяя в удачно написанном тексте.
2 Вышесказанное справедливо в основном для агрегатов с жесткими роторами. У агрегатов с гибкими роторами (особенно крупных турбоагрегатов) могут наблюдаться значительные колебания опор узлов со сбалансированным ротором при дисбалансе роторов других узлов.
4 Необходимо помнить, что эти же особенности может иметь форма сигнала вибрации и при других дефектах, в частности дефектах подшипников качения.
5 Необходимо помнить, что асимметричная вибрация необязательно связана с односторонним нарушением жесткости опоры — подобный эффект может быть связан, например, с анизотропностью и нелинейностью характеристик опоры или комбинацией некоторых других дефектов (синхронная вибрация).
1 Поскольку в России отсутствует единая терминология для некоторых дефектов смазки, авторы приносят извинения за возможное, некорректное с точки зрения читателя, употребление неправильных терминов и их англоязычных аналогов.
[2] Последний факт может говорить не тольно об ослаблениях жесткости: подобный эффект может свидетельствовать о наличии низкочастотной вибрации.
[3] Необходимо помнить, что высокий уровень шумов необязательно бывает связан с ослаблениями жесткости — подобный эффект может появляться, например, при дефектах подшипников качения.
1 В настоящей главе использованы материалы, заимствованные из книги: Гольдин А..С. "Устранение вибрации турбоагрегатов на тепловых электростанциях" М.:Энергия, 1980, 96 с.
Это заимствование носило частичный характер: мы брали отдельный материал, ничего не изменяя в удачно написанном тексте.
3 См. главу "Нарушения жесткости опорной системы".
1 Необходимо помнить, что почти периодическая форма кривой виброускорения характерна и при некоторых других дефектах, например дисбалансе.
2 Необходимо помнить, что асимметричная вибрация может быть не связана с расцентровкой, и подобный эффект во многих случаях вызывается другими причинами, например, с односторонним нарушением жесткости опоры или одновременным (совместным) влиянием на фазу вибрации на частоте вращения ротора и ее гармониках различных дефектов (т.е. при синхронных колебаниях).
1 При написании настоящей главы авторы использовали "Методические рекомендации по проведению диагностических виброизмерений центробежных компрессорных машин и центробежных насосных агрегатов предприятий Министерства химической и нефтеперерабатывающей промышленности" (РДИ, утверждены 28.11.91), рекомендуемые в качестве методического документа для руководства при организации вибродиагностики на поднадзорных предприятиях Государственным комитетом по надзору за безопасным ведением работ в промышленности и горному надзору (Госгортехнадзор России, письмо Nо 04 — 35/54 от 20.05.92).